Understanding BOM Software: Key Insights for Industry
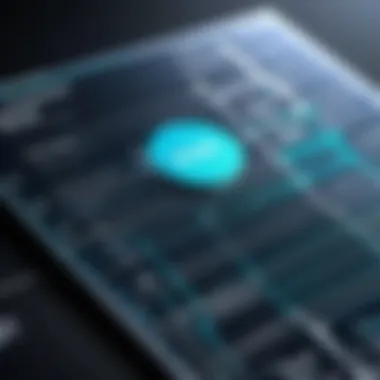

Intro
In the fast-paced world of manufacturing and product development, the Bill of Materials (BOM) has emerged as a pivotal component. It's not just a list of materials; it’s a detailed blueprint guiding the production process from start to finish. Understanding how BOM software works is crucial not only for technical roles but also for decision-makers who seek to harness its potential for optimizing operational efficiencies. As industries evolve, having a reliable BOM system can significantly impact the bottom line. This article takes a deep dive into BOM software, dissecting its key features, pricing models, target users, and much more.
Key Features and Functionalities
Comprehensive Overview
BOM software is built to streamline the creation and management of Bill of Materials. By automating these processes, it reduces the chances of human error and, ultimately, saves time and resources. The core functionalities of BOM software often include:
- User-friendly interface: Simplifies the creation and modification of BOMs.
- Version control: Maintains the integrity of data, allowing users to track changes over time.
- Integration capabilities: Seamlessly connects with other systems like ERP, PLM, and procurement software.
- Real-time collaboration: Supports teamwork across different departments, promoting a more harmonious workflow.
Moreover, many BOM tools offer customizable templates that cater to specific industries, enabling enhanced adaptability to unique processes.
Target Users
While the potential benefits of BOM software can resonate across a diverse set of industries, the main target users typically include:
- Manufacturers: To manage complex product structures and keep track of materials.
- Engineers: To ensure accurate specifications and prevent costly mistakes during the production cycle.
- Product Designers: To facilitate rapid prototyping and product iterations with real-time data.
- Supply Chain Managers: To streamline procurement and inventory processes.
This wide array of users underlines how critically important it is for organizations to choose the right BOM software tailored to their specific needs.
Pricing Models and Cost Analysis
Breakdown of Pricing Tiers
When considering BOM software solutions, understanding the pricing models is essential. These can vary widely depending on the complexity and features of the software.
- Basic Tier: Often includes core features; suitable for small businesses. Pricing might range from $50 to $200 per month.
- Standard Tier: Introduces advanced functionalities like integration; generally priced between $250 and $800 per month.
- Enterprise Tier: Designed for large organizations with extensive needs, often requiring a customized quote due to varied functionalities.
Understanding these tiers can help potential buyers align their budgets with the necessary features they require without being taken for a ride.
Additional Costs to Consider
While pricing tiers provide a starting point, there are extra costs often overlooked. These include:
- Implementation costs: Can vary based on the complexity of the software and the need for training sessions.
- Maintenance fees: Ongoing support and software updates often come at an extra price.
- Customizations: Tailoring features to fit specific business processes may involve additional fees.
By keeping these potential hidden costs in mind, organizations can make more informed budgeting decisions when seeking to adopt BOM software.
"Investing in the right BOM software translates to not just efficiency, but also enhanced innovation in the product development lifecycle."
Navigating the world of BOM software may seem complex, but understanding its features, user base, and pricing models offers a solid foundation. As we continue this guide, we’ll explore further facets of BOM software, offering insights that equip decision-makers and software buyers to make informed choices.
Foreword to BOM Software
In the fast-paced world of manufacturing and product design, understanding BOM software is paramount. It stands as the backbone for many organizations that deal with complex products requiring precise components. This section shines the spotlight on the foundational elements of BOM software, dissecting its definition and emphasizing its critical role in enhancing operational efficiency.
Definition of BOM Software
BOM software, or Bill of Materials software, functions as a structured list of all the materials, components, and assemblies required to create a product. Picture it as a master recipe for a chef, detailing not only the ingredients but also their quantities, sources, and compatible versions. Each entry holds significance, ensuring that the production process is neither delayed nor derailed due to missing parts or wrong specifications.
