Unlocking Manufacturing Potential with OEE Software
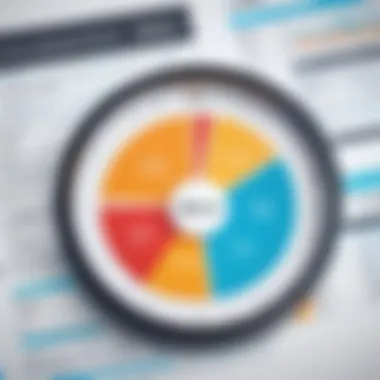
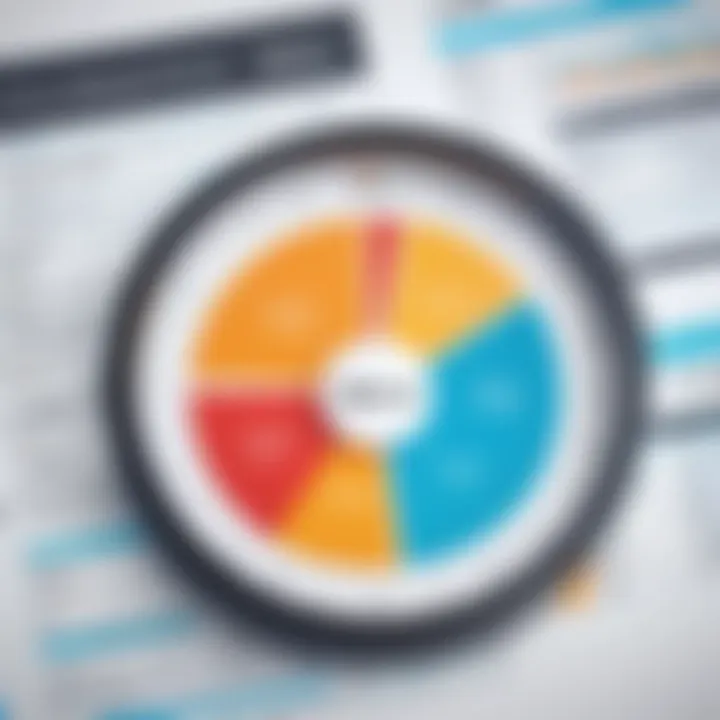
Intro
In the landscape of manufacturing, Overall Equipment Effectiveness (OEE) software has emerged as a critical tool for optimizing performance. OEE provides a metric that reflects how effectively a manufacturing operation is utilized compared to its full potential. This article will dive into the fundamental aspects of OEE software, examining its features, benefits, and implementation challenges. Understanding OEE software is essential not only for decision-makers and IT professionals but also for entrepreneurs looking to enhance productivity through data-driven insights.
OEE software helps identify inefficiencies in operations, enabling organizations to reduce waste and improve overall productivity. As industries evolve, the importance of leveraging technology to monitor and optimize manufacturing processes cannot be overstated.
Key Features and Functionalities
Comprehensive Overview
OEE software typically encompasses several key features that are essential for monitoring and enhancing productivity. These features include:
- Real-time Data Tracking: Provides live insights into production processes, allowing for immediate response to issues as they arise.
- Reporting Tools: Generates comprehensive reports to help analyze performance trends over time, aiding in strategy development.
- Downtime Analysis: Identifies and categorizes reasons for equipment downtime, further assisting in reducing operational interruptions.
- Integration Capabilities: Many solutions offer the ability to integrate with existing systems, such as ERP and MES, ensuring seamless data flow across the organization.
Incorporating these elements, OEE software facilitates a thorough understanding of production efficiency, enabling teams to make informed decisions based on real data.
Target Users
The target audience for OEE software spans various sectors within the manufacturing industry. Key users include:
- Manufacturing Managers: Responsible for overseeing production and ensuring optimum performance.
- Quality Control Teams: Focused on maintaining standards and improving product output.
- IT Professionals: Tasked with implementing and maintaining software solutions within the organization.
- Business Executives: Interested in leveraging insights for strategic planning and operational improvement.
Each of these groups benefits from the insights provided by OEE software, making it a versatile tool for driving efficiency across the board.
