Optimizing Semiconductor Yield Management for Efficiency
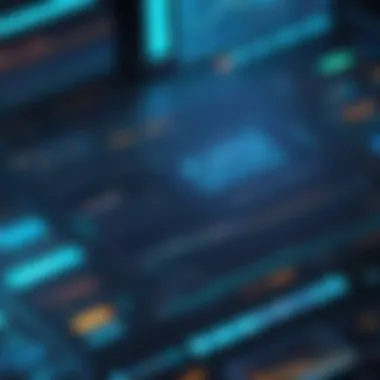
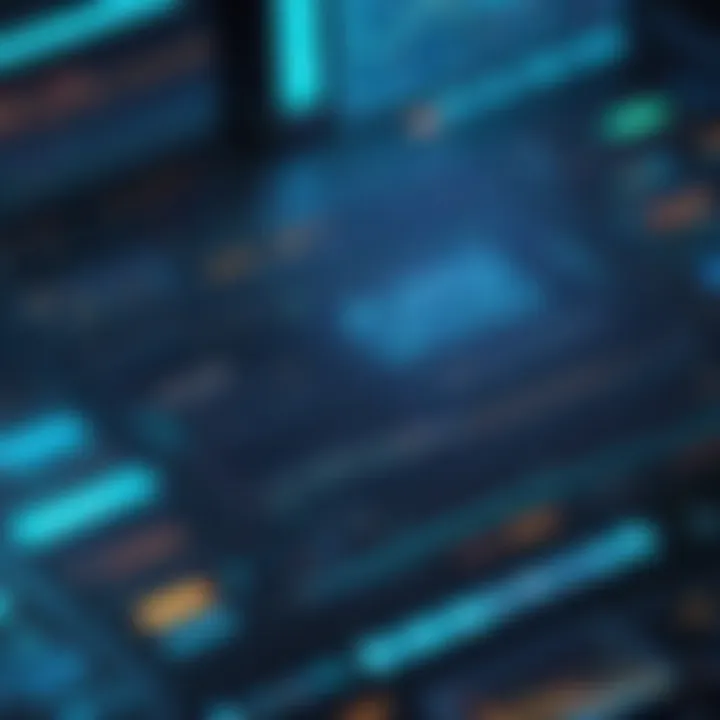
Intro
The semiconductor industry is characterized by rapid advancements and intense competition. In this landscape, yield management software has emerged as a crucial tool for manufacturers aiming to optimize their production processes. This software not only assists in monitoring the yield but also offers insights into improving efficiencies and reducing costs. Understanding its importance is essential for decision-makers. They need a solid grasp of how yield management software can enhance operational processes and the overall performance of semiconductor manufacturing.
The complexities involved in semiconductor production demand robust systems that can handle massive data. The right yield management software seamlessly integrates into existing processes, identifies inefficiencies, and helps in decision-making. It is imperative to explore the features that these systems offer, the target users, and the associated costs. This will provide a comprehensive view of what to expect when considering a yield management solution.
Key Features and Functionalities
Comprehensive Overview
Yield management software must encapsulate several key functionalities to be effective. Essential features include:
- Data Analytics: Provides valuable insights through real-time analysis of production data. This feature is vital for identifying trends and areas for improvement.
- Root Cause Analysis: Helps in pinpointing the reasons behind yield loss. Understanding these causes is crucial for addressing them effectively.
- Reporting Tools: Generate detailed reports that assist stakeholders in making informed decisions based on yield performance.
- Integration Capabilities: The software should integrate with manufacturing execution systems (MES) and equipment automation systems to ensure seamless data flow and operational coherence.
These features contribute to increased data visibility, improved control over processes, and better strategic planning. Ultimately, they enable organizations to respond quickly to any discrepancies in production.
Target Users
The target users of semiconductor yield management software span various roles in the semiconductor industry. These include:
- Production Managers: They utilize the software to oversee manufacturing processes and ensure efficient production runs.
- Quality Assurance Teams: Responsible for maintaining product quality, these teams rely on the software’s analytics to uphold standards.
- IT Professionals: They set up and maintain the software, ensuring that it integrates well with existing systems.
