Understanding Business Work Orders for Efficiency
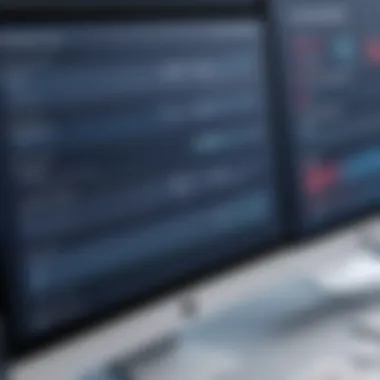
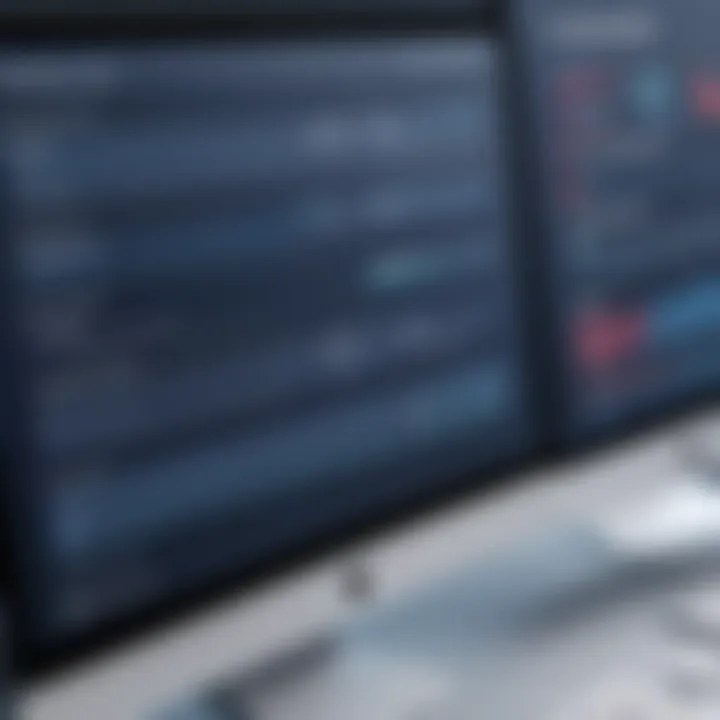
Intro
In any business operation, the efficient handling of tasks is paramount. A vital component in achieving this are work orders. They serve as formal documents that authorize and help manage various tasks, whether for maintenance, repair, production, or service requirements. Understanding the structure and functionality of work orders can significantly influence an organizationโs operational effectiveness.
Work orders not only streamline project management but also enhance communication across departments. They ensure that all team members are aligned on objectives, timelines, and responsibilities. Grasping the nuances of these orders is essential for today's decision-makers and IT professionals. This understanding can lead to improved workflow, proper resource allocation, and ultimately, increased productivity.
With the rapid advancement in technology, the concept of work orders is evolving. Incorporating technology into these processes is becoming standard practice. Organizations that do not adapt may find themselves lagging behind in terms of efficiency and competitiveness.
Intro to Business Work Orders
The purpose of a work order transcends mere documentation. It facilitates communication among team members, supports accountability, and tracks progress on various tasks. By having a clear structure, organizations can avoid common pitfalls such as miscommunication or resource wastage.
Definition and Purpose
A business work order is a written directive that outlines specific tasks that require attention. It includes essential details such as the nature of the work, the personnel assigned, and timelines for completion. The purpose of work orders is to ensure tasks are executed methodically while keeping all stakeholders informed.
Understanding this concept helps organizations streamline operations. Effective use of work orders enhances the workflow and promotes accountability by making it clear who is responsible for tasks. Furthermore, work orders can be vital for record-keeping to analyze performance and improve future operations.
