Maximizing Efficiency with Inventory Management Software
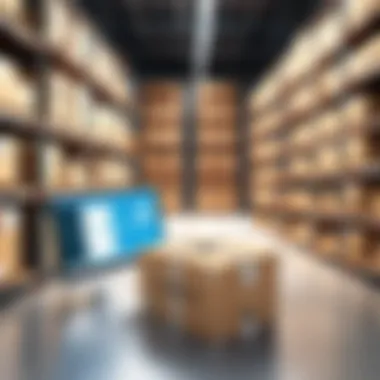
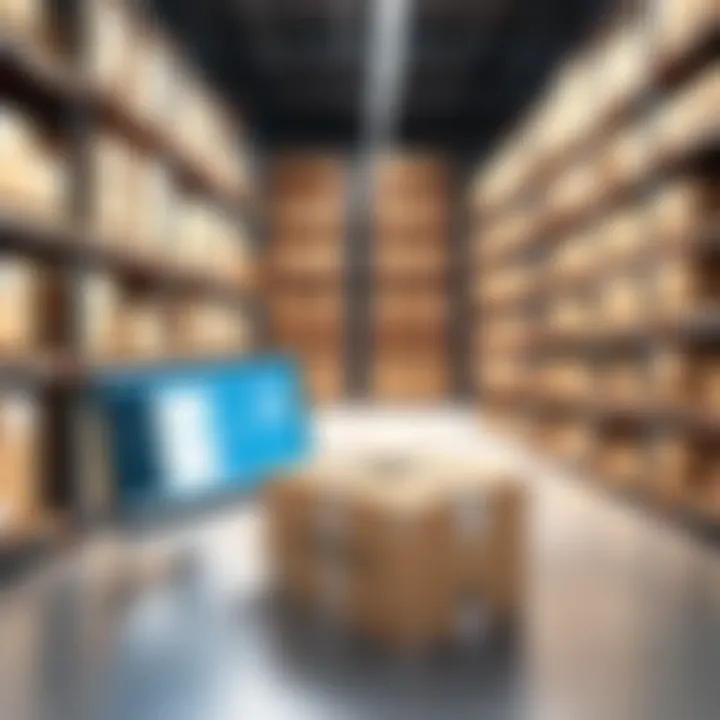
Intro
Efficient inventory management is a cornerstone of successful manufacturing. In todayโs rapidly evolving landscape, businesses must adapt to new technologies that streamline operations. Inventory management software plays a vital role in this adaptation. It provides real-time data, enhances decision-making, and helps to control costs. This article delves into key features of such software, its market relevance, and pricing strategies that can influence a company's bottom line.
Key Features and Functionalities
Comprehensive Overview
Inventory management software is designed to optimize the handling of stock levels, orders, and deliveries. This software supports several functionalities that are crucial for manufacturing processes:
- Real-time tracking: Monitoring inventory levels in real-time can prevent stockouts or excess inventory, allowing for better production planning.
- Forecasting tools: These tools help predict demand based on historical data, ensuring that manufacturers can plan accordingly.
- Integration capabilities: The ability to integrate with other software systems, such as Enterprise Resource Planning (ERP) or Customer Relationship Management (CRM), enhances operational efficiencies.
- Reporting and analytics: Powerful reporting tools provide insights into stock performance, helping to identify trends and areas for improvement.
Target Users
The primary users of inventory management software encompass various roles in the manufacturing sector:
- Manufacturing Managers: Focus on optimizing production schedules and resource allocation.
- Supply Chain Analysts: Analyze data for strategic planning and logistics management.
- IT Professionals: Ensure the seamless implementation and integration of software solutions.
- Finance Managers: Oversee costs associated with inventory holding, contributing to better financial health.
Pricing Models and Cost Analysis
Understanding pricing models is essential for informed decision-making regarding software investment.
Breakdown of Pricing Tiers
Common pricing structures for inventory management software include:
- Subscription-based: Monthly or annual fees that provide access to the software with updates.