Pricing Models and Cost Analysis
Breakdown of Pricing Tiers
Understanding the pricing structure of OEE software is crucial for making an informed decision. Generally, pricing can be categorized into different tiers based on features and support levels. Common models include:
- Basic Packages: Typically include core functionality at a lower cost, ideal for small to mid-sized operations.
- Standard Packages: Offer enhanced features such as advanced reporting and integration, suitable for larger organizations.
- Enterprise Solutions: Comprehensive offerings tailored for large-scale operations requiring extensive customization and support.
Additional Costs to Consider
While evaluating OEE software, it is essential to consider potential additional costs. These may include:
- Training Expenses: Costs associated with training staff to effectively use the software tools.
- Maintenance Fees: Ongoing support and updates necessary to keep the software functional and relevant.
- Integration Costs: Overhead related to connecting the OEE software with existing systems.
Awareness of these factors aids in achieving a better understanding of the total cost of ownership for OEE software solutions.
The End
Understanding OEE Software
Overall Equipment Effectiveness (OEE) software plays a crucial role in modern manufacturing operations. Its significance lies in its ability to optimize production efficiency, reduce waste, and enhance overall equipment utilization. Understanding OEE software requires familiarity with numerous key concepts and elements. This not only bolsters decision-making capabilities for industry professionals but also drives significant improvement in operational outcomes.
To truly grasp the value of OEE software, one must first understand the underlying concept of OEE itself. OEE is a metric that quantifies the efficiency of a manufacturing process. It allows organizations to identify various sources of production losses while providing essential insights into operational performance. These insights often guide managers and operators in implementing practical enhancements to their processes.
Definition of OEE
Overall Equipment Effectiveness (OEE) can be defined as a performance measurement framework used to assess how effectively a manufacturing operation is utilized. This metric combines three elements: availability, performance, and quality. Each of these components is vital to determine the overall percentage of productive time.
- Availability represents the percentage of scheduled production time that is actually utilized. It accounts for downtime due to failures or changeovers.
- Performance indicates the speed at which the operations run compared to their designed capacity. It highlights inefficiencies that can arise from slow cycles or interruptions.
- Quality reflects the proportion of products that meet quality standards, thereby excluding rework or defects.
In essence, the OEE score ranges from 0% to 100%, wherein 100% denotes perfect production without any inefficiencies.
Purpose of OEE Software
The primary purpose of OEE software is to provide organizations with the tools necessary to monitor, analyze, and enhance their manufacturing processes. By leveraging advanced data collection techniques, real-time analytics, and user-friendly dashboards, OEE software helps identify, quantify, and eliminate inefficiencies.
Key purposes include:
- Data Tracking: Capturing accurate data about production processes, including machine performance and output quality.
- Performance Analysis: Analyzing data trends to identify areas for improvement and track changes in performance over time.
- Decision Support: Providing insights that help business leaders make informed decisions about operational improvements, technology investments, and workforce training.
Key Features of OEE Software
Understanding the key features of OEE software is crucial for businesses aiming to enhance their operational efficiency. Each feature plays a vital role in gathering valuable insights, promoting faster decision-making, and ultimately improving productivity. An effective OEE software system empowers organizations to better manage their manufacturing processes, reduces waste, and increases overall equipment effectiveness. Here, we delve into each of the critical features that define OEE software.
Data Collection and Analysis
Data collection is the backbone of OEE software. The ability to gather data from various manufacturing processes allows institutions to analyze their performance comprehensively. This feature enables managers to identify inefficiencies, track machine utilization, and monitor production rates.
