Essential Insights into Product Inventory Management
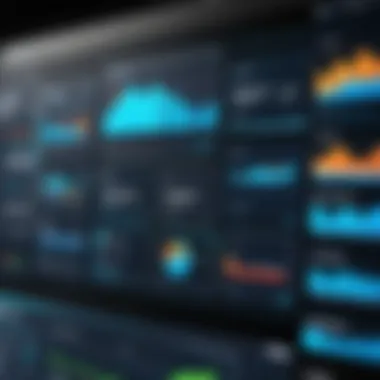
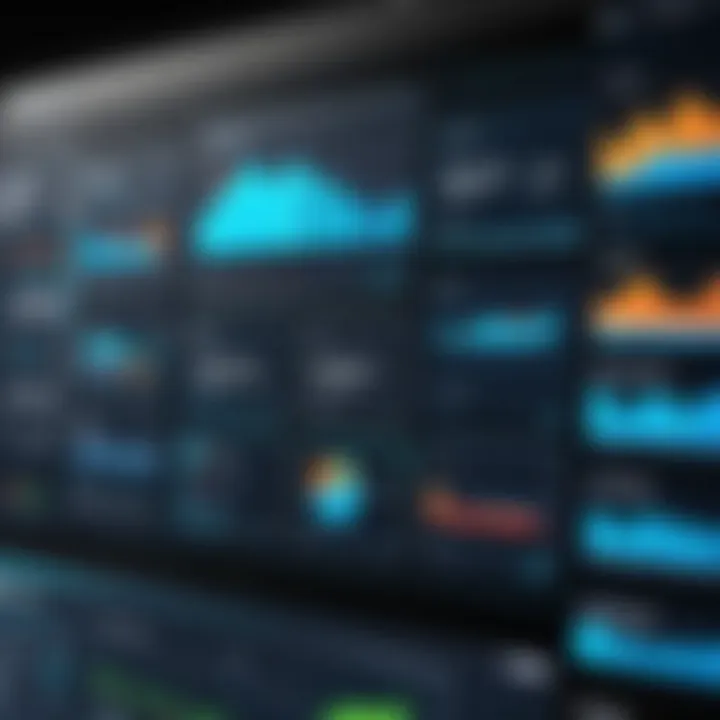
Intro
When you strip away the layers of commerce, at the heart of every thriving business lies an effective product inventory management system. In an era where data reigns supreme, understanding the intricacies of controlling stock levels, forecasting demand, and optimizing supply chains can make or break a business. As organizations expand or pivot, the need for sophisticated inventory oversight becomes increasingly clear. This piece aims to provide an in-depth overview of not just the basic principles of product inventory management, but also its nuanced methodologies and advanced tools designed to meet the dynamic demands of various industries.
In this guide, you will find insights tailored specifically for decision-makers, IT professionals, and entrepreneurs. Whether you're evaluating software solutions or streamlining current practices, the content will equip you with the necessary knowledge to make informed choices in the vast realm of inventory management.
Key Features and Functionalities
Comprehensive Overview
Product inventory management is not merely about counting items on a shelf. It encompasses a range of features including tracking stock levels in real time, integrating with sales systems, and automating reorders. Consider these critical functionalities:
- Real-Time Tracking: Modern systems provide immediate visibility into stock levels, reducing the chances of stockouts or overstocking.
- Reporting and Analytics: These tools generate reports that help in forecasting and understanding purchasing trends, allowing businesses to make data-driven decisions.
- Multi-Channel Management: The ability to handle inventory across various platforms—be it in-store or online—ensures consistency and accuracy.
- Integration Capabilities: Effective inventory management software typically integrates seamlessly with other business systems like accounting, sales, and CRM.
The efficiency gained through these features propels businesses forward and reduces costly errors, ultimately allowing them to focus on their core operations.
Target Users
The landscape of inventory management software caters to a diverse audience. Each user group has unique needs, which must be addressed by suitable tools. Here’s a look at the main players:
- Retailers: From brick-and-mortar stores to e-commerce giants, retailers utilize inventory management software to track sales, manage stock levels, and analyze customer buying behaviors.
- Manufacturers: These users depend on precise inventory tracking to streamline production processes and manage raw materials against finished goods.
- Wholesale Distributors: For wholesalers, managing vast amounts of diverse inventory requires robust systems that can handle bulk orders and complex logistics.
- Food and Beverage Industry: With perishable goods, this sector needs tools that can monitor expiration dates and ensure freshness.
In essence, understanding the distinct requirements of these groups can help businesses select the proper toolsets that enhance their operational workflow.
Pricing Models and Cost Analysis
Breakdown of Pricing Tiers
When assessing inventory management software, it's vital to examine various pricing models. Here’s what to consider:
- Subscription-Based Pricing: This model typically charges a monthly fee, providing continued support and updates. This is common among cloud-based solutions.
