Understanding Siemens Teamcenter: A Comprehensive Guide
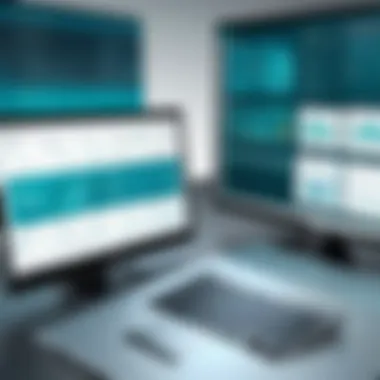
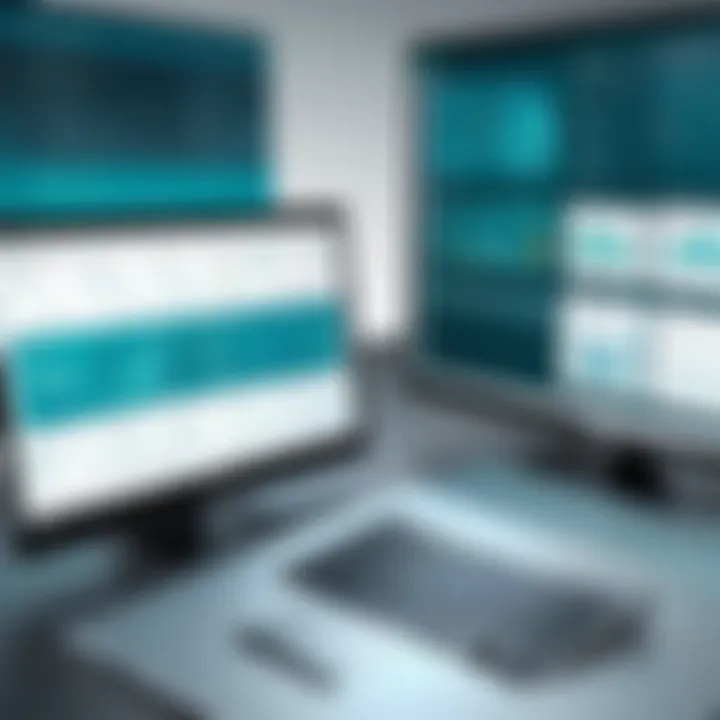
Intro
Siemens Teamcenter stands out in the realm of Product Lifecycle Management (PLM) software. It aids organizations in managing their product development processes effectively. This system streamlines operations from conception to production and beyond, providing an organized framework that supports collaboration and decision-making.
With the growing complexity of products and the need for rapid innovation, understanding how Teamcenter functions becomes crucial for professionals in various industries. It is not just about storing information; it is about integrating that information into a usable platform that fosters efficiency and accuracy.
In this article, we will explore the essential features that make Siemens Teamcenter valuable. We will also discuss its applications and how it enhances the user experience in product management. Further, we will examine pricing models associated with this software and what professionals should factor into their overall cost analysis.
Key Features and Functionalities
Comprehensive Overview
Siemens Teamcenter encompasses a variety of key functionalities. It provides a centralized environment for managing product data. This includes:
- Document management: Store and manage documents efficiently.
- Change management: Control changes in products through comprehensive workflows.
- Collaborative tools: Facilitate communication among team members.
- Integration capabilities: Connect seamlessly with other enterprise systems and tools.
- Reporting tools: Generate insights and analytics on product performance.
These features empower teams to create products that meet customer needs while adhering to regulatory standards.
Target Users
The target users of Siemens Teamcenter are varied. They include:
- Engineering teams: Who require precise data to facilitate design and production.
- Project managers: Seeking oversight on project timelines and deliverables.
- Quality assurance teams: Who need to ensure compliance with industry standards.
- Executive leadership: Looking for insights that drive strategic decisions.
By catering to this diverse audience, Teamcenter transforms the way organizations collaborate, innovate, and succeed in their respective markets.
Pricing Models and Cost Analysis
Breakdown of Pricing Tiers
Understanding the pricing structure of Siemens Teamcenter is essential for organizations considering its implementation. The cost typically varies based on:
- Licensing model: Different options exist, including on-premise and cloud solutions.
- User tiers: Costs may differ based on user access levels, such as basic or advanced functionalities.
- Implementation services: Additional fees can apply for initial setup and training.
Organizations must assess their specific needs to choose the right pricing tier.