- Executives and Decision-Makers: High-level stakeholders use insights from yield management systems to guide strategic directions and investments.
Understanding who will use the software can greatly enhance its deployment and functionality.
Pricing Models and Cost Analysis
Breakdown of Pricing Tiers
Cost is a significant consideration when selecting yield management software. Generally, pricing models vary:
- License Fees: Many companies charge a one-time license fee for perpetual use of the software.
- Subscription Models: An increasing number of companies offer software-as-a-service (SaaS) based on monthly or annual subscriptions. This model can lower entry costs while providing ongoing updates.
- Customization Costs: Depending on specific needs, additional costs may be incurred for customizing the software to fit unique company processes.
Additional Costs to Consider
When evaluating the total cost of ownership, several factors should be taken into account:
- Maintenance Fees: Ongoing support and upgrades can add to the total costs over time.
- Training Costs: Ensuring staff are adequately trained in using the software is critical and can incur extra expenses.
- Integration Costs: Depending on existing systems, integrating new software can necessitate additional investments.
Prospective buyers should carefully analyze these aspects to ensure prudent financial planning in their investment.
"Choosing the right semiconductor yield management software is not just about functionality, but also about aligning it with existing processes and financial resources."
Thorough evaluation of features, target users, and pricing models elucidates the path towards selecting the most suitable yield management solution for semiconductor manufacturing. With informed decisions, organizations can maximize their yield performance effectively.
Preface to Semiconductor Yield Management Software
In the realm of semiconductor manufacturing, yield management software represents a crucial pillar in maintaining operational excellence. This software addresses the complexities involved in producing semiconductors, ensuring that the highest quality products are achieved while minimizing waste and costs. Yield management involves the systematic approach to maximizing the number of good chips produced per wafer. Understanding this concept is essential for professionals aiming to enhance production efficiency and profitability.
Yield management software empowers organizations by enabling them to track production processes in real-time. It collects and analyzes vast amounts of data, allowing decision-makers to spot trends and address issues promptly. Furthermore, the integration of software tools facilitates seamless communication across different departments, ensuring that all stakeholders work towards a common goal — improving yield and overall performance.
The significance of this software cannot be overstated. According to recent studies, efficient semiconductor yield management can result in efficiency improvements of up to 30%, directly impacting a company's bottom line.
Software solutions vary widely, but most share core functionalities, including data analytics, reporting capabilities, and integration with existing manufacturing systems. Therefore, selecting the right software is instrumental for firms looking to stay competitive in this fast-evolving industry.
Moreover, as the semiconductor landscape continues to change with trends such as miniaturization and increased automation, the role of yield management software will become even more pronounced. Companies must adopt agile strategies that utilize these technologies to remain adept in a challenging market.
The Importance of Yield Management in Semiconductor Manufacturing
Yield management is a crucial aspect of semiconductor manufacturing. It focuses on maximizing the number of functional chips produced from a batch of silicon wafers. In this highly competitive industry, improved yield rates lead directly to cost efficiency and profitability. By understanding and managing yield, companies can enhance their overall operational efficiency.
A few factors highlight why effective yield management holds significant importance:
- Cost Efficiency: The semiconductor manufacturing process is expensive. High yield rates mean more products can be created from fewer resources, resulting in reduced waste and improved profit margins.
- Quality Control: Effective yield management helps in identifying defects early in the production cycle. This means that companies can address problems before they escalate, ensuring higher quality products and satisfying customers.
- Resource Allocation: Understanding yield allows manufacturers to allocate resources more effectively. This includes optimizing workforce management and reducing unnecessary expenditures on raw materials and equipment.
