Essential Strategies for Equipment Maintenance Tracking
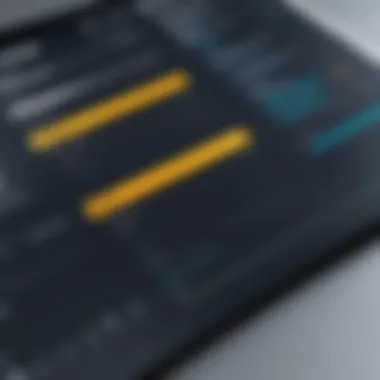
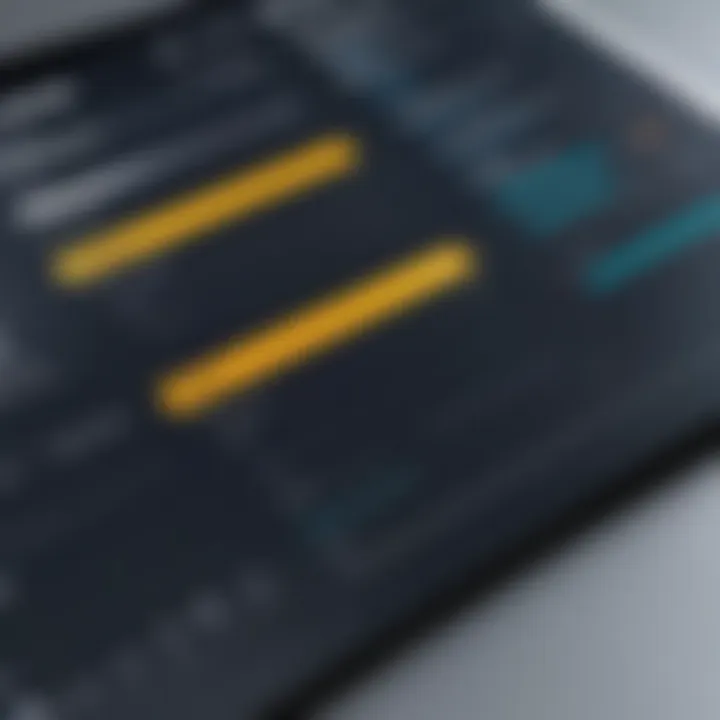
Intro
In today's fast-paced industrial landscape, where every second counts, effectively managing equipment maintenance has become a non-negotiable necessity. Equipment can take a real beating, and without proper tracking of maintenance activities, organizations risk facing unexpected downtimes, spiraling costs, and diminished productivity. This guide lays out a detailed roadmap to understanding the intricate processes of equipment maintenance tracking, aiming to furnish decision-makers, IT professionals, and entrepreneurs with essential insights necessary to tailor robust maintenance systems to their unique operational contexts.
Understanding maintenance tracking is not just about data collection; it encapsulates a strategic approach to maximizing efficiency and minimizing costs. As organizations strive to enhance their operational performance, this comprehensive guide highlights key methodologies and practices that can help in navigating through the maze of equipment management.
The topics explored, from essential strategies and tools to current best practices, cultivate a rich understanding that goes beyond superficial insights. Get ready to uncover the layers behind effective equipment maintenance while ensuring that your initiatives lead towards greater longevity of assets and sustainable cost management.
It is crucial, then, to take a closer look at the Key Features and Functionalities that encapsulate the essence of maintaining and tracking equipment.
Understanding Equipment Maintenance Tracking
Equipment maintenance tracking is more than just a checkbox on a to-do list; it’s a vital cog in the larger machinery of any operational setup. In a world where efficiency is king and cost is the throne it sits upon, understanding what this tracking entails can make or break an organization’s profitability and smooth functioning.
To put it simply, equipment maintenance tracking refers to the systematic approach to monitoring and recording the upkeep of machinery and tools. This includes everything from scheduling regular inspections to logging repairs and replacements, essentially laying the groundwork for minimizing downtime and extending the lifespan of assets.
Definition and Importance
In its core essence, equipment maintenance tracking involves the collection, organization, and analysis of data relevant to the performance and upkeep of machinery. This can include metrics like total operational hours, frequency of maintenance events, or any unscheduled repairs. Though these might seem like mundane details, they pack a punch when it comes down to decision-making.