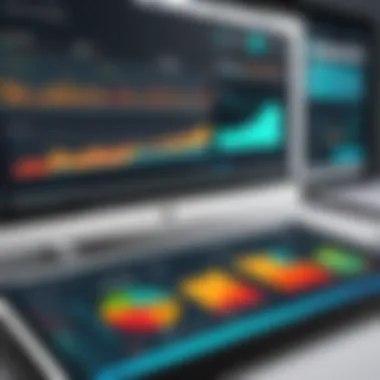
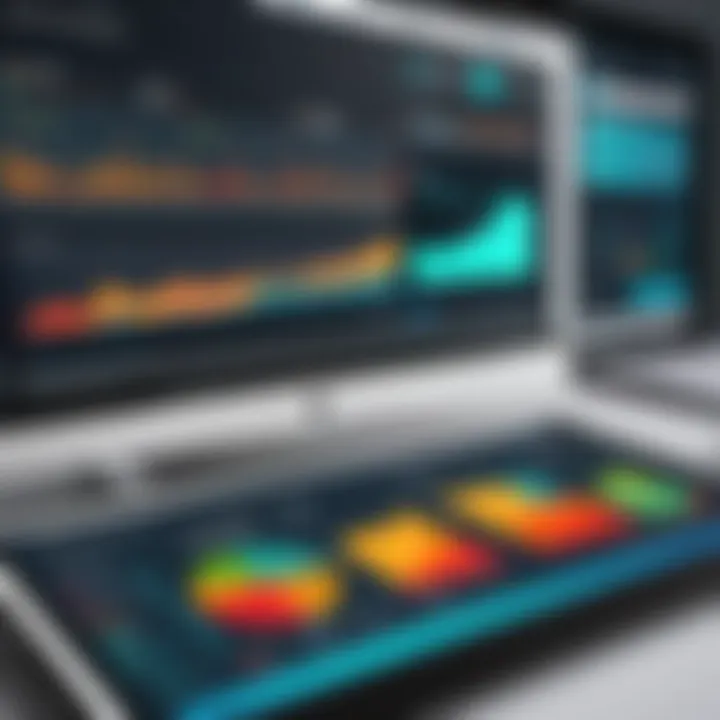
OEE software typically integrates with various sensors and machines to pull real-time data. The data collected is then analyzed to provide actionable insights.
- Real-time data allows for swift interventions and improvements.
- Historical data analysis aids in the identification of trends over time.
By scrutinizing the data collected, businesses can engage in continuous improvement initiatives, making significant strides toward operational excellence.
Real-Time Monitoring
Real-time monitoring is an indispensable feature of OEE software. This function ensures that managers can track operational performance continuously without delays. By using dashboards or alerts, stakeholders can receive instant notifications about any deviations from expected production levels.
Key benefits include:
- Immediate visibility of machine performance
- Alerts for anomalies that hinder production
This level of engagement fosters a proactive work environment, allowing teams to react promptly to issues before they escalate and impact the production schedule.
Reporting and Dashboard Functionality
The reporting and dashboard functionality in OEE software enhances the visualization of critical data. Reports can be generated on demand, providing deep dives into performance metrics. Dashboards summarize key performance indicators, showing trends and important statistics at a glance.
- User-friendly interfaces allow decision-makers to interpret data easily.
- Customizable reports can be tailored to meet specific business needs.
Effective reporting plays a crucial role in strategic planning and helps stakeholders understand the immediate and long-term impacts of their decisions.
Integration with Other Systems
OEE software does not operate in isolation. The capability to integrate with other systems such as ERP (Enterprise Resource Planning) and MES (Manufacturing Execution Systems) is paramount. This feature ensures seamless data flow among various departments and systems.
Integration has compelling advantages:
- Holistic view of operations
- Improved collaboration between departments
Coordinating data across systems allows organizations to streamline processes and reduce redundancies, fostering a more connected and efficient manufacturing environment.
Benefits of Implementing OEE Software
Implementing Overall Equipment Effectiveness (OEE) software brings significant advantages to manufacturing operations. The integration of such systems enhances productivity, reduces downtime, improves quality control, and generates cost savings. Understanding these benefits is critical for decision-makers, IT professionals, and entrepreneurs when considering the adoption of OEE software. Each aspect contributes to gaining a competitive edge in the market.
Enhanced Productivity
Enhanced productivity is one of the main benefits of OEE software. By measuring the effectiveness of equipment, businesses can identify areas for improvement. OEE software provides insights into where processes slow down or where there are bottlenecks. This data enables managers to make informed decisions to optimize operations.
Key features like real-time monitoring allow businesses to track performance continuously. With instant feedback, teams can react to issues faster. They can deploy resources efficiently to maintain productivity levels. The overall outcome is smoother production flows, higher output rates, and greater operational effectiveness.
