Essential Preventive Maintenance Inspection Checklist
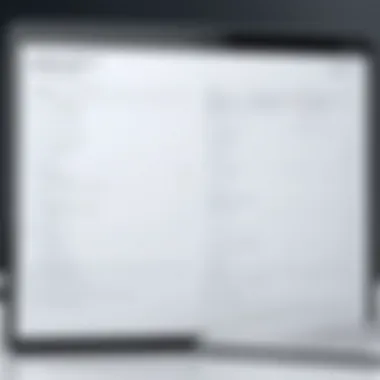
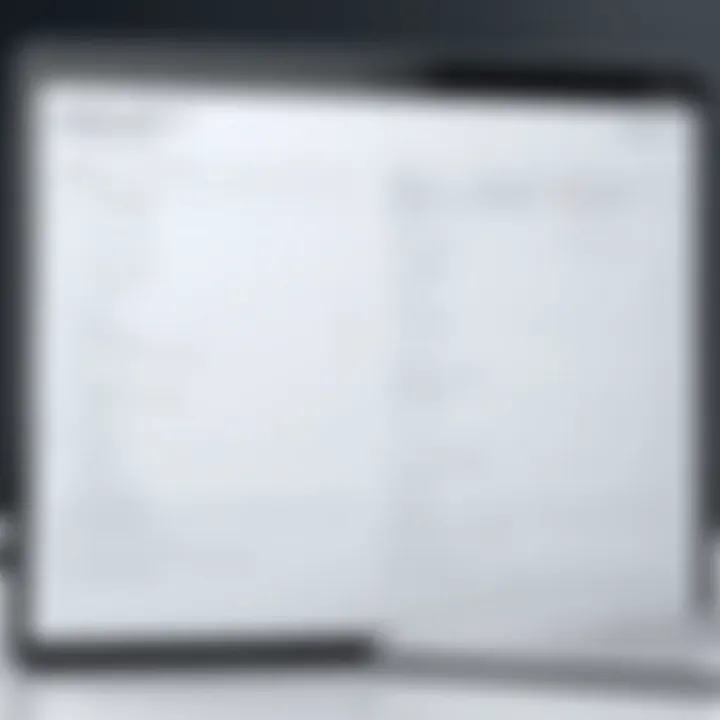
Intro
Preventive maintenance inspections are crucial in today's operational landscape. They offer a structured approach to maintaining systems and equipment, reducing downtime and ensuring operational success. The significance of these inspections extends across various industries, from information technology to manufacturing. Understanding the underlying principles and the checklist involved can significantly impact efficiency and safety. This guide delves into the intricacies of preventive maintenance inspection checklists, catering to the needs of decision-makers and industry professionals.
Key Features and Functionalities
Comprehensive Overview
A well-structured preventive maintenance inspection checklist is essential for tracking critical maintenance tasks. It helps organizations avoid equipment failure and maintain optimal performance. Key features include:
- Systematic Approach: The checklist ensures that all maintenance tasks are executed consistently and thoroughly.
- Customization Options: Organizations can tailor the checklist to their specific needs, accounting for unique systems and processes.
- Documentation: It provides a clear record of inspections performed, which can be referenced for compliance and audits.
- Frequency Scheduling: The checklist aids in determining how often inspections should occur, promoting proactive maintenance.
These features support effective maintenance strategies that enhance reliability and ensure the safety of systems.
Target Users
The target audience for preventive maintenance inspection checklists includes:
- IT Professionals: Responsible for system uptime and performance within organizations.
- Facility Managers: Ensure all electrical, plumbing, HVAC, and other systems function as intended.
- Engineers and Technicians: Directly involved in maintaining, troubleshooting, and repairing equipment.
- Business Owners and Decision Makers: Looking to optimize costs and minimize operational risks.
By understanding the target users, organizations can develop effective training and guidelines for using the checklist. This ensures that all relevant parties understand their roles in the preventive maintenance process.