The importance of this process is manifold:
- Enhanced Reliability: By keeping a close eye on maintenance schedules, organizations can avoid the pitfalls of unexpected equipment failures.
- Cost Savings: Routine maintenance often costs less than emergency repairs. Integrating a robust tracking system can reveal patterns that help in prioritizing preventative measures.
- Compliance and Safety: Many industries are governed by strict regulations requiring documented maintenance. A well-implemented tracking system ensures organizations stay in the good graces of regulators.
By acknowledging these factors, decision-makers can appreciate the foundational role of equipment maintenance tracking in maintaining operational continuity and reducing costs.
Historical Context
Equipment maintenance has roots that run deep in the chronicles of industrial evolution. In earlier days, maintenance often took a backseat until something broke. Managers might have slapped a band-aid on a machine rather than investing in ongoing support. This reactive approach often led to increased downtimes, higher operational costs, and frustrated employees who relied on machinery to complete their tasks.
However, as businesses grew, so did the awareness of the importance of taking a proactive stance. The 20th century heralded the dawn of planned maintenance strategies, influenced by military practices that focused on readiness and efficiency. The lean manufacturing revolution of the late 20th century further emphasized maintaining equipment to support just-in-time production cycles. It was during these pivotal moments that tracking systems began to evolve, leading to the modern software and methodologies we see today.
Now, organizations have access to sophisticated tracking tools that actively monitor equipment performance, schedule maintenance, and provide analytics all rolled into one. These developments, along with increased connectivity through IoT and data analytics, have transformed maintenance tracking from a necessary evil into a strategic asset that speaks volumes about an organization’s commitment to operational excellence.
Key Components of Maintenance Tracking
In the realm of equipment maintenance, having a solid foundation of key components is crucial. Each element plays a significant role in ensuring that systems function smoothly and efficiently. If you think about it, maintenance tracking is akin to a well-oiled machine itself; when all parts move in harmony, the overall system thrives, reducing downtime and saving resources. Let’s break down the primary components that form this intricate network.
Inventory Management
An effective maintenance tracking system begins with robust inventory management. This involves keeping an updated list of all equipment, tools, and spare parts required for maintenance tasks. Think of it as a pantry at home; if you know what you have and what you need, meal prep— or in this case, maintenance—becomes a whole lot easier. This practice not only prevents overstocking or running out of necessary supplies but also helps identify components that need replacing before they become a bottleneck.
- Benefits of Inventory Management:
- Reduces costs associated with emergency purchases.
- Helps avoid downtime that can occur due to unavailable parts.
- Simplifies the planning of regular maintenance activities.
In short, when you're in control of your inventory, you’re step ahead; you can plan maintenance like clockwork.
Maintenance Scheduling
Next up is maintenance scheduling, perhaps one of the most vital cogs in the maintenance tracking wheel. Scheduling means creating a timetable for regular inspections, repairs, or upgrades based on manufacturer recommendations or historical performance data. A proactive approach can often ward off future headaches. Imagine waiting until your car breaks down to get an oil change; that’s not just bad timing, it’s inefficient.
By sticking to a solid schedule:
- Preventative Maintenance is prioritized: Instead of reactive measures, you can tackle issues before they snowball.
- Operational Clarity is achieved: Team members know exactly when equipment will be down and can plan their workload accordingly.
- Safety and Compliance are ensured: Keeping equipment well-maintained is often not just a best practice, but a regulatory requirement in many industries.
Essentially, the foresight provided by a well-planned maintenance schedule is an invaluable asset to any organization.
Documentation Practices
Last but not least comes documentation practices. This involves systematically recording everything from repairs and inspections to changes in equipment. Strong documentation serves multiple purposes: it builds a history that can be invaluable for future maintenance decisions and supports compliance efforts in regulated industries. You can picture it like keeping a diary; every note helps you recall past events, and that understanding arms you with insights for the future.
Good documentation practices include:
- Accurate Record-Keeping: Every maintenance action should be logged; this allows for trend spotting and identifying issues before they escalate.
- Accessible and Organized Information: With a proper structure, anyone in the team can quickly find the data they need without rummaging through piles of paperwork.
- Regular Reviews: Conducting periodic reviews of the collected data can lead to improved maintenance strategies and process enhancements.