BOM software is more than a static list. It serves as a dynamic tool that integrates various aspects of production planning and inventory management. By holding intricate details ranging from part numbers to supplier information, it allows manufacturers to streamline processes by organizing their operations efficiently, reducing errors caused by miscommunication or lack of documentation. \
Importance in Manufacturing and Design
In the realm of manufacturing and product design, BOM software plays a crucial role that cannot be understated. Without it, businesses would be like wandering in a fog—lost among countless part numbers, specifications, and supplier details. Here are a few reasons why this software is indispensable:
- Streamlining Production: BOM software dramatically simplifies production workflows. By providing clear directives on what materials are needed and at what stage, it cuts down on downtime, ensuring a smoother production line.
- Enhanced Accuracy: Mistakes can be disastrous, leading to costly recalls or rework. Accurate BOMs help eliminate errors in ordering and assembling components. This means fewer headaches for project managers and lower costs in the long run.
- Facilitating Collaboration: In modern manufacturing environments, diverse teams—engineers, quality assurance, procurement—must work together seamlessly. BOM software acts as a central hub for all these stakeholders, channeling information effectively and keeping everyone on the same page.
- Adapting to Change: Design modifications are a natural part of product development. BOM software can rapidly adapt to changes, allowing teams to revise bills quickly without missing a beat. It's easier to update a digital document than to scramble in a paper-based system.
"A well-maintained BOM is like a digital thread weaving through the fabric of production, connecting every aspect of product lifecycle management."
As industries evolve, the significance of BOM software only grows. By harnessing this technology, companies can position themselves at the forefront of their sectors, effectively meeting market demands and achieving their operational goals.
Key Features of BOM Software
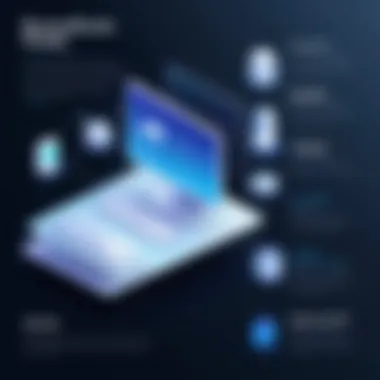
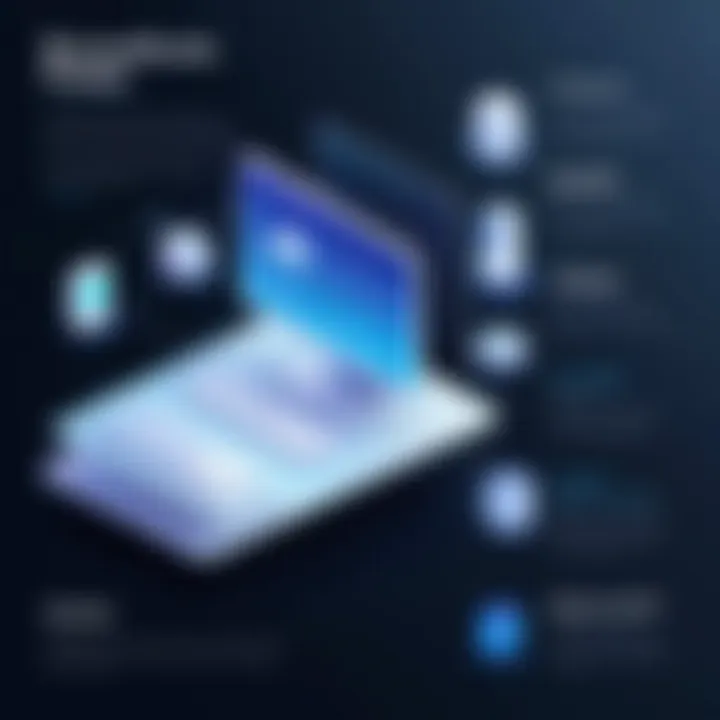
When diving into the realm of BOM software, one cannot overlook the pivotal role that its key features play in optimizing workflows and enhancing productivity. These features collectively form the backbone of the software, enabling businesses to manage complex data efficiently and align processes with broader organizational goals. Understanding these components gives decision-makers an advantage in selecting the right solution to suit their specific needs.