Additional Costs to Consider
Besides the primary cost of licensing, additional costs include:
- Maintenance fees: Regular updates may come at a charge.
- Training resources: Investing in training for staff to maximize benefits of the software.
- Integration costs: Potential expenses to connect Teamcenter with existing systems.
Being aware of these factors supports better financial planning for organizations looking at Siemens Teamcenter for their PLM needs.
"A comprehensive understanding of Teamcenter not only streamlines product development but can lead to significant competitive advantages in the market."
Preamble to Siemens Teamcenter
Siemens Teamcenter is a pivotal tool in the landscape of Product Lifecycle Management (PLM). Understanding its functionalities and role is essential for industry professionals looking to optimize product development processes. This section will elucidate the significance of Siemens Teamcenter, focusing on its key elements, benefits, and the considerations necessary for effective implementation.
Overview of Product Lifecycle Management
Product Lifecycle Management encompasses the management of a productβs entire lifecycle from inception, through engineering design and manufacturing, to service and disposal. Siemens Teamcenter facilitates this process by providing a centralized platform where all product-related information is stored. This comprehensive management leads to improved collaboration and efficiency across different stages of a product's journey. With a structured approach, companies can streamline operations, reduce costs, and enhance product quality, which ultimately positions them favorably in competitive markets.
Role of Siemens Teamcenter in PLM
Siemens Teamcenter serves as an integrative backbone for PLM. By connecting various functions such as design, engineering, and manufacturing, it delivers real-time visibility and control over product data. This integration aids in decision-making processes, allowing teams to work together more efficiently regardless of their geographical locations.
Some key roles of Teamcenter include:

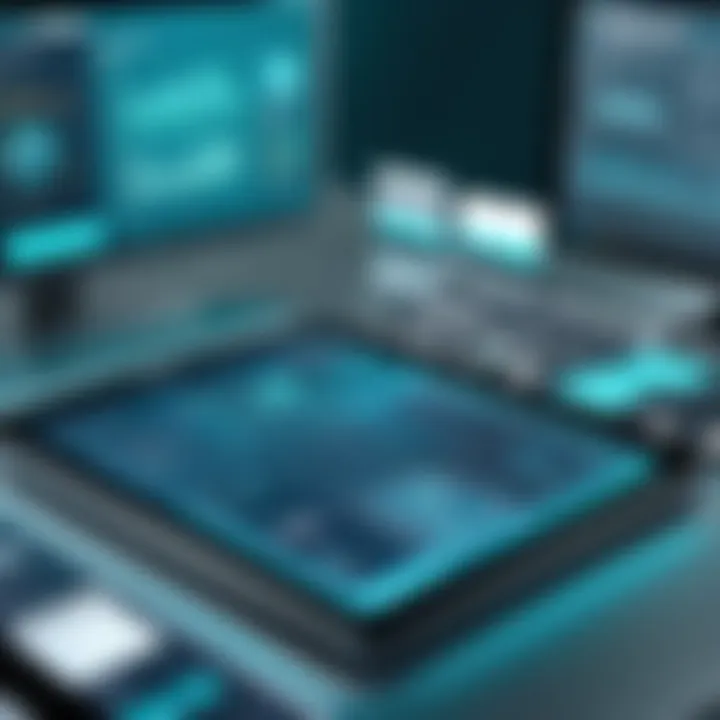
- Centralizing Information: All product information is stored in one place, reducing redundancies and ensuring everyone has access to the most current data.
- Enhancing Collaboration: Teamcenter enables different departments to collaborate seamlessly, fostering innovation.
- Facilitating Compliance: As products evolve, regulatory requirements change. Teamcenter helps businesses stay compliant by automatically updating relevant documentation.
- Supporting Change Management: Changes in design or manufacturing processes can be systematically managed, thereby minimizing risks associated with product updates.
"The integration capabilities of Siemens Teamcenter not only save time but also support agile product development, adapting to meet market demands quickly."
Core Features of Siemens Teamcenter
Siemens Teamcenter is a comprehensive tool designed for managing the complexities of product lifecycle management (PLM). Understanding its core features is pivotal for businesses looking to enhance their operational efficiency and streamline product development processes. These features enable organizations to handle large volumes of data, facilitate collaboration among teams, automate workflows, and manage changes effectively. Each of these elements contributes to reduced time-to-market, improved product quality, and increased innovation.