The accuracy and transparency offered by sound documentation can’t be overstated. It’s about more than just ticking boxes; it provides a backbone to your maintenance strategy.
"Well-maintained equipment is not just a luxury; it’s a necessity for maximizing productivity and minimizing costs."
In summary, understanding and implementing these key components—inventory management, maintenance scheduling, and documentation practices—sets the stage for an effective maintenance tracking system. Each piece of the puzzle working together ensures that organizations can maintain their equipment efficiently, ultimately leading to enhanced performance.
Technological Advancements in Maintenance Tracking
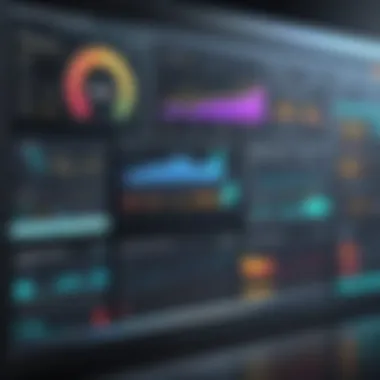
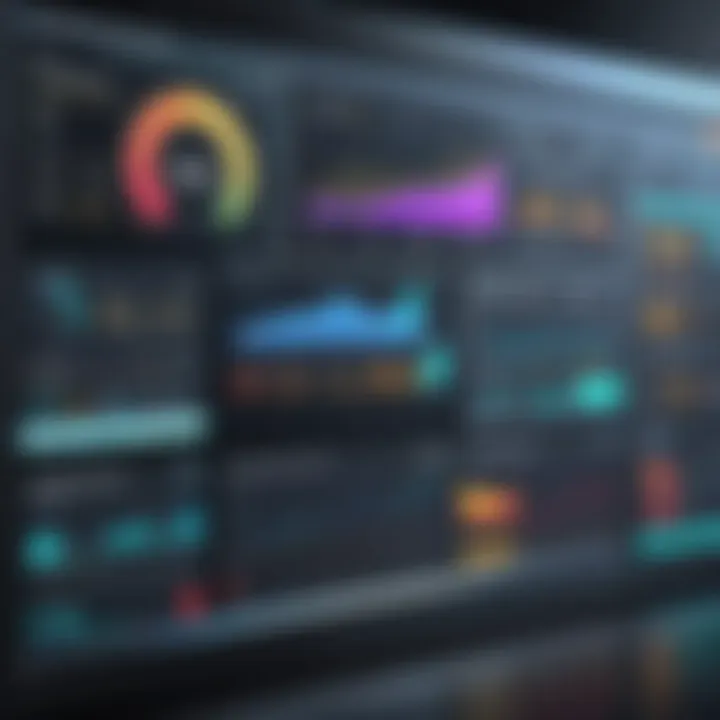
Over the years, the landscape of maintenance tracking has evolved tremendously, propelled by technological advancements. Modern tools and systems allow companies to keep tabs on equipment more effectively than ever before. These innovations are not just about introducing shiny gadgets; they bring tangible benefits that can greatly enhance operational efficiency and cost-effectiveness. Understanding the importance of these advancements can lead to smarter decision-making when implementing maintenance tracking practices.
Software Solutions
In today’s digital age, software plays a central role in equipment maintenance tracking. Solutions such as Computerized Maintenance Management Systems (CMMS) streamline processes by automating tasks that were once manual and time-consuming. These systems can track everything from scheduled maintenance to asset history. With user-friendly dashboards, decision-makers can easily visualize maintenance workflows and spot trends.
For instance, a company might utilize Fiix Software or UpKeep which allow users to manage work orders, create maintenance schedules, and monitor equipment health all in one place. The flexibility to generate reports automatically helps organizations analyze performance metrics, ultimately leading to better resource allocation. Implementing the right software isn’t just a convenience; it’s a smart business move that can yield high returns.
IoT Integration
The advent of the Internet of Things (IoT) has introduced a new level of connectivity in equipment maintenance. Sensors embedded in equipment can relay real-time data about performance and condition directly to maintenance teams. This means issues can be detected before they escalate, allowing for timely interventions that mitigate downtime and save costs.
