The Impact of Barcodes on Warehouse Management

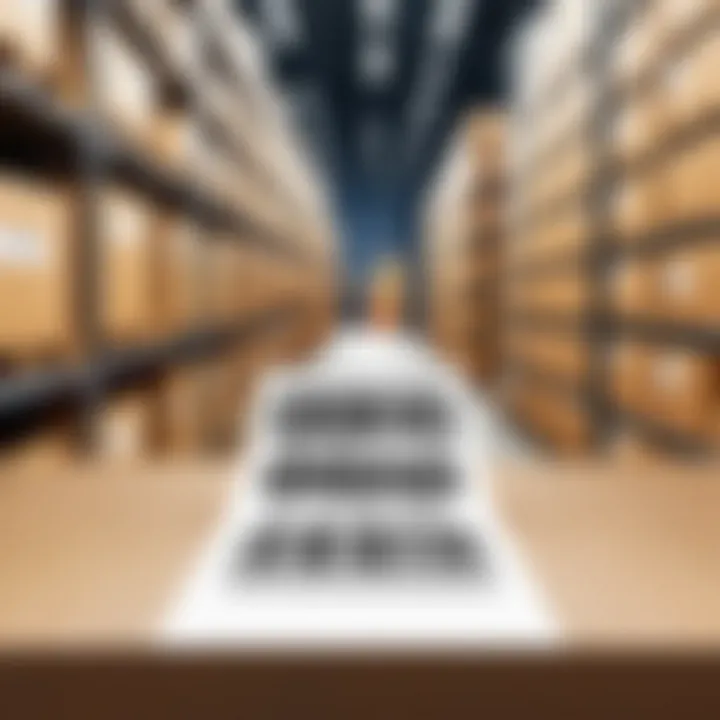
Intro
In the complex sphere of warehouse management, efficiency and accuracy are paramount. The integration of barcode technology has reshaped traditional practices, leading to improved inventory control and operational performance. By enabling swift data capture and streamlined processes, barcodes stand as a vital component in the quest for optimized warehouse functionality.
This article will delve into the nuances of how barcodes operate within warehouse settings, addressing their role in bolstering inventory accuracy, enhancing productivity, and enriching overall supply chain visibility. Additionally, we will explore best practices for implementation, potential challenges faced during the adaptation of barcode systems, and the intersection of barcode technology with emerging innovations.
Decision-makers and industry professionals seeking to refine their warehouse operations will find invaluable insights in the analysis presented here.
Key Features and Functionalities
Comprehensive Overview
Barcode technology offers several essential functionalities that revolutionize warehouse operations. Here are some critical aspects to consider:
- Accuracy: Barcodes significantly reduce human error often associated with manual data entry, promoting precise inventory counts.
- Speed: Scanning barcodes allows for rapid data retrieval and entry, enhancing process flow and reducing time spent on inventory updates.
- Real-time Data: With barcode systems, warehouses can maintain up-to-date inventories, providing visibility at all times.
- Integration: Modern barcode systems can seamlessly integrate with management software, ensuring a cohesive operational framework.
These features collectively contribute to the seamless functioning of warehouse management.
Target Users
The adoption of barcode technology is not limited to specific industries but spans various sectors, including:
- Retail: For tracking stock levels and managing product flow.
- Manufacturing: To monitor raw materials and finished goods.
- Healthcare: For managing medications and supplies efficiently.
- Logistics: To ensure timely delivery of goods and maintain shipment accuracy.
Each of these target users benefits distinctly from barcode systems, positioning them as vital tools in respective supply chains.
Pricing Models and Cost Analysis
Breakdown of Pricing Tiers
Determining the cost of implementing barcode technology varies based on numerous factors. Generally, the pricing can range from affordable handheld scanners to elaborate fixed-position readers. The expenses often involve:
- Hardware Costs: Including scanners, printers, and labels.
- Software Licensing: For inventory management systems that facilitate barcode integration.
- Training Costs: Ensuring staff are well-versed in utilizing systems efficiently.
Additional Costs to Consider
While initial investments are paramount, there are ancillary costs requiring attention. These may include:
- Maintenance Fees: For ongoing support and updates of the systems.