Data Management Capabilities
Data management is a critical aspect of PLM systems, and Siemens Teamcenter excels in this area. The software allows users to centralize all product-related information in a single, accessible location. This capability minimizes data silos and ensures that all stakeholders have access to the most current and accurate data.
Teamcenter's data management supports various file types, enabling integration of design documents, specifications, and other product-related materials. Version control features help track changes and maintain the integrity of information over time. These elements are crucial for compliance with industry standards and regulations, ensuring that all records are up to date and easily retrievable when needed.
Collaboration Tools
Collaboration is essential in product development as it involves multiple teams and stakeholders. Siemens Teamcenter provides robust collaboration tools that facilitate communication across departments. These tools enable real-time sharing of information, which is vital for making informed decisions promptly.
Features like discussion forums, document sharing, and project tracking keep teams aligned, enhancing overall productivity. With Siemens Teamcenter, users can comment on designs, share feedback, and track the progress of tasks, creating a more integrated working environment. The seamless collaboration also helps in reducing misunderstandings and ensuring that all parties are on the same page as the project evolves.
Workflow Automation
Workflow automation in Siemens Teamcenter significantly improves efficiency by streamlining processes that are often repetitive and time-consuming. The software allows organizations to define and automate workflows tailored to their specific needs. This function ensures that tasks are assigned correctly, deadlines are met, and resources are utilized effectively.
By automating routine processes, companies can reduce manual input and eliminate errors that typically arise from human involvement. Moreover, automated notifications and reminders enhance accountability among team members, thus promoting timely completion of tasks. This results in increased speed and efficiency in the product development lifecycle.
Change Management Features
Managing changes is a fundamental aspect of PLM, as modifications in design or specifications are common during development. Siemens Teamcenter offers robust change management features that enable organizations to handle product changes methodically. This includes tracking change requests, assessing impacts, and implementing changes effectively while maintaining previous versions.
The software allows teams to visualize the full impact of changes across associated documents, helping in decision-making. Furthermore, a structured process for change approval minimizes disruption and facilitates a clear process for evaluating the necessity and urgency of proposed changes.
"With Siemens Teamcenter, change management is not just about adjustments; it's about managing transitions without losing control."
Integrating these core features within Siemens Teamcenter represents a strategic advantage for organizations aiming to optimize their product development processes, ensuring they can adapt and thrive in a competitive landscape.
Integration Capabilities of Teamcenter
The integration capabilities of Siemens Teamcenter play a critical role in the overall effectiveness of Product Lifecycle Management (PLM). By enabling seamless interaction between various software tools and enterprise systems, Teamcenter enhances productivity and improves workflow efficiency. Such integrations are essential for organizations that rely on multiple software applications to manage their design, engineering, and business processes.
In the modern competitive landscape, it is vital for businesses to ensure that their processes are synchronized and that data flows unobstructed between departments. Teamcenter's integration capabilities allow companies to connect their design and engineering solutions with operational systems, thus eliminating silos and promoting collaboration across the board. The focus on integration greatly reduces chances of errors and ensures that all teams have access to the same up-to-date information.
Compatibility with CAD Systems
Compatibility with Computer-Aided Design (CAD) systems is one of the significant integration strengths of Siemens Teamcenter. Many engineering teams utilize various CAD tools to support their design processes. Teamcenter supports a broad range of CAD applications, allowing it to work seamlessly with popular platforms such as SolidWorks, CATIA, and Inventor. This compatibility ensures that design data can be transferred smoothly into the PLM system without manual intervention, thereby decreasing the likelihood of errors.
The ability to integrate with CAD systems offers numerous benefits:
- Real-Time Data Access: Teams can access design files in real time, which promotes quicker decisions and innovation.
- Streamlined Workflows: Designers can use their preferred CAD tools while still ensuring that their work is documented and managed within Teamcenter's capabilities.
- Comprehensive Traceability: Changes made within CAD applications are tracked and associated with the relevant project data, enhancing accountability.
Integration with ERP Solutions
Integration with Enterprise Resource Planning (ERP) solutions is another key feature of Siemens Teamcenter. ERP systems manage enterprise-wide resources such as inventory, finance, and supply chain. By linking these systems, Teamcenter creates a unified view of product information throughout the entire organization.
The benefits of integrating Teamcenter with ERP solutions include:
- Holistic Overview of Data: Users obtain a single source of truth, enabling them to make informed decisions based on a comprehensive set of information.