Reduced Downtime
Downtime is a considerable concern in manufacturing, leading to lost revenue and increased costs. OEE software helps minimize downtime through predictive maintenance and real-time alerts. By closely monitoring performance indicators, teams can foresee potential equipment failures before they occur.
For example, OEE tools can analyze machinery data to predict when maintenance is necessary. This proactive approach prevents unexpected breakdowns, allowing for scheduled repairs. As a result, production schedules remain intact, and the likelihood of efficiency losses decreases significantly.
Improved Quality Control
Quality control is crucial in manufacturing. OEE software enhances this by providing accurate metrics related to product quality. Detailed reporting capabilities allow companies to track defects in real-time. As a result, teams can quickly address quality issues before they escalate.
Using OEE software, organizations can implement stricter quality checks and monitor compliance with standards. Regular analysis of quality data supports continuous improvement initiatives. Over time, this leads to less waste, higher satisfaction rates among customers, and an overall boost in brand reputation.
Cost Savings
Cost savings may come from multiple sources when implementing OEE software. Reducing downtime directly correlates to higher production rates, thus increasing profit margins. Enhanced productivity also leads to better allocation of resources, which optimizes labor and material costs.
By lowering defect rates through improved quality control, businesses reduce scrap and rework expenses. This financial efficiency ultimately contributes to a healthier bottom line. Moreover, better visibility into operations helps senior management make strategic decisions that further contribute to reducing overhead costs.
Investing in OEE software is not just an operational decision; it is a strategic move that reflects a commitment to continuous improvement in manufacturing processes.
In summary, the benefits of implementing OEE software extend beyond basic operations. Enhanced productivity, reduced downtime, improved quality control, and cost savings generate a substantial return on investment. As manufacturing becomes increasingly competitive, leveraging these advantages through OEE software can be a vital factor in sustaining success.
Challenges in Implementing OEE Software
Implementing Overall Equipment Effectiveness (OEE) software comes with its unique set of challenges. Understanding these challenges is crucial for organizations looking to optimize their manufacturing processes. Acknowledging potential pitfalls can lead to better planning, improved stakeholder engagement, and successful adoption of the software solutions.
Resistance to Change
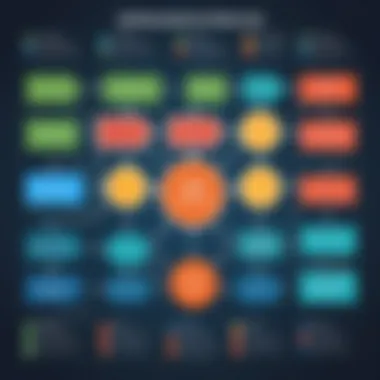
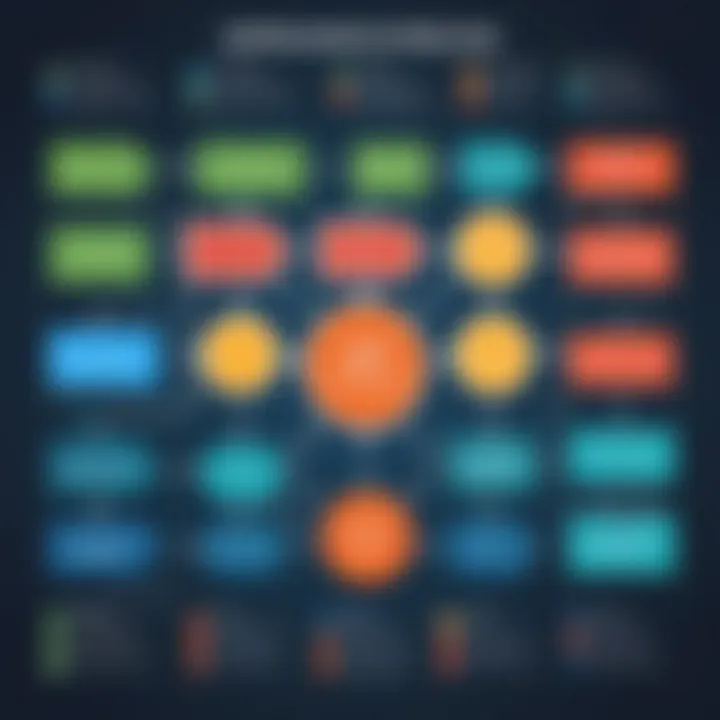
Resistance to change is a common phenomenon in many organizations. When introducing OEE software, employees may be hesitant to adapt to new systems and processes. This resistance can stem from various factors, including comfort with existing practices and lack of understanding of the benefits of OEE solutions. Effective change management strategies are necessary to address this concern.