Pricing Models and Cost Analysis
Breakdown of Pricing Tiers
Investing in preventive maintenance inspection tools encompasses various pricing models. The main options can usually be categorized into:
- Basic Packages: Ideal for small businesses; they include essential checklist features without advanced analytics.
- Intermediate Packages: Targeting mid-sized organizations, they often include customization and additional features.
- Enterprise Solutions: Comprehensive offerings suited for large corporations, often integrating analytics, cloud storage, and mobile access.
Additional Costs to Consider
Beyond initial investment, it's important to account for ongoing costs. These can include:
- Training Expenses: Proper training for staff to effectively use checklists.
- Software Updates: Fees associated with maintaining and updating software.
- Maintenance of Equipment: Regular checks to ensure tools and systems are functioning properly.
Understanding these aspects helps organizations budget effectively and maximize their preventive maintenance strategies.
"Preventive maintenance is not just a best practice; it is a necessity for optimizing performance and safety across systems."
Finale
Prelims to Preventive Maintenance
Understanding preventive maintenance is crucial for sustaining operational efficiency, reliability, and safety across various systems, both mechanical and software-based. This practice is not merely a reactive measure but rather a proactive strategy that can help organizations stave off significant downtime and costly repairs. The central theme of preventive maintenance is to identify potential issues before they escalate into serious problems, ensuring that both equipment and processes run smoothly.
Definition and Importance
Preventive maintenance refers to routine maintenance activities designed to increase the lifespan of equipment and avoid unexpected failures. This can involve regular inspections, cleaning, and adjustments. The importance of preventive maintenance stems from its ability to facilitate a systematic approach to equipment care. By defining clear maintenance schedules and protocols, organizations can guarantee that nothing is overlooked.
In addition, preventive maintenance plays a vital role in aligning business objectives with operational performance. By integrating preventive maintenance into an organization's culture, it becomes easier to foster a mindset focused on long-term asset management. This necessitates a shift from reactive to planned maintenance, a transition that is essential for any business aiming to enhance productivity and minimize operational risks.
Benefits of Preventive Maintenance
The benefits of preventive maintenance are multifaceted. Firstly, it significantly reduces the likelihood of sudden equipment failures. Regular inspections can uncover wear and tear that, if left unchecked, could lead to breakdowns. Here are some pivotal benefits of incorporating preventive maintenance into organizational activities:
- Cost Savings: Routine maintenance is generally less expensive than emergency repairs. Addressing problems early can save substantial amounts on spare parts and labor costs.
- Increased Equipment Lifespan: Regularly maintained equipment is likely to have a longer operational life compared to units that undergo little to no maintenance.
- Enhanced Safety: Equipment failures can pose significant safety risks. Preventive maintenance helps in identifying potential hazards, thereby safeguarding employees.
- Improved Productivity: Well-maintained systems function more efficiently. This translates to higher productivity and less unplanned downtime.
In summary, preventive maintenance is not just a good practice; it is essential for optimizing performance and safeguarding assets. It promotes a culture of vigilance where potential issues are addressed proactively rather than reactively.