- Upgrades: As technology evolves, periodic investments may be necessary to maintain system efficacy and compatibility.
"Integrating barcode technology may appear costly upfront, but the long-term savings on labor and errors often outweigh the investment."
Foreword to Barcode Systems
Barcode systems are essential in modern warehouse management. Their role is not merely functional but transformative. This overview introduces the reader to the fundamental components of barcode systems and their implications in warehouse settings. Barcode technology facilitates accuracy, efficiency, and organization within warehouses, making it pivotal for decision-makers and IT professionals.
Definition of Barcodes
Barcodes are visual representations of data that can be scanned and interpreted by machines. They consist of parallel lines or squares that encode information. This information can relate to products, inventory levels, or shipment details. The ability to capture and retrieve this information quickly makes barcodes indispensable in inventory management. Each barcode is unique, which allows for precise tracking of items within a warehouse. For instance, when scanned, a barcode can provide details about the itemβs quantity, location, and history, critically enhancing operational decision-making.
History of Barcodes
The history of barcodes dates back to the 1940s when they were first conceived by Norman Joseph Woodland and Bernard Silver. Their initial idea was to create a system that could automate grocery checkout processes. In 1952, the first barcode was used on a pack of Wrigleyβs gum. However, it was not until the introduction of the Universal Product Code (UPC) in 1973 that barcodes gained wide acceptance in retail environments. The advancement of scanning technology in the 1980s and 1990s further propelled the adoption of barcodes across various industries, including warehousing. Today, barcodes have evolved to include one-dimensional and two-dimensional formats, enhancing the capacity of data storage and readability.
The Importance of Barcodes in Warehouse Management
Barcodes play a critical role in modern warehouse management. Their integration enhances various aspects of operations, ultimately leading to improved efficiency and accuracy. Relying on barcode technology helps address many challenges faced by warehouses today. In this section, we will discuss three primary benefits of barcodes: enhancing inventory accuracy, streamlining operations, and improving supply chain visibility.
Enhancing Inventory Accuracy
Inventory accuracy is the foundation of effective warehouse management. Barcodes enable precise tracking of products throughout the supply chain. When goods move in and out of the warehouse, scanning barcodes confirms the details associated with each item. This reduces human error significantly. Studies suggest that companies utilizing barcode systems can achieve over 99% inventory accuracy.
The benefits of high inventory accuracy are manifold. For instance, it minimizes the risk of stockouts and overstocking. Businesses can better meet customer demands without excess inventory. Consequently, there is less wastage related to product expiration, especially in industries with perishable goods. Adoption of barcodes also supports efficient stock audits and cycle counts. These processes become more straightforward and less time-consuming, ultimately leading to enhanced operational effectiveness.
Streamlining Operations
Another major advantage of implementing barcodes in warehouse settings is the streamlining of day-to-day operations. With barcode systems, warehouse staff can conduct their tasks more quickly. Scanning barcodes instead of manually entering product information saves significant time. This efficiency allows employees to focus more on value-added activities rather than administrative tasks. Moreover, real-time data updates inform staff about inventory status instantly.
Order picking, shipping, and receiving processes are transformed with barcode systems. For example, when an order is ready for shipment, warehouse workers can scan the barcodes of the package. This confirms that the right items are included, reducing errors. Streamlined processes directly contribute to faster turnaround times and improved customer satisfaction. Thus, investments in barcode technology lead to a robust operational framework that can accommodate growth and adapt to future challenges.
