Understanding Manufacturing Automation: Key Insights
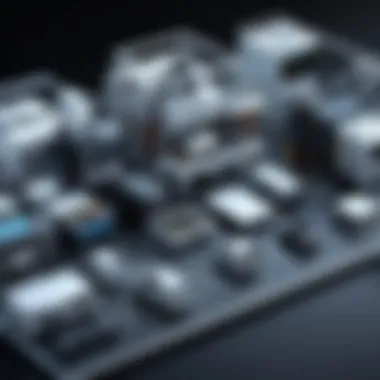
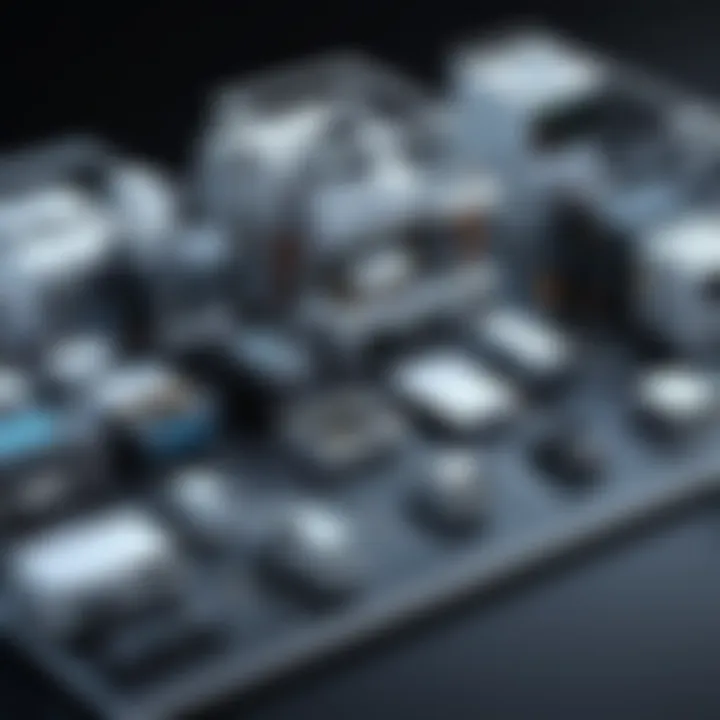
Intro
Manufacturing automation represents a transformative shift within industries, profoundly altering how products are made and services are delivered. As technology advances, understanding this evolution becomes imperative for decision-makers and IT professionals. Automation encapsulates various principles and technologies that enhance production efficiency, reduce labor costs, and improve product quality.
In this article, we explore the core elements of manufacturing automation. By dissecting its key features, target users, pricing models, and the multifaceted impacts it has on industries, readers will gain a nuanced insight into this crucial area. We aim to equip industry professionals with knowledge that assists in strategic decision-making regarding the adoption of automation technologies.
Key Features and Functionalities
Comprehensive Overview
Manufacturing automation includes multiple technologies that seamlessly integrate with traditional manufacturing processes. Such integration allows for real-time monitoring, control, and optimization of systems. Key features often include:
- Robotic Process Automation (RPA): Involves the use of machines to perform routine tasks.
- Programmable Logic Controllers (PLCs): Essential for controlling machinery automation.
- Industrial Internet of Things (IIoT): Connects machinery through smart sensors for data collection.
- Data Analytics: Facilitates real-time analysis and decision-making based on collected data.
These components work together to enhance productivity, minimize errors, and facilitate preventive maintenance. They allow for consistent product quality, enabling manufacturers to meet market demands.
Target Users
The adoption of manufacturing automation appeals to various stakeholders. Key groups include:
- Manufacturing Executives: Overseeing production efficiency and cost-effectiveness.
- Engineers and Technicians: Responsible for implementation and maintenance of automation systems.
- IT Professionals: Ensuring integration with existing technology infrastructure.
- Entrepreneurs and Business Owners: Seeking efficiency and scalability in operations.
By understanding who benefits from these technologies, stakeholders can tailor their strategies effectively to implement the most suitable solutions.
Pricing Models and Cost Analysis
Breakdown of Pricing Tiers
When analyzing the costs associated with manufacturing automation, it's essential to note that pricing can vary widely based on technology and deployment. Automation systems often fall into several pricing categories:
- Basic Automation Packages: Typically includes simple robotic arms; lower initial investment.
- Advanced Integrated Systems: Involves complex IoT devices and sensors; higher costs but offers greater savings over time.
- Custom Solutions: Tailored specifically to a company's needs; costs can be substantial due to personalization.