Understanding Inspection Checklists
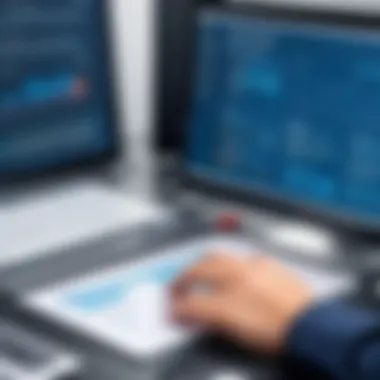
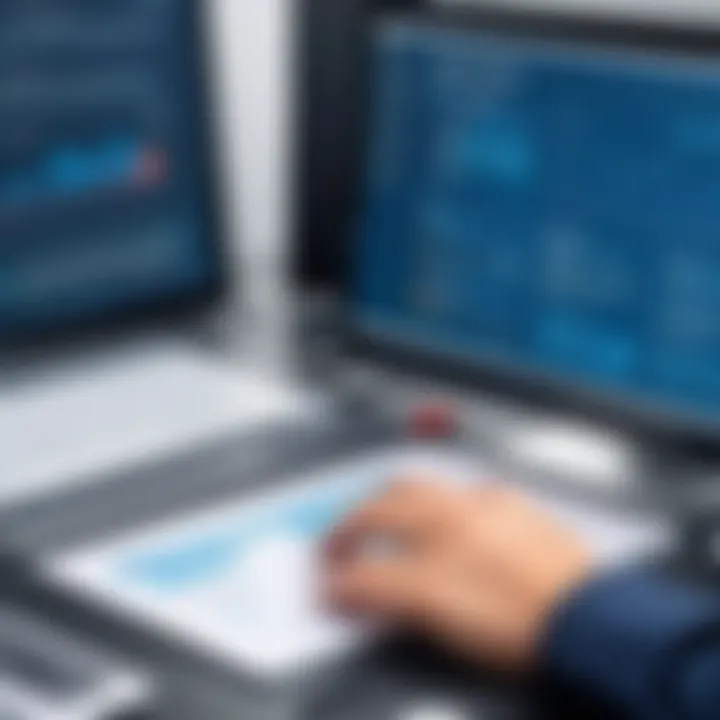
Inspection checklists serve as essential tools in the management of preventive maintenance. They are designed to ensure structured evaluations and systematic monitoring of equipment and systems. By utilizing well-thought-out checklists, organizations can significantly improve their maintenance practices. A checklist clarifies the tasks that need to be completed, helps prioritize actions, and ensures that critical steps are not overlooked.
Creating a robust inspection checklist contributes directly to operational safety and efficiency. The challenges of equipment failure are often linked to neglecting maintenance tasks. Thus, a clear and detailed checklist provides a framework that can curb risks related to equipment malfunction and downtime.
What is a Maintenance Inspection Checklist?
A maintenance inspection checklist is a document that outlines specific tasks and criteria for evaluating the operational state of equipment and systems. It typically includes sections for standard operating conditions, performance indicators, and safety requirements. The primary purpose of this checklist is to facilitate regular evaluations so that any potential problems can be identified and addressed promptly.
The checklist can vary according to the type of equipment being inspected, including but not limited to mechanical, electrical, and software systems. It serves as a guide, allowing maintenance personnel to systematically assess each component and ensure that all necessary checks are performed.
Key Components of a Checklist
Effective maintenance inspection checklists include several key components:
- Specific Tasks: Detailed descriptions of tasks that need to be performed during inspections. They should be clear enough to avoid ambiguity.
- Frequency of Checks: Information on how often different tasks should be performed, which helps ensure that inspections align with the equipmentβs wear and operational demands.
- Responsible Personnel: Identification of who is accountable for performing tasks listed on the checklist. This provides clarity in roles and responsibilities.
- Documentation Space: Areas for notes where inspectors can record findings, actions taken, and recommend follow-ups.
- Criteria for Evaluation: Clearly defined metrics for assessing equipment performance against established standards.
Incorporating these elements into a well-designed checklist can enhance its effectiveness and ensure thorough inspections are applied consistently throughout maintenance routines.
Creating an Effective Preventive Maintenance Checklist
Creating an effective preventive maintenance checklist is critical in ensuring the longevity and reliability of equipment, systems, and processes. It serves as a proactive strategy to avoid potential failures and optimize operational efficiency. A well-structured checklist not only identifies necessary maintenance tasks but also establishes a clear framework to assess individual equipment needs. This, in turn, reduces downtime and enhances productivity across the organization.
Assessing Equipment Needs
Assessment of equipment needs entails evaluating the specific machinery and systems in use. This part of the checklist develops a comprehensive understanding of each item's operational requirements. Decision-makers should consider age, usage frequency, and maintenance history when evaluating needs. Gathering data can include:
- Operational Hours: Understanding how often each piece of equipment is used can guide maintenance frequency.
- Manufacturer Guidelines: Referencing manufacturer specifications provides a baseline for what maintenance is required and when.