- One-Time Fee: This pricing requires a single upfront payment, often for on-premise systems. Maintenance and updates may incur additional costs later.
- Basic Tier: Often includes minimal features, suitable for startups or small retailers.
- Professional Tier: Offers enhanced functionalities, ideal for medium-sized businesses.
- Enterprise Tier: Includes all features and custom solutions for large corporations.
This allows businesses to tailor their budget according to their growth trajectory and immediate needs.
Additional Costs to Consider
It’s easy to get caught up in the sticker price, but there are hidden costs that may arise. Here are some factors to keep in mind:
- Training Expenses: Implementing new software often requires training staff, which can add to the overall cost.
- Customization Fees: If your business has specialized requirements, expect to pay for customization of the software.
- Integration Costs: Integrating inventory management systems with existing platforms can incur additional expenses.
Taking all these elements into account ensures a comprehensive understanding of overall investment.
"An effective product inventory management system is not just a tool, but a strategic advantage that can steer a business toward success."
In summary, mastering the art of product inventory management is like conducting a symphony; each piece must work in harmony to produce a successful outcome. From understanding features to price evaluations, this guide endeavors to illuminate the complex landscape of inventory management, assisting decision-makers in navigating their choices wisely.
Understanding Product Inventory
Product inventory management is not merely a behind-the-scenes operation; it’s an integral foundation for any business that deals with physical goods. Nutritional supplements, electronics, clothes – you name it, if a company handles it, having their inventory organized and well-managed is crucial. Without a solid grip on product inventory, a business can experience serious issues ranging from cash flow problems to missed sales opportunities. In this article, we will navigate through the essential aspects of understanding product inventory, emphasizing its significance across various business operations.
Definition and Scope
At its core, product inventory refers to the total quantity of goods that a business holds at any given time, whether they are raw materials, work-in-progress items, or finished goods ready for sale. This scope extends beyond mere numbers; it encompasses the systems and processes employed to manage these goods effectively.
Inventory can be considered an asset, but it is often termed a double-edged sword. On one hand, it’s important for fulfilling customer orders, while on the other, it ties up capital and may incur storage costs. The goal of product inventory management is to strike a balance between having enough stock to meet demand while minimizing excess stock that could lead to waste or obsolescence.
Moreover, the definition of inventory doesn't reside in a void. It varies across industries, and each sector introduces unique challenges and considerations. Take retail for instance; here, the focus rests heavily on sales turnover, while in manufacturing, the emphasis might shift towards managing raw materials and intermediate products. Understanding these nuances enables businesses to customize their inventory systems tailored to their specific needs, ultimately improving efficiency and profitability.
Importance in Business Operations
The significance of understanding product inventory extends far beyond the rudiments of counting items on a shelf. It ties directly into the overall health of a business. Here are some key points to consider:
- Cash Flow Management: Effective inventory control helps in avoiding over-purchasing, ensuring that the cash flow remains stable. After all, money tied up in excess inventory is money that could be working for a business in different ways.
- Customer Satisfaction: Efficient inventory management prevents stockouts, which can frustrate customers and drive them to competitors. Ensuring that products are readily available fosters customer loyalty.
- Operational Efficiency: It streamlines processing orders and shipping products, thus enhancing the speed and agility of a company in responding to market demands.
- Informed Decision-Making: Having accurate inventory data enables businesses to make better purchasing decisions, optimize sales forecasts, and adjust marketing strategies based on actual demand.
Effective inventory management isn’t just about having what you need when you need it; it’s about knowing every single detail about what you have.
Types of Inventory
Understanding the different types of inventory is pivotal to managing a company’s resources efficiently. Each type serves a distinct purpose and impacts the overall inventory management strategy. Recognizing these categories allows businesses to make informed decisions that can significantly enhance profitability and operational effectiveness. By navigating through the types of inventory, organizations can better predict inventory needs and respond swiftly to market demands, ultimately leading to improved customer satisfaction and reduced costs.