- One-time purchase: A single payment for perpetual access, typically coupled with annual maintenance fees.
- Freemium models: Basic features provided at no cost, with premium features available for an additional charge.
Additional Costs to Consider
Beyond the initial pricing, other potential costs may include:
- Implementation fees: Costs associated with installing and configuring the software.
- Training expenses: The need for training staff to use the new system effectively.
- Maintenance and support: Ongoing costs for tech support and software updates.
"Investing in the right inventory management software can lead to significant operational efficiencies and cost savings."
Understanding Inventory Management Software
Inventory management software plays an essential role in the efficiency of manufacturing processes. It allows businesses to keep track of their materials, products, and supplies. Understanding this software is crucial for optimizing operations, reducing errors, and ensuring timely delivery of goods. As the manufacturing industry evolves, so does the need for sophisticated solutions that aid in decision-making and strategy development.
Definition and Importance
Inventory management software is defined as a system used to oversee the ordering, storage, and use of materials and products. This software is crucial for manufacturers because it enhances operational control. Proper inventory management ensures that materials are available when needed, helping to prevent production delays and stockouts. Without this software, businesses may struggle with inefficiencies that lead to increased costs and decreased customer satisfaction.
Key Components of Inventory Management Software
Understanding the key components of inventory management software enables manufacturers to harness its full potential. Each component provides specific functionalities that contribute to streamlined operations.
Inventory Tracking
Inventory tracking is a critical function of inventory management software. It involves monitoring stock levels in real-time. This capability allows manufacturers to maintain optimal stock levels and avoid excess inventory. The key characteristic of inventory tracking is its ability to provide accurate data regarding stock on hand. A unique feature of this tracking is the use of barcode or RFID scanning technology. This technology helps reduce human errors during stocktakes. However, the integration of such technologies requires initial investment, which some smaller manufacturers may find challenging.
Forecasting
Forecasting predicts future inventory needs based on historical data and trends. This function aids in planning and avoids issues like stockouts and overstock situations. The key characteristic of forecasting is its reliance on advanced algorithms that analyze patterns in inventory usage. A notable feature is its ability to adjust predictions based on external factors such as seasonality or market changes. While beneficial, inaccurate forecasts can lead to the production of surplus goods, adding to holding costs.
Reporting
Reporting is vital for insightful decision-making. Inventory management software generates detailed reports on stock levels, turnover rates, and trends over time. This key characteristic allows manufacturers to identify inefficiencies. The unique feature of reporting includes customizable dashboards, which enable users to focus on metrics that matter most to their operations. However, generating reports can sometimes require specialized knowledge, making it a potential barrier for some users.
Integration with Other Systems
Integration with other systems is another important aspect of inventory management software. It allows seamless communication with finance, sales, and supply chain management tools. The key characteristic here is the ability to automate data transfer between systems. This feature enhances overall operational efficiency and ensures that all departments work with the same accurate information. However, compatibility issues can arise if systems are not designed to work together, leading to potential operational disruptions.