Improving Supply Chain Visibility
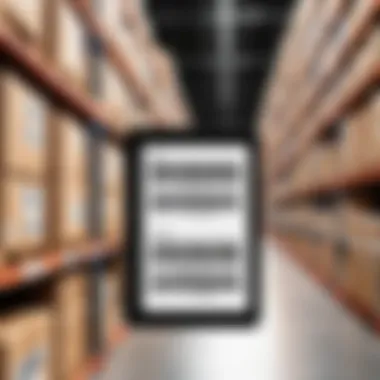
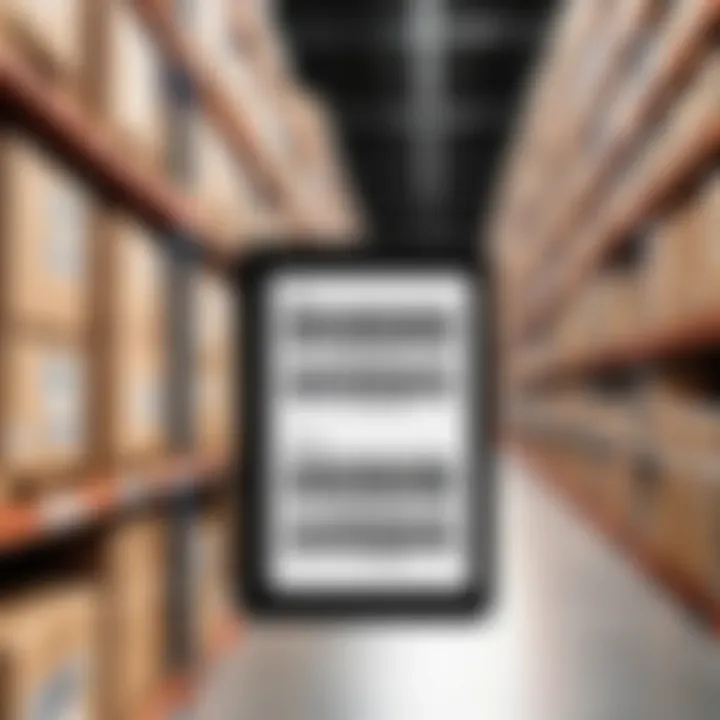
Supply chain visibility is vital for effective warehouse management. Barcodes enable real-time tracking of products as they flow through the supply chain. Each scan provides critical data which enhances transparency. Stakeholders can monitor products from supplier to customer, allowing companies to identify delays or disruptions promptly.
This visibility improves decision-making. Managers can analyze trends and response times, facilitating timely interventions when necessary. Furthermore, effective supply chain visibility fosters collaboration among different departments. When all teams have access to the same accurate information, they can work together seamlessly to solve problems. This interconnectedness ultimately enhances the overall performance of the warehouse.
"Investing in barcode technology transforms warehouse management by providing accurate data that enhances visibility and performance."
Types of Barcode Technologies
Barcodes play a crucial role in warehouse management by serving as efficient tools for tracking and managing inventory. Understanding the various types of barcode technologies is essential for organizations looking to enhance their operational effectiveness. Different types of barcodes come with unique features that cater to specific needs. Each barcode technology has its advantages and considerations which can significantly impact inventory processes.
1D Barcodes
1D barcodes, also known as linear barcodes, consist of parallel lines of varying widths. They are the most common type of barcodes used in many industries, including warehousing. Typically, 1D barcodes can hold information such as product identification numbers and are scanned using laser barcode scanners.
Some benefits of 1D barcodes include:
- Simplicity: Easy to create and print.
- Cost-effectiveness: They require less complex technology for scanning and printing compared to other types.
- Widely used: Compatibility with various systems and equipment makes them versatile.
However, they also have limitations; for instance, they can store limited information compared to 2D barcodes. Despite this, their suitability for high-volume applications keeps them in demand.
2D Barcodes
2D barcodes, or matrix barcodes, contain data both horizontally and vertically, allowing them to hold much more information than 1D barcodes. Common types of 2D barcodes include Data Matrix and PDF417. These barcodes are usually scanned using camera-based scanning devices.
Advantages of 2D barcodes include:
- High Capacity: They can store extensive data like URLs, contact information, or product details.
- Error Correction: Many 2D codes include built-in error correction, minimizing read errors.
- Flexible Size: They can be printed smaller without losing readability, making them ideal for products with limited space.
Businesses looking for more data storage options may consider transitioning from 1D to 2D barcodes, especially in complex inventory systems.
QR Codes
QR codes, or Quick Response codes, have gained popularity due to their ability to be scanned quickly and easily with smartphones. They are a specific type of 2D barcode that can direct users to websites, provide product information, or link to promotional content.
The benefits of QR codes in warehouse management include:
- Fast Scanning: They can be scanned from various angles, reducing the time needed for inventory checks.
- Dynamic Content: QR codes can direct users to different content, which can be updated without changing the code itself.