For example, in a manufacturing setting, machines equipped with IoT devices can alert staff when parts are wearing out or require attention. A system like GE Digital's Predix can help in collecting and analyzing this data, leading to what’s known as predictive maintenance. IoT integration changes the game not only by enhancing monitoring capabilities but also by enabling a proactive approach in maintenance strategies.
Data Analytics Utilization
Data analytics adds another layer of sophistication to maintenance tracking. Companies can collect vast amounts of data from various sources, but without proper analytics, that data is little more than noise. By utilizing data analytics, organizations can sift through this information to identify patterns and correlations that might not be immediately obvious.
Using tools like Tableau or Power BI, a company can visualize trends in maintenance activities, helping prioritize tasks based on urgency or frequency. Moreover, predictive analytics can forecast when equipment is likely to fail, which allows maintenance teams to make informed decisions. As the saying goes, "knowledge is power," and when it comes to equipment maintenance, leveraging data effectively can empower organizations to optimize their operations.
"Harnessing technology in maintenance tracking is not just about keeping equipment running; it's about making informed decisions that drive efficiency and cost savings."
Through these advancements, businesses can transform their maintenance strategies from reactive to proactive, laying the groundwork for sustainable growth in a competitive landscape.
Benefits of Effective Maintenance Tracking
Gathering and analyzing data on equipment maintenance is more than just keeping a tidy schedule. The benefits of effective maintenance tracking permeate every corner of operational effectiveness, ensuring that resources are used wisely and equipment functions optimally for the long haul. When organizations embrace a structured approach to maintenance tracking, they unearth a treasure trove of advantages. Below, we dive into three critical benefits: cost reduction, increased equipment lifespan, and enhanced operational efficiency.
Cost Reduction
One of the most immediate benefits of effective maintenance tracking is the potential for significant cost reduction. Maintaining a clear record of maintenance activities helps identify patterns and trends that could lead to financial savings. For instance, regularly scheduled inspections allow issues to be caught while still minor, preventing them from escalating into expensive breakdowns. Breakdowns are not just costly in terms of repairs but can also have broader effects, such as lost productivity and revenue.
Cost-saving strategies include:
- Preventive maintenance: Doing maintenance work at set intervals based on equipment usage rather than waiting for a failure.
- Resource optimization: By tracking maintenance, organizations can better allocate labor and materials, avoiding overstaffing or stockpiling of parts.
- Supplier relations: Having reliable records may lead to stronger relationships with suppliers, paving the way for bulk discounts and better pricing on necessary elements.
In light of these factors, organizations that invest in maintenance tracking not only save money but also position themselves for strategic financial planning.
Increased Equipment Lifespan
Tracking equipment maintenance diligently can also significantly extend its operational life. When machinery and tools are kept in peak condition, they naturally experience a slower rate of degradation. Equipment that undergoes routine checks, adjustments, and repairs will likely run smoother, leading to a more productive lifecycle.
Key points to consider in this context:
- Timely repairs: Addressing wear and tear before it progresses ensures that machinery remains reliable.
- Manufacturer recommendations: Sticking to predefined schedules according to manufacturer guidelines can enhance durability and reduce unnecessary replacements.
- Quality of service: A well-maintained piece of equipment is more likely to perform efficiently, resulting in fewer surprises and more predictable operations.
Overall, fostering a culture of meticulous maintenance tracking cultivates an environment where equipment thrives and runs optimally, saving costs associated with replacements and emergency repairs.
Operational Efficiency
The effectiveness of any organization hinges not only on what it does but how it does it. Good maintenance practices lead to operational efficiency, which plays a crucial role in driving value across various sectors. Equipment that is efficiently monitored allows for smooth workflows, helping to eliminate bottlenecks that could derail productivity.
Consider the following aspects that highlight operational efficiency:
- Data-driven decision-making: The insights gleaned from maintenance tracking empower decision-makers to make informed choices regarding replacements, upgrades, and resource allocation.
- Minimized downtime: Predictive maintenance alerts help in scheduling repairs during off-peak hours, thus reducing the impact of equipment unavailability on production flows.
- Employee morale: When equipment operates reliably, employee satisfaction often improves, as workers can execute tasks without dealing with faulty tools or machinery.
In summary, effective maintenance tracking is not merely an administrative task—it's part of a broader strategy to create efficiencies and sustainable procedures within an organization.
By leveraging the benefits of a comprehensive maintenance tracking system, businesses can significantly decrease costs, prolong equipment life, and improve overall operational efficiency.