- Improved Resource Management: This integration leads to enhanced alignment between product development and operational efficiency, perhaps affecting everything from manufacturing schedules to cost management.
- Accelerated Time to Market: With synchronized data, teams can respond faster to market changes and customer requirements, which ultimately reduces product lead times.
It is clear that the integration capabilities of Teamcenter greatly enhance the tool's value proposition. Ensuring that various systems work together not only alleviates potential points of failure but also drives efficiency and innovation across the product lifecycle.
User Experience and Interface Design
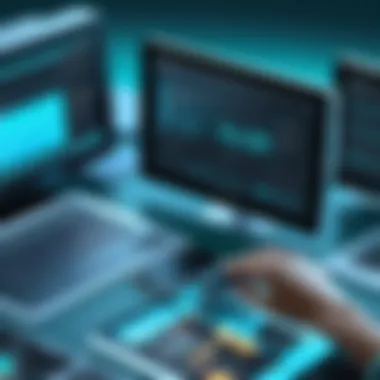
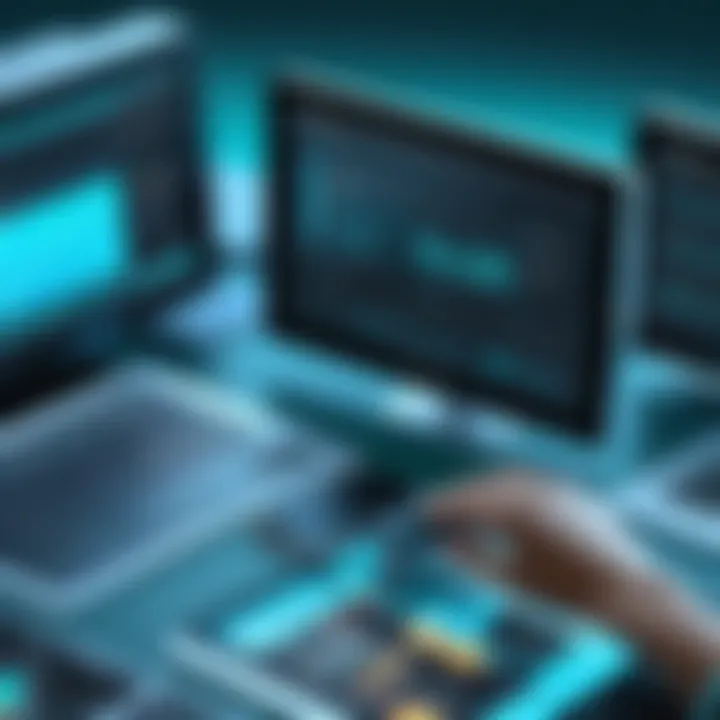
In the realm of product lifecycle management, the user experience and interface design of Siemens Teamcenter play a crucial role. A well-designed user interface directly impacts efficiency and user adoption. If the software is cumbersome or difficult to navigate, users are less likely to utilize its full potential. Hence, investing time in understanding the interface design can lead to significant improvements in productivity and collaboration within teams.
Navigation and Usability
Navigating through complex data and workflows can be a challenging task. Siemens Teamcenter addresses this with an intuitive layout that simplifies navigation. The interface is organized logically, which helps users find what they need quickly. Key functions such as searching for documents, managing workflows, and accessing tools are situated in easily accessible areas of the screen. This minimizes the time spent looking for features and maximizes productivity.
Usability is enhanced by the presence of consistent icons and clear labeling of functions. Users can adapt to the interface faster, reducing the learning curve associated with software. For IT professionals and decision-makers, understanding the layout serves as a basis for training users effectively and ensuring that the software is utilized to its fullest extent.
"A seamless user experience can significantly reduce training time and enhance overall operational efficiency."
Personalization Options
Personalization plays an important part in enhancing the user experience within Siemens Teamcenter. Users have different preferences and working styles. The software recognizes this need by offering various customization options. Users can modify dashboards to prioritize tasks that matter most to them. They can select widgets that provide real-time information or workflow summaries based on their role.
Moreover, settings can be adjusted to suit individual needs, such as changing the layout or the theme of the interface. This level of personalization enhances user satisfaction and engagement. When users feel that the tool is tailored to their personal workflow, it fosters a more meaningful connection to the software.