Additional Costs to Consider
In addition to initial costs, there are ongoing expenses that businesses should factor into their budget. These include:
- Maintenance and Upgrades: Regular service to ensure systems operate effectively.
- Training and Support: Essential for staff to efficiently use and manage new technologies.
- Software Licenses: Some systems require ongoing software subscriptions.
Understanding these expenditures is crucial in making a well-informed investment in automation technologies.
The successful implementation of manufacturing automation can result in significant gains in efficiency, production quality, and overall profitability.
What is Manufacturing Automation
Manufacturing automation represents a pivotal shift in how industries produce goods. Its importance lies not only in its capacity to enhance productivity but also in its potential to redefine operational methodologies. Understanding manufacturing automation is vital for decision-makers, IT professionals, and entrepreneurs.
This section aims to clarify fundamental concepts surrounding manufacturing automation, including its definition, scope, and historical context. By grasping these elements, readers will appreciate how automation technologies can lead to transformative advantages such as improved efficiency, cost savings, and enhanced product quality.
Definition and Scope
Manufacturing automation refers to the use of control systems, such as computers or robots, for handling different processes and machinery in an industry. Its scope encompasses a wide range of applications, from the simple control of a single machine to the complete automated production line. The term includes various technologies like robotics, computer-aided design, and manufacturing execution systems.
The main goals of manufacturing automation include reducing human involvement in processes, increasing reliability, and ensuring consistent quality. It is crucial to define what aspects of the manufacturing process will be automated to successfully implement these systems. Different levels of automation can be employed based on a companyβs specific needs, resources, and technological readiness.
Historical Context
The evolution of manufacturing automation began during the Industrial Revolution, with early machinery that replaced labor-intensive tasks. Over time, technology advanced from mechanical systems to the sophisticated automation we see today. The introduction of programmable logic controllers in the late 1960s marked a significant leap, allowing for more complex control of machine operations.
By the 1980s and 1990s, computerization expanded significantly, enabling real-time monitoring and control of manufacturing processes. Today, we stand on the brink of a new era characterized by smart factories, where interconnected devices communicate and operate independently. This historical context illustrates how manufacturing automation has progressed from basic mechanization to advanced automated systems that integrate a variety of technologies. It helps underline the enduring relevance of automation trends in modern manufacturing.
Key Components of Manufacturing Automation
Understanding the key components of manufacturing automation is fundamental in grasping how automation transforms production environments. Each component plays a vital role in enhancing operational efficiency, reducing costs, and ensuring output quality. As industries adopt these technologies, knowledge about these elements becomes essential for informed decision-making.
Robotics
Robotics are essential in manufacturing automation. They can perform repetitive and complex tasks with precision and speed that surpasses human capabilities. Companies utilize robotic arms in assembly lines, welding, and packing. Incorporating robotics can lead to higher productivity levels and fewer errors in production. Moreover, robots can be programmed for varied tasks, which adds flexibility to manufacturing operations. Careful selection and integration of robots are crucial. Factors such as payload capacity, reach, and compatibility with existing systems must be considered.
Control Systems
Control systems form the backbone of automation processes. They oversee and regulate various functions in manufacturing plants. Through sophisticated software and hardware combinations, control systems ensure that machines and processes operate cohesively. For example, a programmable logic controller (PLC) can execute commands to machines based on input from sensors. These systems can improve productivity by reducing response times and enhancing accuracy in processes. Thus, understanding how control systems work and integrate is vital for those involved in automation projects.
Sensors and Actuators
Sensors and actuators are pivotal in gathering real-time data and executing operations based on that information. Sensors detect changes in the environment, such as temperature, humidity, and pressure. This data is crucial for maintaining optimal conditions in manufacturing processes. On the other hand, actuators convert commands received from control systems into physical actions, like moving a robotic arm or adjusting a valve. Their seamless integration allows for responsive and adaptive manufacturing environments. Prioritizing these components enhances overall productivity and safety.
Data Acquisition and Management
Data acquisition and management systems collect, store, and analyze data generated from various manufacturing processes. With the advent of Industry 4.0, the role of data management has expanded significantly. These systems help in tracking performance, analyzing trends, and identifying issues early. By leveraging big data, manufacturers can make informed decisions that lead to optimization of operations. It is crucial to ensure data integrity and security in the management process. Choosing the right tools and platforms can make a significant difference in achieving operational excellence.
"The integration of key components in manufacturing automation leads to improvements in efficiency and effectiveness across the entire production chain."