Raw Materials
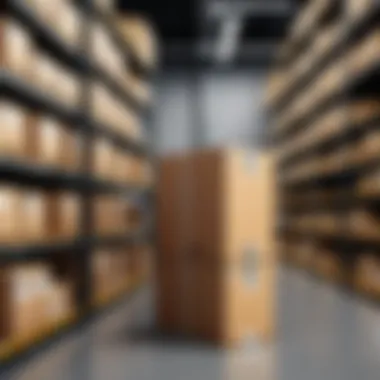
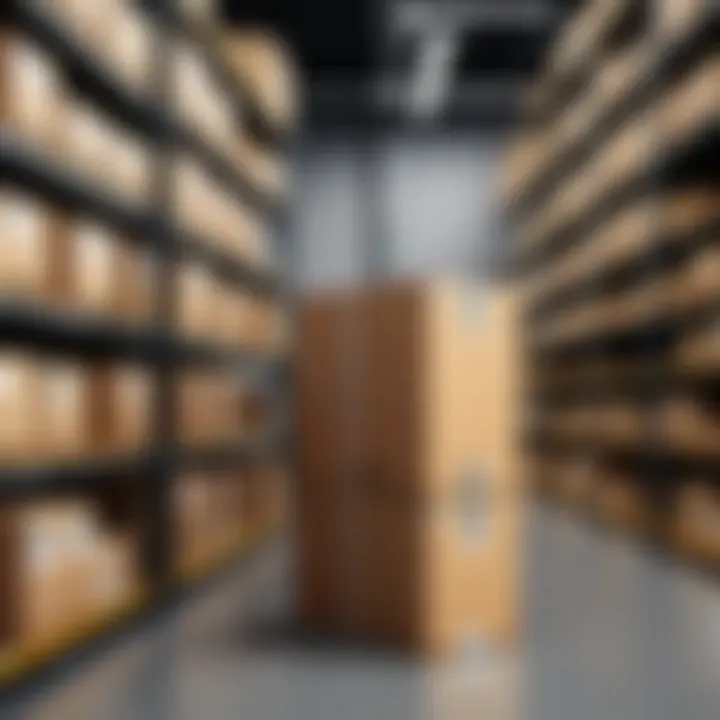
Raw materials are the foundational elements for production. These are basic components used in the manufacture of products. They can be anything from metal for an automobile to flour for a bakery. Managing raw materials effectively is crucial as it directly influences production capabilities. If there's a shortage, operations can grind to a halt. On the other hand, having too much can tie up capital unnecessarily.
Benefits of raw materials management include:
- Cost Efficiency: Proper tracking ensures you buy only what you need, minimizing excess.
- Production Continuity: Maintaining optimal levels prevents delays.
- Quality Control: Regular monitoring helps in ensuring raw materials meet necessary standards.
Work in Progress
Work in Progress (WIP) refers to items that are in the production process but not yet completed. This inventory type includes partially finished goods that are at various stages of manufacture. The management of WIP is essential because it reflects the efficiency of production processes.
Key considerations include:
- Workflow Efficiency: Monitoring measures the time taken at each stage, pinpointing bottlenecks.
- Resource Allocation: Helps in adjusting labor and materials based on production flow.
- Cost Tracking: Knowing the WIP can provide insight into production costs and potential overruns.
Finished Goods
Finished goods are products that have been completed and are ready for sale. This inventory type needs careful management because it represents the final stage of the production cycle and includes everything from high-end electronics to simple household items. Balancing finished goods is crucial to avoid stockouts, which could lead to lost sales, or overstocks, which can lead to markdowns.
Benefits of effectively managing finished goods include:
- Increased Sales Opportunities: Having the right products available when customers want them leads to more sales.
- Optimal Shelf Life: Regular inventory checks help in managing perishables or seasonal products, preventing waste.
- Market Responsiveness: Quick adjustments can be made based on sales trends or consumer demand.
Maintenance, Repair, and Operations (MRO) Items
MRO items are necessary for running a business but are not directly tied to the production of goods. Think cleaning supplies, tools for repairs, or office supplies. While they may seem like minor components, managing MRO effectively is vital to maintaining the productivity of every aspect of an organization.
Considerations regarding MRO inventory include:
- Cost Control: Over-ordering these items can lead to unnecessary expenditures.
- Operational Efficiency: A lack of MRO supplies can disrupt operations, causing delays in production or service.
- Inventory Visibility: Easy tracking can help identify when to reorder, ensuring seamless operations without hitches.
"In the world of inventory, it's not just about having more; it's about having what you need when you need it."
Inventory Management Techniques
Various techniques in inventory management stand at the core of effective product oversight. These methodologies not only streamline operations but also enhance decision-making processes crucial for sustaining profitability in competitive markets. Each technique carries its own unique advantages, and understanding them allows business leaders to tailor their inventory strategies to fit specific needs.
Just-In-Time (JIT)
Just-In-Time (JIT) inventory management is a strategy that aligns production schedules with demand. The primary objective of JIT is reducing waste—most notably, unnecessary inventory costs. Instead of stockpiling goods, businesses using JIT receive products only as they are required for production or sales.
A significant advantage of JIT is the minimization of holding costs. By reducing the average inventory level, a company enhances cash flow and enables capital to be used more efficiently. However, it requires precise coordination with suppliers and a robust understanding of demand forecasting.
Implementation of JIT often involves technology integration. Many businesses adopt software solutions that track sales patterns in real-time, ensuring that new stock arrives just before it’s needed. This way, businesses avoid excess and out-of-date inventories, leading to a more streamlined operation.
"In JIT, timing is everything, and getting products to the right place at the right time can lead to significant savings and efficiencies."