Benefits of Inventory Management Software in Manufacturing
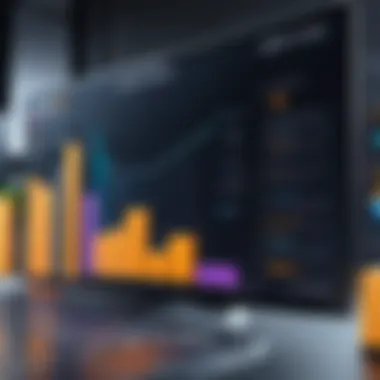
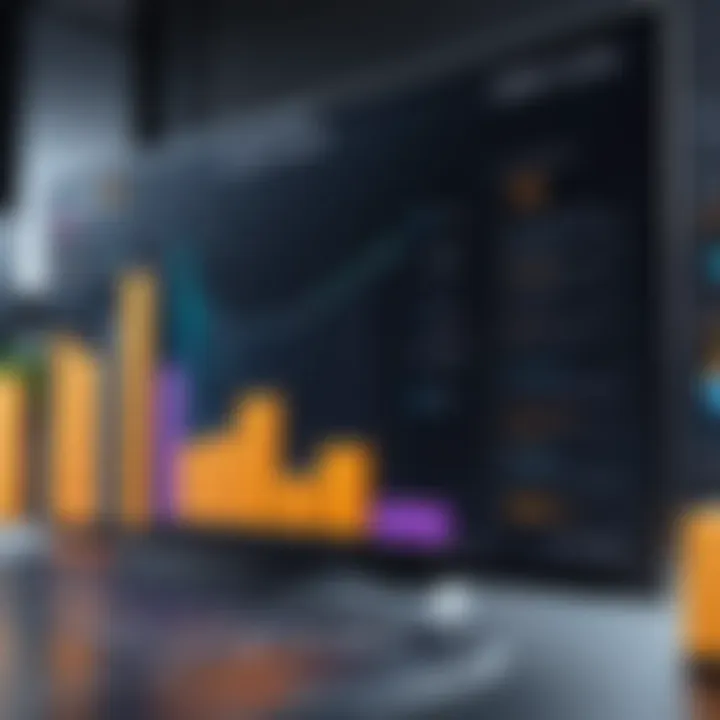
The advantages of utilizing inventory management software in the manufacturing sector are substantial. Given the rapidly changing market conditions, manufacturers must adopt strategies that promote efficiency and reduce costs. This software provides myriad benefits that enhance operational performance, minimizes waste, and facilitates better decision-making.
Enhanced Visibility and Control
With advanced inventory management software, businesses gain improved visibility of their inventory levels, production processes, and supply chains. This enhanced visibility allows decision-makers to monitor inventory in real time, helping identify potential shortages or surpluses before they become problematic. Improved control over inventory data ensures decisions are based on up-to-date and accurate information. For instance, using software like Fishbowl or NetSuite, organizations can track stock movements and monitor key performance indicators related to inventory.
Furthermore, real-time visibility aids in better supplier relationship management. Companies can assess supplier performance, negotiate contracts more effectively, and plan procurement strategies based on actual demand trends. With enhanced control over inventory processes, organizations can improve their responsiveness to market needs.
Reduction of Waste and Overstocks
Manufacturers constantly face the challenge of excess inventory or scarcity of materials. Inventory management software can significantly reduce waste and overstock issues. By leveraging advanced analytics and reporting features, businesses can make data-driven decisions that align with production capacities and sales forecasts.
For example, software such as SAP Business One and QuickBooks Inventory can automatically update inventory counts, reorder levels, and provide alerts for low stock situations. This minimizes the risk of overproduction and excess stock, which can lead to increased holding costs. Moreover, it allows for adopting a Just-In-Time inventory system, ensuring that materials arrive as they are needed, rather than accumulating unnecessary surplus.
Improved Forecasting and Planning
Effective inventory management hinges on accurate forecasting and planning. The right software can analyze historical data and determine future inventory needs based on sales trends and seasonality. This capability not only enhances resource allocation but also strengthens production planning.
Solutions like Oracle NetSuite and DEAR Inventory offer predictive analytics features that allow businesses to anticipate market demands. This helps in making informed decisions about what to stock and when to replenish items. Improved planning leads to optimized production schedules and reduces downtime, ultimately enhancing overall efficiency and productivity.
"Investment in robust inventory management solutions can yield significant returns in terms of efficiency and cost reduction. Manufacturers must choose wisely to enhance their operations."
Selecting the Right Inventory Management Software
Selecting the right inventory management software is a critical step in enhancing efficiency and streamlining processes. In the manufacturing landscape, the appropriate software ensures that resources are allocated effectively and that production flows smoothly. Proper selection can greatly impact your operational success, influencing not just inventory control but also overall business performance.
