Unraveling the Sage Warehouse Management System
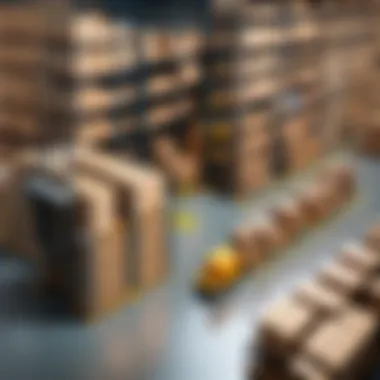
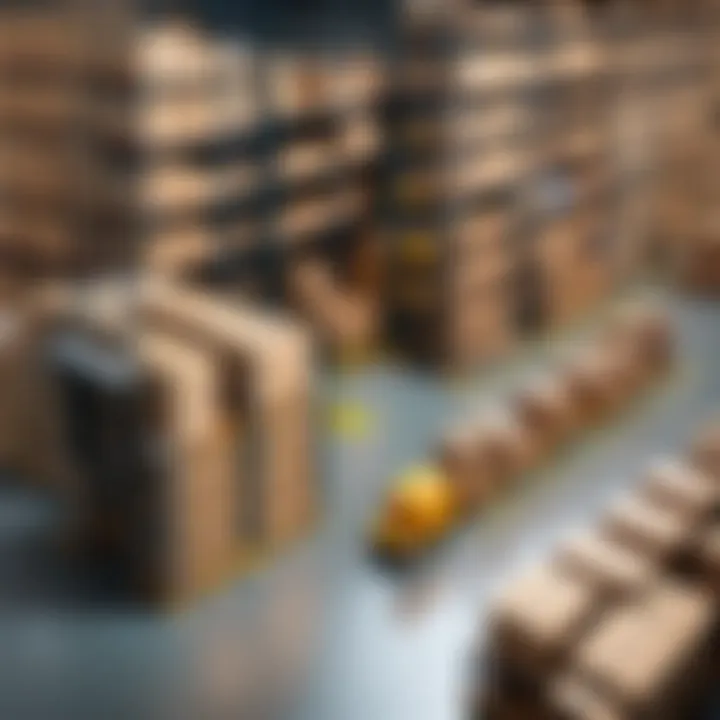
Intro
The logistics industry faces increasing demands, pushing companies to adopt more effective solutions. The Sage Warehouse Management System emerges as a key player in this arena by optimizing operational efficiency. Understanding this system is crucial for industry advisors and decision-makers who seek to enhance their warehousing strategies.
This article dissects various aspects of the Sage Warehouse Management System. It will focus on its key features, pricing models, and the user experience, providing a comprehensive guide. Those engaged in supply chain management and inventory control will find this information valuable for making informed decisions.
Foreword to Sage Warehouse Management System
The Sage Warehouse Management System serves as a cornerstone in the ever-evolving landscape of logistics and warehousing. Understanding its core functionalities is crucial for professionals and businesses aiming to streamline operations. This integrated software brings forth a multitude of benefits that cannot be overlooked.
In today's fast-paced markets, efficiency and accuracy are paramount. The Sage system enhances visibility and control over inventory, which is essential for informed decision-making. By centralizing data, businesses can tackle challenges like stock discrepancies and fulfillment delays head-on. Moreover, the utilization of real-time information can lead to substantial operational improvements.
Importance of the Sage Warehouse Management System
In a competitive business environment, companies must adapt swiftly. The importance of adopting systems like Sage cannot be understated. This software solution provides tailored functionalities that address specific warehousing needs.
A significant part of its appeal lies in its flexibility. Businesses of varying sizes can implement it according to their unique challenges. Whether dealing with fluctuating inventory levels or complex order requirements, Sage can offer solutions that fit. This helps in minimizing overhead costs while maximizing productivity.
Benefits of Implementation
- Centralized Data Management: Sage assists businesses in maintaining a cohesive database. Information about stock levels, orders, and returns is accessible in real-time, promoting greater transparency during operations.
- Enhanced Inventory Control: The software helps in tracking and managing stock accurately. This reduces the risk of overstocking or stockouts, which can deteriorate customer satisfaction.
- Scalability: As a business grows, so do its warehousing needs. Sage adapts to these changes without requiring significant system overhauls.