Data Management Capabilities
Data management is at the heart of BOM software. Companies generate a staggering amount of information as they design, manufacture, and distribute their products. The ability to process, organize, and retrieve this data is vital for operational success. The primary data management capabilities include:
- Centralized Database: A single repository for all components and materials minimizes confusion and ensures that everyone in the organization is on the same page. With a centralized database, product information is easily accessible for engineering, manufacturing, and procurement teams.
- Real-time Updates: With the fast-paced nature of manufacturing, real-time data updates help teams make informed decisions without delay. This feature reduces the risk of costly errors by ensuring that all stakeholders work off the latest information.
- Custom Fields and Attributes: Different industries and companies often have unique requirements. BOM software allows for the customization of fields and attributes to match specific needs, ensuring that the data gathered is relevant and useful.
Integration with Other Systems
No software operates in isolation. Integration capabilities are essential for BOM tools to function effectively within the broader ecosystem of manufacturing operations. By linking with other systems, BOM software drives efficiency and continuity across different functions. Key points of integration include:
- ERP Systems: Linking BOM software with Enterprise Resource Planning (ERP) systems means that accounting, human resources, and planning departments can access product data seamlessly, enhancing cross-departmental communication and reducing errors in order processing.
- CAD Software: Integrating with Computer-Aided Design (CAD) systems helps in automatically generating BOM from design files, making the transition from design to manufacturing more fluid. This eliminates the need for manual entry and the potential for discrepancies in data.
- Supply Chain Management Tools: Integrating BOM software with supply chain management systems allows for better inventory control and material management, ensuring that businesses can navigate supply chain challenges more effectively.
Version Control and Tracking
In an industry where changes happen at lightning speed, having robust version control and tracking capabilities in BOM software is crucial. It allows teams to monitor changes systematically, ensuring that everyone is referring to the most accurate version of product data. Key elements include:
- Change Management Logs: Every alteration made to the BOM, whether a slight design tweak or a major overhaul, is logged. This feature provides accountability and traceability, which is vital during audits or production reviews.
- Historical Data Access: Retaining historical data allows organizations to learn from past projects, making it easier to replicate successes and avoid prior mistakes. Future projects can benefit significantly from this accumulated knowledge.
- User Permissions: Enforcing user permissions streamlines who can view or edit BOMs, which both enhances security and helps to maintain data integrity. This control minimizes the risk of unauthorized changes that can lead to manufacturing discrepancies.
In summary, the key features of BOM software not only facilitate better data management and integration but also ensure that revisions and modifications are handled with precision. For decision-makers, comprehending these features is essential for making well-informed choices tailored to their unique operational demands.
Analytical Tools and Reporting Features
In today’s fast-paced manufacturing environment, analytical tools and reporting features within BOM software cannot be overlooked. These tools offer a gateway for businesses to not only optimize their processes but also to ensure informed decision-making. By harnessing the power of data, organizations can navigate complexities, anticipate issues, and act swiftly, ensuring that they stay ahead of their competition.
Utilizing Analytics for Decision Making
The application of analytics in BOM software significantly enhances the decision-making process. It enables companies to sift through vast amounts of data and extract meaningful insights. For example, engineers can analyze production trends to evaluate whether to ramp up order quantities or adjust workflows. This level of foresight can stave off bottlenecks in production.
Benefits of analytics include:
- Enhanced Prediction: By employing historical data, businesses can forecast future needs and avoid shortages.
- Performance Metrics: Analytics allows teams to track efficiency rates and downtime, serving as a barometer for operational health.
- Data-Backed Decisions: With clear visualization of data, managers can present cases to stakeholders convincingly, ensuring that changes are justified.
When companies incorporate analytics effectively, they find themselves in a position to not only react to data but to anticipate it.