One must consider several elements when choosing this software. First, understanding specific business needs is essential. Each manufacturing setup is unique, with its own set of requirements dictated by product lines, volume, and industry regulations. Thus, conducting a thorough analysis of these needs will lay the groundwork for making an informed decision.
Another vital aspect is evaluating software features. A well-rounded software should provide robust tools that address tracking, forecasting, and reporting, among other capabilities. These features ensure that users can manage inventory with precision, which directly affects productivity and profitability. Moreover, considerations around budget play a crucial role in this process. Companies often work within financial constraints, making it essential to balance features with affordability.
Overall, selecting the right inventory management software involves careful reflection on your operations and mindful assessment of available options. The proper choice can lead to improved efficiency, cost savings, and a stronger competitive position in the market.
Identifying Business Needs
Before delving into software options, it is paramount to pinpoint the specific needs of your business. This can be achieved by evaluating existing processes, understanding the gaps, and recognizing areas for improvement. Conducting stakeholder interviews and gathering feedback from team members can provide valuable insights into what is required from an inventory management system.
Common business needs may include:
- Real-time inventory tracking
- Demand forecasting capabilities
- Integration with current systems
- User-friendly interfaces
Engaging these various perspectives will help frame your requirements more clearly and guide your selection process.
Evaluating Software Features
In evaluating software features, you should consider different aspects that can enhance your inventory management processes.
User Interface Considerations
User interface considerations are pivotal for user adoption and overall satisfaction with the software. A clean and intuitive design allows users to navigate the system efficiently. The key characteristic here is usabilityโif employees find the interface cumbersome, it could lead to resistance or errors in operation.
A notable feature in user interface design is the dashboard functionality. This allows users to see critical inventory data at a glance, promoting quick decision-making. The benefits of a well-designed interface extend to reduced training times and increased productivity.
Customization Options
Customization options can significantly enhance the relevance of the software to your specific operations. This aspect allows users to tailor features according to their workflows, enhancing efficiency. The primary characteristic of customizable systems is adaptabilityโthey can evolve as your business grows or changes.
One unique feature is modular functionality, which lets businesses add or remove features as needed. This flexibility can be advantageous in ensuring that the system meets changing business requirements without incurring unnecessary costs. However, over-customization can complicate upgrades and support, making caution necessary in this area.
Scalability
Scalability refers to the software's ability to grow with your business. As manufacturing needs change, the system must accommodate larger inventories or more complex operations. The key characteristic of a scalable solution is its capacity to handle increased loads without significant performance loss.
A unique feature often found in scalable software is cloud-based infrastructure, which enables easy adjustments in storage and processing power. This can provide businesses with a cost-effective way to manage growth, but it may require careful consideration of data security and system reliability.
Considering Budgetary Constraints
When selecting inventory management software, you cannot ignore budgetary constraints. Each organization operates with a budget that dictates its possible investments. Hence, balancing cost-effective solutions while meeting functionality needs is crucial.