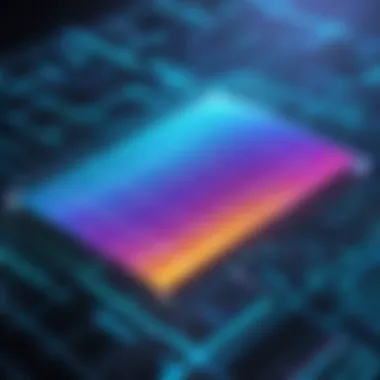
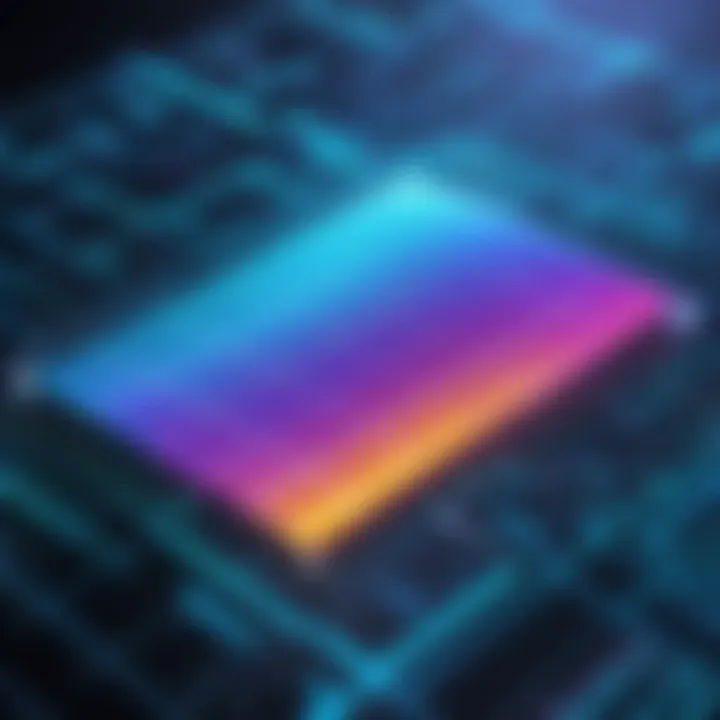
Given the complex nature of semiconductor processes, yield management becomes even more crucial. Small improvements in yield rates can lead to substantial financial benefits. As manufacturers strive for better products, they must prioritize yield management to remain competitive in the market.
Moreover, the integration of advanced technologies in yield management can facilitate better decision-making. Companies can leverage data analytics and automation to refine processes, reduce manual errors, and enhance overall productivity.
"In semiconductor manufacturing, effective yield management is not just an operational necessity; it is a catalyst for innovation and profitability."
Defining Yield in Semiconductor Context
In the semiconductor field, yield refers to the ratio of functional semiconductor devices to the total number produced in a manufacturing process. It is a key performance indicator indicating the effectiveness of production operations. A higher yield signifies that most devices produced meet the quality requirements and function as intended.
Defining yield effectively involves understanding several terms:
- Functional Yield: This includes only the chips that pass all quality tests.
- Parametric Yield: This considers chips that may not be functional but still fulfill specific performance criteria.
Tracking yield requires precise data collection methods and quality assessment protocols. Manufacturers often use various metrics, including defect density and wafer throughput, to gauge yield effectively.
Impact of Yield on Operational Efficiency
Yield has a direct link to operational efficiency. When yield rates increase, operational costs decrease, leading to better overall resource utilization. Companies see diminished waste levels and cost savings across production stages. Increased operational efficiency typically results in:
- Faster Production Cycles: Higher yields mean fewer interruptions in the manufacturing process. This allows faster turnaround and can significantly enhance factory output over time.
- Improved Profit Margins: Improved yields lead to optimized resource consumption, subsequently driving higher profit margins for companies. A few percentage points increase in yield can represent millions of dollars in additional revenue.
- Enhanced Forecasting: Through understanding yield patterns, companies can predict future production needs more effectively. This data-driven approach aids in making informed decisions related to inventory management and supply chain planning.
Core Features of Yield Management Software
The foundation of effective yield management software rests on its core features. These functionalities provide the necessary tools for professionals to monitor, analyze, and enhance yield performance. By focusing on these critical elements, organizations can streamline their manufacturing processes and improve overall operational efficiency. The integration of such features not only facilitates real-time problem-solving but also fosters a proactive approach to decision-making.
Real-time Data Analytics
Real-time data analytics is a vital feature in yield management software. It allows companies to access and assess production data as it happens, rather than waiting for periodic updates. This immediacy enables manufacturers to identify trends and anomalies quickly. For example, if a sudden dip in yield occurs, operators can trace issues back to specific processes or materials, facilitating rapid intervention. The capability to visualize data through dashboards enhances clarity and supports data-driven decisions.