Industry Applications of Teamcenter
Understanding the industry applications of Siemens Teamcenter is crucial for organizations looking to enhance their product lifecycle management strategies. By employing a comprehensive PLM solution like Teamcenter, businesses can streamline operations, reduce time-to-market, and foster innovation. This section explores the key sectors where Teamcenter proves its value, including aerospace and defense, automotive, and consumer products. Each of these industries has unique requirements that Teamcenter can address, driving efficiency and effectiveness in product development and management.
Aerospace and Defense
The aerospace and defense industry is characterized by complex systems and stringent regulatory requirements. Here, Teamcenter serves as a critical tool, ensuring that all processes adhere to compliance standards. Its robust data management capabilities help in controlling documentation associated with certifications, making it easier for companies to meet the necessary legal obligations. With Teamcenter, teams can collaborate seamlessly across different departments and locations, facilitating a shared understanding of project status and requirements.
Moreover, the software allows for powerful configuration management, essential for tracking changes in design and engineering decisions. This capability is vital in aerospace and defense, where modifications can significantly impact safety and performance metrics.
Automotive Industry
In the automotive sector, where innovation is rapid, Teamcenter provides a backbone for effective product development. The automotive industry faces fierce competition, demanding efficient collaboration and quick responses to market changes. Teamcenterβs integration with CAD systems allows engineers to visualize design modifications in real-time. This immediate feedback fosters creativity and accelerates the development processes.
Additionally, automotive manufacturers benefit from change management features within Teamcenter. This ensures that all stakeholders are informed and aligned when changes occur. The result is a significant reduction in errors and a streamlined workflow. As a result, companies can improve their time-to-market performance, which is crucial in the auto industry.
Consumer Products
The consumer products industry is rapidly evolving to meet changing consumer demands. Teamcenter aids these companies in understanding market trends and consumer preferences, thus aligning product development with market needs. With its collaboration tools, teams can work on product concepts and marketing strategies in a unified platform, reducing the silos that often plague organizations.
Effectively managing product changes through Teamcenter is also vital for consumer brands. Quick shifts in consumer preferences require agile responses. Teamcenter's capabilities empower teams to iterate and adapt designs swiftly while maintaining the integrity of the product line. This adaptability is essential in an industry where brand loyalty can hinge on the latest trends and innovations.
"Siemens Teamcenter enables companies in various industries to align product strategies with market dynamics, ensuring greater success and sustainability."
In summary, Teamcenter plays a pivotal role across various industry applications. By providing tailored solutions for aerospace and defense, the automotive industry, and consumer products, it helps organizations optimize their workflows, enhance collaboration, and ultimately, drive product success.
Best Practices for Implementing Siemens Teamcenter
Implementing Siemens Teamcenter can bring significant advantages, but effective adoption requires careful planning and execution. Best practices play a vital role in ensuring a smooth transition and maximizing the utility of the software. Here we outline essential strategies that decision-makers and IT professionals can follow to realize successful implementations.
Initial Assessment and Planning
Before diving into the implementation of Siemens Teamcenter, it is crucial to conduct an initial assessment. This phase involves evaluating current processes, systems, and tools. Understanding existing workflows helps to identify gaps and areas needing improvement. It is also essential to define clear objectives aligned with business goals. Consider conducting workshops with stakeholders to gather insights. This process ensures that everyone understands how Teamcenter aligns with organizational strategy.
Effective planning follows the assessment. Develop a project roadmap detailing key milestones and timelines. Factor in resource allocation, as well as the budget. This roadmap not only guides the implementation process but also promotes accountability among team members.
Training Users Effectively
User adoption is a key determinant of the success of Siemens Teamcenter. A structured training program tailored to various user roles can significantly enhance proficiency. Utilize training resources from Siemens, such as user manuals and instructional videos, alongside interactive sessions led by expert trainers.
Consider a tiered training approach. Start with basic functionalities for new users and progressively introduce advanced features. Encouraging hands-on practice in a controlled environment helps users build confidence. Regular feedback sessions can identify additional training needs, ensuring continuous learning.
Continuous Improvement Strategies
Post-implementation, organizations should focus on continuous improvement strategies to maximize the benefits of Siemens Teamcenter. One effective method is to establish a feedback loop where users can share experiences and suggest enhancements. Regularly scheduled reviews of workflows and processes can highlight inefficiencies, leading to ongoing optimization.