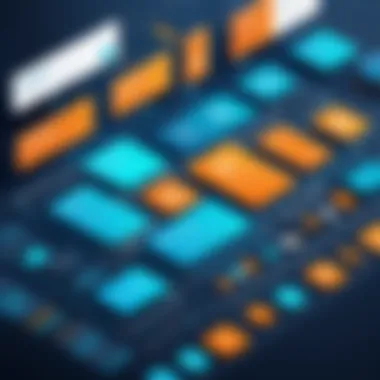
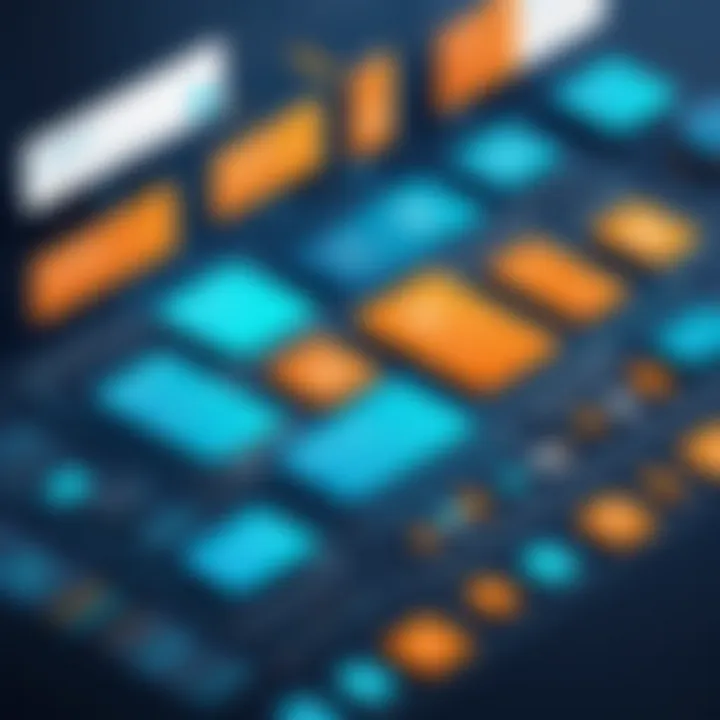
It is important to evaluate not only the initial acquisition cost but also the total cost of ownership. This can include:
- Maintenance and support costs
- Training expenses
- Additional modules or features in the future
Considering these elements will assist in making a prudent decision regarding which software to purchase, minimizing possible financial strain while ensuring operational effectiveness.
Implementation Strategies for Manufacturing Software
The successful deployment of inventory management software within manufacturing processes is not merely a technical operation; it demands careful strategizing. Implementation strategies are necessary to ensure that the investment in software translates into tangible benefits such as improved efficiency, cost savings, and better inventory accuracy. Addressing the nuances of these strategies can significantly affect how well the software performs in real-world settings.
Planning the Implementation Process
Good planning forms the bedrock of any successful software implementation. First, stakeholders need to clearly define objectives. This includes understanding what they want the software to achieve, whether it is lowering inventory costs, enhancing stock accuracy, or streamlining order fulfillment. By establishing clear goals, it allows for focused decision-making.
Second, timelines should be developed. Complex implementations can consume a lot of time, so having a realistic timeline helps manage expectations and track progress. Additionally, identifying the right personnel for the implementation team is vital. This team should comprise individuals from various departments including IT, operations, and human resources to ensure diverse perspectives.
Training Employees on New Systems
Any new system is only as effective as the people using it. Training employees is a crucial step in the implementation process. This training should go beyond basic operation; it should delve into why the new system replaces the old one and how it fits into the overall business strategy. Effective training programs utilize varied methods, incorporating hands-on sessions and detailed documentation.
Employees often resist new technologies, so addressing the reasons for this resistance is essential. Engagement and involvement during the training process can enhance acceptance. Real-world scenarios and practical examples help bridge the gap between theory and practice, making it easier for employees to adapt.
Conducting Post-Implementation Reviews
Post-implementation reviews are vital to assess the effectiveness of the inventory management software. These reviews allow organizations to evaluate if they met their initial objectives, enabling them to identify areas requiring further improvement. It is essential to gather feedback from users as their experience provides valuable insights into the softwareโs performance.
Organizations should employ key performance indicators (KPIs) to measure success. Metrics such as inventory turnover rates, order accuracy, and user satisfaction scores are useful for this purpose. This evaluation can also highlight any training gaps that may need addressing and can inform strategies for continuous improvement in the system.
"Regular assessments post-implementation are key to ensuring that software continues to meet evolving business needs."
Future Trends in Inventory Management for Manufacturing
Understanding future trends in inventory management for manufacturing is crucial for businesses aiming to stay competitive. This field is rapidly evolving, influenced by advancements in technology and shifting market dynamics. By embracing these trends, companies can optimize processes, enhance efficiency, and reduce costs. The key topics within this section will include the integration of artificial intelligence, the shift towards cloud-based solutions, and the rise of automation. Each of these elements holds significant potential for manufacturers seeking improved inventory management strategies.