Challenges in Maintenance Tracking
Understanding the challenges in maintenance tracking is crucial for any organization looking to optimize its equipment management processes. The maintenance tracking system can effectively sustain productivity, but various hurdles can impede the journey toward seamless execution. Addressing these issues not only paves the way for smoother operations but also enhances the longevity of critical equipment. Below, we delve into specific challenges faced in data management, skill gaps, and system integration.
Data Management Issues
Inadequate data management is like trying to navigate without a map - it leads to confusion and inefficiencies. Compiling accurate data on maintenance activities, equipment conditions, and service history is fundamental. However, businesses often struggle with inconsistency in data entry, leading to inaccuracies that can be costly.
For example, when a technician logs information about maintenance performed on a generator, inconsistent formats or ambiguous descriptions can arise. If a follow-up technician cannot comprehend what's been recorded, it could lead to overlooking critical repairs. To combat this, organizations should establish standardized data entry protocols to ensure uniformity across all maintenance logs. In addition, implementing real-time data capture tools can greatly improve the accuracy of data collection.
- Utilize cloud-based platforms for immediate data accessibility.
- Regular audits of information quality can catch errors before they escalate.
"Accurate data is the backbone of any successful maintenance strategy; without it, decision-making becomes a shot in the dark."
Skill Gaps in Workforce
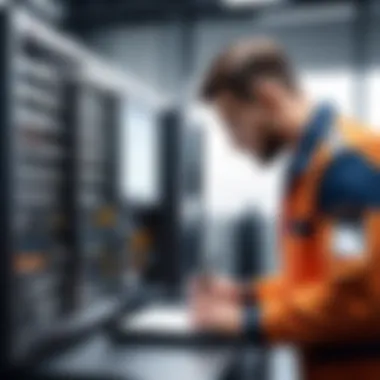
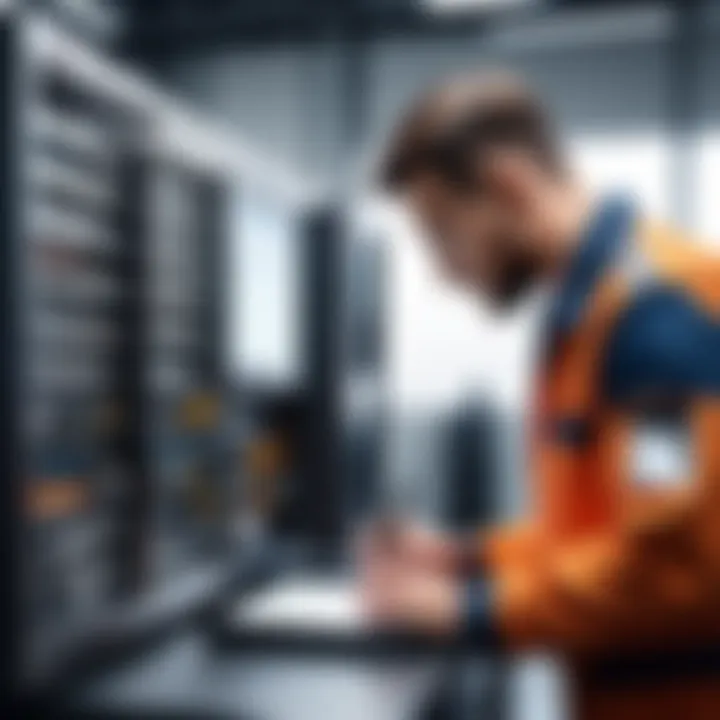
A well-trained workforce is indispensable for effective maintenance tracking. However, many organizations encounter significant skill gaps among employees handling the maintenance processes. The lack of knowledge regarding proficient usage of tracking systems or understanding equipment nuances can hinder overall efficiency.
For instance, a technician familiar with traditional maintenance practices may not be adept at utilizing modern software solutions. This gap not only results in delayed maintenance responses but can also negatively impact the equipment's health. To bridge this divide, companies ought to implement robust training programs. Regular workshops and practical training sessions can empower employees with the essential skills needed.
- Evaluate employee competencies regularly.
- Foster a culture of continuous learning and adaptability.