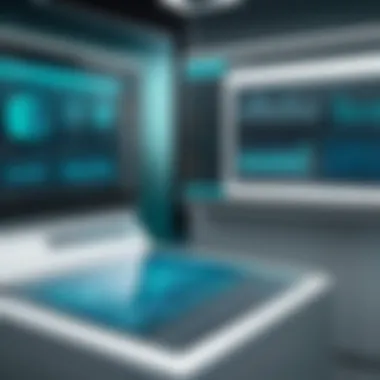
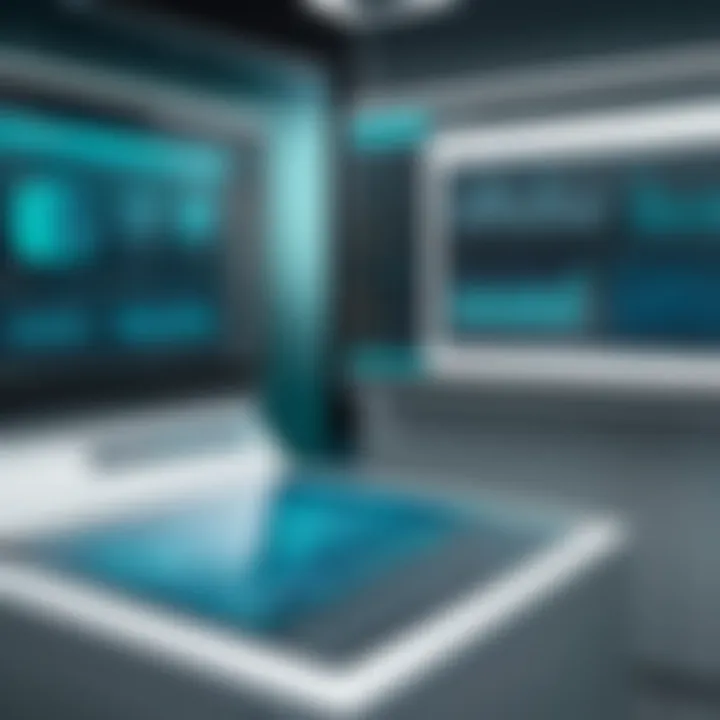
Emphasize the importance of keeping the software up-to-date with the latest features and improvements from Siemens. Update training materials accordingly and encourage a culture of learning. By fostering an environment that values feedback and improvement, organizations can enhance user engagement and increase overall productivity.
"Investing time in initial assessment, training, and continuous improvement helps organizations fully leverage Siemens Teamcenter's capabilities."
Challenges and Solutions
In the realm of implementing Siemens Teamcenter, navigating through challenges is a key part of the process. This section emphasizes the significance of understanding these hurdles and identifying effective solutions. Acknowledging these obstacles not only prepares organizations for what lies ahead but also paves the way for smoother implementation. It is essential for stakeholders, especially decision-makers and IT professionals, to recognize that effective change management can bolster the potential benefits of Teamcenter.
Common Implementation Issues
When organizations begin to implement Siemens Teamcenter, they often face several issues that can hinder success. Some of these include:
- Data Migration Difficulties: Transitioning existing data to a new system can be complex. The challenge lies in ensuring accuracy and completeness during the migration process. Data quality is critical; inconsistencies can lead to confusion and inefficiency.
- Integration Challenges: Teamcenter integrates with various tools, including CAD and ERP systems. However, ensuring seamless compatibility often presents technical issues. Misalignment between systems can disrupt workflows and create gaps in data sharing.
- Inadequate Training: A frequent issue is the lack of sufficient training for users. Even with an advanced system like Teamcenter, if users are not effectively trained, it can lead to poor utilization, resulting in underwhelming returns on investment.
- Resistance to Change: Employees accustomed to previous systems may resist transitioning to Teamcenter. This resistance can stem from fear of the unknown or simply a preference for familiar processes.
Addressing these challenges early in the implementation journey is vital. Determining specific strategies tailored to the organization can mitigate various risks effectively.
Addressing User Resistance
User resistance is a significant hurdle when introducing new technology such as Siemens Teamcenter. Understanding the roots of this reluctance helps in crafting appropriate strategies. Here are several approaches:
- Effective Communication: Transparency about the reasons for the transition can alleviate fears and uncertainties. When users understand the benefits and how Teamcenter improves their day-to-day tasks, they are more likely to embrace the change.
- Involving Users Early: Getting feedback from users during the planning phase increases buy-in. Allowing users to express concerns or suggestions can create a sense of ownership in the new system.
- Comprehensive Training Programs: Providing thorough training sessions helps mitigate anxiety associated with learning a new system. Users should feel confident about navigating Teamcenter.