Integration of Artificial Intelligence
Artificial intelligence (AI) is reshaping inventory management by enabling faster and more accurate decision-making. AI algorithms analyze large datasets to predict trends and optimize stock levels. Companies leveraging AI can benefit from better demand forecasting, reducing the risk of overstocking or stockouts.
The application of machine learning allows systems to learn from historical data and adapt to changing consumption patterns. For example, when a manufacturing firm integrates AI, it can automate reorder processes based on anticipated demand rather than relying solely on historical averages. This leads to both cost savings and improved customer satisfaction through timely delivery.
Potential challenges include the initial setup and need for quality data. However, the long-term benefits of reduced waste and enhanced operational visibility outweigh these concerns.
Cloud-Based Solutions
Cloud-based inventory management software offers manufacturers scalability and flexibility. Unlike traditional on-premises solutions, cloud systems allow for remote access and collaboration across various departments or locations. This accessibility is vital in today's global market, where teams need to operate seamlessly.
Moreover, updating software and accessing support becomes significantly easier with cloud deployments. For manufacturers, this means less downtime and reduced IT costs associated with maintenance. Analytics capabilities in cloud solutions also provide real-time insights, which are necessary for informed decision-making.
However, adopting cloud-based solutions requires a solid strategy to ensure data security and integration with existing systems. Manufacturers must evaluate vendors carefully to mitigate risks related to data breaches and system outages.
The Rise of Automation
The rise of automation in inventory management streamlines processes and reduces the likelihood of human errors. Automated systems handle tasks such as inventory counts and order processing, freeing up staff for higher-level responsibilities. For instance, robotic process automation can manage routine data entry tasks, allowing employees to focus on analysis and strategy.
Automation not only enhances operational efficiency but also leads to cost benefits over time. By integrating automated inventory systems, manufacturers can improve their response times to market changes and customer demands. Furthermore, automated systems provide better accuracy in inventory tracking, eliminating discrepancies that arise from manual input.
However, implementing automation introduces challenges, including the need for employee training and potential resistance to change. To address these issues, manufacturers should invest in change management practices and ensure clear communication throughout the transition process.
"Embracing future trends in inventory management is not an option, but a necessity for manufacturers seeking long-term success."
In summary, the future of inventory management in manufacturing is promising and filled with opportunities driven by technology. Integration of AI, cloud-based solutions, and automation are pivotal trends that traditional practices must embrace. By staying informed and adaptable, manufacturers can ensure they meet evolving customer expectations and operational demands.
Challenges in Implementing Inventory Management Software
Implementing inventory management software in manufacturing is often a complex task. Companies face numerous obstacles. Recognizing these challenges is vital. Understanding what can go wrong helps in devising strategies to mitigate risks. This section discusses two significant hurdles: resistance to change among staff and data integration issues. Each of these challenges can inhibit system adoption, affecting the overall efficiency and benefits expected from the software.