Customizable Reporting Capabilities
When it comes to reporting, one size does not fit all. The ability to customize reports allows decision-makers to focus on the metrics that truly matter to their specific objectives. Whether it’s ensuring compliance with industry standards or tracking costs across multiple products, tailored reports provide clarity.
Key elements of customizable reporting include:
- User-Defined Metrics: Every organization has unique priorities. Customizable reports allow users to create metrics that align with their goals.
- Visual Dashboards: Integrating visual elements into reports can make data easily digestible, aiding comprehension during meetings.
- Automated Scheduling: Instead of manual extraction, reports can be generated and distributed automatically, freeing time for higher-level strategic tasks.
The ability to create tailored reports transforms how departments interact with data, leading to clearer communication and more strategic initiatives.
When considering reporting capabilities in BOM software, it's paramount that teams prioritize features that align with their operational realities. The focus should be on building a reporting framework that not only captures essential information, but also presents it in a manner that drives actionable insights.
Benefits of Implementing BOM Software
The implementation of Bill of Materials (BOM) software presents numerous advantages that can propel organizations towards enhanced productivity and effectiveness. Businesses, especially in manufacturing and design sectors, often grapple with complex data and logistical challenges. A robust BOM software solution becomes a pivotal tool in navigating these challenges. It streamlines processes, improves accuracy, manages costs, and fosters collaboration. Consequently, we will explore three significant benefits that stem from deploying BOM software, each of which directly impacts operational performance and strategic decision-making.
Improving Efficiency and Accuracy
One of the most tangible benefits of BOM software is the significant boost in efficiency and accuracy it provides. Traditional methods of managing bills of materials often rely on spreadsheets or manual documentation, which are prone to errors and time-consuming to update. With BOM software, all material data resides in a centralized system, ensuring real-time updates and easy access.
- Data Consistency: When teams work from a single source of truth, the risk of version conflict diminishes. Changes made to the BOM are instantly reflected across the organization, helping everyone stay on the same page, regardless of their department.
- Automated Processes: Many BOM programs offer automation of repetitive tasks, reducing the amount of time spent on paperwork. Inventory management, cost estimation, and compliance checks can all be handled more efficiently, freeing teams to focus on higher-value activities.
- Error Reduction: By automating calculations and data inputs, BOM software minimizes human error, leading to more accurate production schedules and material requirements.
The result? Faster lead times and an end product that aligns more closely with customer expectations. Organizations that once dealt with lengthy approval processes find that BOM software helps things move along nose-to-the-grindstone much faster.
Cost Reduction and Material Management
Cost management is another crucial area where BOM software shines. Effective material management not only minimizes waste but also aligns procurement with production needs. The insights provided by BOM tools help organizations make informed decisions about sourcing materials, thereby optimizing their budgets.
- Inventory Optimization: With precise tracking of materials and quantities, businesses can avoid overstocking or stockouts. This equilibrium helps maintain optimal inventory levels, reducing carrying costs.
- Supplier Negotiation: Detailed analytics on material usage can provide leverage during negotiations with suppliers. Organizations can present data on purchasing trends and usage rates, improving their bargaining position to secure better terms.
- Waste Reduction: Understanding the exact materials needed for production allows organizations to minimize scrap and surplus. These reductions, in turn, contribute directly to the bottom line, marking not just savings but also an environmentally-friendly approach to operations.
