Exploring the Importance of Traceability Software in Manufacturing
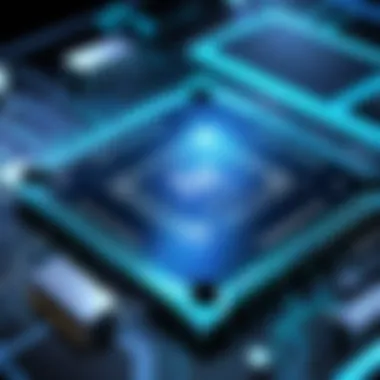
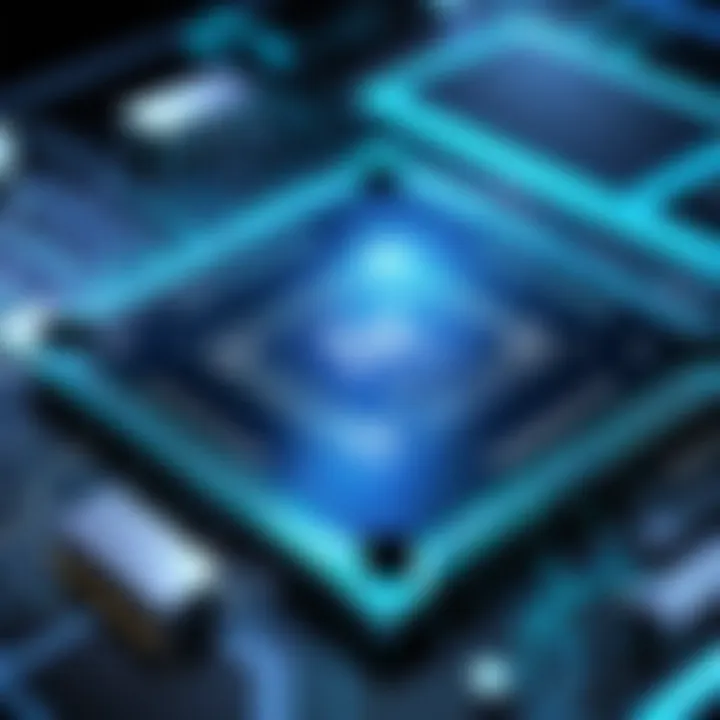
Intro
In today’s rapidly evolving manufacturing landscape, the ability to trace products through every phase of production has become paramount. Traceability software plays a pivotal role, offering tools that empower manufacturers to monitor, analyze, and improve processes while ensuring compliance with industry standards. As we navigate through the complexities of manufacturing, understanding the essence of traceability software is not just valuable—it's crucial for staying competitive.
The demand for accountability and transparency is soaring, with customers and regulators alike emphasizing the need for traceable manufacturing processes. This article will delve into the various intricacies surrounding traceability software, discussing its key features and functionalities, pricing structures, and real-world applications. By uncovering these elements, we aim to provide a thorough understanding that will assist decision-makers, IT experts, and entrepreneurs in effectively implementing traceability solutions.
It’s not just about technology; it’s about weaving a fabric of integrity and efficiency into the supply chain. From navigating regulatory landscapes to leveraging data analytics, this article will serve as a roadmap, steering you through the significant facets of traceability software for manufacturing.
Prolusion to Traceability Software
In the fast-paced world of manufacturing, traceability software is no longer a luxury—it's a necessity. Companies are facing mounting pressure to maintain high quality, ensure compliance, and streamline operations. The significance of traceability software lies in its ability to provide an organized approach to the management of critical data throughout a product's lifecycle. With traceability, businesses can track each component's journey from inception to final assembly. This not only enhances accountability but also plays a pivotal role in quality assurance.
Definition and Purpose
Traceability software serves a specific function: it enables organizations to document and oversee the intricate details that accompany the manufacturing process. The primary purpose is to facilitate the tracking of materials, components, and finished goods, thus ensuring that every element conforms to the established standards. Think of it as a digital ledger that meticulously records every move a product makes through the supply chain. This is vital for pinpointing the origins of defects, tracing batch numbers, and gathering valuable insights on production efficiency.
However, the utility of traceability software extends beyond mere tracking. It arms decision-makers with real-time data that can inform strategies and bolster decision-making. By employing such technology, businesses position themselves to swiftly resolve any hiccups in the supply chain and to respond effectively when regulatory bodies come knocking.
Historical Context of Traceability in Manufacturing
Historically, the need for traceability in manufacturing came into sharp focus in the latter half of the 20th century. As globalization reshaped the landscape of production, businesses started to recognize that more oversight was necessary. The food and drug industries were the trailblazers—their scandals laid bare the catastrophic consequences of lack of accountability. Key regulatory frameworks emerged, demanding more comprehensive documentation and reliable tracking systems.
Fast forward to today, and the manufacturing sector has witnessed a seismic shift. The advent of the Internet of Things (IoT) has revolutionized how data is captured and utilized. With sensors being embedded in machinery and products, manufacturers can continuously monitor production processes and materials. As a result, maintaining a detailed record through traceability software has transitioned from a cumbersome requirement to an integral part of operations. Now, every component is cataloged, providing a wealth of data that significantly enhances transparency.
One might consider the case of a pharmaceutical company where traceability is literally a matter of life and death. Keeping track of raw materials from supplier to consumer ensures that safety standards are met at every step of the way. This has become a non-negotiable aspect of production.
The trajectory of traceability in manufacturing reflects not just compliance requirements but also a growing awareness of consumer rights to know what goes into the products they use. Businesses that fail to adapt may find themselves at a disadvantage, both from a regulatory and reputational standpoint.