Understanding these components allows decision-makers to identify which areas of their manufacturing processes can benefit the most from automation technologies. By implementing automation solutions adeptly, businesses can enhance their competitiveness in an increasingly demanding market.
Types of Automation in Manufacturing
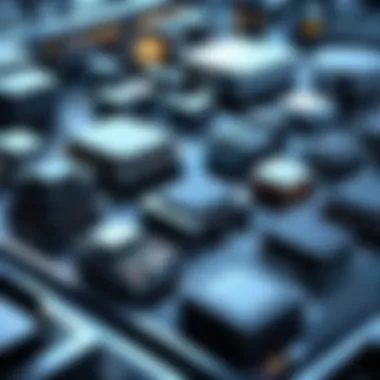
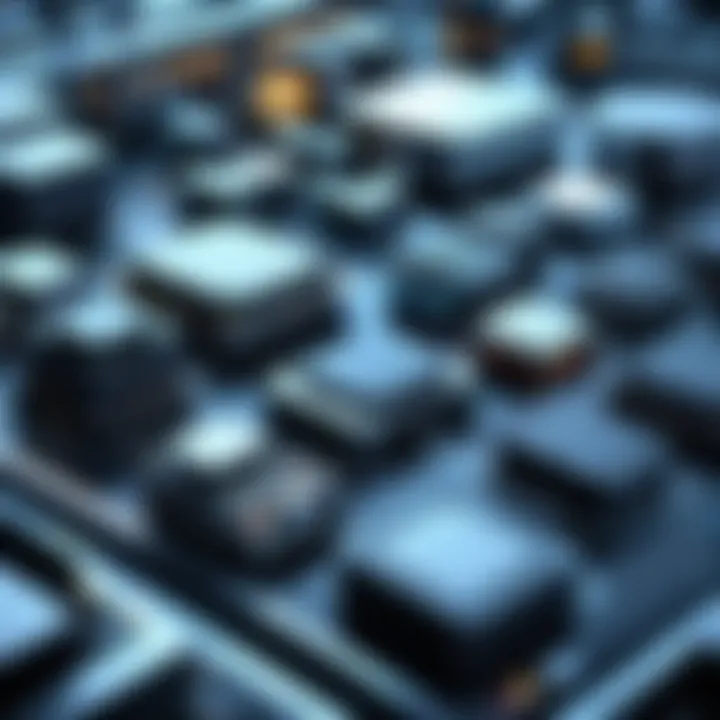
Understanding the various types of automation in manufacturing is crucial for decision-makers and industry professionals aiming to optimize production efficiency. Each type features unique characteristics and caters to different production needs. In this section, we will explore three main categories: Fixed or Hard Automation, Programmable Automation, and Flexible Automation. Each offers distinct benefits and considerations that influence their implementation in manufacturing processes.
Fixed or Hard Automation
Fixed or hard automation is designed for a specific set of operations with minimal flexibility. It is often used in high-volume production settings where the same tasks are repeated consistently. Common applications include assembly lines for automobiles or consumer goods. The advantages of fixed automation include high production rates, lower production costs per unit, and minimized labor costs due to its repetitive nature.
However, there are limitations. Adaptability is a significant concern; changes in product design or production volume can necessitate costly retooling. When considering fixed automation, it is essential to evaluate the expected lifespan of the product and market demands to ensure that the investment aligns with long-term objectives.
Programmable Automation
Programmable automation allows for greater flexibility compared to fixed automation. This type is suitable for batch production where products undergo frequent changes in production volume or design. Programmable systems can be reconfigured through software adjustments, making them ideal for manufacturers that produce a variety of products in smaller quantities.
The key benefits include adaptability, reduced downtime during setup changes, and versatility in product lines. Nevertheless, the complexity of programming and the need for skilled personnel to operate these systems can pose challenges. Businesses should weigh the benefits of flexibility against the costs of training and technology investment when considering programmable automation for their operations.
Flexible Automation
Flexible automation offers the highest level of adaptability among the three types discussed. It is built to handle variable production volumes and diverse product types simultaneously. This is advantageous for industries that face rapidly changing consumer preferences or need to customize products on demand.
Implementing flexible automation involves a combination of hardware and software that can quickly adjust production lines to new tasks. The benefits include lower inventory costs, improved responsiveness to market changes, and increased product variety. On the flip side, the initial setup cost can be significant, and while it allows for rapid adaptation, it may require higher oversight and management to ensure efficiency.
"The right type of automation can streamline production and enhance competitiveness in the market."
Considering these various types of automation allows for informed decision-making that can significantly improve operational efficiency in manufacturing.