- Historical Performance: Reviewing past maintenance records helps identify recurring issues that may need attention.
By systematically assessing these elements, organizations can tailor their maintenance strategies, aligning them with actual equipment conditions.
Identifying Frequency of Inspections
Once equipment needs are assessed, establishing the frequency of inspections is crucial. This ensures that all systems are maintained effectively without overburdening resources. It is good practice to categorize inspections based on operational impact. Consider the following aspects:
- Critical Systems: Equipment integral to operations should have frequent inspections. For example, a data center's cooling system.
- Usage-Based: Increase inspection frequency for equipment that sees intensive use. High usage often leads to faster wear.
- Seasonal Factors: Some systems might require more attention in specific periods. For instance, HVAC systems before cooling or heating seasons.
Creating a schedule that reflects these considerations will provide a balanced approach to maintenance activities.
Standardizing Procedures
To maximize efficiency, standardizing procedures in the checklist is essential. This involves outlining steps to maintain different equipment types and ensuring consistency across the organization. Here are points to include:
- Clear Instructions: Detailed guidelines for each inspection task, so personnel understand what is required.
- Documentation: Maintaining accurate records of inspections, issues found, and repairs made should be compulsory practice.
- Roles and Responsibilities: Define who is responsible for various tasks. Clearly articulating roles enhances accountability.
Standardization helps ensure that maintenance approaches are replicable and easier to follow, setting a benchmark for performance across facilities.
"A well-conceived checklist leads to sustained performance and minimizes unexpected downtimes."
By developing a robust preventive maintenance checklist with key elements addressed thoroughly, organizations can greatly enhance their preventive maintenance strategies. This not only fosters an efficient operation but also aligns maintenance activities with broader strategic objectives.
Common Categories for Maintenance Checklists
In a comprehensive preventive maintenance inspection strategy, categorizing maintenance tasks is crucial. Proper categorization allows for tailored approaches specific to various system types. Moreover, it ensures that no aspect of maintenance gets overlooked. This section will cover the primary categories vital for creating an effective maintenance checklist.
Mechanical Systems
Mechanical systems include machinery and equipment in various industries, such as manufacturing and transportation. Regular inspections are essential to ensure that components function correctly and do not pose risks to safety or efficiency.
Common elements to inspect include:
- Lubrication: Ensuring all moving parts are well lubricated.
- Alignment: Checking that parts are aligned to avoid excessive wear.
- Wear and Tear: Identifying any visibly worn components that need replacement.
Benefits of focusing on mechanical systems include reduced downtime and extended equipment lifespan. By adhering to a strict checklist, organizations can mitigate the risks associated with mechanical failures.
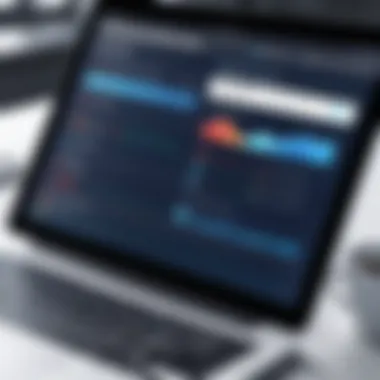
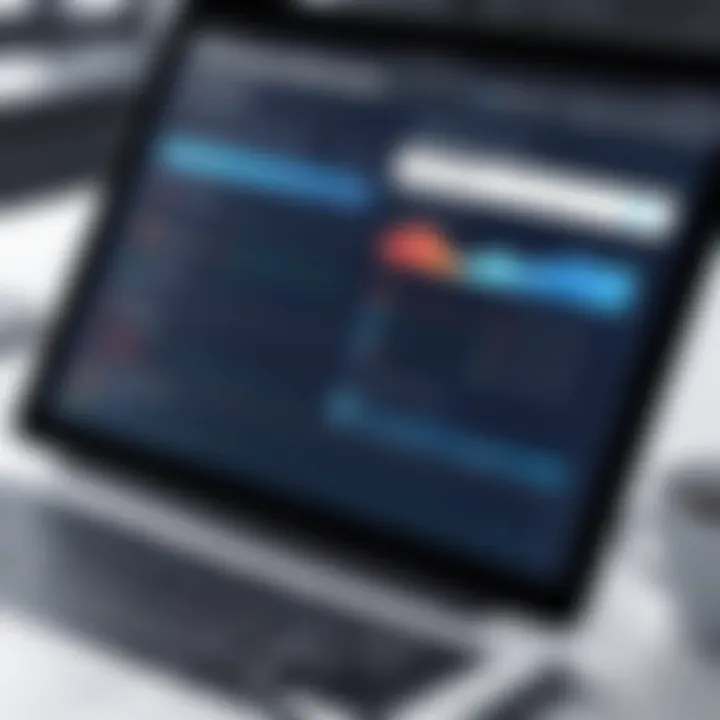
Electrical Systems
Electrical systems are integral to the operation of virtually every modern facility. Maintenance in this category safeguards against failures that can lead to significant operational disruption or safety hazards.