Implementation is not without its considerations. The initial setup may present some challenges, but the return on investment can be substantial. Organizations are increasingly recognizing that investing in systems such as this one may very well be the competitive edge needed in their sector.
In this article, we will explore the various facets of the Sage Warehouse Management System in detail. From analyzing its key features to evaluating user experience and discussing future trends, this comprehensive examination aims to guide decision-makers in navigating their options in warehouse management solutions.
"The right warehouse management system can transform logistics operations, leading to improved efficiency and cost-effectiveness."
By delving into these topics, the article seeks to provide a thorough understanding of how the Sage Warehouse Management System aligns with contemporary supply chain needs.
Key Features of Sage Warehouse Management System
The Sage Warehouse Management System (WMS) grants businesses the tools necessary to manage their warehouse operations efficiently. Its significance lies not only in improving workflows but also in optimizing overall productivity. The system integrates various functions such as inventory management, order fulfillment, and real-time tracking, allowing organizations to streamline their processes. Each feature plays a crucial role in enhancing these aspects, ultimately leading to a balance of efficiency and effectiveness.
Inventory Management Capabilities
Inventory management is at the core of any warehouse operation, and Sage's capabilities offer substantial benefits. The system allows businesses to maintain precise counts of stock levels while providing insights into stock movement and turnover rates. With features like automated reordering and batch tracking, companies can ensure they never run low on essential items. This proactive strategy prevents stockouts that can hinder service quality. Moreover, the system supports multiple storage methods, adapting to the unique needs of the warehouse, whether it employs pallet racking, shelving, or other configurations.
Order Fulfillment Processes
Efficient order fulfillment is essential for customer satisfaction. The Sage WMS enhances this process via advanced picking and packing features. The system employs various picking methodologies, such as wave picking or zone picking, tailored to the specific needs of the warehouse. This flexibility allows staff to fulfill orders swiftly and accurately. Integration with shipping solutions further accelerates dispatch times, streamlining logistics.
Real-time Data Tracking
Real-time data tracking is a unique strength of the Sage Warehouse Management System. It enables users to access current inventory levels, order statuses, and warehouse activities at any moment. This immediate visibility aids in decision-making, allowing managers to identify issues as they occur. By leveraging such data, businesses can enhance their operational strategies and respond promptly to market fluctuations or customer demands. The accuracy of real-time data also contributes to better planning and forecasting, ensuring that operations are aligned with expected outcomes.
Integration with Other Software Solutions
To maximize operational potential, the Sage WMS integrates effortlessly with other software solutions, such as accounting or CRM systems. This integration fosters a unified platform, minimizing errors that arise from manual data entry. Users can synchronize financial data, customer information, and inventory levels across all software, providing a holistic view of business performance. The ability to connect various systems is essential, as it supports a seamless flow of information. Companies gain efficiency by reducing redundancies and ensuring that every department operates with up-to-date data.
"Efficient integration can significantly amplify productivity, leading to sustained business growth."