Technologies Driving Manufacturing Automation
Technologies play a critical role in the evolution of manufacturing automation. Understanding these technologies is vital for decision-makers looking to enhance operational efficiency and gain a competitive edge. Each technological component brings certain advantages, but also considerations and challenges that need careful evaluation.
Artificial Intelligence and Machine Learning
Artificial intelligence (AI) and machine learning (ML) are transforming how manufacturers operate. They enable systems to learn from data and adapt to various conditions without human intervention.
Benefits:
- Predictive Maintenance: AI algorithms can analyze machine data to predict failures before they occur, reducing downtime.
- Quality Control: By using image recognition, AI can assist in monitoring product quality during production.
- Process Optimization: Machine learning models help in adjusting production parameters to optimize efficiency.
Considerations:
Implementing AI and ML requires a solid data infrastructure. Additionally, organizations need to ensure that their workforce is prepared to work alongside these advanced technologies.
Internet of Things (IoT)
The Internet of Things (IoT) connects machines and sensors to the internet, providing real-time data access. This connectivity enables better decision-making and enhances responsiveness within manufacturing processes.
Benefits:
- Real-Time Monitoring: IoT devices offer real-time insights into equipment performance and supply chain metrics.
- Enhanced Collaboration: Data from machines can be shared across departments, improving cooperation and reducing silos.
- Remote Management: IoT allows for remote monitoring and management of equipment, facilitating quick interventions when required.
Considerations:
Cybersecurity is a significant concern when integrating IoT devices, as the increase in connected devices can also increase vulnerability to data breaches.
Cloud Computing
Cloud computing has emerged as an essential driver of manufacturing automation. By allowing companies to store and analyze data off-site, it removes the physical constraints of traditional storage methods.
Benefits:
- Scalable Resources: Manufacturers can scale their IT resources up or down based on demand.
- Cost Efficiency: Cloud solutions often reduce the need for on-premise hardware, leading to cost savings.
- Enhanced Collaboration: Cloud services facilitate better collaboration among teams regardless of their location.
Considerations:
Migrating to the cloud requires careful planning and a clear strategy to protect data integrity and ensure compliance with regulations.
Advanced Manufacturing Technologies
Advanced manufacturing technologies encompass various methods, including additive manufacturing (3D printing), additive and subtractive processes, and digital twins.
Benefits:
- Customization: These technologies allow for more customized products tailored to specific customer needs.
- Efficiency: Techniques such as 3D printing can reduce material waste and cut down production time.
- Digital Prototyping: Advanced technologies enable rapid prototyping, helping manufacturers innovate faster.
Considerations:
Investing in advanced manufacturing technologies requires understanding costs and the technical skills needed to operate new systems effectively.
βThe impact of technologies on manufacturing automation is profound, guiding industries towards greater efficiency and innovation.β
Integrating these technologies into manufacturing processes is not merely a trend, but a strategic imperative for firms aiming for long-term viability and success. Each technological advancement should be carefully assessed for its benefits and challenges to enable effective implementation.
Benefits of Manufacturing Automation
Manufacturing automation offers numerous advantages that can significantly enhance operational performance, reduce costs, and improve overall production quality. Embracing automation can transform traditional manufacturing processes, providing meaningful benefits that are relevant to industry leaders and decision-makers. Understanding these benefits is crucial for assessing the value proposition of investing in automation technologies.
Increased Efficiency
One of the most compelling advantages of manufacturing automation is the increase in efficiency it brings to production processes. Automated systems can operate continuously, with minimal downtime compared to manual labor. Machines, such as robotic arms and conveyor systems, can perform repetitive tasks faster and with a higher degree of precision.
The efficiency of automated processes often results in a higher throughput. This allows manufacturers to meet demand more effectively while also reducing lead times in the production cycle. Higher efficiency not only means producing more in less time but also enables better floor space utilization, leading to optimized operations.
Like this, companies may experience improved resource allocation. This aspect translates into an enhanced ability to leverage materials efficiently and minimize waste.