Essential inspection tasks involve:
- Wiring Checks: Examining for fraying or damage to cables.
- Connection Tightness: Ensuring that connections are secure to prevent short-circuits.
- Load Testing: Adopting measures to ensure circuits can handle required loads.
By routinely focusing on these areas, companies enhance the reliability of their electrical systems, which in turn supports overall operational efficiency. This category is often overlooked, yet it can yield practical benefits when managed properly.
Software Systems
In todayβs digital landscape, software systems require just as much attention as hardware systems. Poorly maintained software can result in operational downtime, data loss, and security breaches. A dedicated checklist for software inspections is vital.
Key tasks include:
- Update Management: Regularly applying updates to keep systems secure and performing optimally.
- Backup Verification: Ensuring that data backups occur correctly and are retrievable.
- Performance Monitoring: Using tools to monitor applications for efficiency.
Software maintenance not only protects organizational data but also ensures that operations run smoothly. By paying attention to these elements, decision-makers can better leverage their technological investments, addressing the evolving needs of the business environment effectively without encountering significant disruptions.
Regularly scheduled inspections of these distinct categories can greatly enhance operational longevity and efficiency.
Implementation Strategies for Checklists
Effective implementation strategies for maintenance checklists are crucial to their success. A well-structured checklist can only achieve its potential when it is integrated with the daily practices of an organization. Establishing solid strategies can enhance accountability and ensure that all the necessary checks are performed regularly. This is important to maintaining operational integrity and extending the life of equipment and systems.
Training Staff
Training staff is one of the most important aspects of establishing effective checklists. Employees must understand not only how to use checklists but also their value. Without proper training, personnel may overlook critical points or disregard established procedures.
A robust training program should cover the following areas:
- Understanding Checklists: Employees should grasp what a preventive maintenance checklist is and its role in ensuring system reliability.
- Hands-On Demonstrations: Practical sessions can help staff familiarize themselves with the checklist. This can include real-life scenarios to illustrate task execution within a checklist format.
- Continuous Learning: Maintenance technologies evolve. Customizing training to include periodic workshops will keep staff updated on the latest maintenance protocols and checklist applications.
Integrating Checklists into Daily Operations
Integrating checklists into daily operations ensures that maintenance activities are not seen as additional burdens but as essential parts of regular tasks. When checklists are seamlessly woven into workflows, compliance improves. To achieve this, consider the following:
- Embed Checklists in Workflows: Design workflows that incorporate checklist tasks at the right points. For instance, link checklist usage to machinery operation or troubleshooting processes.
- Use Visual Reminders: Place checklist visuals near equipment or in common areas so they serve as constant reminders. This helps with compliance and encourages accountability.
- Regular Status Updates: Schedule regular meetings to review checklist outputs and address any complications or oversights. This practice keeps staff engaged and emphasizes the significance of the task.