- User Engagement: They can enhance customer interactions with products by providing additional information through mobile devices.
Incorporating QR codes into inventory management strategies can enhance both warehouse efficiency and customer engagement.
Conclusion: Understanding the different types of barcode technologies is vital for businesses. Companies must evaluate their specific needs and choose the right technology that aligns with their goals. This choice can lead to improved inventory accuracy, efficiency, and customer satisfaction.
Implementation of Barcode Systems
In warehouse management, the implementation of barcode systems is a critical step that can significantly influence operational success. Proper implementation ensures that a company can effectively track inventory, reduce errors, and streamline processes. The chosen system should align with the specific requirements of the warehouse, integrate effortlessly with existing operations, and provide measurable benefits that enhance overall efficiency.
Assessing Warehouse Needs
Before deciding on a barcode system, it is essential to assess the specific needs of the warehouse. This assessment should encompass the current inventory system, the volume of goods processed, and the type of products managed. Each warehouse has distinct characteristics, from the layout to the items stored, which directly impact how barcodes are utilized.
- Analysis of Inventory Levels: A thorough evaluation of existing inventory levels and turnover rates can provide insights into the most effective barcode solutions.
- Warehouse Layout: Understanding the physical layout will assist in determining the optimal placement of scanning stations and barcode labels.
- Operational Workflow: Observing daily operations helps identify areas where barcode systems can simplify processes.
Choosing the Right Barcode System
Selecting the appropriate barcode system involves a careful examination of several factors. Organizations should consider various barcode types, scanning technologies, and compatibility with current systems.
Key Considerations:
- Type of Barcode: Whether to use 1D, 2D, or QR codes depends on the data requirements and scanning capabilities available.
- Scanning Technology: Evaluate the need for handheld scanners vs. fixed point-of-sale systems based on the warehouse workflow.
- Compatibility: Ensure that the new barcode system is compatible with existing inventory management software to avoid data silos.
Hardware Considerations
Hardware selection is vital. The choice of scanners, printers, and labeling systems can affect efficiency.
- Durability: Choosing rugged scanners is crucial for warehouse environments where equipment may face wear and tear.
- Printing Options: High-quality label printers should match the type of barcode used, ensuring clarity and durability of labels under various conditions.
- Maintenance: Consider maintenance requirements for hardware to avoid disruptions in operations.
Software Integration
Finally, successful implementation hinges on proper software integration. The new barcode system should integrate smoothly with existing warehouse management systems.
- Data Synchronization: Ensure real-time data sharing between barcode systems and inventory management software. This integration prevents discrepancies and centralizes information.
- User Interface: A user-friendly interface is vital for warehouse staff to adapt quickly to the new system. Training should include instructions on using both the hardware and software effectively.
- Scalability: Opt for a software solution that can grow with the business. This flexibility is essential as inventory and operational needs evolve over time.
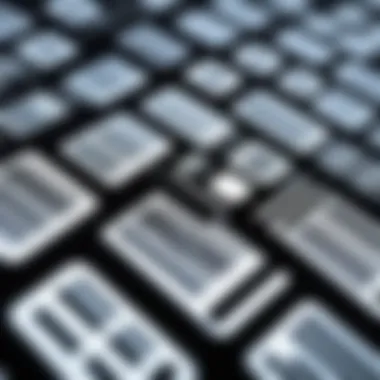
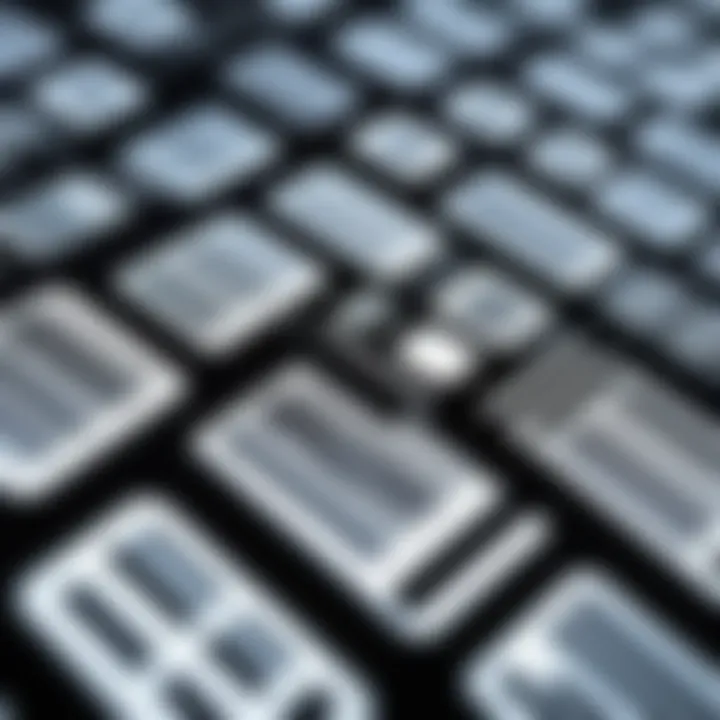
"A barcode system without proper integration is like a ship without a compass; it may float but wonβt reach its destination efficiently."