Historical Context
Historically, work orders have evolved alongside industrial advancements. In the earlier days, work orders were often informal and based on verbal instructions. This led to inefficiencies and errors. As businesses grew and processes became more complex, the need for formal work orders emerged. Organizations began documenting requests to improve clarity and communication.
During the 20th century, particularly with the rise of large manufacturing industries, work orders became more standardized. They are now integral to various sectors, ranging from construction to IT services. This historical transformation highlights their importance in adapting to changing business environments and maintaining operational effectiveness.
Types of Work Orders
The concept of work orders is integral to business operations. Understanding the different types of work orders allows companies to effectively allocate resources, prioritize tasks, and streamline workflows. Each type serves a distinct purpose, aligning with specific operational needs. This section discusses three prominent types of work orders: maintenance work orders, repair work orders, and construction work orders. Each type has unique elements and benefits that play a crucial role in the overall efficiency of an organization.
Maintenance Work Orders
Maintenance work orders are essential for routine inspections and upkeep of equipment and facilities. They ensure that systems remain operational, prolonging the lifespan of assets while minimizing unplanned downtime. Businesses often rely on a schedule for these orders, allowing teams to proactively address issues before they escalate.
A well-structured maintenance work order includes:
- Identifying information: Details like the location, equipment involved, and responsible personnel.
- Task description: Clear guidelines on what maintenance is required, such as cleaning, lubricating, or adjusting.
- Priority levels: Indicating urgency can help teams focus on tasks that need immediate attention.
- Due dates: Establishing timelines ensures that maintenance is conducted regularly and comprehensively.
The benefits of maintenance work orders extend beyond mere compliance. They can enhance productivity by keeping systems running efficiently, thus reducing overall operational costs.
Repair Work Orders
Repair work orders come into play when equipment fails or malfunctions. Unlike maintenance work orders, which are preventive, repair work orders respond to existing issues. They require prompt attention to mitigate any impact on operations.
Key elements of a repair work order typically include:
- Detailed task description: Information about the nature of the fault or damage and steps needed for rectification.
- Parts and tools required: A list of any materials necessary to complete the repair work.
- Assigned personnel: Identifying the technician responsible helps in tracking accountability and ensuring expertise.
- Estimated time for completion: Giving an expected timeframe for repairs can help in scheduling and resource management.
Repair work orders are critical for minimizing disruptions. A swift and effective repair process can significantly affect productivity, customer satisfaction, and ultimately, the bottom line.
Construction Work Orders
Construction work orders are specialized for projects that involve building or renovating. These orders generally entail a broader scope than the other types of work orders and require comprehensive planning and execution.
Important aspects of construction work orders include:
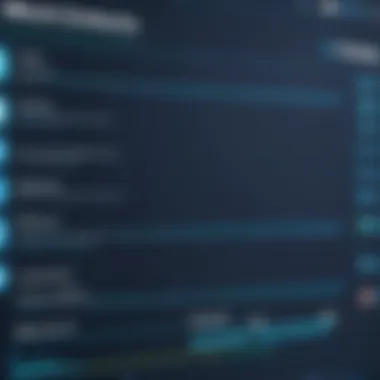
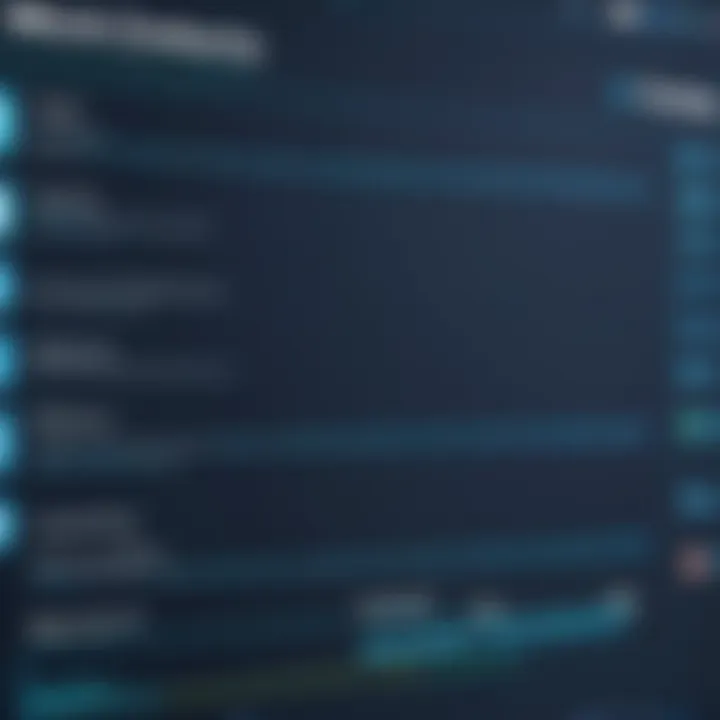
- Scope of work: A detailed outline of the construction project, including materials, labor, and timelines.