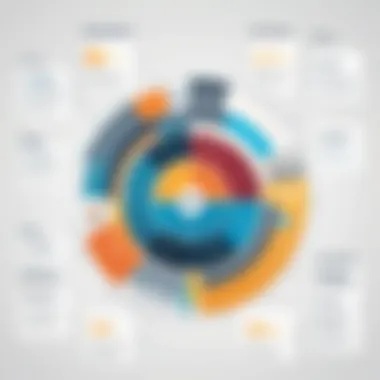
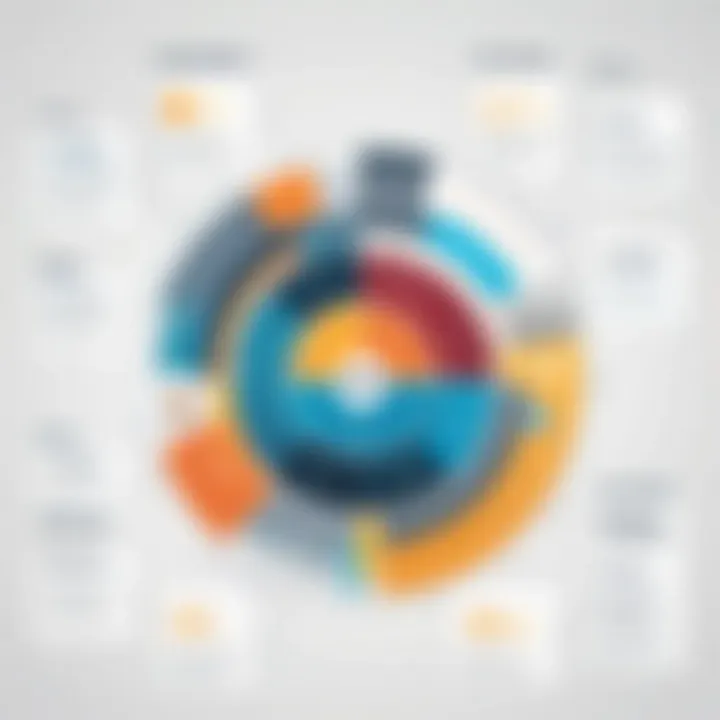
By implementing BOM software, companies reduce unnecessary costs while enhancing overall material flow management.
Enhancing Collaboration Across Teams
In today’s interconnected business environment, collaboration across various teams is essential to achieving organizational goals. BOM software facilitates this collaboration by integrating communication and information into one platform.
- Cross-Departmental Visibility: Various departments, from engineering to procurement, can access and share information instantly. Enhanced transparency leads to cohesive planning and execution.
- Project Coordination: With clear documentation and real-time updates, cross-functional teams can work on projects simultaneously without stepping on each other's toes. This means that design changes can be communicated promptly to production teams, reducing delays.
- Better Stakeholder Engagement: When all relevant parties are informed and involved, decision-making becomes smoother and more efficient. Stakeholders are more likely to engage and provide valuable input when they can easily see how their roles interlink with others.
Implementing BOM software doesn't just enhance the workflow of individual teams; it unites them toward a common goal, fostering a culture of collaboration.
Challenges in Adopting BOM Software
Understanding the challenges faced during the adoption of BOM software is crucial. Many organizations often overlook these hurdles, thinking the implementation process is all smooth sailing. However, a deep dive reveals that a variety of issues can surface, possibly hindering the success of a new system. Identifying these challenges allows organizations to put strategic measures in place, ensuring that the transition is as seamless as possible.
Resistance to Change in Organizations
It’s no secret that people love comfort. When it comes to introducing new systems like BOM software, the natural inclination is often to resist change. Employees might worry that their routines and jobs are on the line. This kind of pushback can manifest in many ways, from reluctance to engage with new technology to outright refusal to use it.
A big part of overcoming this resistance ideally hinges on solid communication and training. Proper guidance about why the software is being introduced and how it can make jobs easier often eases the tension in the workplace.
There's a saying, "You can lead a horse to water, but you can't make it drink." Well, no one can force someone to embrace new tech, but giving employees the full picture—specifying how the software can ease their workload, improve accuracy, and facilitate collaboration—can be a game changer.
- Encourage managers to lead by example, showcasing the benefits they themselves have gained from the software.
- Conduct training sessions that focus not just on how to use the software, but also on the value it brings to their work.
By addressing concerns up front and creating a culture that embraces change, businesses can better prepare their teams for the shift.
Integration Issues with Existing Systems
Adopting new BOM software often leads to a major headache if it doesn’t play well with the systems already in place. Integration issues can slow down processes or, in the worst-case scenario, disrupt operations entirely. Integrating various software tools isn't just a technical task; it requires a thoughtful plan and thorough testing.
In many cases, businesses may already rely on platforms like ERP or project management software. If the new BOM solution doesn’t mesh with these systems, it can create data silos. These silos can prevent different departments from obtaining or sharing important information—resulting in miscommunication and inefficiencies.