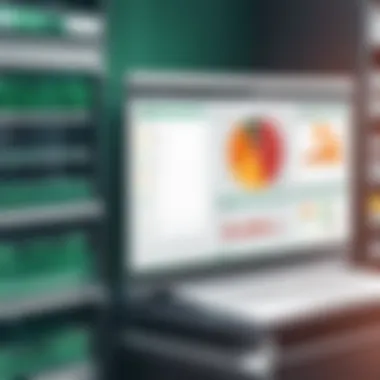
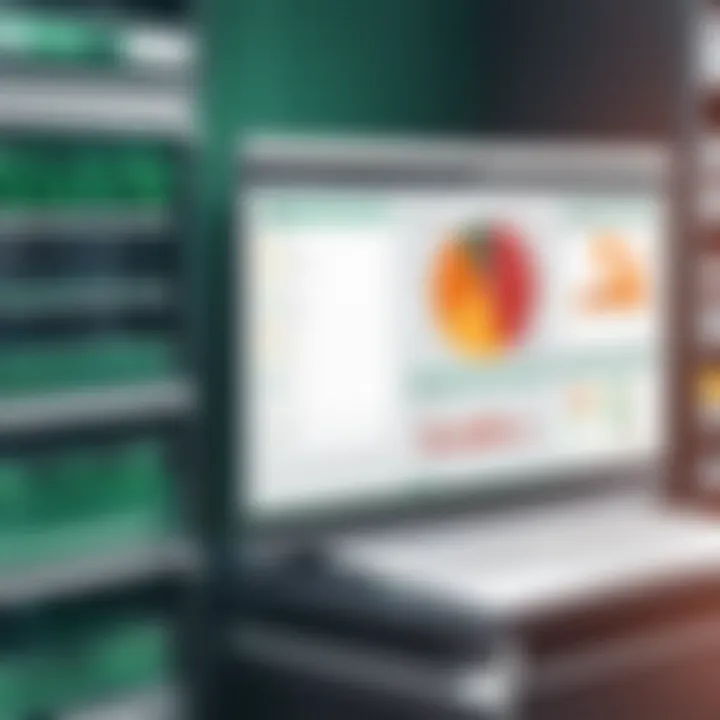
Advantages of Implementing Sage Warehouse Management System
Implementing the Sage Warehouse Management System offers numerous advantages for businesses looking to streamline their warehousing operations. The shift towards automated solutions in logistics reflects an urgent need for accuracy and efficiency. This system addresses these needs by enhancing operational processes while minimizing errors and delays. The significance of understanding these advantages lies in the potential for impactful changes in your supply chain management. Recognizing how the Sage system can transform warehouse operations better equips decision-makers and IT professionals to make informed choices.
Enhanced Operational Efficiency
The primary benefit of the Sage Warehouse Management System is increased operational efficiency. By automating many processes, the system reduces the time and effort needed for routine tasks. This software centralizes data management which allows for quicker access to critical information. For example, employee time spent on inventory counts or order processing can be significantly reduced, freeing up resources for more strategic tasks.
Moreover, inventory tracking becomes seamless. With the integration of RFID technology and barcoding, inventory items can be scanned in real-time. This leads to faster processing speeds and reduces the likelihood of human error. Efficiency gains are measurable in terms of throughput. Companies witness a growth in the number of orders processed, which ultimately results in better service levels and customer satisfaction. Multiple case studies demonstrate the positive impact of this efficiency on overall business performance.
Improved Inventory Accuracy
Optimized inventory management is a crucial element of warehouse operations. The Sage Warehouse Management System enhances inventory accuracy through real-time updates and systematic tracking. By creating a single source of truth, companies can avoid the pitfalls of disparate information silos. This is essential in preventing stock discrepancies that can lead to financial losses and customer dissatisfaction.
The accuracy of inventory has critical implications. When stock levels are correct, it minimizes the risks of overstocking or stockouts, which can disrupt operations. Users can monitor stock movements effectively and rely on analytics to make data-backed decisions. In turns of reporting, the system can provide insights into trends that inform purchasing decisions. Overall improved accuracy not only saves time during audits but also ensures that businesses maintain better control over their supply chain.
Cost Reduction Strategies
Implementing the Sage Warehouse Management System ultimately leads to numerous cost savings across warehousing operations. The efficiency gained from streamlined processes translates directly to lower operational costs. For instance, by reducing labor hours spent on manual processes, companies can optimize labor costs significantly. This does not just refer to salaries; it encompasses overtime and error-related costs where inefficiencies can create financial liabilities.
Transportation costs also see a potential reduction as optimized routing and inventory management decrease the requirement for last-minute shipping solutions. Companies can capitalize on economies of scale when they have accurate data on stock levels and order volumes, allowing for smarter shipping decisions.
Furthermore, reduced errors in order fulfillment lower the rate of returns and associated costs. Adopting the Sage system positions an organization to monitor its expenses closely, paving the way toward robust fiscal health.
In summary, the Sage Warehouse Management System is not merely a software solution; it is a comprehensive tool that addresses key operational pain points, fostering a more efficient and cost-effective warehouse environment.
Challenges in Sage Warehouse Management System Adoption
The implementation of a Warehouse Management System (WMS) like Sage is not without its challenges. Understanding these difficulties is crucial for organizations that are contemplating the adoption of such a system. By examining the hurdles associated with Sage's implementation, decision-makers can better prepare, thus reducing potential disruptions and maximizing the system's benefits.