Integration with Existing Systems
Integrating new maintenance tracking systems with existing operational frameworks poses a considerable challenge. Companies often face resistance when adopting new technologies due to a fear of disruption. This hesitance can delay upgrades necessary for keeping maintenance practices contemporary.
If a factory utilizes a legacy inventory management system, introducing a new maintenance tracking system could lead to data silos or inconsistent information. To facilitate smoother integration, businesses should perform a thorough analysis of existing systems. Additionally, gradual implementation can ease the transition.
- Consider phased rollouts to minimize disruptions.
- Ensure that new systems are compatible with current workflows.
Implementing a Maintenance Tracking System
Implementing a maintenance tracking system isn't just yet another task on a to-do list; it's the bedrock of operational excellence for any organization that relies on equipment. Proper maintenance tracking can help avoid unforeseen breakdowns that derail productivity. Without a rigorous system in place, the costs of reactive maintenance can skyrocket, draining both budgets and time.
One important aspect here involves understanding your unique operational needs, which is especially crucial in racially diverse work environments. This requires a keen assessment of what equipment needs regular upkeep and the frequency of these maintenance tasks. A well-thought-out tracking system can lead to safer work environments, consistent performance, and ultimately, prolonged equipment life.
Identifying Requirements
At the outset, identifying requirements forms the foundation for a successful maintenance tracking system. You can't set sail without knowing where you're going, after all. Start with a thorough inventory of all equipment and its unique maintenance needs.
- Type of Equipment: Different machines have different needs. For instance, a hydraulic press operates on entirely different schedules compared to a CNC machine. Understanding these nuances is paramount.
- Frequency of Maintenance: Some equipment may need inspection weekly, while others might require annual checks. Having a clear schedule minimizes downtime and maximizes productivity.
- Regulatory Compliance: Be aware of industry standards that may dictate specific maintenance routines. Ensure your tracking system accounts for compliance with these regulations.
Crafting a clear and detailed requirements list will go a long way in ensuring the system you choose will meet the needs of your organization.
Choosing the Right Software
Once you’ve figured out your requirements, the next logical step is selecting the right software. A plethora of options exists, and as the saying goes, not all that glitters is gold.
- Scalability: Make sure the software can grow alongside your business. Sometimes, what starts as a small operation can expand rapidly.
- User-Friendly Interface: Even the most feature-packed software can be useless if employees struggle to navigate it. Opt for an intuitive design that facilitates a smooth learning curve.
- Integration Capabilities: Your chosen software should play nicely with existing systems. If it can’t connect smoothly with inventory management tools or ERP systems, it might create more problems than it solves.
The decision here should not be rushed. Take your time, read reviews, and, if possible, utilize trial versions before committing.
Training Staff and Management
Your newly implemented system is only as good as the people using it. Training is absolutely vital in this aspect. If operational staff don’t understand how to use the new software, it's like owning a brand-new sports car without knowing how to drive it.
- Comprehensive Training Sessions: Arrange for in-depth training sessions that cover all functionalities of the maintenance tracking system. Having subject matter experts lead these sessions can lend a layer of credibility.
- Regular Refresher Courses: As new features roll out or as policies evolve, schedule periodic training sessions to keep everyone updated. This not only reinforces learning but creates an environment of continuous improvement.
- Fostering a Feedback Loop: Encourage operators to voice their thoughts on the system. Their on-the-ground experience can help tailor the system more to daily operational needs, thus optimizing it further.
In sum, the implementation of a maintenance tracking system is crucial. The effort invested at each stage—whether identifying what’s needed, selecting the software, or training your team—will pay dividends in operational efficiency and cost management.
"Properly maintained equipment is essential for operational longevity. The emphasis shouldn't just be on fixing things when they break but on preventing breakage altogether."
Achieving this balance paves the way to smoother operations and a healthier bottom line.
Best Practices for Maintenance Tracking
Established practices often make the difference between a smoothly running operation and one riddled with costly, unexpected downtime. It’s vital to understand that maintenance tracking isn’t merely a set of tasks to tick off a list. Instead, it’s a comprehensive approach that can streamline processes, safeguard investments, and enhance the overall effectiveness of equipment management. Adopting best practices for maintenance tracking guarantees every piece of equipment receives the attentive care it needs, leading to better operational performance and financial viability.