- Budgeting: Estimating financials related to the project to ensure it stays within limits.
- Permits and approvals: Documentation that may be needed based on local regulations or project size.
- Progress tracking: Monitoring advancement through stages to adhere to timelines and budgets.
Construction work orders facilitate smooth project management. Ensuring all stakeholders are informed and engaged is vital in achieving project goals, enhancing collaboration among teams.
Components of a Work Order
The components of a work order are essential elements that ensure clarity and effectiveness in the management process. Each part serves a purpose that contributes to the overall efficiency, tracking, and execution of tasks. Understanding these components is crucial for decision-makers and professionals in any field. When implemented correctly, these components can significantly enhance a company's operational workflows.
Identifying Information
Identifying information is at the core of any work order. This includes the unique ID of the order, names of the employees involved, and the location of the work to be completed. Having precise identifying information helps in organizing and tracking work orders efficiently. It must be complete to avoid confusion among teams or departments that might be collaborating.
Provision of basic contact information also ensures that quick communication can occur when needed. Noticing if there are repeated errors in information can signal a need for training or clearer processes, ultimately saving time and resources.
Task Description
The task description outlines what needs to be accomplished. It should be concise but detailed enough to provide clarity. A well-defined task helps technicians or employees understand their objectives, reducing time spent interpreting vague instructions. This description should also include any specific requirements, tools needed, and safety considerations.
Providing comprehensive task descriptions ensures that everyone involved on the project can align their efforts towards a common goal, leading to increased accountability and performance. It is a key aspect in minimizing downtime and improving project turnaround.
Priority Levels
Priority levels indicate the urgency of a task. They allow teams to manage their time effectively by distinguishing between critical and non-essential work. Assigning priority levels can also help in resource allocation, ensuring that urgent tasks are addressed before less pressing matters. A clear system to rate the urgency of each job is vital; otherwise, organizations might misallocate resources or overlook important tasks.
Teams may use categories such as high, medium, or low priority. Consistent use of a priority system can enhance the overall workflow, helping team members respond quickly and efficiently to immediate needs.
Due Dates
Due dates establish a timeframe for task completion. They create a sense of accountability, encourage promptness, and help in project planning. When employees know when a task is due, they can effectively manage their workload and ensure that all projects proceed as scheduled. Timelines can alert teams to potential delays, allowing them to adjust plans proactively.
It is crucial to regularly update due dates based on project developments while maintaining communication lines open between team members.
Work Order Processes
In the realm of business operations, the processes surrounding work orders are essential for ensuring tasks are initiated, approved, executed, and completed in an organized manner. Work order processes facilitate effective communication among teams, allow for tracking progress, and help maintain productivity within various departments. This section covers the crucial stages of work orders by dissecting the initiation, approval, and execution phases, thereby enhancing the understanding of how effective management can lead to operational excellence.