Implementing barcode systems requires thoughtful planning and execution. By assessing needs, choosing the right technology, considering hardware, and prioritizing software integration, warehouses can unlock the full potential of barcode solutions in enhancing their operational capabilities.
Best Practices for Barcode Usage
Implementing barcodes effectively can significantly enhance warehouse management processes. Best practices for barcode usage ensure operations run smoothly and efficiently. Considerations in this area focus on elements such as label design, staff training, and regular audits. Each of these plays a crucial role in maximizing the benefits derived from barcode systems. They aid in reducing errors, improving accessibility, and streamlining workflows.
Label Design and Quality
The design and quality of barcode labels carry considerable importance. When labels are clear and durable, they are more likely to endure the wear and tear of a busy warehouse. Essential factors to consider include:
- Clarity: Barcodes should be easy to scan. If not properly printed, they may lead to scanning errors.
- Durability: Labels must withstand various warehouse environments, like high humidity or extreme temperatures. Materials like polyester or vinyl often provide durability.
- Size: Barcodes should not be too small. This can result in scanning difficulties. Standard sizes, when possible, should be adhered to for consistency.
Paying attention to these elements ensures that barcodes maintain functionality over time. Investing in high-quality label printers can also enhance barcode effectiveness in the long term.
Training Warehouse Staff
Staff training is paramount in utilizing barcode systems efficiently. Employees must understand not only how to use the equipment but also the significance of accurate data entry. Key components include:
- Hands-On Training: Programs should be interactive, allowing staff to use scanners in real-life situations.
- Continual Learning: Regular update sessions to reflect improvements in technology or procedures are critical.
- Understanding Data: Employees should recognize the value behind the scanned information, increasing their awareness of inventory accuracy.
Ultimately, a well-trained workforce minimizes human error and maximizes the system's efficiency by enhancing overall operational performance.
Regular System Audits
Conducting regular audits of the barcode system is crucial. This ensures that the scanning technology is functioning correctly and that the data remains accurate. Areas to focus on during audits include:
- Inventory Checks: Regular comparisons of scanned data with actual stock levels can highlight discrepancies.
- Equipment Maintenance: Scanners and printers should be checked for malfunctions or wear. Addressing issues promptly extends the lifespan of these devices.
- Process Evaluation: Reviewing scanning processes and user feedback can lead to valuable insights for improvement.
Regular system audits serve to catch potential problems early, maintaining the integrity of the barcode system and ensuring optimal performance.
"Investing in best practices for barcode usage can turn an average warehouse into an efficient hub of operation."
Challenges in Barcode Implementation
The integration of barcode systems into warehouse management is not without its challenges. While the adoption of barcodes brings numerous benefits, understanding the obstacles is essential for effective implementation. Identifying these challenges enables businesses to prepare and adapt strategies that enhance the success of barcode technology in their operational processes.
Common Obstacles
Warehouse managers often encounter several specific obstacles during barcode implementation. Some of these challenges include:
- Inadequate Infrastructure: Many warehouses may not have the necessary technological backbone to support barcode systems. This involves both hardware, such as scanners and printers, and software for inventory management.
- Employee Resistance: Staff may resist adopting new technologies due to fear of change or lack of understanding. This can result in suboptimal usage of the barcode system.