Regularly Scheduled Inspections
Regular inspections stand as a cornerstone of effective maintenance tracking. These inspections shouldn’t be a sporadic event but rather a structured part of an organization’s routine operations. When inspections are scheduled regularly, it creates a rhythm that allows potential issues to be identified and addressed long before they escalate into major problems.
Imagine a manufacturing plant that conducts inspections every two weeks. This allows technicians to spot wear and tear on machines before they break down, saving both time and money in repairs. To formalize this process, consider drawing up a check-list or a maintenance calendar, ensuring that nothing slips through the cracks.
- Benefits of Regular Inspections:
- Identifies wear patterns of equipment.
- Reduces the likelihood of unplanned downtime.
- Extends the life of the equipment.
Additionally, inspections can serve as an opportunity for training. Technicians performing inspections can refresh their knowledge on equipment operation and maintenance procedures. The better informed they are, the more effective they’ll be at identifying problems.
Utilizing Automated Alerts
In today’s fast-paced environment, relying on human memory alone isn’t enough. Automated alerts have transformed the way organizations approach maintenance management. By utilizing a system that sends reminders and notifications, decision-makers can ensure that nothing gets overlooked.
A simple alert can notify staff when a piece of equipment is due for its next maintenance check, creating a proactive rather than reactive maintenance culture. Furthermore, automated tracking systems can analyze data and report on trends, flagging anomalies that might require immediate attention.
Here are some notable advantages of automated alerts:
- Helps in timely response to maintenance needs.
- Reduces reliance on human oversight.
- Allows for data-driven decisions based on alerts.
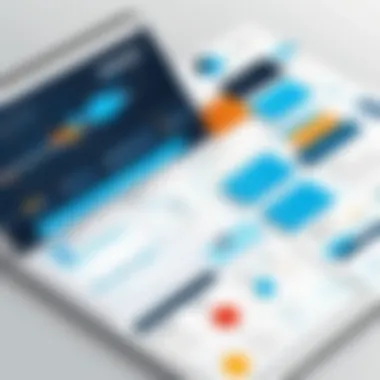

The integration of automated alerts can also grant management insight into equipment usage patterns, optimizing maintenance schedules and reducing unnecessary costs.
Continuous Training
The landscape of technology is constantly evolving. Hence, continuous training should not be just a box to check off but rather a fundamental component of maintenance tracking practices. Only those who stay updated on the latest equipment and maintenance practices can handle the responsibilities of maintenance effectively.
A maintenance technician might, for instance, receive ongoing training on new diagnostic tools or software systems as part of their development. By providing training, organizations boost employee confidence, reduce errors, and enable staff to embrace new technologies with ease.
- Strategies for Continuous Training:
- Offer workshops and seminars.
- Create an internal training program.
- Encourage attendance at industry conferences.
These training efforts benefit the overall organization by developing a culture of learning and adaptability. Staff members who feel empowered are less likely to miss critical maintenance needs, ultimately safeguarding company assets and improving efficiency.
"A well-trained workforce can significantly enhance the effectiveness of any maintenance tracking system, yielding results that go beyond just preventing equipment failure.”
Case Studies of Successful Implementations
When it comes to understanding the practical outcomes of equipment maintenance tracking, case studies stand as crucial evidence. They reveal how various sectors have effectively adopted tracking systems to drastically improve their workflows, reduce costs, and enhance equipment longevity. By examining real-life implementations, decision-makers can better appreciate the effectiveness of certain strategies and systems, while also learning from both successes and challenges faced by their peers. This section will navigate through three distinctive examples across different industries: manufacturing, healthcare, and transportation.
Manufacturing Sector Examples
In the manufacturing world, precision and uptime are the names of the game. A notable example is the implementation of a maintenance tracking system at a mid-sized automotive parts manufacturer. Faced with frequent machinery breakdowns due to lack of scheduled maintenance, the company opted for a digital tracking solution to monitor equipment health.
- Key Features Utilized:
- Automated Alerts: Ensured that maintenance personnel received notifications ahead of scheduled maintenance, reducing the likelihood of unexpected failures.
- Data Integration: By integrating machine sensors with the tracking software, the company could collect real-time data on performance.
The result? A 40% reduction in unplanned downtime and significant savings on repair costs. More importantly, the company could allocate maintenance resources more efficiently, further elevating productivity in an already competitive market.