Moreover, the reliance on real-time insights helps create a culture of continuous improvement. Teams can iteratively refine processes based on actual production performance, reducing waste and improving yield rates. With this feature, companies are not only reacting to historical data but are also optimizing production workflows on-the-fly, equipping them to meet market demands swiftly.
Automated Reporting Tools
Automated reporting tools represent another significant advantage of yield management software. These tools enable companies to generate reports encompassing crucial performance indicators without manual data entry. This automation saves time and reduces human error, ensuring accurate reporting.
Benefits of automated reporting include:
- Consistency in Metrics: Automated reports ensure that everyone in the organization refers to the same data point, reducing the chances for miscommunication.
- Time Efficiency: Decision-makers can focus on analysis rather than data gathering, allowing them to prioritize strategic initiatives.
- Customization: Many software solutions offer customizable report templates, providing insights tailored to specific operational needs.
- Enhanced Compliance: For industries regulated by standards, automated reporting helps ensure compliance by maintaining accurate records easily accessible for audits.
Integration with Manufacturing Systems
The integration of yield management software with existing manufacturing systems is essential for achieving unparalleled efficiency. This core feature allows for seamless communication between various applications, such as Enterprise Resource Planning (ERP) and Manufacturing Execution Systems (MES). Synchronizing data from multiple sources not only improves accuracy but also enhances the overall visibility of the production process.
Successful integration leads to:
- Streamlined Workflows: Eliminating data silos means that operators can access comprehensive information, facilitating faster and more informed decisions.
- Enhanced Data Integrity: Integrated systems minimize duplication and errors, ensuring that all departments are working with the same data sets.
- Scalability: As organizations grow, their processes evolve. Software capable of integrating with new tools enables companies to expand their operational scope without significant modifications in their management systems.
In summary, the integration capabilities of yield management software create a comprehensive ecosystem, enhancing operational performance and ensuring that companies can adapt to changing production requirements.
Benefits of Implementing Yield Management Software
In the semiconductor industry, the efficiency of yield management software plays a crucial role in improving production processes. Implementing such software offers significant advantages that can enhance overall manufacturing outcomes. The necessity of integrating yield management software extends beyond basic operations; it becomes part of a broader strategy for continuous improvement. Each benefit provides a distinct contribution to a company's long-term success.
Enhanced Yield Performance
One of the most notable benefits of yield management software is the improvement in yield performance. This software enables manufacturers to track and analyze production data in real time. With accurate insights, companies can identify bottlenecks and areas of inefficiency within the manufacturing process.
- Continuous monitoring of processes helps in detecting variations that may lead to defects.
- The software equips teams to address these variations promptly, subsequently reducing waste and enhancing product quality.
Investing in sophisticated yield management tools allows for proactive strategies. For instance, applying statistical process control (SPC) techniques helps in maintaining desired yield levels. Implementing these methods assures that products align with strict quality benchmarks. As a result, companies experience a marked increase in yield rates, translating directly into higher revenue.
Cost Reduction and Resource Optimization
Cost reduction is a pressing consideration for semiconductor manufacturers. Yield management software aims to optimize resources and minimize unnecessary expenditures. With greater visibility into operational efficiencies, resources can be allocated more judiciously.