Complexity of Installation
Installing the Sage Warehouse Management System can be a complex venture. Companies often expect a straightforward setup process, but the reality is more layered. Several factors contribute to this complexity. The company's existing infrastructure must be thoroughly assessed to ensure compatibility with Sage's requirements. Data migration is another key issue. Transferring vast amounts of inventory data from outdated systems can introduce errors or data loss.
Moreover, customization needs can further complicate the installation. Each business has unique processes, and tailoring the system to fit these can be time-consuming. Organizations should allocate sufficient time in their project plans for this stage. A rushed installation may lead to burnout or mistakes that could jeopardize future operations.
Training Requirements for Staff
Training is a significant concern when adopting any new technology. The success of the Sage Warehouse Management System relies heavily on how well the staff understand the software. Poorly trained employees can lead to operational inefficiencies, mismanagement of inventory, and potential losses.
Training should be thorough and ongoing. Initial training sessions can help staff navigate the system, but continuous learning opportunities must be established to accommodate updates and upgrades. Additionally, the diverse skill levels among employees present a challenge. Tailoring training programs to vary skill sets ensures that everyone is comfortable with the WMS, which ultimately leads to better utilization of its features.
Cost Implications of Implementation
Adopting the Sage Warehouse Management System comes with associated costs that extend beyond initial software purchases. Organizations must consider not just the direct fees for the system itself but also the broader financial implications. These include installation, training, and potential downtime during the transition period.
Furthermore, companies should analyze the long-term financial impacts. Maintenance costs, upgrade fees, and any additional hardware necessary will contribute to the total investment. Organizations must conduct a cost-benefit analysis to weigh these costs against the projected efficiency gains. Effective planning can ultimately minimize unexpected expenses and ensure the WMS adoption remains within budget.
User Experience and Feedback
User experience is crucial when evaluating any system, including the Sage Warehouse Management System. In the context of warehousing, a positive user experience can lead to increased productivity, lower training costs, and enhanced employee satisfaction. Understanding user feedback is essential for several reasons. It highlights the effectiveness of the system in real-world settings and identifies potential areas for improvement.
Insights from users help in making informed decisions regarding system enhancements. When utilizing a software tool like Sage, decision-makers can look into various aspects of user experience to gauge how well the system meets operational needs.
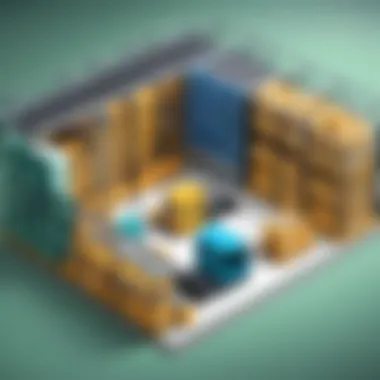
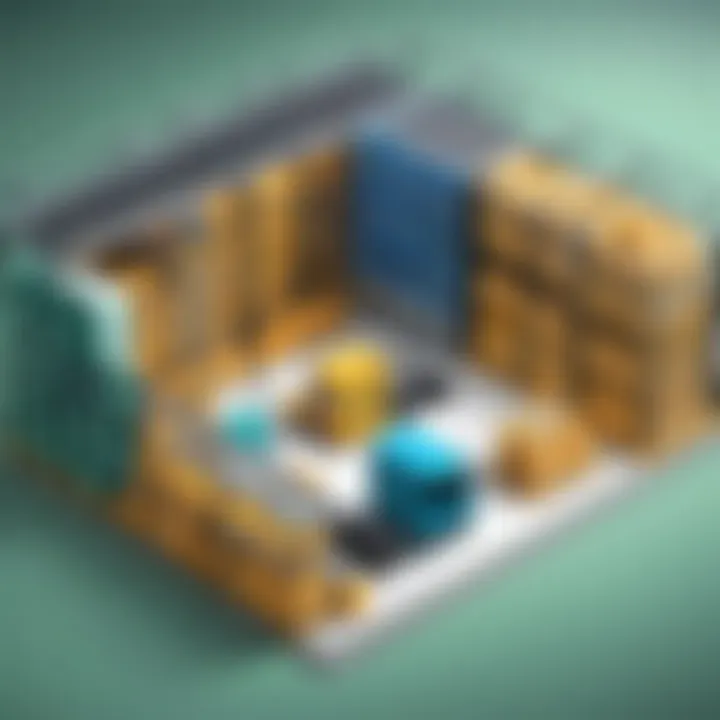
Case Studies from Different Industries
Case studies offer concrete examples of how organizations successfully implement the Sage Warehouse Management System across various sectors. For instance, a retail company might find that the system significantly reduces order processing times, leading to quicker customer deliveries. Another case could involve a manufacturing firm, where Sage's advanced inventory management capabilities help streamline stock replenishment, thus reducing downtime.