Healthcare Equipment Maintenance
In healthcare, the stakes are even higher. Patient safety and equipment reliability are paramount. A prominent case in this sector was a large hospital that adopted a centralized maintenance tracking system for its medical devices. Historically, each department managed its own equipment schedules, leading to inconsistencies and missed maintenance.
- Implementation Insights:
- Centralized Database: The hospital created a single database that recorded all equipment specifications, maintenance histories, and compliance statuses.
- Staff Training: Continuous training programs for staff on this system ensured that everyone was on the same page regarding equipment handling and maintenance.
The results were immediate and profound. The hospital experienced a dramatic decrease in equipment-related incidents (some even measure it in terms of patient outcomes), plus significant cost savings, allowing it to redirect funds toward patient care.
Transportation and Fleet Management
Fleet operations depend heavily on the reliability and performance of vehicles. One illustrative case involved a logistics company that managed a fleet of delivery trucks. After experiencing escalating maintenance costs and delayed deliveries, the company turned to a maintenance tracking solution tailored for fleet management.
- Critical Features:
- Predictive Maintenance: Utilizing data analytics, the system could predict when a vehicle would likely require servicing, based on usage patterns.
- Driver Feedback: Features enabled drivers to report issues directly, improving communication between drivers and maintenance teams.
After implementing these updates, the organization reported a remarkable 30% reduction in maintenance costs and a 20% boost in on-time deliveries. They achieved not only operational cost efficiencies but also improved customer satisfaction—a crucial element in the transportation sector.
"By learning from the experiences of others, an organization can avoid the pitfalls that others have encountered and tailor a solution that meets their unique needs."
In sum, these case studies are more than just numbers; they reflect real improvements in accountability, efficiency, and cost savings resulting from effective equipment maintenance tracking. Whether you're in manufacturing, healthcare, or fleet management, the lessons learned from these implementations can offer valuable insights for your operational strategies.
Future Trends in Maintenance Tracking
The landscape of equipment maintenance tracking is shifting, steered by technological innovations and evolving industry standards. This section explores the future trends that hold significant importance for decision-makers and IT professionals alike. Understanding these trends allows organizations to adapt and harness the advantages they offer, ensuring systems are not just efficient but also forward-thinking.
AI and Machine Learning Applications
Artificial Intelligence (AI) and machine learning are taking the maintenance tracking world by storm. These technologies can analyze vast amounts of data quickly and accurately, identifying trends that manual tracking might miss. For instance, an AI algorithm can predict when a machine is likely to fail based on historical performance data. This predictive capability enables proactive maintenance, reducing downtime and costs associated with unexpected repairs.
Moreover, AI can recommend the best course of action for maintenance tasks based on predictive insights. This empowers technicians with data-driven decisions, thus enhancing the overall efficiency of the maintenance processes. It’s like having a personal assistant that never sleeps, always on the lookout for potential issues and ready to deliver insights at a moment’s notice.
Predictive Maintenance Strategies
Predictive maintenance has emerged as a key strategy that can minimize expenses and improve equipment reliability. By leveraging data analytics and real-time monitoring, organizations can pinpoint when maintenance tasks should be carried out, rather than relying on time-based schedules.
Instead of waiting for a machine to break down, decision-makers can plan maintenance during non-peak hours, thus conserving resources and time. This strategy aligns perfectly with the trend towards data-driven decision-making.
For example, if vibration sensors on a turbine detect anomalies in operational patterns, alerts can be generated for immediate investigation. This approach not only saves money but also extends the lifespan of critical equipment.
Sustainability Practices
Sustainability is no longer just a buzzword; it’s a necessary component of modern business strategies. As organizations look to reduce their carbon footprint, integrating sustainability practices within maintenance tracking is crucial. It encompasses everything from energy-efficient machinery to reduction in waste generated during repairs and maintenance tasks.
For example, organizations can track the energy consumption of their equipment through specific software tools. By analyzing this data, they can identify which machines are performing inefficiently and either upgrade them or implement better maintenance routines.
"The key to the future is not just technology; it’s how we adapt and integrate it into our systems."
By focusing on these developments, industry leaders can ensure their maintenance practices do not just keep pace with change, but rather anticipate and thrive in it.