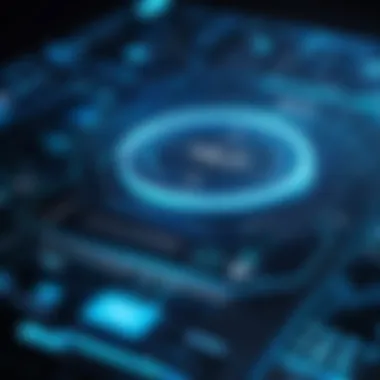
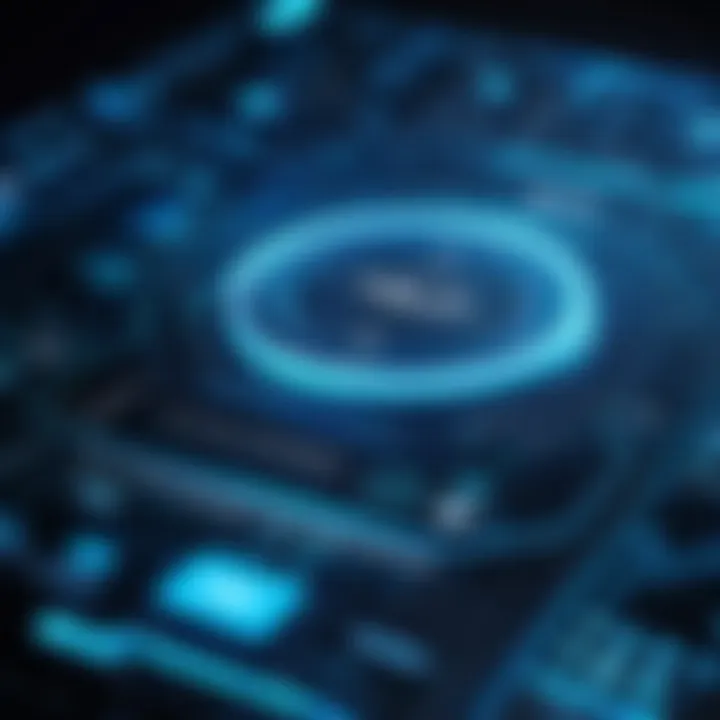
- Automation of routine tasks significantly decreases labor costs.
- By eliminating manual errors, companies not only save on costs but also improve accuracy, leading to less rework.
This software supports advanced analytics to forecast production needs accurately. Consequently, firms can adapt resource usage, thereby minimizing excess inventory or wastage. The overall effect of better resource management is enhanced profitability, allowing organizations to invest more in innovation and development.
Improved Decision-making Processes
Another essential advantage of yield management software is the enhancement of decision-making processes. Access to real-time data fosters informed decisions among leaders and team members alike.
- The integration of data analytics means that patterns and trends become evident, guiding strategic choices.
- When management can easily interpret data, it empowers them to make timely and effective decisions.
Facilitating communication and collaboration across departments is another crucial aspect. Closer alignment between teams allows for quicker responses to challenges or changes in production demands. This collective intelligence leads to an agile organization capable of navigating market dynamics effectively.
"Incorporating yield management software reshapes manufacturing decisions, leading to an agile and responsive environment."
All these benefits wrap together to create a framework where semiconductor companies can operate more efficiently. As the industry faces increasing pressures for innovation and speed, harnessing the capabilities of yield management software will be indispensable for future growth.
Challenges in Yield Management Software Implementation
The implementation of semiconductor yield management software is not without its challenges. Understanding these obstacles is crucial for decision-makers and IT professionals tasked with optimizing processes and enhancing productivity. Effective management of yield is essential in the semiconductor industry, where even minor discrepancies can have significant financial repercussions. This section discusses critical challenges that companies often face during the software implementation and provides insights into how to navigate these hurdles effectively.
Data Quality and Accuracy
One of the foremost challenges in yield management software implementation is ensuring data quality and accuracy. In semiconductor manufacturing, data serves as the backbone of operations. High-quality and accurate data is vital for making informed decisions. Companies need to have strong data collection methods, adequate data governance, and coherent data management practices. If data is of poor quality, the insights derived from the software become questionable. Organizations may face issues such as data duplication, inconsistency, and outdated information. These problems can lead to inaccurate yield analysis, ultimately impacting production efficiency.
To address this challenge, businesses can utilize data cleansing and validation tools. Regular audits of data can help catch errors early. Employing advanced algorithms to monitor data quality continuously allows for timely interventions. By prioritizing data accuracy, companies set a strong foundation for their yield management efforts, amplifying the effectiveness of the software.
Integration Difficulties with Legacy Systems
Integration between new yield management software and existing legacy systems often presents a considerable challenge. Many semiconductor companies have long-standing infrastructure that is deeply embedded in their operational framework. The disconnect between modern software and legacy systems can lead to complications such as system downtime, data silos, and inefficient workflows.