Leveraging Technology for Efficiency
Technology can significantly enhance the efficiency of preventive maintenance checklists. Various tools and software solutions streamline checklist workflows and improve data collection processes. Some advantages include:
- Digital Checklists: Using tablet or mobile applications allows immediate access and updates to checklists. This reduces paper usage and allows for real-time reporting and amendments.
- Data Analytics: Tools can gather data over time, allowing for trend analysis. By reviewing this data, organizations can find patterns that may indicate underlying issues concerning equipment.
- Automated Alerts: Certain maintenance management systems alert staff when scheduled checks are due. This proactive approach minimizes the chances of skipped inspections.
"Effective checklist implementation combines staff training, integration into daily operations, and appropriate technological tools."
Adopting these strategies ensures that maintenance checklists serve their intended purpose and ultimately contribute to a more productive and efficient organizational environment.
Monitoring and Updating Checklists
Monitoring and updating checklists is a critical practice in preventive maintenance. With the fast-paced changes in technology and operational requirements, it is essential to keep checklists relevant and effective. This section explores how regular monitoring can enhance the utility of checklists and the significant advantages of keeping them updated.
Regular Review Processes
Regularly reviewing maintenance checklists ensures they maintain their effectiveness over time. Establishing a systematic review process can lead to significant benefits, including:
- Identification of Obsolete Tasks: Over time, some tasks may become irrelevant due to updates in equipment or procedures. Regular reviews help to identify and remove these items, preventing wasted time.
- Incorporation of Feedback: Feedback from staff who use the checklists can provide valuable insights into their practical application. Regular reviews afford opportunities to incorporate practical suggestions, enhancing the checklist's effectiveness.
- Adaptation to New Technologies: As new technologies are adopted, corresponding updates to checklists are necessary. Keeping a routine for reviews ensures that changes in tools or systems are recognized and addressed in the maintenance process.
The review frequency can be defined by the operational context. For example, daily checks might be necessary for critical systems, while a monthly or quarterly review could suffice for less critical equipment.
Adapting to New Developments
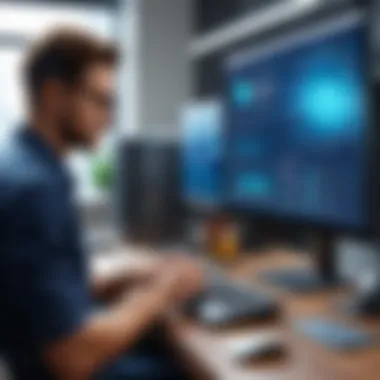
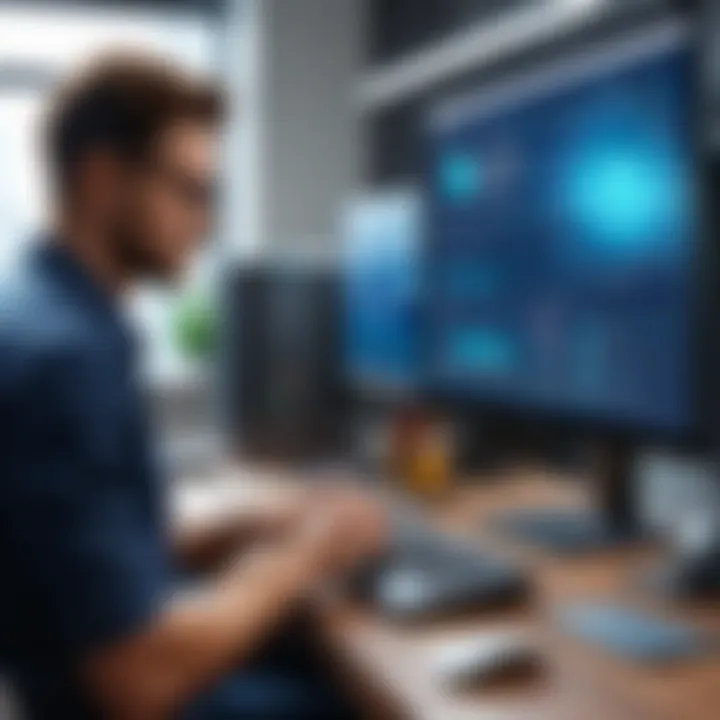
Adapting checklists to new developments is an ongoing requirement in any organization. Failure to adapt can lead to inefficiencies and potential failures. These developments may arise from various sources:
- Regulatory Changes: New regulations can necessitate immediate updates to procedures. Ensuring compliance through regular updates to checklists can minimize risks.