To minimize resistance, management must actively engage with employees. Communication about the purpose and advantages of OEE software can help alleviate fears. Involving staff in the implementation process, such as choosing the software or aiding in its installation, can also foster a sense of ownership.
Making training accessible and continuous ensures that users feel competent and confident in utilizing the software. Encouraging feedback can further create a supportive environment where everyone feels included in the transformation.
Data Quality Issues
Data quality is indispensable for deriving accurate insights from OEE software. If the data collected is inconsistent or incomplete, it can lead to erroneous conclusions and misinformed decision-making. Poor data quality may arise from various sources, including outdated machinery, inadequate data entry processes, and lack of standardized procedures.
To tackle data quality issues, organizations should establish clear data collection guidelines. Implementing automated data capture systems can help reduce human error. Regular audits of data integrity will ensure that information remains accurate.
Moreover, fostering an organizational culture that values data-driven decision-making is essential. Employees should understand the importance of accurate data and the role it plays in optimizing manufacturing processes.
Training Requirements
Training is a vital aspect of implementing OEE software. Without adequate training, employees may not utilize the software to its full potential. It is essential to provide both initial training during the rollout and ongoing support as users become more familiar with the system.
A tailored training program can address the varying roles within an organization. Operators, managers, and IT staff may require different levels of understanding. Utilizing real-life scenarios during training can enhance retention of information and encourage practical application.
Additionally, resource materials such as user manuals, video tutorials, and FAQs can support continuous learning. Establishing mentoring or peer support groups enables users to share their experiences and assist each other in the learning process.
"A well-trained staff is key to successfully leveraging OEE software and achieving overall productivity goals."
In summary, addressing these challenges head-on can pave the way for successful implementation of OEE software. Taking proactive steps to manage resistance, ensure data quality, and provide comprehensive training will enhance overall user experience and minimize disruption in operations.
Comparative Analysis of OEE Software Solutions
Comparative analysis of OEE software solutions is crucial for organizations aiming to enhance their operational efficacy. With numerous vendors providing a variety of solutions, decision-makers must discern which tools align best with their unique needs. This analysis covers key factors, including software capabilities, integration potential, and overall usability. Understanding these elements aids in evaluating software options against each other, which in turn influences productivity, reporting accuracy, and ultimately profit margins.
Leading OEE Software Vendors
The landscape of OEE software is populated by several reputable vendors known for their distinctive offerings. Vendors like Siemens, Rockwell Automation, and Dassault Systèmes provide robust OEE solutions tailored for a variety of industries. Each company has developed its tools with unique features that cater to different operational needs.
Siemens' solutions often emphasize integration within their extensive automation portfolio, which offers a seamless user experience across devices and platforms. Rockwell Automation focuses on delivering real-time data visibility, thus enabling rapid decision-making in manufacturing processes. Dassault Systèmes presents an interactive interface that allows users to visualize their operations in a more engaging manner. Evaluating these vendors involves analyzing specific features that impact usability and effectiveness in streamlining processes.
Feature Comparison
A feature comparison of OEE software solutions highlights the various functionalities that users can expect from different vendors. Critical features to assess include:
- Data Collection: Some systems automate data capturing directly from machines, ensuring accuracy.
- Real-Time Monitoring: This enables operators to address issues promptly, mitigating downtime.
- Reporting Tools: Efficient reporting mechanisms assist in generating insights that help adjust operational strategies.
- Integration Capabilities: The ability to connect with existing systems is vital for a smooth transition and enhanced efficiency.