Cost Reduction

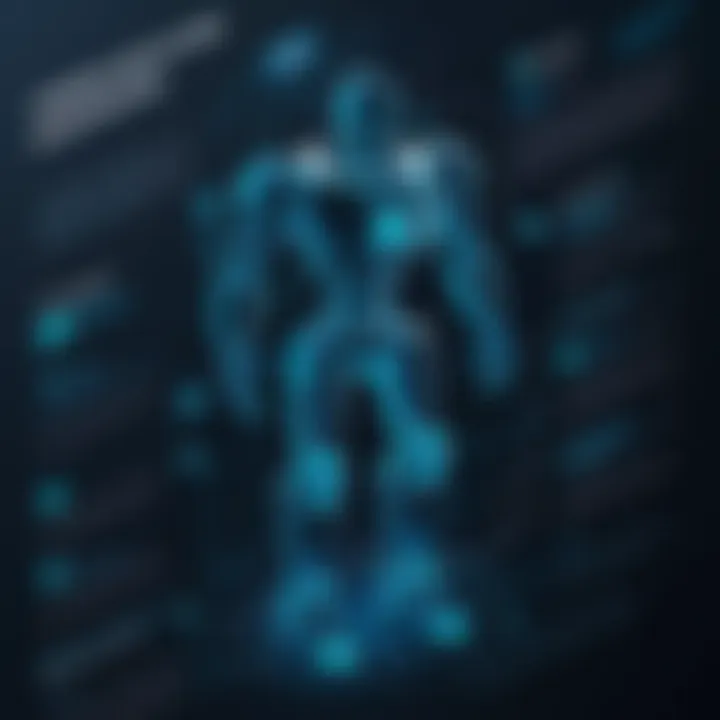
Cost reduction is a key driver for manufacturers when considering automation. While the initial investment in automation technology can be substantial, the long-term savings often outweigh these costs. By automating repetitive and labor-intensive tasks, companies can significantly decrease labor costs. This shift is particularly beneficial in industries facing labor shortages or increasing wage rates.
Furthermore, automation reduces the costs associated with errors and defects. Manual processes are more prone to human error, leading to rework and scrap. By contrast, automated systems maximize consistency and accuracy, resulting in fewer defects.
In summary, while the entry costs can be high, the cumulative long-term savings that companies experience in labor, error reduction, and operational efficiency contribute to a strong return on investment.
Quality Improvement
Quality improvement is another pivotal benefit of manufacturing automation. Automation introduces standardized processes that enhance product quality consistency. Machines maintain uniformity in production, unlike humans, who may have variations in performance.
Moreover, automated systems often integrate quality control measures that monitor production in real-time. This capability allows for immediate detection and correction of issues, ensuring that only high-quality products reach the final stages of production and distribution.
Companies that invest in automation often observe a marked increase in customer satisfaction due to the superior quality of their products, fostering brand loyalty and repeat business.
Safety Enhancements
Safety is a paramount concern in manufacturing environments. Automation can significantly improve workplace safety by taking over dangerous tasks and reducing the risk of workplace accidents. For instance, robots can handle hazardous materials or operate in environments with extreme conditions that pose risks to human workers.
Moreover, automated systems can be designed with safety features that minimize the likelihood of accidents. These may include fail-safes, emergency shut-offs, and real-time monitoring systems that can flag potential hazards before they escalate.
As a result, companies that implement automated solutions often see lower injury rates and reduced lost workdays due to accidents, ultimately preserving workforce productivity.
Challenges of Implementing Automation
The journey toward automating manufacturing processes is not without obstacles. Understanding these challenges is critical for decision-makers who are contemplating the transition to automated systems. This section will illuminate three primary challenges: the high initial investment, the skill gap in the workforce, and the integration with existing systems. Each of these factors plays a significant role in how organizations approach automation and can influence the decision-making process.
High Initial Investment
Investing in automation often requires substantial financial resources. Companies may face hurdles related to the cost of acquiring new equipment, software, and technology needed for automation. These expenses can deter organizations, especially small to medium-sized enterprises, from embracing automation.
The costs associated with automation can be divided into two categories: tangible and intangible. Tangible costs include purchasing robots or machinery, while intangible costs may involve the disruption of existing workflows or the potential need for building renovations. Thus, it's essential for businesses to perform a thorough cost-benefit analysis before committing to automation.
"The decision to invest in automation should be based on a clear understanding of long-term returns on investment rather than mere upfront costs."
Companies also need to account for ongoing maintenance and potential upgrades of automated systems, which can further inflate total costs over time. Properly maintaining automation systems is crucial for long-term efficacy and reliability.
Skill Gap in Workforce
A significant barrier to implementing automation is the skill gap that exists within the labor force. Many workers may not possess the necessary skills to operate or maintain automated systems effectively. As industries adopt new technologies, there is often a corresponding need for a workforce that is well-trained in these new tools.
Failure to address this skill gap can lead to underutilization of automated systems. For example, without adequately trained personnel, businesses may find themselves unable to operate machinery to full capacity, hindering the potential benefits of automation.