- Technological Advancements: As equipment and software evolve, maintenance needs may change. Checklists should reflect the latest maintenance requirements based on current technology.
- Industry Best Practices: Industries often evolve, with new best practices emerging. Keeping abreast of these practices and implementing them in checklists can enhance maintenance standards.
Keeping checklists current not only assures operational reliability but also signifies a proactive maintenance culture within the organization.
Case Studies on Effective Maintenance Checklists
The significance of case studies on maintenance checklists cannot be overstated. They provide real-world examples of the practical application of preventive maintenance. Such studies not only showcase the effectiveness of checklists but also highlight areas where improvements are needed. In deploying these checklists, organizations can identify trends and patterns that lead to enhanced operational efficiency and reliability. By leveraging case studies, decision-makers can learn from the successes and challenges of others in their field, ultimately creating better maintenance practices.
Industry-specific Applications
Different sectors face unique challenges when it comes to preventive maintenance. For example, in the aviation industry, maintenance checklists are vital for ensuring aircraft safety. Regular inspections help in identifying issues that could endanger flights. An airline might implement a detailed checklist that covers every part of the aircraft, from engines to navigation systems.
In the manufacturing sector, machinery downtime can be costly. Here, preventive maintenance checklists play a critical role. A factory may use a tailored checklist that includes schedules for lubricating machinery, checking for wear and tear, and validating safety features. As a result, these companies can minimize downtime and enhance productivity.
In the IT industry, where software systems are pivotal, effective maintenance checklists help in ensuring system integrity. Such checklists may include routine checks for software updates, security patch deployments, and backup verifications. Organizations find that these practices lead to fewer disruptions and increased user satisfaction.
Success Stories and Lessons Learned
Examining success stories around maintenance checklists reveals numerous benefits. For instance, a well-known automotive manufacturer once faced significant issues with vehicle quality due to inconsistencies in maintenance procedures. After adopting a standardized checklist across its production plants, the inconsistency greatly reduced. The quality control team was able to track defects more effectively, leading to a rise in customer satisfaction ratings.
Another case involved a hospital that struggled with equipment failures. By implementing a thorough maintenance checklist, they could schedule regular inspections on critical medical apparatus. This proactive approach resulted in fewer equipment downtimes, allowing medical staff to provide timely care.
Additionally, organizations must be wary of common pitfalls. Simply adopting a checklist without training staff can lead to ineffective maintenance practices. Lessons from various sectors emphasize the importance of thorough training and regular updates to the checklists. Continuous improvements based on real-life experiences can make the difference between success and failure.
"Real-world applications of maintenance checklists have shown that a structured approach can lead to significant improvements in operations."
Ultimately, the examination of case studies provides invaluable insight into the importance of effective maintenance checklists. Decision-makers can better strategize by understanding both the successes and challenges faced by their peers.
Challenges in Maintaining Checklists
In any organization, preventive maintenance inspection checklists are essential tools that help ensure systems function optimally. However, maintaining these checklists is not without its challenges. Acknowledging these challenges is critical in implementing effective maintenance strategies. This section highlights common issues and suggests ways to overcome them, ultimately enhancing organizational productivity.
Common Pitfalls
Many organizations encounter pitfalls when it comes to their maintenance checklists. Some of the most notable include:
- Lack of Consistency: Teams may follow checklists differently, leading to gaps in maintenance activities. A fragmented approach diminishes the checklist's effectiveness.
- Inadequate Training: Staff may not fully understand the checklist or how to use it properly. This leads to oversights in inspections and maintenance tasks.