Initiation of Work Orders
The initiation of work orders is the first step in the process and sets the foundation for all subsequent actions. This stage typically begins when a need or request arises within the organization. Employees or managers submit requests that outline the nature of the work required, whether it be maintenance, repairs, or other operational tasks.
An effective initiation process includes:
- Clear Request Submission: Ensuring that all requests contain adequate detail minimizes confusion and streamlines the workflow. Requests should define the nature of the task, including location, equipment involved, and any supporting documents.
- Categorization: Accurate categorization of work orders into relevant types helps in routing them to appropriate teams or individuals. This classification can often reduce processing time.
- Prioritization: Understanding the urgency of tasks is critical. Implementing a system to rank work orders based on priority can enhance response times and resource allocation.
In this stage, it is pivotal to keep detailed records of requests. This not only provides clarity but also supports future analysis and continuous improvement of the process.
Approval Workflow
After initiation, work orders must undergo an approval workflow to determine if they should proceed. The approval process serves as a checkpoint to ensure resources are used efficiently and that the requested work aligns with organizational goals.
Key components of an effective approval workflow include:
- Designated Approvers: Establishing roles for who can approve work orders reduces bottlenecks and accelerates processing time. Depending on the organization, this might include managers, team leads, or resource coordinators.
- Digital Approvals: Utilizing electronic systems can streamline this workflow. Software solutions allow for notifications and can speed up the process of obtaining approvals, which is generally more efficient than paper-based systems.
- Feedback Mechanism: Implementing a way for approvers to provide feedback can be beneficial. It assists requesters in understanding decisions and can serve as a learning tool for future submissions.
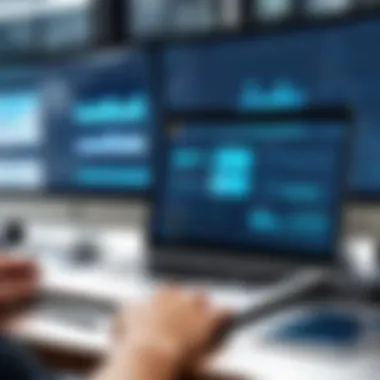
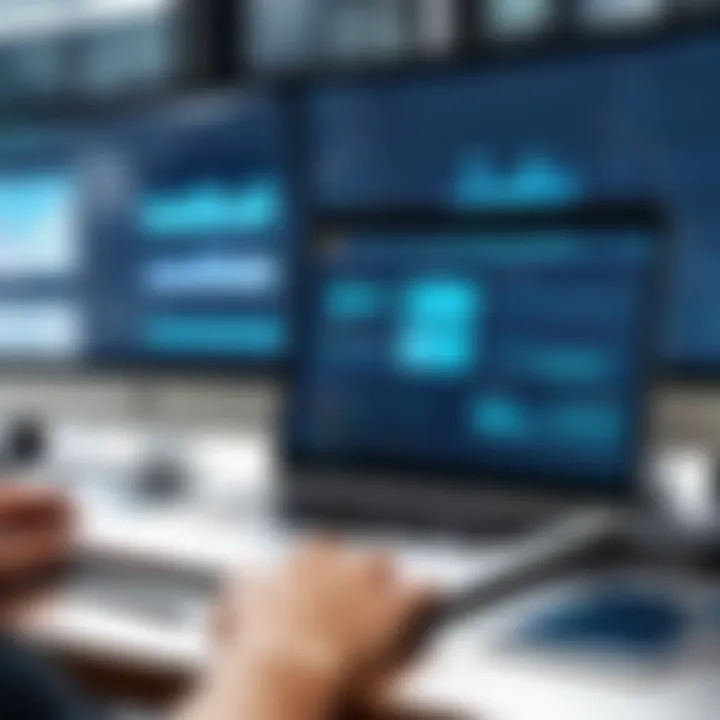
By optimizing the approval workflow, businesses can reduce delays and enhance the overall efficiency of work order management.