When integrating new software, organizations must assess compatibility with existing systems. Thorough testing during the integration phase helps identify potential risks. The choice of yield management software should involve understanding how well the new system will communicate with legacy platforms. Moreover, a structured integration plan is necessary to minimize disruptions and ensure smooth transitions. Companies should consider investing in middleware solutions that can facilitate data exchange and communication between disparate systems.
Change Management and User Training
Another challenge that arises during the implementation of yield management software relates to change management and user training. Transitioning to a new system can meet resistance from employees who are accustomed to the old ways. Effective change management strategies are vital to ease this transition. Communication is essential. Management should clearly articulate the benefits of the new system. Inviting input and feedback from team members enhances buy-in and reduces resistance.
Additionally, proper training is crucial for maximizing software efficiency. Users must be adequately trained to understand the functionalities of the new yield management system. Organizations can provide a combination of hands-on training, workshops, and access to learning resources. Ongoing support is also essential to address any issues that users may encounter after the initial rollout. Inadequate training can result in diminished software usage, leading to wasted investments and missed opportunities for efficiency gains.
Best Practices for Maximizing Software Efficiency
Optimizing semiconductor yield management software is essential for achieving high operational efficiency in semiconductor manufacturing. Implementing best practices ensures that the software works effectively, meets business needs, and adapts to changes in technology and processes. Establishing these practices can minimize downtime, reduce errors, and lead to better yield outcomes. Understanding and applying specific elements will enable professionals to extract the maximum value from their software investments.
Regular Calibration and Maintenance
Regular calibration and maintenance of yield management software is necessary to keep systems functioning at peak performance. This includes routine checks for software updates, performance assessments, and timely adjustments based on evolving production requirements.
Software that is not routinely calibrated may yield inconsistent results. This can lead to inaccurate data being used for decision-making, affecting overall yield performance. Scheduling periodic reviews helps detect issues before they escalate. These maintenance activities often involve collaboration between IT teams and production staff to ensure that all systems are aligned with the specific needs of manufacturing processes. One key aspect is to establish a standardized maintenance protocol for the software that is easily accessible for all users.
Continuous Training for Users
Continuous training for users is critical for maximizing software efficiency. The semiconductor industry is fast changing, with new technologies and methodologies often introduced. Training ensures that users stay informed about the latest features of the software and understand how to leverage those features for optimally tracing yield losses and improving performance.
Investing in comprehensive training programs, including workshops and online courses, reflects the organization’s commitment to user development. It also reduces the likelihood of user errors, which is vital for maintaining data integrity and achieving production goals. A knowledgeable user base can drive innovation by suggesting improvements based on actual use cases, enhancing productivity.
Feedback Loops for Software Improvement
Establishing feedback loops is an effective strategy for continuous software improvement. These loops enable users to provide insights on software performance, usability, and feature requests. This feedback is invaluable for software developers looking to enhance the system. Collecting user input through surveys, suggestion boxes, or direct discussions makes it possible to prioritize updates and address user concerns.
Organizations should adopt a response mechanism that ensures user suggestions are acknowledged and acted upon. This not only encourages team engagement but also contributes to an iterative process of product enhancement that aligns the software more closely with user needs. By creating an environment where feedback is welcomed and acted on, organizations can elevate their software’s alignment with operational goals.
Regular attention to calibration, ongoing training, and establishing feedback loops are vital for optimizing yield management software. This proactive approach leads to sustained efficiency and enhanced productivity in semiconductor manufacturing.
The Future of Semiconductor Yield Management
The future of semiconductor yield management is poised to integrate sophisticated technologies which can significantly enhance operational efficiency. As the semiconductor landscape grows, manufacturers must adapt to not only stay relevant but also to maximize their yield potential. The push towards modernization calls for a focus on emerging technologies, advanced methodologies, and an ever-increasing need for sustainability practices within this sector. This article will delve into these areas, revealing how they contribute to improved performance.