Before diving into software selection, organizations should evaluate their current infrastructure and define clear integration objectives. Here are some considerations:
- Compatibility: Ensure the new BOM software can effectively communicate with existing systems.
- Data Migration: A plan must be in place to transition data accurately without loss.
- Testing: Before full-fledged implementation, run integration tests to identify potential glitches.
"Failing to prepare is preparing to fail." If a company skips this preparation phase when adopting BOM software, they may find themselves backpedaling instead of moving forward.
Addressing resistance to change and integration troubles head-on can lead to smoother transitions and enhanced operational efficiency. Building a robust foundation for adopting BOM software will ultimately yield long-lasting benefits.
Selecting the Right BOM Software
Choosing the appropriate BOM software is akin to picking the right tool for a craftsman. It can make or break your operations. The right software not only streamlines manufacturing processes but also fosters better collaboration among teams. This section dives into essential aspects of selection that can aid decision-makers in identifying the best fit for their specific needs.
Assessment of Business Needs
When it comes to BOM software, a one-size-fits-all approach simply doesn’t cut it. First off, you need to thoroughly assess your organization’s unique requirements. Begin by asking yourself:
- What specific challenges am I trying to overcome?
For instance, if your team is struggling with tracking inventory, you might need software that excels in data management capabilities. - How large is my product range?
A company producing a handful of items won’t have the same needs as a manufacturer with a vast array of complex products. Tailoring the software ’s capabilities to match the scale of your operation is crucial.
Additionally, involve various departments in the assessment process. Input from production, engineering, and finance can uncover requirements you might not have considered, ensuring a holistic approach to selection.
Evaluating Vendor Reputation and Support
The vendor behind the BOM software can have a significant impact on your experience. Like looking for a good mechanic, you want someone reliable and knowledgeable. Focus on:
- Reputation:
Check online reviews and ratings on platforms like Reddit or industry forums. A vendor with a strong track record can often save you a lot of headaches down the line. - Customer Support:
Consider the level of support offered. Is it 24/7? A responsive support team is worth its weight in gold when you encounter issues, as problems can and will arise.
Assess the vendor's training options too. A good software solution is only as effective as your team’s ability to use it. Vendors that offer training sessions can go a long way in ensuring smooth adoption.
Trial Options and Customer Feedback
Before forking over substantial sums, it’s wise to test the waters. Many software vendors offer trial options that let you explore the system before you commit. Here’s what to do:
- Take advantage of free trials:
Engage fully with the trial. Involve team members in testing the program. Gather their feedback as they navigate the software. Are they finding it intuitive? Does it meet their needs? - Customer feedback:
After the trial, dive into user experiences and success stories, often found on vendor websites or independent review sites. Hearing how others have integrated the software into their workflows provides valuable insight into its suitability.
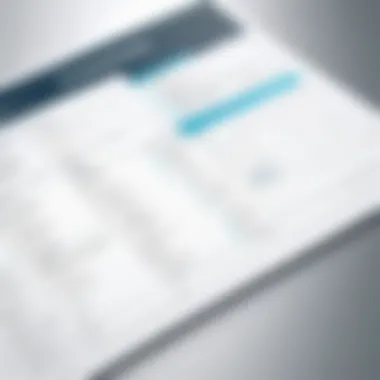
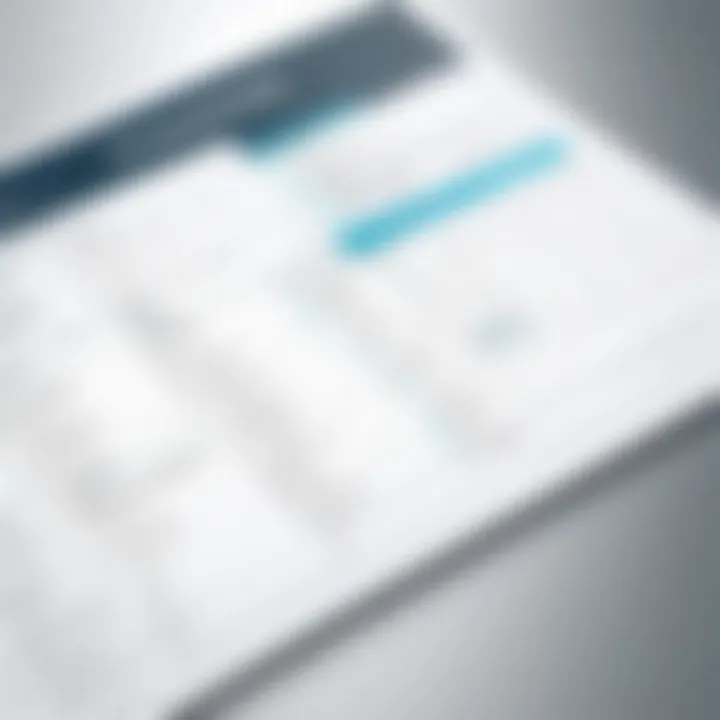
Ultimately, selecting the right BOM software isn’t just about the features it offers; it’s also about its fit with your business culture, processes, and future goals. Solid groundwork in understanding needs, vendor reliability, and getting hands-on experience through trials will pave the way for a successful implementation.