Economic Order Quantity (EOQ)
Economic Order Quantity (EOQ) is a formula used by businesses to determine the optimal order quantity that minimizes total inventory costs. The costs included in the EOQ calculation encompass ordering costs and holding costs, thus providing a comprehensive view of the inventory management structure.
By applying EOQ, businesses can calculate how much inventory to order each time, preventing stockouts and over-ordering. In industries characterized by fluctuating demand, this technique becomes paramount for maintaining financial health without sacrificing customer service levels.
This method is particularly useful for organizations with stable demand patterns. For those experiencing seasonality or high variability in sales, it may require adjustments based on market conditions.
ABC Analysis
ABC Analysis is a technique that categorizes inventory into three classes based on their importance and value to the business. The idea is simple:
- A-items are the most valuable to the organization, making up a small percentage of total items.
- B-items are moderate, representing a larger portion of the inventory but with less total value.
- C-items are the least valuable, covering a large volume but contributing little to overall value.
This analysis helps companies prioritize their management efforts. For instance, A-items should be monitored closely and reordered timely, while C-items need not receive the same level of scrutiny. Introducing this method can lead to focused resource allocation, resulting in improved efficiency.
Dropshipping
Dropshipping is a unique inventory management model where the retailer does not hold products in stock. Instead, when a retailer sells a product, they purchase the item from a third-party supplier who then ships it directly to the customer. This approach can be appealing to new businesses or those looking to minimize inventory risks.
In dropshipping, the retailer saves on storage costs and can offer a broader range of products without significant investments in inventory upfront. However, it is essential to maintain strong relationships with suppliers to ensure timely fulfillment and quality control, as the retailer’s reputation hinges on the supplier's reliability.
In sum, understanding and employing specific inventory management techniques like JIT, EOQ, ABC Analysis, and dropshipping can lead to improved efficiency, optimized costs, and ultimately a more successful business model.
Inventory Software Solutions
Efficient inventory management is the backbone of successful businesses, and this is where inventory software solutions come into play. These tools are designed to streamline the tracking and management of stock, enhancing both productivity and profitability. As businesses grapple with increasingly complex supply chains and customer demands, having robust software becomes indispensable. By automating tasks and providing real-time data, these solutions allow decision-makers to focus on strategic growth instead of getting bogged down in manual processes.
Features to Consider
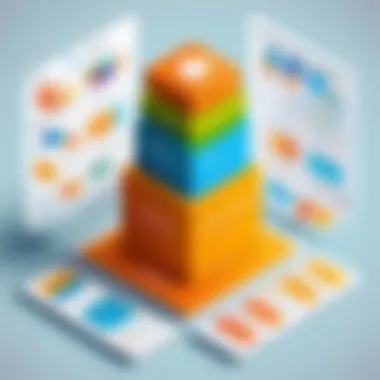
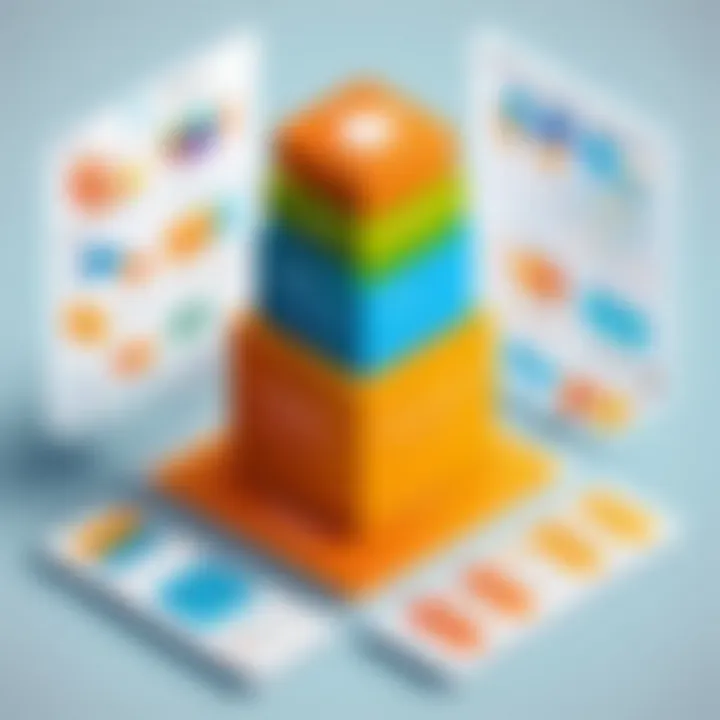
When it comes to selecting the right inventory management software, there are several critical features to consider:
- User-Friendly Interface: A simple, intuitive design enables employees to adapt quickly without extensive training. The last thing you want is a complicated system that leaves your team scratching their heads.
- Real-Time Tracking: Implement software that gives you live updates on stock levels, locations, and order statuses. This prevents annoying stockouts and overstocks, saving you both time and money.