To combat this issue, companies must invest in ongoing training programs aimed at upskilling their employees. This involves not just technical training but also fostering a mindset that embraces change and learning. Reskilling initiatives may include workshops, online courses, and partnership with institutions to ensure that the workforce evolves alongside the technology.
Integration with Existing Systems
Integrating new automation solutions with existing manufacturing systems poses another challenge. Many organizations have legacy systems that may not be compatible with new technologies. This discrepancy can result in operational silos where automated processes do not fully connect with traditional operations, leading to inefficiencies.
For successful integration, companies should prioritize compatibility. It is essential to evaluate existing systems and design automation solutions that fit seamlessly within current operational frameworks. This might involve custom software development or investing in middleware solutions that facilitate communication between old and new systems.
Successful integration not only ensures rapid operations but also enhances data flow across various departments, improving overall decision-making processes in the organization. Thus, careful planning and execution are critical to overcome the hurdles posed by integrating modern automation technologies into legacy systems.
Through addressing these key challenges, organizations can better position themselves for successful automation transitions, ultimately leading to enhanced efficiency and competitiveness in the manufacturing sector.
Future Trends in Manufacturing Automation
Manufacturing automation is experiencing rapid changes due to technological advancements and shifting market demands. Understanding future trends is crucial for industry leaders and decision-makers. This section will explore specific trends such as smart factories, sustainable practices, and customization. Each of these elements offers significant benefits and presents considerations that can influence decision-making in manufacturing.
Smart Factories
Smart factories represent a significant leap forward in manufacturing automation. These facilities leverage the Internet of Things (IoT), artificial intelligence, and big data analytics to create interconnected systems. This advanced integration allows for real-time monitoring and management of production processes.
The adoption of smart factories can lead to:
- Enhanced Efficiency: Automation streamlines operations, resulting in faster production cycles.
- Improved Resource Management: Real-time data enables better allocation of resources, minimizing waste.
- Predictive Maintenance: IoT devices can predict equipment failures before they happen, reducing downtime.
To succeed in implementing smart factories, manufacturers need to focus on selecting the right technologies and ensuring seamless integration with existing systems.
Sustainable Manufacturing Practices
Sustainability is becoming an imperative for modern manufacturing. Companies are increasingly adopting sustainable practices to meet regulatory requirements and consumer demands. Automation contributes to sustainability by optimizing processes and reducing energy consumption.
The advantages include:
- Reduced Environmental Footprint: Automated systems can minimize waste and lower emissions during production.
- Resource Conservation: Advanced technologies help in using materials more efficiently, which lowers costs.
Incorporating sustainability in manufacturing requires a shift in focus towards long-term benefits over short-term gains. Evaluating automation solutions through the lens of sustainability can lead to more responsible production processes.
Customization and Personalization
Customization is a vital trend shaping the future of manufacturing. Customers seek products tailored to their preferences, pushing manufacturers to adopt flexible automation solutions. This shift enables rapid changes in production without significant downtime.
Key aspects of customization include:
- Flexible Automation Systems: These systems can easily adapt to produce varying product specifications.
- Customer-Centric Design: Incorporating feedback into design processes enhances customer satisfaction.
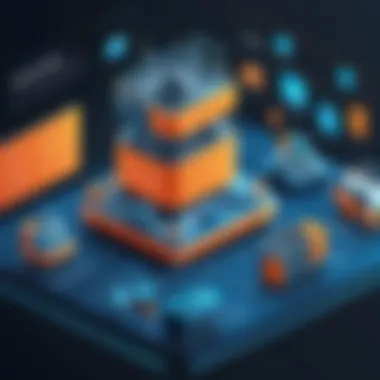
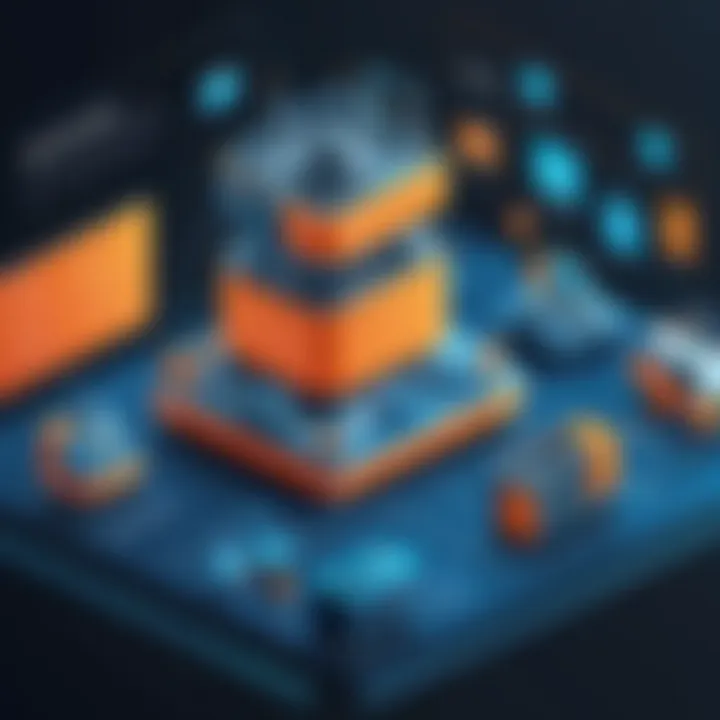
As firms embrace customization, they create competitive advantages through enhanced responsiveness to market needs. This trend demands innovative thinking about automation strategies.