By making side-by-side comparisons, organizations can better understand which softwareβs features will best address their specific operation requirements. This insight aids in making informed decisions while considering both current and future needs.
Pricing Models
Understanding pricing models is essential for effective budget management in OEE software implementation. Pricing may vary significantly based on the vendor, features provided, and deployment options such as cloud-based versus on-premises solutions.
- Subscription-Based Pricing: Some vendors offer a monthly or annual subscription model that includes updates and support.
- Licensing Fees: Traditional licensing often requires a one-time payment, usually including some form of maintenance and support.
- Pay-Per-Use: This model allows companies to only pay for what they utilize, which can be beneficial for smaller operations or seasonal production companies.
Ultimately, a thorough understanding of these pricing structures can help decision-makers allocate resources effectively. Choosing the correct financing strategy ensures long term value from the chosen software without overspending.
"Choosing the right OEE software solution can be the difference between operational stagnation and breakthrough efficiency."
Assessing these comparative elements will better inform decision-makers, enabling organizations to select an OEE software solution that not only meets but exceeds their operational expectations.
Case Studies on OEE Implementation
The practical applications of Overall Equipment Effectiveness (OEE) software are best illustrated through real-world case studies. Evaluating these case studies is crucial as they provide tangible proof of the effectiveness and benefits that OEE software can bring to various manufacturing contexts. They allow decision-makers and IT professionals to analyze success scenarios and extract lessons learned from actual implementations. By examining these real-world examples, organizations can see how addressing specific challenges can lead to significant improvements in productivity, efficiency, and profitability.
Manufacturing Sector Applications
In the manufacturing sectors, OEE software typically plays a pivotal role in driving improvement initiatives. Various industries, from automotive to pharmaceuticals, have adopted OEE software to optimize their processes. A notable example is the automotive manufacturing sector. Here, OEE software helps in tracking machine performance, identifying bottlenecks, and offering insights for improvement.
Key applications in the manufacturing sector include:
- Tracking Downtime: Monitoring equipment downtime provides insights that allow manufacturers to address machine failures more efficiently.
- Quality Control: OEE software ensures that high-quality standards are maintained by analyzing production defects and variations during runs.
- Performance Measurement: Real-time performance metrics assist manufacturers in assessing operation efficiency and adjusting strategies promptly.
By implementing OEE software within these facets, businesses within the sector can streamline processes and maintain a competitive edge.
Success Stories
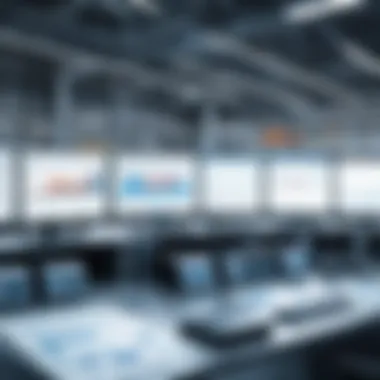
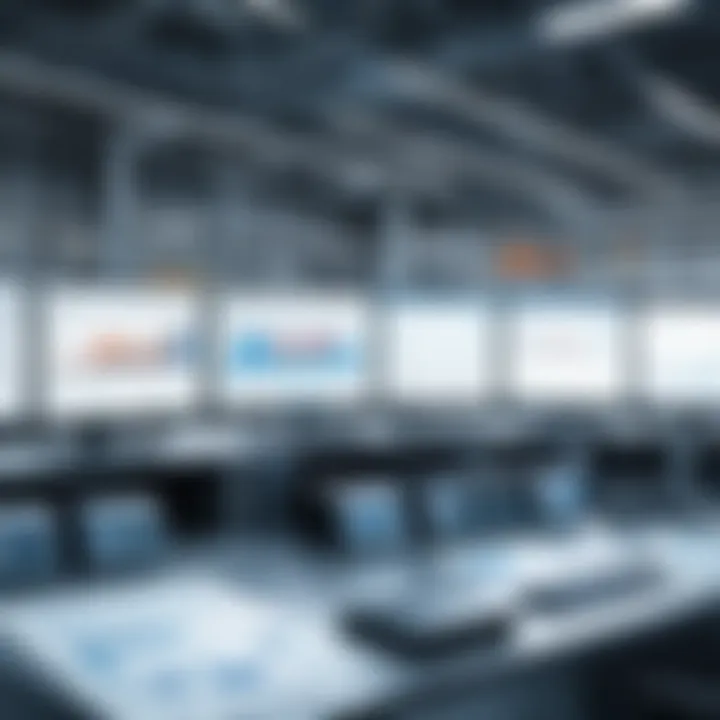
Numerous organizations have successfully implemented OEE software, leading to measurable results. For example, a well-known beverage manufacturing company faced persistent production delays due to equipment inefficiencies. By integrating OEE software, they could monitor equipment performance and downtime in real-time.