- Reporting and Analytics: Detailed insights can help identify slow-moving items or high-demand products. Having data-driven decisions leads to smarter inventory practices.
- Scalability: As your business grows, your software should grow with you. Check if the platform can easily handle an expanding inventory list without a hitch.
An emphasis on these features can guide you toward making a well-informed decision, ensuring the software meets your business’s unique needs.
Popular Inventory Management Software
A variety of inventory management software options are available today, each offering distinctive capabilities. Some leading choices include:
- TradeGecko: A favorite among small to medium-sized enterprises, TradeGecko combines inventory and order management with an easy-to-navigate interface.
- NetSuite ERP: Known for its comprehensive approach, NetSuite offers powerful inventory management features and integrates well with other business functions.
- Fishbowl: This software is especially advantageous for manufacturers and wholesalers aiming for greater control over their inventory.
- Cin7: A cloud-based solution that connects inventory management with point-of-sale, eCommerce, and third-party logistics, making it ideal for businesses with multiple sales channels.
Choosing the right software often means analyzing what specific features align with your operational challenges.
Integration with Other Systems
Integration plays a vital role in maximizing the effectiveness of inventory software. Inventory management does not exist in a vacuum; it needs to communicate seamlessly with other systems such as:
- Accounting Software: Syncing with tools like QuickBooks or Xero ensures that inventory costs are accurately reflected in your financials.
- Customer Relationship Management (CRM): By linking with CRM systems, businesses can track sales trends and improve customer interactions based on inventory availability.
- eCommerce Platforms: Systems like Shopify or WooCommerce should interface with inventory software to maintain accurate stock levels. This helps prevent overselling, which can damage customer trust.
Integrating these systems facilitates a smoother workflow and provides a holistic view of operations, enabling better decision-making.
"Investing in the right inventory software is not just about managing stock; it’s about empowering your business to adapt, scale, and thrive in a fast-paced market."
Challenges in Inventory Management
Effective inventory management stands as a pillar for any business that deals with physical products. It isn’t just about keeping tabs on what’s on hand; it’s a balancin act that impacts every corner of operations. Various challenges can emerge, presenting significant hurdles to seamless inventory management. These challenges can lead to lost sales, increased costs, and ultimately, a hit to your bottom line. Therefore, identifying and understanding these challenges is paramount for any decision-maker engaged in this space.
Stockouts and Overstocks
Managing stock levels is a delicate dance. On one side, you have stockouts—when products run out before replenishment—and that’s a real headache. Imagine a customer searching high and low for a specific gadget, only to find that it’s out of stock. Such scenarios not only drive customers away but can also harm a brand’s reputation.
On the flip side, there’s the issue of overstocks. This occurs when businesses have excess inventory, often due to poor forecasting or a failure to adjust to changing demand. Overstocks tie up capital and can lead to markdowns, spoiling any anticipated profit. The relation between stockouts and overstocks is crucial; balancing the two is necessary to maintain customer satisfaction while also safeguarding resources.
Inaccurate Data
In the digital age, data reigns supreme. However, inaccuracies can plague inventory management, creating chaos rather than clarity. Relying on outdated systems or manual entries can result in discrepancies between what’s recorded and what’s physically present. For example, if a business believes it has 100 units of a product, but actual counts reveal only 80, it can derail planning and customer expectations.
Accurate data is the foundation upon which effective inventory strategies are built. When analysis and reporting are flawed, businesses may miss opportunities or even continue costly business practices that no longer serve their goals. Investing in tools that ensure data integrity is not just a good practice; it's a necessity in the intricate world of inventory management.
Supplier Reliability
The relationship with suppliers can greatly influence inventory management. If suppliers are unreliable—whether due to delays, inconsistent quality, or abrupt price changes—it creates a ripple effect. A company relying on a shaky supplier could find itself in a jam, dealing with stockouts that leave customers frustrated.
Choosing suppliers isn’t merely about pricing; it’s about ensuring alignment with your business needs. Conducting due diligence and regularly assessing supplier performance can help mitigate risks. Moreover, fostering solid relationships with trustworthy suppliers can add a layer of stability, ensuring a smoother supply chain and enhancing overall inventory effectiveness.
"A stable supply chain is like a well-oiled machine; even the smallest glitch can throw off the entire operation."
Automation in Inventory Management
Automation in inventory management is becoming increasingly vital in the fast-paced world of business. Automating processes allows companies to streamline operations, reduce the chances of human error, and improve overall efficiency. As companies look for ways to enhance productivity, automation stands out as a key strategy in achieving these goals. The role of automation transcends mere speed; it contributes significantly to accuracy, thereby ensuring that all inventory-related activities align with business objectives.
Benefits of Automation
When discussing the benefits of automation in inventory management, several aspects come to the forefront:
- Accuracy: Manual inventory tracking often leads to discrepancies. Automation significantly reduces these errors, leading to precise stock counts.