"The future of manufacturing hinges on the ability to merge automation with responsiveness."
Case Studies of Successful Automation in Manufacturing
Case studies demonstrate the real-world impacts and benefits of automation in various manufacturing sectors. They provide tangible evidence of how automation can transform processes, improve efficiency and enhance productivity. Understanding these cases is crucial for decision-makers attempting to navigate the complexities of automation implementation in their enterprises. Through the examination of specific sectors, we gain insights into the unique challenges and triumphs associated with automating production.
Automotive Industry
The automotive industry is a prime example of successful automation. Major manufacturers like Ford and Toyota have long embraced automation to improve production speeds and ensure precision. For instance, Ford's use of robotic assembly lines has led to significant reductions in production time. Robots that handle welding and painting operations can work precisely and continuously, allowing for around-the-clock manufacturing.
The benefits of automation in this sector extend beyond speed. Quality assurance becomes more robust with the implementation of automated systems. For example, automated inspection systems can identify defects in real-time, which mitigates the risks of costly recalls. Automation also allows for customization; vehicles can be tailored to specific consumer preferences without sacrificing efficiency.
Electronics Manufacturing
Electronics manufacturing has similarly embraced automation to meet the high demands of the market. Companies such as Apple and Samsung have integrated sophisticated automated processes in their production lines. Using surface mount technology (SMT) machines, these companies place components on circuit boards with high accuracy and speed.
Automation in electronics manufacturing is pivotal as product life cycles tend to be short. Quick production allows companies to maintain competitiveness. Furthermore, automated assembly reduces human error and increases the consistency of products, leading to improved overall quality. The ability to quickly pivot in response to market demands is a significant advantage.
Food and Beverage Sector
The food and beverage sector faces stringent safety and quality standards, making automation essential. Companies like Coca-Cola and NestlΓ© employ automation to handle everything from bottling to packaging. Automated systems ensure that production runs smoothly and efficiently while adhering to hygiene protocols.
In this sector, automation contributes to waste reduction. For instance, precise measuring and control systems minimize overproduction and spoilage. Additionally, automated systems increase the throughput of factories, allowing for quicker responses to consumer demand. Automation not only enhances efficiency but also ensures compliance with health regulations, critical in the food industry.
"Automation in manufacturing is not just an operation upgrade; it is a strategic necessity that enhances competitiveness across sectors."
In summary, these case studies illustrate that the successful implementation of automation processes can lead to enhanced performance in manufacturing. By examining specific industries, we see that the benefits transcend mere efficiency; they encompass quality improvement, customization capabilities, and compliance with standards. Such insights empower industry leaders to make informed decisions regarding automation investments.
Evaluating Automation Solutions for Manufacturing
Evaluating automation solutions is a critical phase that determines the success of implementing manufacturing automation. This process encompasses identifying specific automation needs, understanding potential impacts, and selecting the right technologies and vendors. As industries increasingly adopt automation, comprehending these aspects becomes essential for decision-makers who seek to optimize production efficiency, improve quality, and reduce costs. Failing to evaluate properly can lead to misallocated resources and unsatisfactory outcomes.
Identifying Requirements
To effectively evaluate automation solutions, it is crucial to first identify the specific requirements of your manufacturing operation. This step involves analyzing current processes, determining pain points, and defining the goals of automation. Questions to consider include:
- What are the main objectives? Is it to increase speed, improve quality, or reduce labor costs?
- Are there particular tasks that are labor-intensive or prone to error?
- What is the current production capacity, and what is the desired output?