Across industries, benefits may include:
- Retail: Enhanced order fulfillment efficiency.
- Manufacturing: Optimized inventory tracking and restocking.
- Wholesale: Better demand forecasting and management.
Each industry comes with unique challenges, and Sage's adaptability plays a vital role in overcoming these obstacles. These case studies emphasize not just the successes but also the lessons learned during implementation, offering practical advice to future adopters.
Common User Challenges
Despite the system's strengths, users often encounter challenges when using the Sage Warehouse Management System. Common issues include:
- Learning Curve: This is a significant factor, particularly for employees not familiar with technology. It can slow down initial deployments as staff might struggle with system navigation.
- Integration Difficulties: Connecting Sage with existing software solutions may present some technical challenges, particularly if legacy systems are involved.
- Inflexible Processes: Some users report that certain processes within the system are not easily customizable, which can lead to operational inefficiencies.
These challenges indicate the importance of thorough training and robust support during the initial phases of implementation.
"Understanding user challenges is just as important as recognizing triumphs in any software system."
Ultimately, collecting feedback systematically can empower organizations to make adjustments that enhance user engagement and overall performance of the Sage Warehouse Management System.
Comparison with Competitor Solutions
In an increasingly competitive landscape, evaluating the Sage Warehouse Management System alongside its rivals is crucial for decision-makers. Understanding how Sage stands apart allows businesses to make informed choices that align with their operational goals. This section discusses key differentiators and market positioning, emphasizing why such comparisons matter in selecting the right warehouse management solution.
Key Differentiators
Sage Warehouse Management System has distinctive features that set it apart from other solutions. These features focus on flexibility, user-friendly interfaces, and scalability. Here are some of the unique aspects:
- Customization Options: Unlike many competitors, Sage allows significant customization to fit specific business needs. This flexibility ensures that users can adapt the system as their operations evolve, thus promoting longevity in software use.
- Comprehensive Integration: Sage offers seamless integration capabilities with existing enterprise systems, such as Sage X3 or Sage Business Cloud. This creates a cohesive workflow that optimizes data sharing and ensures that all departments benefit from warehouse insights effectively.
- Robust Reporting Tools: Advanced analytics and reporting features in Sage enable users to extract valuable insights from their operations. This capability enhances decision-making and provides a clearer picture of inventory levels, order statuses, and more.
These differentiators signify not just a competitive edge, but also an alignment with modern business needs that prioritize adaptability and efficiency.
Market Positioning
In terms of market positioning, Sage occupies a unique space within the warehouse management software industry. It caters primarily to medium to large enterprises, focusing on sectors like retail, manufacturing, and e-commerce. This positioning showcases several strategic advantages:
- Established Reputation: Sage has a longstanding reputation in the business software realm. This history instills a sense of trust among potential users, as it demonstrates reliability and proven results over time.
- Focus on Supply Chain Alignment: Sage places great emphasis on ensuring that its warehouse management is not in isolation but integrated with the broader supply chain. This approach attracts enterprises that are looking for comprehensive solutions that bridge various operational silos.
- Targeted Vertical Solutions: Sage tailors its offerings to specific industries, enhancing its appeal. By providing solutions that are uniquely designed to meet the challenges of certain sectors, Sage positions itself as a go-to choice for those industries, thereby creating niche expertise.
"A clear understanding of a product's market positioning can drastically influence its usability in a specific field."
Integration with Supply Chain Management
The integration of the Sage Warehouse Management System with overall supply chain management is pivotal in enhancing operational coordination and responsiveness. This relationship provides a framework through which warehouses can operate not just as isolated units, but as integral components of larger logistical ecosystems. A seamless integration ensures that inventory levels align with demand forecasts, directly impacting the efficiency of distribution.