- Time-Saving: Automation handles repetitive tasks like order processing and stock updates. This saves valuable time for employees, allowing them to focus on more strategic tasks.
- Real-Time Reporting: The ability to access up-to-date information is critical. Automation provides instant visibility into inventory levels, enabling better decision-making.
- Cost Efficiency: While initial investments in automation tools might seem steep, the long-term savings associated with reduced labor costs and minimized stock losses often outweigh these concerns.
- Scalability: As businesses grow, their inventory management needs evolve. Automated systems can easily scale to accommodate increasing demands without requiring a complete overhaul of existing processes.
"Adopting automation in inventory management transforms chaos into clarity, ensuring smooth sailing through turbulent market waters."
Choosing the Right Tools
Choosing the right automation tools is crucial for achieving the desired outcomes in inventory management. Some considerations to keep in mind include:
- Compatibility: Ensure that the chosen software integrates seamlessly with existing systems. Whether it's your accounting software or e-commerce platform, integration is key to avoiding disruptions.
- User-Friendliness: A steep learning curve can lead to frustration and inefficiencies. Opt for tools that offer intuitive interfaces to facilitate easier onboarding for staff.
- Customization Options: Every business has unique inventory challenges. The ability to customize tools to fit specific needs is essential for maximizing their effectiveness.
- Support and Training: Look for vendors that provide ongoing support and training resources. This ensures that your team can leverage the tool’s full potential, minimizing downtime.
- Cost vs. Value: Analyze not just the upfront costs but the value provided by the tools in relation to your business goals. Basic tools may save money initially but might lack the necessary features for growth.
Data Analysis in Inventory Management
In the modern landscape of business, the role of data analysis in inventory management cannot be overstated. It acts as the backbone that supports decision-making, ensuring that businesses not only keep their stock levels optimal but also respond to market dynamics effectively. Understanding data allows businesses to track sales patterns, spot trends, and handle fluctuations in demand more gracefully. Through data analytics, one can detect problems before they snowball into grave issues, thereby saving valuable time and resources.
Key Performance Indicators (KPIs)
Key Performance Indicators are essential metrics that offer insights into the efficiency and effectiveness of inventory management strategies. Selecting the right KPIs can aid in making informed decisions and refining operational processes. Here are some crucial KPIs that every manager should consider:
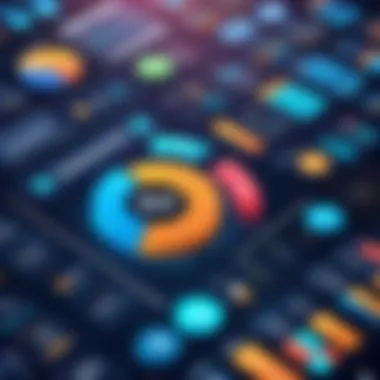
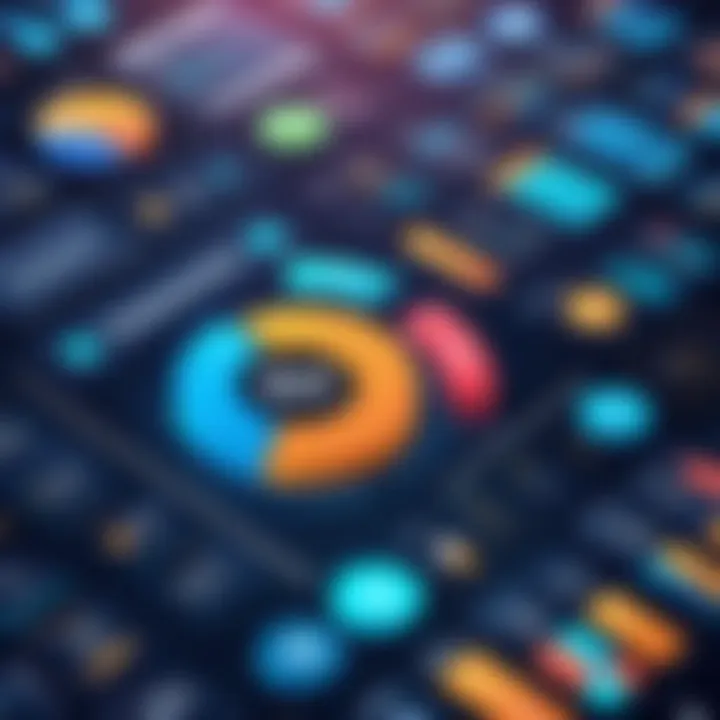
- Inventory Turnover Rate: This measures how often inventory is sold and replaced over a given period. A higher turnover rate often indicates effective inventory management, whereas a low rate could signify overstocking or a decline in sales.
- Days Sales of Inventory (DSI): This KPI quantifies how long an item typically stays in inventory before being sold. It can spotlight slow-moving products that might need a marketing boost or a reevaluation of purchasing decisions.