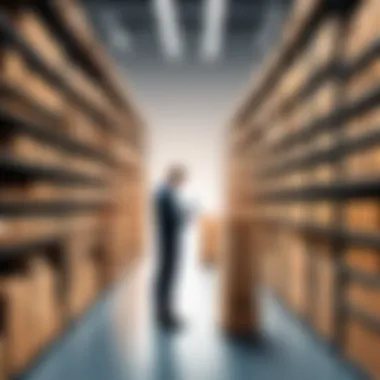
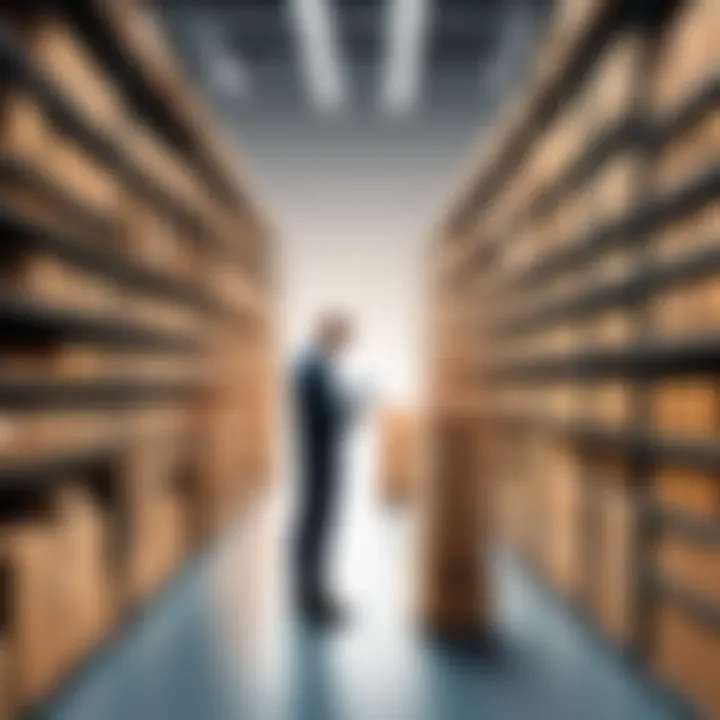
Resistance to Change Among Staff
Resistance to change is a common issue during the introduction of new technologies. Employees may feel threatened by new systems or doubt their effectiveness. This can lead to reluctance in using the software, hindering the implementation process. For many, the comfort of familiar processes outweighs the apparent benefits of a new system.
To address this, it is crucial to involve staff early in the process. Explain the reasons for the switch and how it helps them. Training sessions can ease fears and improve understanding of the softwareโs capabilities. In addition to technical training, focus on the potential for enhanced job satisfaction as processes become more streamlined.
Some effective methods to reduce resistance include:
- Providing Comprehensive Training: Equip staff with the knowledge to confidently use the new system.
- Encouraging Open Communication: Create a platform for staff to express concerns and provide feedback.
- Incentivizing Usage: Consider reward systems for those who engage with the software effectively.
Acknowledging these points can significantly ease the transition and foster a constructive environment.
Data Integration Issues
Data integration is another critical challenge when implementing inventory management software. Existing systems may not communicate well with new solutions. This can lead to data silos, in which vital information is trapped in different platforms. As a result, this affects the real-time visibility and accurate reporting expected from optimized inventory management.
To ensure smooth integration, it is important to analyze the current data systems before selecting new software. Metrics, like data formats and the compatibility of different platforms, should be considered. Additionally, assess whether the new software supports APIs that can facilitate data exchange.
Key strategies to overcome data integration issues include:
- Conducting a Thorough Data Audit: Understand existing data structures and identify potential obstacles pre-implementation.
- Choosing Compatible Software: Select inventory management software that integrates well with your existing systems.
- Utilizing a Dedicated IT Team: Have a team on standby to address any integration hurdles swiftly.
"A successful integration process can result in a more seamless workflow and better decision-making across the board."
By addressing resistance and data integration issues effectively, manufacturers can lay the groundwork for successful inventory management software implementation. This approach not only fosters an efficient transition but also enhances the overall performance of the manufacturing processes.
Case Studies of Successful Implementation
Understanding how inventory management software can lead to enhanced efficiency in manufacturing is best realized through real-world examples. Case studies illuminate the journey of various organizations, showcasing the distinct approaches they took to implement these systems. By examining these scenarios, decision-makers can identify best practices, potential pitfalls, and innovative solutions. Successful implementations offer a practical framework to evaluate the return on investment and the transformative potential of these software solutions.