Case Studies and Real-World Applications
Case studies serve as a critical bridge between theory and practice in the context of BOM software. They provide tangible evidence of how software functions in real-world settings, illustrating the questions and concerns faced by various industries. Understanding how other organizations have navigated the implementation of BOM software can offer invaluable insights for decision-makers. The successes and failures documented in these case studies can inform best practices for future undertakings. In this section, we will explore successful implementations and also delve into lessons learned from those that didn’t pan out.
Successful Implementations in Various Industries
Successful implementations of BOM software often showcase how companies across different sectors adapt the tools to their unique needs. For instance, in the automotive industry, companies like Ford have adopted BOM software not just for organizing components but for integrating supply chains more cohesively. By using software to create a centralized view of inventory and production processes, they minimize delays and ensure better handling of logistics. The experience at Ford emphasizes the importance of integration with existing systems which can bolster the overall efficiency of production.
Another classic example comes from the pharmaceutical sector, where Johnson & Johnson leveraged BOM software to streamline their complex manufacturing operations. The regulations in pharmaceuticals are strict, and the traceability of materials is not something to take lightly. Their case highlights the role of BOM software in maintaining compliance while also managing changes in product lines efficiently. With version control and real-time tracking capabilities, they improved their regulatory reporting processes.
- Key Takeaways from Successful Implementations:
- Enhanced communication across teams
- Improved traceability and compliance management
- Increased efficiency in the supply chain
Lessons Learned from Failed Integrations
While success stories inspire confidence, failed integrations of BOM software serve as sobering reminders of what can go wrong. A notable case is that of a mid-sized electronics manufacturer. They decided to adopt a robust BOM system, hoping to better manage parts and streamline workflows. However, the implementation became mired in challenges. They didn’t appropriately engage their team during the transition, leading to significant employee pushback and misunderstanding of the software's functionality. As a result, the project was deemed a failed integration, costing them valuable time and resources.
This particular scenario stresses the significance of user buy-in and thorough training when introducing new technology. Understanding the workflows and hesitations of end-users is paramount. Moreover, overlooking the need for integration with legacy systems is another common misstep.
"The road to success is dotted with many tempting parking spaces."
- Will Rogers
In a different sector, a startup in the retail space failed to account for scalability in their BOM software selection process. Initially, the software seemed to meet their requirements, but they rapidly outgrew its capacity. This scenario highlights that not only the immediate needs should be considered but also potential future growth.
- Lessons to Learn from Failed Integrations:
- Engage users in the decision-making process
- Ensure proper training and onboarding
- Consider scalability along with current business needs
In summary, both successful cases and lessons from failures equip organizations with the knowledge to navigate their implementations with greater prudence. With the complexities associated with BOM software, understanding these real-world applications adds depth to the conversation around its utility and effectiveness.