- Data Management Issues: Keeping track of large volumes of data can be overwhelming. Mismanagement of data can lead to system failures and loss of accuracy.
- Cost Concerns: Businesses often worry about the costs associated with implementing a new system, including training and ongoing maintenance.
Effective planning can help address these and other challenges with barcode integration.
Mitigation Strategies
To overcome the hurdles associated with the implementation of barcode systems, several effective strategies can be employed:
- Conduct Needs Assessment: Evaluating the current processes and specific needs of the warehouse ensures that the selected barcode system aligns with operational goals.
- Invest in Training: Providing comprehensive training helps employees adapt to the new technology. Understanding how to effectively use barcode systems enhances overall productivity.
- Ensure Data Hygiene: Regular audits of stored data keep information accurate and up-to-date, minimizing errors related to data management.
- Start Small: Implementing the barcode system in phases allows for manageable transformation. This approach gives teams opportunities to learn and adapt before full-scale implementation.
- Calculate Total Cost of Ownership: Understanding all costs involved, including long-term returns, can help in justified investments in barcode technology.
"Preparation and strategic planning are crucial in overcoming the barriers to barcode implementation, ensuring streamlined operations and accuracy in the long run."
By addressing these obstacles thoughtfully, warehouses can enhance the success of their barcode systems and gain significant operational advantages.
Integrating Barcodes with Emerging Technologies
Integrating barcode systems with emerging technologies is crucial for improving warehouse management processes. As the industry evolves, the demand for more efficient solutions intensifies. Barcodes, when combined with innovations like the Internet of Things (IoT) and artificial intelligence (AI), create a synergy that enhances operational efficiency and data accuracy. This integration allows businesses to optimize their supply chain and reduce errors significantly.
Barcode Systems and IoT
The Internet of Things represents a network of interconnected devices that communicate and share data. Combining barcode systems with IoT enhances the tracking and tracing of inventory within warehouses. Sensors connected to barcode scanners can monitor the movement of goods in real-time. This capability provides immediate visibility into inventory levels, reducing the chances of stockouts or overstock situations.
Using IoT in conjunction with barcode technology also facilitates automation. For example, when an item is scanned, the IoT system can automatically update inventory records in centralized software. This reduces the need for manual entry and minimizes human error.
Additionally, the data collected from connected devices can be analyzed to forecast demand better. This predictive capability allows companies to adjust their inventory accordingly, which leads to operational savings and increased responsiveness.
Utilizing AI for Inventory Management
Artificial intelligence significantly enhances the overall functionality of barcode systems in warehouses. AI algorithms can analyze historical and real-time data gathered from barcode systems to identify patterns in inventory movement. This analysis can lead to improved accuracy in inventory forecasting.
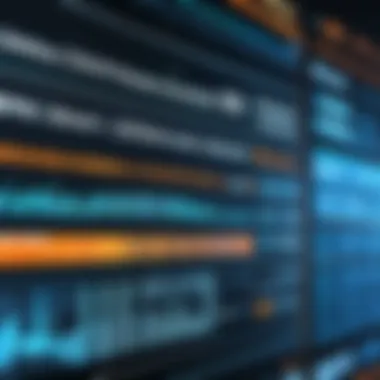
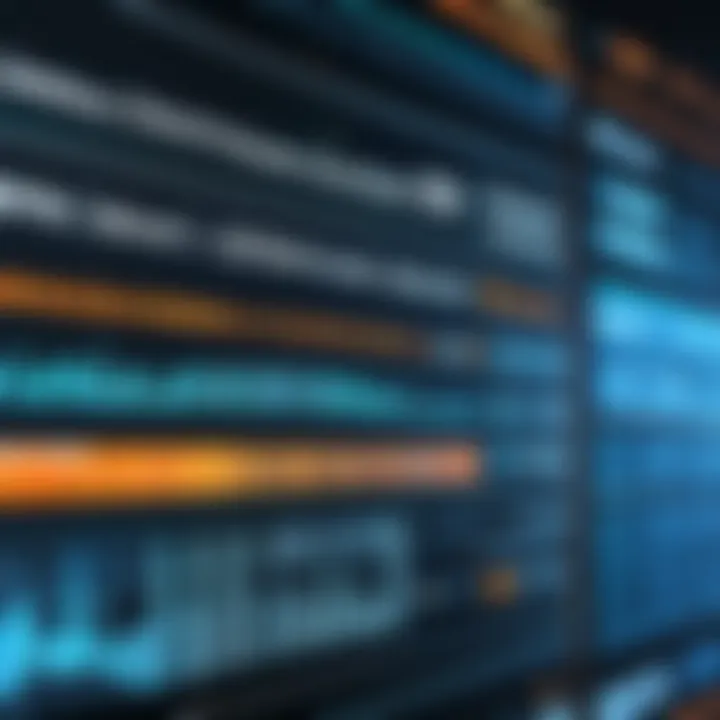
Moreover, AI can be employed to optimize storage configurations and improve pick routes within warehouses. By processing data from scans, AI systems can suggest the most efficient paths for picking2. As a result, warehouse staff can work more efficiently, which saves time and reduces labor costs.