Execution and Completion
The execution phase is where all planning and approvals transform into action. This is the stage where tasks are assigned to teams, and actual work begins. Successful execution requires clear communication, adequate resource allocation, and supervision to ensure compliance with standards.
Here are critical factors in the execution phase:
- Task Assignment: Delegating tasks effectively is vital. All team members should clearly understand their responsibilities and expected outcomes.
- Resource Management: Proper allocation of resources, such as tools, equipment, and personnel, is essential for successful completion. Ensuring that resources are readily available minimizes downtime and enhances efficiency.
- Progress Tracking: Regularly monitoring the progress of tasks is necessary to address any roadblocks promptly. Utilizing a project management system or software can aid in this tracking.
- Completion and Documentation: Once work is finished, itโs crucial to review outcomes and update records accordingly. Documenting completed work orders provides a historical perspective for future analysis and can highlight areas for improvement.
"An efficient work order process not only improves productivity but also aligns operations with strategic objectives."
In summary, understanding work order processes is fundamental for operational success. Each stageโinitiation, approval, and executionโplays a significant role in enhancing productivity and efficiency. By refining these processes, organizations can respond effectively to work requests and maintain high standards in operation.
Benefits of Effective Work Order Management
Effective work order management is a cornerstone of operational success for organizations across various sectors. This process encompasses not merely the management of tasks, but also the optimization of resources, time, and communication, ensuring that businesses can respond swiftly to their operational needs. In this section, we will discuss the key benefits of effective work order management, focusing on improved operational efficiency, enhanced communication, cost management, and data tracking and reporting.
Improved Operational Efficiency
Operational efficiency is critical in driving productivity within a business. A structured work order system streamlines the workflow, reducing bottlenecks that can hamper progress. Properly managed work orders allow teams to understand priorities and allocate resources effectively. This clarity helps prevent misunderstandings and ensures that tasks are executed on time.
When employees know what needs to be done and by when, they can focus their effort. Tools and software that facilitate work order management automate many tasks, ensuring that teams can work more efficiently. Integrating such systems leads to notable time savings. Furthermore, the systematic approach helps in identifying recurring issues, enabling organizations to take proactive steps rather than reactive ones.
Enhanced Communication
Clear communication channels are vital for any organization, particularly when it comes to managing tasks. A well-implemented work order system enhances communication among teams. It provides a centralized platform where employees can access up-to-date information regarding tasks and deadlines. The transparency in the process minimizes confusion, and everyone is kept informed.
Enhanced communication fosters collaboration, as team members can update each other on progress or challenges. Regular updates through the system allow management to track task completion and intervene when necessary. Overall, this leads to a cohesive working environment where employees are aligned towards common goals.
Cost Management
Managing costs is essential for any business to remain competitive. Effective work order management directly contributes to better cost control. By having a clear overview of tasks, necessary resources, and timelines, managers can avoid overspending.
Additionally, tracking work orders can reveal inefficiencies, which can be addressed to lower costs. For instance, if certain tasks take longer than expected, it signals an opportunity to evaluate workflows and address issues. Moreover, reduced downtime and faster task completions lead to cost savings by maximizing the use of resources.
Data Tracking and Reporting
Data tracking and reporting are integral to understanding business performance. A robust work order system captures and organizes data related to various tasks, providing insights that can inform future strategies. This data can include information on time taken to complete tasks, resource utilization, and cost incurred.
Such insights help identify trends and patterns that can lead to more informed decision-making. By analyzing historical data, companies can make strategic adjustments to improve their operations. Reports generated from work order systems can inform stakeholders about productivity and efficiency, ensuring that decisions are data-driven.
"Effective work order management not only saves time but also enhances overall operational success by ensuring that organizations can adapt proactively to changing demands."
In summary, effective work order management facilitates improved operational efficiency, enhances communication, supports effective cost management, and enables insightful data tracking and reporting. Each of these benefits works in concert to create a more resilient and adaptable organization, essential in todayโs fast-paced business environment.