Aligning Warehouse Operations with Supply Chain Needs
Aligning warehouse operations with supply chain needs requires a clear understanding of the interplay between forecasting, inventory management, and fulfillment processes.
To ensure that warehouse activities are synchronized with broader supply chain strategies, decision-makers must consider:
- Demand Forecasting: Utilizing accurate demand projections allows warehouses to adjust their inventory levels appropriately.
- Inventory Management Systems: Employing sophisticated inventory systems within Sage helps to maintain optimal stock levels, reducing the chances of overstocking or stockouts.
- Communication Channels: Consistent communication between warehouse teams and supply chain planners is essential. This relationship allows for immediate responses to demand fluctuations.
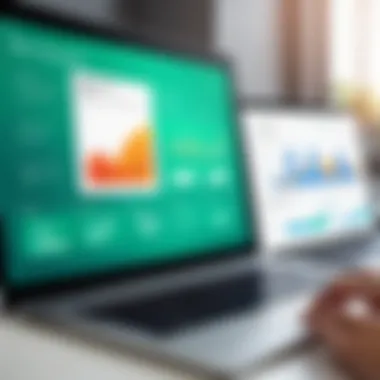
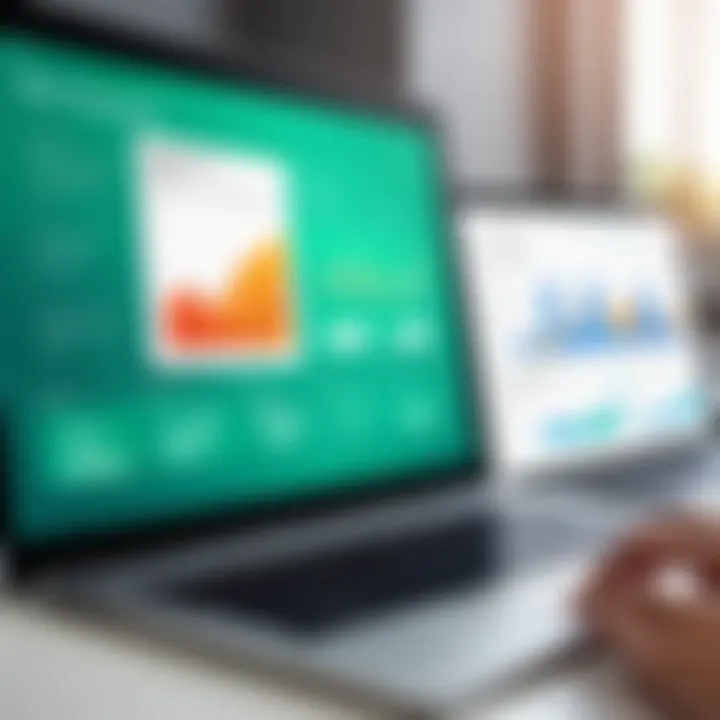
With these elements in place, warehouses can greatly enhance their role within the supply chain, ensuring agility and responsiveness to market changes.
Utilizing Real-time Data in Decision Making
Real-time data utilization stands at the forefront of effective decision-making within supply chain management. The integration of Sage Warehouse Management System allows for continuous monitoring of inventory and order status. This capability provides several advantages.
- Informed Decision-Making: Having access to real-time information helps managers make timely decisions regarding stock replenishment and resource allocation.
- Responsiveness to Market Changes: With immediate data insights, businesses can quickly adapt to unexpected demand changes or supply chain disruptions.
- Enhanced Operational Transparency: Real-time data fosters a transparent operational environment where all stakeholders can access up-to-date information, promoting mutual awareness.
- Improved Resource Allocation: Decision-makers can identify underutilized resources, allowing for better allocation and ultimately reducing operational costs.
"Real-time data provides businesses the agility to pivot efficiently, responding to the demands of customers without delay."
Integrating real-time data insights into warehouse operations facilitates informed decision-making that aligns closely with supply chain objectives. This results in a coherent strategy that supports the entire operational structure.