Furthermore, the combination of AI and barcode systems can automate repetitive tasks, alerting staff to replenish stock just in time. This ensures that inventory levels are not only maintained but optimized based on actual needs.
"The integration of barcode systems with IoT and AI is not just about technology, but about transforming the entire operational landscape of warehouse management."
Integrating barcodes with emerging technologies leads to a smarter, more efficient warehouse environment. Decision-makers should recognize the value of these innovations, as they prepare to face the challenges of the future.
Case Studies and Real-World Applications
In the realm of warehouse management, case studies and real-world applications serve as powerful testaments to the efficacy of barcode systems. These examples provide valuable context and insight into how various organizations have utilized barcodes to enhance their operations. By examining specific scenarios, industry professionals can better appreciate the nuances involved in implementing barcodes and identify strategies that could apply to their own needs.
Many companies across diverse sectors have integrated barcode technology into their workflows, leading to significant improvements. For instance, in the retail sector, Walmart has long been recognized for its use of barcodes to track inventory. The retailer's ability to scan products at checkout and efficiently manage stock levels has set a benchmark in the industry. The data collected through barcode scanning allows Walmart to maintain optimal stock levels and reduce excess inventory, thus enhancing overall efficiency.
Similarly, in the logistics industry, FedEx employs barcodes extensively to monitor package movement. By scanning barcodes at each checkpoint, FedEx ensures that packages are tracked throughout their journey. The implementation of barcode systems reduces errors and provides real-time visibility into shipment status. This feature is essential for fast-paced logistics operations where precision is crucial.
Success Stories from Various Industries
The key to understanding the value of barcode technology lies in examining successful applications across different sectors.
- Healthcare: Hospitals and clinics have adopted barcode systems for patient safety and medication management. By scanning patient wristbands and medication labels, healthcare providers minimize the risk of errors in drug administration. This not only enhances patient outcomes but also ensures compliance with regulations.
- Manufacturing: Companies like General Motors use barcodes to streamline inventory and assembly line processes. The implementation of barcode tracking systems on parts reduces assembly time and ensures that the correct components are used in production, thus boosting overall quality control.
- Food Distribution: In the food industry, companies like Sysco use barcodes to manage perishable inventory. By efficiently tracking expiration dates and quantities, they can reduce waste and ensure that customers receive fresh products. The transparency brought by barcode systems allows better planning and forecasting.
These stories highlight how barcode systems have enabled industries to enhance efficiency, accuracy, and reliability in their operations. By learning from their experiences, decision-makers can develop informed strategies for implementing similar systems in their own organizations.
Lessons Learned
From these case studies, several lessons emerge that can inform future implementations of barcode technology.
- Prioritize Training: Successful adoption of barcode systems hinges on comprehensive training for staff. Companies that invest in training their workforce tend to experience smoother transitions and better overall outcomes.
- Emphasize Maintenance: Regular system checks and maintenance are crucial to ensure that barcode scanners and software are functioning optimally. Neglecting this aspect can lead to errors and operational disruptions.
- Choose the Right Technology: The selection of barcode technology must align with specific business needs. Whether it is 1D barcodes or QR codes, understanding the unique requirements of the operation is pivotal for success.