Challenges in Work Order Management
Work order management plays a critical role in achieving operational efficiency within a business context. However, there are numerous challenges that organizations often face. These challenges can lead to decreased productivity, inefficiencies, and ultimately, higher operational costs. Understanding these challenges is crucial for decision-makers and industry professionals who wish to optimize their work order management processes. By addressing them, a business can significantly improve its overall performance and services.
Lack of Standardization
One of the primary challenges in work order management is the lack of standardization. Without a standardized process, different departments may adopt varied approaches to creating, processing, and managing work orders. This inconsistency can lead to confusion and miscommunication among teams. Furthermore, a non-standardized system can result in delays and errors.
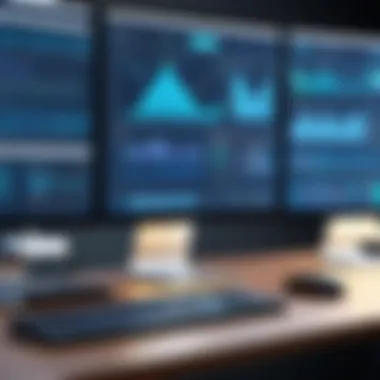
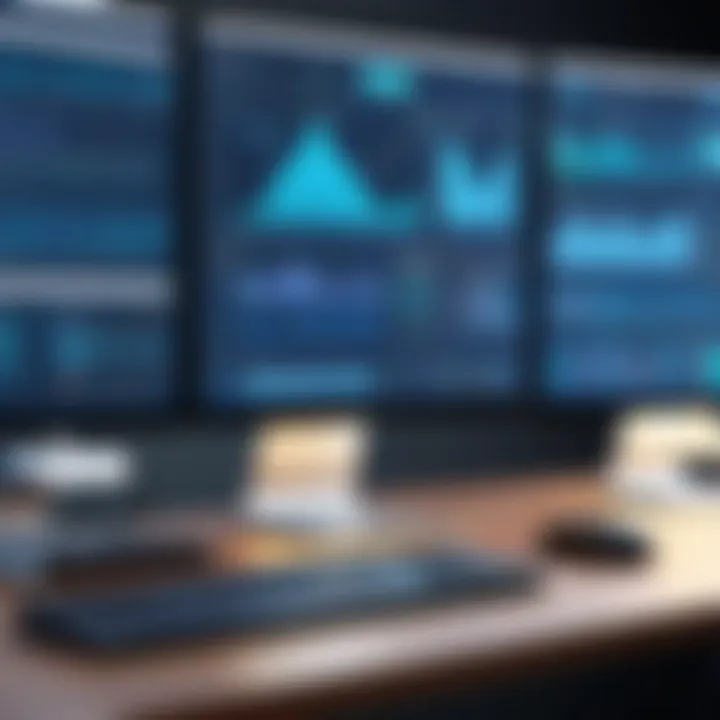
To combat this issue, organizations should develop clear guidelines outlining how work orders should be handled. Establishing standard operating procedures can create a uniform process across all departments. This helps ensure that every employee is on the same page, thereby enhancing communication and streamlining operations. It's beneficial for companies to invest in training programs for staff to familiarize them with these protocols.
Inadequate Resource Allocation
Another significant challenge faced by businesses is inadequate resource allocation. Properly prioritizing resources is key to successful work order execution. When resources are not effectively allocated, delays and uncompleted tasks can arise. This often frustrates employees and customers alike.
Organizations can minimize this challenge by implementing resource management software that tracks and allocates resources efficiently. This software can analyze workload and availability, ensuring that personnel and materials are where they need to be. It also enables managers to make data-driven decisions regarding resource deployment, ultimately resulting in faster completion of work orders.
Technological Limitations
In today's fast-paced business environment, technological limitations can severely hamper work order management. Many organizations still rely on outdated systems that lack integration with other essential business tools. This can lead to data silos, creating barriers to effective communication and workflow.