The outcomes were significant:
- Increased OEE by 15%: The insights from OEE measurements revealed areas of improvement. The company was able to optimize machine scheduling and enhance maintenance practices.
- Reduced Waste by 10%: By pinpointing inefficiencies, the manufacturer minimized the material waste associated with production.
- Improved Employee Engagement: With transparent data reporting, employees took an active role in identifying inefficiencies, leading to a culture of continuous improvement.
"Success in manufacturing increasingly relies on how effectively organizations use data. OEE software transformed our operations and set the foundation for ongoing development." - Operations Manager, Beverage Manufacturer
These success stories serve as vital testament to the capabilities of OEE software. They offer critical insights that supply more than just numbers; they provide a narrative of transformation through data-driven decision-making. As organizations continue to face pressures for efficiency, such examples become essential learning tools for others looking to embark on similar journeys.
Future Trends in OEE Software
Understanding the future trends in OEE software is essential for decision-makers and industry professionals. As manufacturing processes evolve, OEE software must adapt to meet new challenges and opportunities. Keeping abreast of these trends ensures that companies remain competitive and can leverage technology to optimize operations.
AI and Machine Learning Integration
The integration of Artificial Intelligence (AI) and Machine Learning (ML) into OEE software is transforming how data is utilized. These technologies enable systems to learn from data patterns and make informed predictions about equipment performance. With historical data, OEE systems can provide insights that previously required significant manual analysis.
Key benefits include:
- Predictive Maintenance: AI can forecast when machines will require maintenance, significantly reducing unplanned downtime.
- Anomaly Detection: Machine learning algorithms can identify unexpected changes in performance, allowing for swift action.
- Data-Driven Decisions: Enhanced analytics from AI leads to better decision-making on resource allocation and production planning.
Moreover, incorporating AI allows for a more tailored experience. Custom alerts and suggestions based on the specific needs of the manufacturing operation can be generated, making OEE software more responsive and user-centric. It is essential for businesses to consider AI and ML as investment avenues for future-proofing their operational efficiencies.
Data Analytics Advancement
Advancements in data analytics significantly impact how OEE software functions. As manufacturing continues to generate vast amounts of data, the ability to analyze this data effectively becomes crucial. New analytical methods and tools are emerging that provide deeper insights into production workflows.
Noteworthy trends in data analytics include:
- Real-Time Analysis: Instant data analysis offers real-time insights, enabling manufacturers to quickly respond to issues as they arise.
- Big Data Integration: Data from various sources can now be combined for a comprehensive view of operations, enhancing overall decision-making capabilities.
- User-Friendly Dashboards: Modern OEE software features intuitive dashboards that present complex data clearly. This ensures that users at all levels of the organization can understand metrics effortlessly.
"Investing in advanced OEE software is not just about immediate gains but securing long-term competitiveness in the manufacturing landscape."
Keeping pace with these trends will be vital for companies aiming to optimize their manufacturing processes and remain ahead of the competition.
Best Practices for OEE Software Implementation
Implementing Overall Equipment Effectiveness (OEE) software requires a thoughtful approach. The success of the implementation hinges upon understanding key best practices that can significantly impact the operational outcomes. This section addresses essential elements to keep in mind, such as vendor selection, stakeholder engagement, and the establishment of clear metrics and KPIs. Each of these components plays a crucial role in deriving the maximum benefit from OEE software.