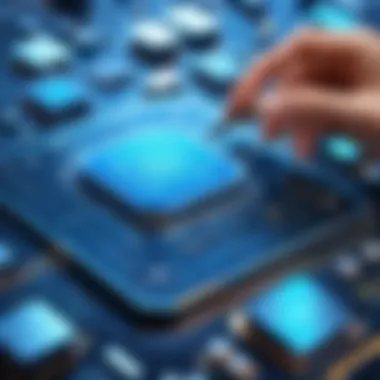
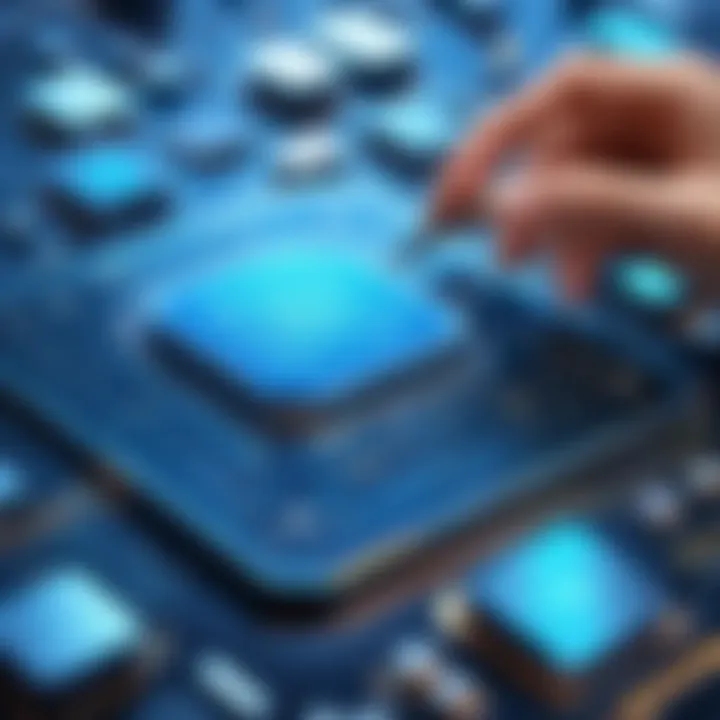
Emerging Technologies in Yield Management
Emerging technologies are reshaping yield management in profound ways. Digital twins, for instance, can simulate physical processes and predict outcomes before implementing them in real settings. This predictive capability allows companies to optimize workflows, leading to better yield performance. Additionally, IoT devices can continuously monitor equipment and environments, providing critical data that informs decision-making. These technologies not only enhance real-time visibility but also foster a culture of data-driven decision-making.
- Digital Twins: Create a virtual model of processes.
- IoT Integration: Enable real-time monitoring for better insights.
- Cloud Computing: Offers scalable storage and processing power for big data analytics.
Through these developments, businesses can expect not just performance gains but also increased agility in responding to market fluctuations and demands.
Artificial Intelligence and Machine Learning Applications
Artificial intelligence and machine learning are pivotal in advancing semiconductor yield management. These technologies analyze vast amounts of data to identify patterns and anomalies that humans might overlook. AI algorithms can streamline processes by predicting equipment failures, optimizing resource allocation, and improving production schedules. This constant learning ability enhances the system over time, leading to smarter manufacturing operations.
"Integrating AI into yield management transforms traditional processes, making them more efficient and less prone to human error."
Implementing AI can lead to the following benefits:
- Predictive Maintenance: Anticipates equipment breakdowns.
- Yield Prediction: Provides forecasts based on historical data.
- Anomaly Detection: Identifies defects early in the production cycle.
Harnessing AI and machine learning facilitates lightning-fast decision-making, translating to cost savings and improved product quality.
Sustainability and Environmental Considerations
As the global emphasis on sustainability grows, semiconductor manufacturers must consider environmental impacts in their yield management practices. Sustainable practices can reduce waste and energy consumption during production processes. Companies can implement methodologies that focus on minimizing their carbon footprint while maximally utilizing resources.
Some considerations include:
- Reducing Energy Usage: Implementing energy-efficient machinery.
- Waste Management: Enhancing recycling processes and reducing hazardous materials.
- Renewable Energy Sources: Using solar or wind energy to power manufacturing facilities.
By prioritizing sustainability, businesses not only align with global standards but also appeal to a more environmentally conscious consumer base.