Assessing the specific results and practical applications from case studies reveals actionable insights. They serve not only to validate the effectiveness of inventory management software but also to provide a narrative that resonates with businesses facing similar challenges. These accounts highlight key elements such as improved inventory control, decreased operational costs, and enhanced customer satisfaction. These metrics are significant for decision-makers in choosing software solutions tailored to their needs.
Additionally, the importance of contextual understanding is considerable. Different industries, production scales, and operational models influence how inventory management software is implemented and the resulting success. This section will explore two distinct contexts: small business success stories and enterprise-level solutions, both of which illustrate adaptability and strategic foresight in inventory management.
Small Business Success
In the realm of small businesses, limited resources often necessitate more deliberate planning. Companies such as Green Leaf Packaging faced challenges with inventory tracking and order fulfillment before implementing inventory management software. With solutions like Fishbowl Inventory, they streamlined their operations, significantly reducing manual errors and operational delays.
The switch allowed Green Leaf Packaging to improve inventory accuracy by over fifty percent and reduce order fulfillment time by an impressive thirty percent. Such advancements illustrate how even modest investments in technology can yield significant operational improvements. The real-time visibility into stock levels helped them optimize purchases, ensuring they maintained the right amount of inventory to meet customer demands without overstocking.
Key takeaways from this case include:
- Improved Accuracy: Significant reduction in stock-taking errors.
- Speedy Order Fulfillment: Faster delivery times to customers.
- Cost-Efficiency: Lowered storage costs through better inventory control.
These elements paint a clear picture of how small businesses can thrive by leveraging tailored inventory management solutions, manifesting their effectiveness as a stepping stone in their growth journey.
Enterprise-Level Solutions
On the other end, larger organizations face complexities that often require scalable and robust inventory management systems. For instance, Ford Motor Company implemented a customized solution to manage their vast supply chain and inventory across several production facilities. By utilizing SAP Integrated Business Planning, they created a more cohesive inventory management strategy that aligned with their global operations.
The results were striking. The company reported a thirty-five percent improvement in inventory turnover rates and a considerable reduction in carrying costs. Furthermore, the integration of real-time data analytics allowed Ford to anticipate production needs more accurately, subsequently decreasing lead times and boosting productivity across the board.
Pivotal insights from Ford's case demonstrate:
- Scalability: Ability to adapt the software to meet growing demands.
- Real-Time Analytics: Enhanced decision-making capabilities based on real-time data.
- Cost Saving: Decreased excess inventory and optimized storage use.
Both case studies serve as compelling examples within the discourse on inventory management software. Whether a small business or a large enterprise, the impact of these tools can be profound when properly managed and optimally utilized. Their stories not only inspire but also provide a blueprint for firms aiming to enhance their inventory management practices.
The End
Summarizing Key Insights
Key insights from the article emphasize that inventory management software is not merely a tool for tracking stock. It serves as the backbone for strategic planning in manufacturing.
- Visibility and Control: Improved visibility into inventory levels helps firms manage stock more effectively. Users can quickly assess supply levels and reduce costs associated with overstock.
- Customization: Tailoring software options to meet specific business needs is critical. Each manufacturer has unique requirements, making customization a priority for successful implementation.
- Future Trends: Staying updated with trends like artificial intelligence and cloud-based solutions helps manufacturers remain competitive. The rise of automation will further streamline processes and improve operational efficiencies.
"Optimizing inventory management software is not just about having the right technology; it's about integrating it seamlessly into manufacturing processes to drive real change."
Future Directions in Inventory Management
Looking ahead, several pivotal directions shape the future of inventory management in manufacturing:
- Integration of Advanced Technologies: Incorporating AI can enhance forecasting and reporting. This leads to more accurate inventory levels and effective decision-making.
- Cloud Solutions: Embracing cloud-based systems offers accessibility and scalability. Manufacturers can adapt to changing needs and access real-time data from anywhere.
- Rise of Automation: As industries evolve, automation will play an increasing role. Automated systems improve precision and reduce human error in inventory management processes.