Emerging Trends in BOM Software
In the fast-paced world of manufacturing and product design, keeping pace with emerging trends in Bill of Materials (BOM) software is crucial. These trends often dictate how effectively organizations can manage resources, streamline operations, and maintain competitive edges. Furthermore, understanding these developments ensures that firms can leverage the best tools available for their specific needs and objectives.
Automation and AI Integration
Automation stands to revolutionize the role of BOM software significantly. By incorporating artificial intelligence, companies tap into a toolkit that not only reduces human error but also enhances efficiency across the board. Tasks that were once manual, requiring close attention to detail, can now be automated. For example, data entry procedures can be streamlined so that changes in material specifications are reflected in real-time across all relevant documents, saving considerable time and effort.
Moreover, AI can aid in predictive analysis, using historical data to forecast material requirements more accurately. This integration not only ensures timely availability of parts but also minimizes excess stock, so companies avoid tying too much cash into inventory. After all, nobody wants to see dollars sitting on shelves rather than in the bank.
"The road to efficiency is paved with automated solutions. Organizations that embrace automation can expect improvements in both turnaround times and workforce morale."
Cloud-Based Solutions
Another trend that's hard to ignore is the shift toward cloud-based solutions. The shift represents a significant departure from traditional on-premises setups, giving organizations the flexibility they crave. With cloud-based BOM software, teams can collaborate in real-time, regardless of their physical location. Illustrated by the rise of remote working models, the ability to access and update BOM data from anywhere has become a vital necessity.
Additionally, cloud solutions often provide comprehensive security features, ensuring that sensitive material information remains protected against unauthorized access. They also enable continuous software updates without the hassle of manual installations, keeping your BOM tools in line with the latest technological advancements.
Practically speaking, this means that smaller companies can access sophisticated tools previously available only to larger corporations. The scalability factor allows them to grow without the usual tech headaches. Every user can enjoy the benefits of high-grade software, leveling the playing field irrespective of company size.
As we venture deeper into an age dominated by tech advancements, staying informed about trends in BOM software assures that organizations can better anticipate market demands and make strategic decisions that align with their growth objectives.
Culmination
In wrapping up this comprehensive guide on BOM software, it's crucial to underscore the myriad ways such systems can revolutionize manufacturing and design processes. The advancement in technology has not only shaped the capabilities of BOM software but also its significance in streamlining operations. Emphasizing traceability, accuracy, and integration, BOM software serves as a linchpin for businesses looking to improve efficiency and bottom-line results.
In today’s competitive landscape, clarity and precision in materials and product structuring are not just beneficial, they are utterly essential. Without a robust BOM system, organizations risk miscommunication and errors that can lead to extensive delays and increased costs. By harnessing the various features outlined throughout this guide, companies can solidify their position and pivot toward innovation and excellence in their practices.
"In manufacturing, it's not just about what you make, but how well you manage your resources that determine your success."
Summary of Key Insights
- Critical Role of BOM in Manufacturing: BOM software bridges the gap between engineering, manufacturing, and supply chain, ensuring that materials are accurately accounted for throughout the production cycle.
- Enhanced Collaboration: Teams working on the same project can access a single source of truth, improving collaboration and decision-making which can ultimately lead to faster project completions.
- Data-driven Decisions: With integrated analytical tools, companies can extract valuable insights that facilitate informed decisions. This ability can separate thriving businesses from those struggling to adapt.
- Long-term Cost Savings: Implementing BOM software, despite the initial investment, typically results in significant cost savings over time due to improved resource management and reduction of waste.
Final Recommendations for Buyers
As potential buyers of BOM software, it is recommended to keep the following in mind:
- Understand Business Needs: Before making any software choice, clearly define your organization’s specific requirements. Conduct internal assessments to align features with goals.
- Choose a Reputable Vendor: Research vendors and their market reputation. Look for companies known for good customer service and support, as this will be invaluable after you implement the system.
- Take Advantage of Trials: Many vendors offer trial periods. Utilize this feature to assess suitability without heavy commitments. Feedback from teams during this phase can illuminate potential issues or unique needs.
- Stay Updated on Trends: Keep an eye on emerging trends like AI integration and automation. Solutions that adapt to industry changes will likely offer greater longevity and relevance for your business.