Case Studies: Successful Implementation Examples
Evaluating successful implementations of semiconductor yield management software exposes nuances that underline its importance. Case studies provide a narrative enriched with real-world applications and outcomes. They illustrate specific elements such as tailored solutions, measurable benefits, and learned lessons in the adoption process. This section will uncover why these examples matter in reinforcing strategies for yield optimization.
Company A: Achieving Higher Yields
Company A, a prominent player in the semiconductor industry, faced challenges with yield rates that significantly affected profitability. The firm decided to implement a new yield management software solution. They focused on real-time data analytics as a core feature. By utilizing this software, they accessed immediate insights on production quality. This was crucial in identifying defects and their root causes promptly.
Over a six-month period, Company A reported a yield improvement of approximately 15%. Management credits this success to continuous monitoring and iterative adjustments guided by data. They capitalized on the software's automated reporting tools which streamlined decision-making processes. The capability to visualize performance trends in real-time led the company to proactively address quality issues, significantly reducing waste.
Company B: Overcoming Integration Challenges
Company B encountered hurdles when integrating yield management software into its pre-existing systems. The legacy software posed compatibility issues, which delayed deployment. Instead of viewing this as a setback, they adopted a phased implementation approach. This included involving key stakeholders in the planning stages for better alignment.
Through meticulous testing and adjustments, the new yield management software became compatible with legacy systems. Team training sessions were essential to ensure all users understood the new functionalities. After overcoming these integration challenges, Company B experienced a notable enhancement in operational efficiency. They managed to reduce cycle times by 10%, demonstrating how strategic planning and execution can turn initial difficulties into successful outcomes.
"The best way to predict the future is to create it." – Peter Drucker
In summary, these case studies showcase how distinctly different companies approached the implementation of yield management software. Company A’s focus on analytics and continuous monitoring contrasts with Company B’s emphasis on strategic integration. Both companies witnessed significant benefits, illustrating that tailored solutions to specific problems can lead to enhanced yield performance.
Epilogue
The conclusion of this article serves as a pivotal reflection on the importance of optimizing semiconductor yield management software. Throughout the discussion, we have highlighted how effective yield management can significantly influence the operational efficiency of semiconductor manufacturing. Enhancements in yield management lead to better resource allocation, reduced waste, and ultimately, improved profitability.
Key elements of yield management software, such as real-time data analytics and automated reporting tools, are critical for decision-makers. These features not only streamline operations but also provide actionable insights. A focus on integrating these tools into existing workflows can result in marked improvements in production yield.
Furthermore, recognizing the challenges in implementing such software cannot be understated. Issues surrounding data quality, system integration, and user training must be addressed proactively. Companies that invest time and resources in these areas are more likely to see beneficial outcomes.
"Effective yield management is not just a tool; it is a strategy that pertains to the entire operational framework."
Finally, this article encourages IT professionals and decision-makers to view yield management as a long-term investment. A commitment to ongoing training, calibration, and user feedback loops ensures software effectiveness. As technologies evolve, adapting to new advancements will be essential for maintaining a competitive edge in the semiconductor industry.
Importance of Reliable Sources
- Aligning with Industry Standards
Reliable references ensure that the software aligns with current industry standards and practices. This is crucial for maintaining competitiveness in the rapidly evolving semiconductor market. - Evidence-Based Decision Making
Citing trusted references contributes to evidence-based decision-making. If a software option is backed by peer-reviewed studies or case studies, it instills confidence in its effectiveness and ability to deliver enhanced yields. - Identifying Proven Strategies
Reference materials often highlight successful case studies. Learning from the experiences of other companies can offer valuable insights into best practices, common challenges, and viable solutions to complex issues.
Key Considerations for References
- Credibility: Always evaluate the credibility of the sources. Consider the author’s qualifications, the publication’s reputation, and the recency of the information.
- Relevance: Ensure that the references are pertinent to your specific needs and the challenges faced in yield management.
- Diversity: Use a diverse range of sources, including academic publications, industry reports, and peer-reviewed articles, to build a comprehensive understanding.
"Quality references should not only inform but also inspire innovation and improvement in yield management practices."