- Leverage Data: Gathered data from barcode systems provides valuable insights. Companies that analyze this data can make informed decisions that drive operational improvements.
In summary, the examination of case studies enhances the understanding of barcodes in warehouse management. The success stories across industries confirm the potential benefits, while the lessons learned guide future implementations with practical strategies.
Future Trends in Warehouse Management and Barcodes
The evolution of barcode technology is pivotal in the transformation of warehouse management. Understanding the future trends in this area is essential for decision-makers looking to enhance efficiency, reduce costs, and improve service quality. As industries embrace advancements in technology, the integration of barcodes into warehouse operations continues to provide significant benefits. These benefits span automation, improved data analytics, and enhanced operational visibility.
Automation in Warehousing
Automation reshapes many aspects of warehouse operations. The use of automated systems in conjunction with barcode technology can lead to substantial improvements in productivity. Various automated solutions, such as robotic picking systems, utilize barcodes to identify and locate products accurately. This capability not only reduces manual labor but also minimizes human error.
Barcodes can streamline processes like receiving, storage, and order picking. When an item arrives at the warehouse, scanning its barcode allows automated systems to determine its proper storage location instantly. This reduces processing times and accelerates the entire supply chain operation.
Moreover, with the integration of automated guided vehicles (AGVs), barcodes enable real-time tracking of inventory movements. AGVs equipped with barcode scanners can navigate through the warehouse environment autonomously, picking up goods and delivering them to designated areas without human intervention. This leads to significant time savings and enhances the accuracy of inventory management.
Key Points in Automation:
- Enhanced speed in order processing
- Reduction in labor costs
- Increased accuracy in inventory management
- Real-time data access for decision-making
Predictive Analytics and Barcode Data
Predictive analytics is becoming a vital tool for warehouse management. The data generated from barcode systems can be analyzed to forecast demand patterns, inventory levels, and optimize stock replenishment cycles. By utilizing historical data and market trends, warehouses can better prepare for fluctuations in demand.
For instance, retailers can analyze past sales data tagged with barcode information to predict future inventory needs accurately. This minimizes the risk of stockouts or overstock situations, leading to reduced carrying costs.
Integrating predictive analytics with barcode data also enhances decision-making capabilities. Real-time insights derived from barcode scanners allow managers to identify inefficiencies in their operations and act upon them promptly. By employing advanced analytics tools, companies can visualize their inventory turnover rates and adjust their strategies based on actionable insights.
"The ability to anticipate future trends and customer demands through barcode data is a game-changer for warehouse management."
Benefits of Predictive Analytics:
- Enhanced accuracy in inventory forecasts
- Reduced operational costs
- Improved stock optimization
- Data-driven decision-making processes
The End
The significance of integrating barcode technology into warehouse management cannot be overstated. This article emphasizes the transformative impact that barcodes have on inventory control, operational efficiency, and overall supply chain visibility. Each aspect of warehouse processes is enhanced significantly by adopting barcode solutions.
The Ongoing Evolution of Barcode Technology
Barcode technology is in a state of continuous change. New standards and formats are constantly being introduced to meet the demands of ever-evolving market needs. These advancements in barcode technology streamline operations further and create new possibilities for data tracking and management. Technologies such as RFID are supplementing traditional barcodes, offering additional dimensions of efficiency. The versatility of barcode systems enhances not only the speed but also the accuracy of inventory processes.
In the future, we expect to see greater interoperability among various barcode systems and improved integration with mobile technology. As businesses strive for more efficiency, the relevance of adopting up-to-date barcode solutions becomes particularly clear.
Final Thoughts on Warehouse Management Integration
Integrating barcode technology into warehouse management strategies is more than just an operational upgrade; it is a necessary evolution for businesses aiming to remain competitive. The benefits are multi-faceted, ranging from improved data accuracy to enhanced productivity.
Moving forward, decision-makers need to consider the long-term advantages of implementing comprehensive barcode systems. Proper training is essential for staff to realize the maximum potential of barcode technology. Furthermore, aligning barcode systems with warehouse management software creates a seamless operational flow that can adapt to changing demands and market conditions.
In summary, adopting barcode technology represents a vital step toward modernizing warehouse management, ensuring companies can meet future challenges effectively.