To overcome these limitations, businesses should evaluate their current technology landscape. Integrating modern Computerized Maintenance Management Systems (CMMS) and mobile applications can enhance work order management significantly. By utilizing up-to-date technology, organizations can achieve real-time visibility into their work orders, improved tracking capabilities, and faster communication among teams.
"Investing in the right technology is essential for overcoming challenges in work order management."
Technological Advances in Work Order Systems
In today's fast-evolving business landscape, the implementation of technological advances in work order systems plays a pivotal role. These advancements not only enhance operational efficiency but also enable businesses to meet their growing demands with agility. Companies that adopt such technologies gain competitive edges, ensuring that work orders are processed swiftly and accurately.
Computerized Maintenance Management Systems (CMMS)
Computerized Maintenance Management Systems (CMMS) are essential software solutions that help organizations manage their maintenance activities effectively. By utilizing a CMMS, businesses can generate, monitor, and track work orders seamlessly. These systems provide significant benefits:
- Improved Data Management: CMMS centralizes all maintenance data in one location, making it easier to access historical records and analyze trends.
- Predictive Maintenance: With analytics features, organizations can predict equipment failures before they happen, thus minimizing downtime.
- Resource Allocation: CMMS can help allocate personnel efficiently by prioritizing work orders based on urgency and skill sets required.
The efficiency of a CMMS does not only streamline operations but significantly reduces costs associated with maintenance.
Mobile Applications for Work Orders
The rise of mobile applications for work orders is another game-changer for businesses. These applications allow workers in the field to receive, update, and close work orders directly from their mobile devices. The benefits are substantial:
- Real-Time Updates: Staff can update work order statuses immediately, ensuring that information is accurate and current.
- Increased Efficiency: With functionalities like barcode scanning, users can complete tasks quicker and with less chance for error.
- Accessibility: Field teams can access important dataโsuch as manuals or safety protocolsโon the go, ensuring they have the right information to complete tasks effectively.
The integration of mobile technology enhances communication both within teams and across departments, leading to better collaboration and productivity.
Integration with Other Business Systems
Integrating work order systems with other business applications is vital for maximizing their utility. A well-integrated system can harmonize multiple departments, leading to enhanced information flow and better decision-making. Key integration points include:
- Enterprise Resource Planning (ERP): Linking work orders with ERP systems allows for better budgeting and resource allocation.
- Customer Relationship Management (CRM): This connection ensures that customer issues related to work orders are prioritized properly.
- Supply Chain Management Systems: Integration here helps manage inventory levels in accordance with work orders, avoiding delays due to lack of supplies.
Ultimately, effective integration fosters a smoother operational framework and contributes to a holistic view of the business processes.
The real value lies in how work order technology can transform operational workflows and lead to enhanced decision-making across all business functions.
These technological advances are not merely trends; they represent essential tools for businesses looking to thrive in a competitive market. By understanding and embracing these technologies, companies can significantly improve their work order management practices.
Best Practices for Work Order Management
Effective management of work orders significantly impacts operational efficiency and overall success of businesses. This section outlines essential best practices that should be routinely applied to harness the full potential of work order systems. Such practices enhance workflow, improve communication, and ultimately drive productivity.
Establishing Clear Protocols
Clear protocols are fundamental for successful work order management. This includes defining steps for creating, processing, and completing work orders. Organizations should ensure that everyone involved understands their roles and responsibilities within the process. Establishing standard operating procedures minimizes confusion and promotes consistency.
Using templates for common tasks can streamline the initiation of work orders. A consistent format helps maintain uniformity and ensures that all necessary information is captured. Examples of information to include are task descriptions, resource requirements, and expected time frames.
- Define clear roles for staff and teams
- Create standard operating procedures (SOPs)
- Utilize templates for common work orders
- Ensure documentation is accessible to all relevant parties