- Order Accuracy Rate: This metric tracks the precision of order processing. A high order accuracy rate is indicative of a well-functioning inventory management system, while lower rates highlight potential issues needing attention.
- Stockout Rate: Frequent stockouts can lead to lost sales and frustrated customers. Monitoring this can help assess whether stock levels adequately meet demand.
Utilizing KPIs helps businesses stay on their toes, enabling them to adjust their strategies as needed in reaction to the data being churned.
Forecasting Methods
Forecasting methods are critical in predicting future inventory needs based on historical data and market analysis. When businesses leverage proper forecasting techniques, they can minimize excess stock, ultimately driving down holding costs. Several methods stand out:
- Time Series Analysis: This technique examines past demand data to predict future trends. By understanding seasonal variations, businesses can plan inventory levels more accurately.
- Qualitative Forecasting: Often used when historical data is scarce, this method relies on expert opinions, market analysis, and intuition. It can be especially valuable in new product launches or emerging markets.
- Causal Forecasting: This method identifies relationships between variables, using them to predict future behavior. For example, if an increase in advertising corresponds with higher sales, businesses can adjust their stock accordingly.
- Collaborative Forecasting: Here, supply chain partners share information to generate a more comprehensive forecast. It fosters transparency and enhances collective efficiency, leading to balanced inventory levels.
By integrating these forecasting methods into their inventory management practices, businesses can enhance their agility in responding to market needs. The use of data-derived strategies nurtures a proactive approach instead of a reactive one, curbing issues like overstocking and stockouts before they arise.
"Forecasting methods are not just an option anymore; they are a necessity for companies wanting to thrive in a dynamic market environment and stay ahead of their competitors."
In closing, data analysis is not devoid of challenges. However, when approached strategically, it can significantly streamline inventory management processes, offering a competitive edge in today's fast-paced business world.
Sustainability and Inventory Practices
Sustainability in inventory management has gradually shifted from a mere buzzword to a core principle influencing how businesses operate. In an age where environmental concerns are making headlines, integrating sustainable practices within inventory management isn't simply beneficial; it’s becoming crucial for long-term viability. An organization’s commitment to sustainability can resonate throughout its inventory processes, affecting everything from the materials sourced to how products are delivered to end users. This section will explore eco-friendly inventory strategies and the role of the circular economy.
Eco-Friendly Inventory Strategies
Implementing eco-friendly inventory strategies does more than just appeal to ethically minded consumers. It can significantly reduce costs while simultaneously improving operational efficiency. One effective approach involves optimizing stock levels to minimize waste. Excess stock can lead to spoilage, particularly in perishable goods, or it might require additional storage space, incurring higher costs.
Here are several eco-friendly strategies to consider:
- Sourcing Sustainable Materials: Prioritizing vendors who practice sustainable sourcing can reduce a company’s overall carbon footprint. Materials that come from renewable resources tend to be more sustainable.
- Implementing Energy-Efficient Warehousing: Use energy-efficient lighting and climate controls in warehouses. This not only minimizes the energy consumed but also extends the lifespan of both equipment and product stock.
- Adopting Inventory Audits: Regular inventory audits can help identify excess stock and slow-moving items, enabling timely decisions that reduce waste.
- Utilizing Technology: Software solutions like RFID tracking and inventory management systems allow real-time data analysis, making it easier to maintain optimal inventory levels and reduce unnecessary stock.
- Packaging Innovations: Switching to biodegradable or recyclable packaging can help minimize waste and enhance the brand’s image in sustainability.
"A commitment to sustainable inventory management not only safeguards the environment but also enhances a brand's reputation among consumers who prioritize ethical practices."
Circular Economy in Inventory Management
The concept of a circular economy emphasizes reducing waste and promoting the continual use of resources. This stands in stark contrast to the traditional linear economy, where products are typically made, used, and then discarded. By adopting the principles of circular economy in inventory management, companies can significantly enhance their sustainability efforts.
Some key aspects to consider include:
- Product Life Cycle Assessment: Regularly evaluating the entirety of a product’s life—from raw material extraction through production, use, and disposal—can guide companies on how to make their processes more sustainable.
- Remanufacturing: This involves refurbishing or upgrading old products instead of discarding them. For example, companies can take back used products, repair them, and resell them at a lower cost. This encourages a cycle where materials are continually reused, reducing the demand for new resources.
- Resource Recovery: Establishing strategies for collecting and recycling end-of-life products fosters a culture of sustainability. Programs that emphasize returning products to the supply chain can close the loop in the inventory process.
- Collaboration and Partnerships: Collaborating with suppliers and stakeholders in sustainability initiatives can amplify impact. By working together, businesses can share resources and insights to create a more sustainable inventory practice.