- Overwhelming Complexity: Some checklists may become excessively detailed, making them cumbersome for on-site use. Complex checklists can lower compliance rates and reduce the likelihood of thorough inspections.
- Failure to Update: Checklists must evolve with changing technologies and processes. Outdated checklists can miss critical checks or become irrelevant, resulting in compliance failures.
- Neglecting Data Analysis: Organizations may fail to analyze inspection data effectively. Without insights from past inspections, it is challenging to improve or identify recurring issues.
Effective management of maintenance checklists requires understanding these pitfalls and developing strategies to address them.
Overcoming Resistance to Change
Change is often met with resistance in established organizations. When it comes to implementing new or revised preventive maintenance checklists, the challenges compound, requiring tactful strategies to foster acceptance.
- Communicate Benefits: Clearly articulate the advantages of updated checklists to the team. Sharing data on efficiency improvements or reduced failure rates can motivate staff to embrace changes.
- Involve Staff in Development: When staff members contribute to the checklist development process, they are more likely to own the changes. This increases the likelihood they will incorporate the new practices into their routine.
- Provide Ongoing Training: Continuous education on any updates is necessary. Training sessions help reinforce the importance of compliance and ensure all staff feel competent in using the checklist.
- Recognize and Reward Compliance: Incentives can encourage adherence to new processes. Recognizing individuals or teams for diligent use of checklists cultivates a culture of accountability.
- Solicit Feedback Regularly: Establishing a feedback loop allows team members to share their experiences with the checklist. Regular reviews based on real-world use can lead to further refinements, ensuring utility and relevance.
By addressing these challenges head-on, organizations can optimize their preventive maintenance checklists and ensure continuous improvement in operations.
Closure and Future Perspectives
In todayβs fast-paced world, the necessity of a well-structured preventive maintenance inspection checklist cannot be overstated. This article highlights the key components essential for creating such checklists, the strategies for their implementation, and the importance of continuous monitoring. A robust preventive maintenance plan not only enhances the reliability of systems but also significantly contributes to operational safety.
The insights discussed in this guide underscore the crucial benefits organizations can reap from adopting preventive maintenance practices. By minimizing unplanned downtimes and associated costs, businesses can maintain competitive advantage while ensuring their assets are functioning at peak performance. This systematic approach assists in predicting equipment needs, ultimately saving both time and resources.
As technology evolves, the integration of advancements in data analytics, Internet of Things (IoT), and machine learning may further enhance preventive maintenance strategies. Organizations that embrace these innovations will likely find themselves ahead of the curve, equipped to detect issues before they manifest into significant problems. Thus, the future of preventive maintenance looks promising but requires adaptability and vigilance.
"An investment in maintenance is an investment in continuity."
Summary of Key Takeaways
- Preventive Maintenance Defined: Understanding preventive maintenance as a proactive measure is vital for organizations.
- Benefits: Regular maintenance can lead to reduced repair costs, enhanced safety, and improved operational efficiency.
- Checklist Development: Development of a comprehensive checklist is a structured process that involves identifying equipment needs and establishing inspection frequency.
- Training and Technology: Staff training and technology integration are essential for effective checklist implementation.
- Continuous Improvement: Regular updating of checklists promotes their relevance and effectiveness.
Emerging Trends in Preventive Maintenance
The field of preventive maintenance is undergoing significant changes influenced by technological advancements. Some notable trends include:
- Digital Twins: The use of digital twins allows for real-time monitoring and diagnostics, enabling quicker responses to potential issues.
- Predictive Analytics: Analyzing historical data to predict equipment failures before they occur is becoming increasingly common.
- Mobile Inspections: With the availability of mobile devices, inspections can be conducted on-site more efficiently, allowing for immediate data entry and analysis.
- Cloud Computing: Leverage of cloud technologies facilitates better data sharing and collaboration among maintenance teams.
- Sustainability Measures: An increasing focus on sustainability is leading organizations to employ maintenance strategies that reduce energy consumption and waste.