Selecting the Right Vendor
When choosing an OEE software vendor, several factors come into play. First, assess the vendor's reputation in the industry. Look for reviews, testimonials, and case studies that reflect their capabilities. Consider their experience with businesses similar to yours. This can indicate their ability to understand and meet your specific needs.
Additionally, review the softwareβs flexibility. It should easily integrate with your existing systems, such as Enterprise Resource Planning (ERP) and manufacturing execution systems. Compatibility ensures a seamless data flow, reducing the risk of data silos. Another key point is the support services the vendor offers. Efficient customer support can resolve issues quickly, minimizing downtime.
Pricing models also vary. Make sure to find a solution that fits your budget without compromising on important features. It might help to perform a cost-benefit analysis to ensure the selected software will yield a good return on investment. Overall, selecting the right vendor sets a strong foundation for a successful implementation process.
Engaging Stakeholders
Engaging all relevant stakeholders is a vital step in maximizing the impact of OEE software. This includes not only upper management but also operational staff who will use the software daily. Involving a diverse group ensures multiple perspectives are considered and can lead to a more comprehensive understanding of potential challenges.
Clear communication about the benefits of OEE software is essential. Educate stakeholders on how the software will enhance operational efficiency and productivity. This can foster buy-in and reduce resistance to change. Conduct workshops or informational sessions to gather insights and address any concerns they may have. Having a change management strategy in place can also help ease the transition.
Building a culture of accountability is extremely important. Encourage stakeholders to actively participate in data reporting and analysis. When they see their contributions influence performance metrics, it enhances engagement and motivation.
Setting Up Metrics and KPIs
Establishing relevant metrics and Key Performance Indicators (KPIs) is crucial for tracking the performance of OEE software. Start by defining what constitutes success in your context. Consider your specific operational goals such as reducing downtime, improving quality, and increasing production speed.
Common metrics in OEE include availability, performance, and quality. Each of these metrics offers insights into different aspects of equipment effectiveness. For example, availability measures the percentage of scheduled time that the equipment is actually running. Performance considers the speed of production compared to designed capacity. Quality reflects the percentage of produced items that meet quality standards.
Furthermore, ensure the chosen KPIs are measurable and achievable. Regularly reviewing these metrics helps in identifying trends and making informed decisions. Continuous improvement should be part of a feedback loop, allowing for course corrections as necessary. These steps will ensure OEE software delivers its maximum potential when properly implemented.
Closure
In this article, we have explored the extensive landscape of Overall Equipment Effectiveness (OEE) software and its critical role in manufacturing optimization. As industries continue to evolve, harnessing the capabilities of OEE software is paramount for businesses aiming to maintain a competitive edge. The significance of this software lies not only in enhancing productivity but also in fostering a culture of continuous improvement.
The concrete benefits of implementing OEE software are evident. These tools provide insights that help in minimizing downtime, improving quality, and driving cost savings. Decision-makers who adopt OEE software can expect significant improvements in operational efficiency, allowing them to respond effectively to market demands and challenges.
However, the successful implementation of OEE software comes with challenges. Resistance to change, data quality issues, and the necessary training requirements must be considered carefully. A clear understanding of these elements can guide organizations as they embark on this transformative journey.
Summary of Key Insights
- Importance of OEE: OEE serves as a vital metric, offering clear visibility into operational performance. It allows for the identification of efficiency gaps and the implementation of corrective measures.
- Benefits Realized: Improved productivity, reduced downtime, and enhanced quality control represent just a few advantages of utilizing OEE software. Such tools drive not only immediate benefits but also long-term success by optimizing manufacturing processes.
- Challenges Recognized: While transitioning to OEE software, organizations face challenges, including employee resistance and the need for robust training programs. Addressing these barriers upfront can lead to a healthier adoption curve and maximize the system's potential.
- Future Perspectives: The landscape of OEE software is set to evolve. Integrations with AI and advanced data analytics are predicted to reshape how organizations perceive and utilize OEE metrics.
The exploration of OEE software is more than just a guide; it is a call to action for companies ready to embrace a future characterized by data-driven decisions and operational excellence. As businesses move forward, an ongoing commitment to utilizing OEE software will be crucial to achieving lasting success and efficiency in the manufacturing sector.