- Support Systems: Establishing a support network for ongoing help is essential. Users should know that assistance is readily available to help them adjust to the transition.
The smooth adoption of Siemens Teamcenter is not just about the technology itself, but rather how well the organization manages the human aspects of the change.
Implementing these strategies aids in addressing resistance and streamlining the adoption of Siemens Teamcenter. Recognizing the challenges and deploying tailored solutions will ultimately contribute to a more successful implementation.
Future Trends in PLM and Teamcenter
The landscape of Product Lifecycle Management (PLM) is rapidly evolving. Understanding these trends is vital for organizations that aim to remain competitive. Digital transformation is a key driver of change in PLM systems, particularly in the context of Siemens Teamcenter. As industries strive for increased efficiency, collaboration, and innovation, being aware of the future trends helps organizations anticipate shifts in the market.
A major element to consider is the need for greater integration across platforms. Companies find that they benefit from systems that not only manage design processes but can also interact seamlessly with tools across various departments. This interconnectedness enhances data accuracy, reduces errors, and accelerates the decision-making process. In essence, successful PLM strategies will prioritize holistic integration to harness the full potential of digital resources.
Additionally, organizations will also benefit from investing in employee training and development regarding these emerging technologies to ensure a smoother transition and application.
Impact of Digital Transformation
Digital transformation has profoundly reshaped the approach to PLM. It has shifted focus from traditional methods to more agile ways of working. This transition improved collaboration among various departments, fostering faster product development cycles. With the digitization of processes, Siemens Teamcenter integrates advanced technologies like cloud computing, artificial intelligence, and data analytics.
By leveraging these technologies, organizations can gain better insights into product performance at every stage of the lifecycle. For instance, predictive analytics tools in Teamcenter help in anticipating possible failures, thus allowing for proactive decision-making. It results in improvements in quality and efficiency.
Moreover, the adaptability of Siemens Teamcenter allows companies to tailor their PLM processes based on real-time data, enhancing both customer experience and profitability. Organizations adopting a digital-first approach find themselves better positioned to respond to market demands.
"Digital transformation is not merely a trend; it is a fundamental shift in how products are developed, managed, and sold."
Emerging Technologies in PLM
Emerging technologies are transforming the PLM landscape in ways that were unimaginable a few years ago. Technologies like artificial intelligence, machine learning, and the Internet of Things are now integral to platforms like Siemens Teamcenter.
AI facilitates smarter data management, enabling organizations to analyze vast amounts of information quickly. This capability not only supports streamlined workflows but also enhances understanding of customer needs and product performance.
Additionally, machine learning algorithms can forecast trends, helping companies stay ahead of their competitors. As these technologies continue to develop, they will provide deeper insights into product lifecycle stages, informing decisions that optimize each phase.
The integration of IoT into PLM systems raises the tenant of real-time monitoring and feedback. With IoT-enabled devices, companies can gather data continuously about how products perform in the field. This information is invaluable for future product development and innovation, enabling more responsive planning and design processes.
Epilogue
The conclusion serves as a critical part of the article, reinforcing the significance of Siemens Teamcenter in the realm of Product Lifecycle Management. It encapsulates the core themes discussed, emphasizes the necessity for effective integration of PLM tools, and highlights the role of Teamcenter in enhancing productivity and collaboration across various industries.
In recent years, as businesses aim to streamline their processes and improve their product offerings, the choice of a robust PLM solution has become vital. Teamcenter stands out due to its comprehensive data management capabilities, powerful collaboration tools, and seamless integration with existing systems. The benefits of implementing such a solution extend beyond mere efficiency; they include better product quality, reduced time-to-market, and improved compliance with industry standards.
Summarizing Key Points
- Teamcenter is integral for PLM: Its features support real-time collaboration and effective data management.
- Importance of integration: Compatibility with other systems like CAD and ERP is essential for maximizing utility.
- Industry versatility: Teamcenter is applicable across diverse sectors such as aerospace, automotive, and consumer goods.
- User experience matters: A well-designed interface enhances usability, facilitating quicker adoption by users.
Final Thoughts
The future of Product Lifecycle Management is closely tied to advancements in technology, including the rise of digital transformation. As businesses adapt to rapid changes, tools like Siemens Teamcenter will remain pivotal in navigating these challenges. Investment in PLM can lead to innovations that allow companies to stay competitive.