Case Studies in Effective Inventory Management
Understanding how companies successfully manage their inventory can provide invaluable lessons for others. Case studies serve as practical illustrations of how theory translates into practice. They reveal not just successes but also the pitfalls companies encounter and the strategies they employ to overcome these challenges.
Engaging with these case studies allows decision-makers and IT professionals to examine real-world applications of inventory management principles. Such analyses can shed light on the specific elements that make certain strategies more effective than others. One of the key benefits is that they provide tangible proof of how proper inventory management can lead to increased efficiency and reduced costs.
Successful Implementation Examples
Looking at successful case studies can be a great way to learn and adopt best practices. For instance, the famous toy company LEGO streamlined their inventory management by implementing a revised logistics strategy. They employed data analytics and forecasting models to predict seasonal demands better. By leveraging a tailored software solution, they managed to dramatically decrease excess stock levels while ensuring that customer demand was met during peak seasons. As a result, LEGO not only foresaw a marked decline in inventory costs but also enhanced overall sales performance.
Another example is the multinational retail corporation, Walmart. They are renowned for their sophisticated supply chain management techniques, which enable them to restock their stores with timely precision. By adopting a centralized inventory system linked directly to their suppliers, they have minimized stockouts and overstock situations. This not only improves customer satisfaction but also reduces storage costs, which is a vital consideration in retail operations.
Lessons Learned from Failures
Not every attempt at effective inventory management leads to success, and failures offer lessons just as valuable as victories. Take, for example, the case of a major electronics company that once faced massive stockpile issues. Despite investing heavily in advanced software to monitor stock levels, their lack of integration between sales and inventory data led to over-purchasing and significant losses.
This situation highlighted the importance of cohesive systems that communicate effectively with one another. One lesson learned was the need for regular audits and reviews of inventory practices. Without ongoing evaluations, even the best systems can become ineffective over time, leading to misalignment between inventory and actual market demands.
Moreover, another cautionary tale comes from a clothing retailer that failed to adapt to changes in consumer preferences. Their rigid inventory guidelines caused them to miss emerging trends, which resulted in a surplus of unsold seasonal items. Adapting inventory strategies to be agile and responsive is crucial—not just selecting the right tools.
Future Trends in Inventory Management
In today’s rapidly evolving marketplace, staying ahead of the curve in inventory management is not merely beneficial; it's essential. The trends emerging in this domain are shaping the future of how businesses operate, ensuring that inventory practices can keep pace with customer demands and technological advancements. Embracing these trends will enable businesses to optimize operations, reduce costs, and improve customer satisfaction.
Impact of Artificial Intelligence
Artificial Intelligence, or AI for short, is making big waves in various business sectors, and inventory management is no exception. The potential benefits of AI are extensive. Companies can leverage machine learning algorithms to forecast demand more accurately, ensuring that stock levels align closely with actual consumer behavior. This not only reduces the chances of stockouts but also minimizes the risk of overstock situations, which can tie up valuable resources.
AI can also automate routine tasks, like reordering and tracking inventory levels. This is especially useful in larger operations where keeping tabs on multiple stock-keeping units (SKUs) can feel like chasing a wild goose. With automation, employees can focus more on strategic decision-making rather than getting bogged down in mundane tasks. Moreover, AI-driven insights can reveal patterns and trends that human eyes might miss, giving businesses an edge in their competitive landscape.
Consider the example of a retail company that uses AI to analyze sales data. By identifying peak buying periods for specific products, the business can adjust its ordering processes accordingly. In turn, this results in less waste and maximized sales opportunities. It’s a real win-win situation, paving the way for a more adaptable inventory strategy moving forward.
Blockchain Technology in Inventory
Blockchain technology isn't just a buzzword; it has the potential to revolutionize inventory management. At its core, blockchain offers a decentralized ledger system that provides transparency and traceability. This means that every transaction or movement of goods is recorded and accessible to relevant parties. The benefits of this traceability are manifold.
Firstly, businesses can track their products throughout the supply chain. This not only reassures customers about the authenticity of goods but also assists in quickly identifying bottlenecks or issues that may arise. Imagine a scenario where a batch of products is recalled—blockchain makes it easier to pinpoint where the products are at any given moment, thereby reducing turnaround time for addressing such issues.
Additionally, using smart contracts can streamline purchasing processes. These are self-executing contracts with the agreement directly written into code. Once defined conditions are met, actions are taken automatically. For instance, payment can be triggered once goods are received and verified. This reduces the time spent on manual reconciliation processes, leading to faster and more efficient operations.
"The integration of blockchain technology in inventory management can enhance accountability, making it easier to verify product history at a glance."
As businesses look towards the future, those that integrate AI and blockchain into their inventory practices will undoubtedly set themselves apart from the crowd. These technologies not only improve operational efficiency but also instill trust in both suppliers and consumers. In summary, keeping an eye on these trends is crucial for any organization seeking to thrive in the competitive landscape of product inventory management.