Future Trends in Warehouse Management Systems
The landscape of warehouse management systems (WMS) is evolving rapidly. As businesses strive for greater efficiency and adaptability, it becomes essential to explore future trends that can influence operational strategies. Understanding these trends allows decision-makers to align their tools and processes with industry innovations. This foresight plays a key role in optimizing operations, reducing costs, and enhancing overall productivity.
Automation and Robotics in Warehousing
Automation is no longer a luxury; it has become a necessity in modern warehousing. Many organizations are investing in robotics to handle various tasks within the warehouse. From automated picking systems to autonomous mobile robots, technology is significantly changing the way warehouses operate.
The benefits of incorporating automation are manifold:
- Increased Efficiency: Automation reduces the time taken to pick and pack orders, ensuring faster fulfillment.
- Consistent Accuracy: Robots minimize human errors during inventory management, leading to improved stock accuracy.
- Cost Savings: Although the initial investment can be substantial, the long-term savings in labor costs and increased throughput can justify these expenditures.
Challenges do exist, however. Implementing robotic systems requires significant planning and integration with current software solutions, such as Sage Warehouse Management System. Companies must assess their operational needs carefully before proceeding with such technology.
"Automation is vital to maintain competitive advantage in the warehousing sector."
Predictive Analytics and Data-Driven Insights
Predictive analytics is transforming decision-making processes in warehouse management. This trend leverages data to forecast demand, optimize inventory levels, and enhance operational performance. Utilizing advanced algorithms, businesses can ascertain patterns and trends that may not be immediately apparent.
Key aspects of adopting predictive analytics include:
- Enhanced Demand Forecasting: By analyzing historical data and market trends, companies can predict changes in demand more accurately.
- Optimized Inventory Management: Data-driven insights enable better inventory control, reducing excess stock and avoiding stockouts.
- Improved Operational Efficiency: Analysis can reveal inefficiencies in current operations, allowing for targeted improvements.
Data is at the core of these predictive capabilities. However, organizations must ensure that they have the right infrastructure and tools to collect and analyze this data effectively. Integration with existing systems like Sage can amplify these benefits, providing a robust platform for data usage.
In the shift towards more sophisticated warehouse management, understanding these trends is critical. It equips decision-makers with the knowledge to make informed, strategic decisions that can significantly enhance warehouse operations.
Finale: Evaluating Sage Warehouse Management System for Your Needs
The decision to implement the Sage Warehouse Management System is significant. This conclusion draws together the various themes discussed throughout the article. It is essential to understand how this system aligns with the unique operational requirements of your organization. By evaluating key features, benefits, and potential challenges, you can make an informed choice that enhances efficiency and productivity within your warehouse environment.
When deliberating the adoption of the Sage Warehouse Management System, consider examining its core functionalities. This system provides integrated inventory management, real-time data tracking, and seamless integration with other software solutions. These functionalities play a crucial role in optimizing operations and ensuring accuracy in inventory levels. Failure to assess these features could lead to ineffective management and increased operational costs.
Moreover, recognize the potential advantages of this system. Enhanced operational efficiency, improved inventory accuracy, and cost reduction strategies can transform your warehouse management processes. Yet, it is equally critical to be aware of the challenges involved. Installation complexity, staff training requirements, and implementation costs can arise. Addressing these aspects will help in determining if the benefits outweigh the challenges for your particular context.
Final Considerations
Before committing to the Sage Warehouse Management System, reflect on your organizationβs specific needs. Each business has distinct requirements based on size, complexity, and industry. The solution that works for one organization may not necessarily suit another. Therefore, a thorough assessment of your warehousing needs, including scalability and the ability to integrate with current systems, is vital.
Furthermore, engage with other users and evaluate case studies. Learning about real-world applications and experiences can provide insight into how well the system may serve your operations.
Making an Informed Decision
To ensure a sound decision, it is beneficial to gather comprehensive information on the Sage Warehouse Management System. Here are steps to consider:
- Conduct a Needs Assessment: Analyze your current warehousing operations to identify specific areas requiring improvement.
- Engage Stakeholders: Include team members from various departments to obtain diverse perspectives on the functionalities needed.
- Evaluate Cost vs. Benefit: Assess potential costs against the anticipated operational gains from implementing the system.
- Seek Demos and Trials: Utilize available demos to gain hands-on experience with the software before finalization.