By answering these questions, stakeholders can pinpoint the relevant requirements that automation solutions must fulfill. This clarity ensures that the selected systems align with the production goals and operational context. It also helps prioritize features such as adaptability, scalability, and user-friendliness in the technology considered.
Vendor Selection Criteria
Once requirements are outlined, the next logical step is to establish criteria for selecting vendors. Not all vendors offer the same level of expertise, services, or offerings. Important considerations include:
- Experience and Reputation: Look for vendors with proven track records and positive customer reviews. Their past projects can provide insight into their capabilities.
- Technical Support and Training: Consider whether the vendor provides adequate support during and after installation. Training for existing staff on new systems is also crucial to ensure smooth transitions.
- Customization Options: Because every manufacturing facility is unique, the ability to customize automation solutions to meet specific needs is essential.
- Costs and Payment Terms: Understand the total cost of ownership, including installation, maintenance, and potential upgrades. Comparing quotes can help in making an informed choice.
"Choosing the right vendor can significantly influence the long-term success of your automation project."
Adopting a structured yet flexible approach while evaluating automation solutions will support manufacturers in reaping the full benefits of their investment. This diligence not only fosters efficiency but also helps cultivate a culture where technology is embraced as a key resource in achieving organizational goals.
The Impact of Automation on Labor
The rise of automation in manufacturing creates critical discussions about its effects on labor. As industries become more automated, the shift from manual tasks to automated processes raises important questions on job security, workforce dynamics, and skills development. Decision-makers and industry professionals must be aware of these factors when considering automation solutions. The consequences of automation extend beyond mere operational efficiency; they shape the future of the workforce.
Job Displacement Concerns
The introduction of automation raises valid concerns regarding job displacement. Many workers have experienced shifts in their roles due to the implementation of automated systems. Jobs that involve repetitive tasks are particularly susceptible to replacement by machines. For instance, assembly line workers in automotive manufacturing may find their positions endangered as robots increasingly handle tasks.
Data suggests that entire sectors could experience declines in workforce requirements.
- According to a report by the World Economic Forum, millions of jobs may disappear in the upcoming years due to automation.
Despite these concerns, itβs essential to approach the situation with a balanced perspective. While some jobs will indeed vanish, others will emerge that require new skill sets. Understanding this transition is vital for policy makers and educational institutions as they work to manage the workforce impacts of automation.
"Automation certainly poses a threat to certain jobs, but it also opens up opportunities for new roles and innovation in the labor market."
Upskilling Opportunities
As manufacturing environments evolve through automation, there is a significant need for upskilling the existing workforce. Upskilling refers to the process of training workers to equip them with the necessary skills to thrive in a more automated workplace. This is not only beneficial for individual employees, but it also enhances overall productivity within organizations.
Industries can invest in training programs that focus on the following aspects:
- Technical Skills: Familiarizing workers with advanced technologies and automated systems.
- Soft Skills: Encouraging critical thinking, adaptability, and problem-solving capabilities.
- Digital Literacy: Developing proficiency in digital tools and platforms critical for modern manufacturing.
By upskilling their workforce, companies can mitigate job displacement effects and ensure that their employees are prepared for new roles that arise due to automation. This shift towards reskilling not only aids in retaining talent but also strengthens a company's competitive edge in a rapidly changing market.
In summary, while the impact of automation on labor presents challenges, it also inspires innovative approaches to workforce management and skills development. Through proactive measures, industries can foster an environment in which both automation and human labor coexist productively.
End
The conclusion of this article synthesizes the key insights presented throughout the discussion on manufacturing automation. It serves as an essential aspect as it encapsulates the importance of understanding both the benefits and challenges that accompany the adoption of automation in manufacturing processes.
One of the most significant elements discussed is the potential for increased efficiency. Automation enables companies to streamline operations, reduce cycle times, and enhance productivity. By embracing technologies such as robotics and artificial intelligence, manufacturers can optimize their workflows and focus resources on areas that can drive value.
Additionally, the article highlights the cost reduction aspect of automation. Though the initial investment may be substantial, the long-term savings gained from decreased labor costs and improved product quality can lead to an attractive return on investment. This makes a strong case for automation as a strategic move for many businesses.
However, it is also important to consider the challenges, such as workforce implications. The automation of certain tasks leads to job displacement concerns, emphasizing the need for upskilling and reskilling efforts. Businesses and decision-makers must be aware of the repercussions on labor markets and work toward building a skilled workforce capable of adapting to new technologies.
"Automation is not a replacement for human labor; rather, it enhances human ability to produce value."
This perspective is vital in shaping a future where automation coexists with human skills, creating a symbiotic environment that fosters innovation and growth.