Core Features of Traceability Software
Traceability software serves as the backbone of modern manufacturing, weaving transparency into intricate processes. It’s not just about overseeing production; it’s about embedding a culture of accountability that ripples through the supply chain. By understanding the core features of this software, decision-makers can equip their organizations with tools that not only meet compliance but also enhance operational efficiency.
Data Capture and Management
A pivotal function of traceability software is its ability to capture and manage data throughout the manufacturing process. Think of it as having a digital ledger that notes every move from raw material sourcing to the final product shipment. This wealth of information enables manufacturers to track items at every stage of production, ensuring that every piece can be traced back through the entire lifecycle.
Data capture can include everything from batch numbers and expiration dates to supplier details and shipment logs. Having all this information organized means that when something goes pear-shaped—like a product recall due to a quality issue—companies can rapidly pinpoint the source of the problem. It streamlines not just recovery efforts but also helps mitigate risks, potentially saving significant costs down the line.
- Efficiency in Reporting: Automated data management can generate real-time reports, highlighting trends or anomalies. This is crucial for informed decision-making.
- Error Reduction: By reducing the reliance on manual entry, traceability software minimizes human error, which can impact product quality and compliance.
Real-Time Tracking Capabilities
In a fast-paced production environment, being able to track items in real time is indispensable. Real-time tracking allows manufacturers to monitor the status and location of products as they move through production processes. It’s akin to having a GPS for your inventory. The immediacy of this information not only enhances visibility across operations but also has a significant impact on efficiency.
When manufacturers have instant access to the whereabouts of their materials and products, they can better manage workflows and anticipate issues before they escalate. For example, if a delay is flagged, adjustments can be made instantly to the production schedule, saving time and resources.
Furthermore, the implementation of RFID technology and IoT devices can further enhance these tracking capabilities, allowing data to be collected and relayed seamlessly. This leads to:
- Reduced Downtime: With real-time insights, companies can address potential bottlenecks proactively.
- Inventory Optimization: Monitoring stock levels in real-time supports better inventory management, reducing overstock and stockouts.
Compliance and Reporting Tools
Manufacturers operate under a landscape of regulations that vary widely by industry. Compliance is not just a nice-to-have; it’s a must. Traceability software typically includes robust compliance and reporting tools that help ensure that all operations adhere to required standards. This feature helps in navigating the complex web of regulations, making it straightforward to generate reports that demonstrate compliance.
The best compliance tools provide users with the capability to:
- Automate Audit Trails: Keep records of every transaction and change made in the system, proving invaluable during inspections.
- Standardized Reporting: Tailor templates for various regulatory bodies, ensuring accurate and timely submissions.
- Real-Time Alerts: Notify users of compliance hurdles, allowing them to take corrective actions before non-conformity issues arise.
"In an age where regulatory pressure continues to mount, leveraging traceability software not only facilitates compliance but positions a company as a leader in accountability and transparency."
By encompassing these core features—data capture and management, real-time tracking capabilities, and compliance tools—traceability software establishes a solid foundation for enhancing product quality and operational efficiencies across the manufacturing landscape.
Benefits of Implementing Traceability Software
In today's fast-paced manufacturing world, traceability software stands out not just as a tool but as an essential component that drives multiple advantages across industries. Embracing this technology can profoundly influence everything from quality control to overall operational efficiency. The focus on traceability is not merely about product lineage—it's about ensuring accountability through every step of the manufacturing process.
Enhanced Quality Control
Quality control isn't a mere box-ticking exercise anymore; it’s a critical part of the manufacturing puzzle. With traceability software in place, organizations can monitor each phase of production meticulously. The bundles of data collected in real-time allow for immediate identification of defects at any stage. When an error does crop up, manufacturers can track it back to its origin—be it raw materials or a specific machine malfunction—to rectify it effectively.
Imagine a scenario where a small widget in a complex assembly is found defective. Without traceability, spotting the flaw may involve guesswork and trial and error, potentially jeopardizing entire batches. But with a robust traceability system, the manufacturer can pinpoint the precise batch of components that went into that faulty widget. With the click of a button, they can effortlessly backtrack and implement focused corrective actions, reducing waste and safeguarding the brand's reputation.
Increased Operational Efficiency
Operational efficiency is about doing more with less. When implemented correctly, traceability software can drastically streamline various processes in manufacturing. Consider a plant that produces various products on the same assembly line. Without an intelligent system to track parts and materials, inefficiencies abound. But with clarity from traceability tools, inventory is managed effectively, reducing surplus and shortages alike. Information flows seamlessly, leading to quicker decision-making.
Another aspect is resource utilization; having precise data means that every machine and labor hour can be optimized. For instance, if specific machinery is only used during certain production runs, traceability software can help plan maintenance and repairs during downtimes, ultimately saving costs and extending the life of expensive equipment.
"The control and efficiency gained from traceability can flip operational woes into successes before they even surface."
Improved Supply Chain Transparency
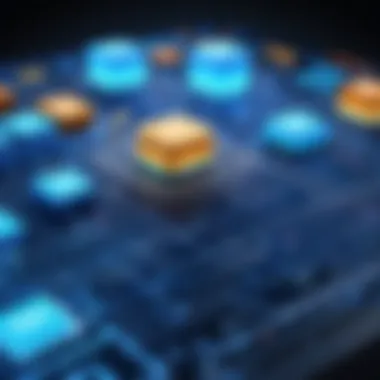
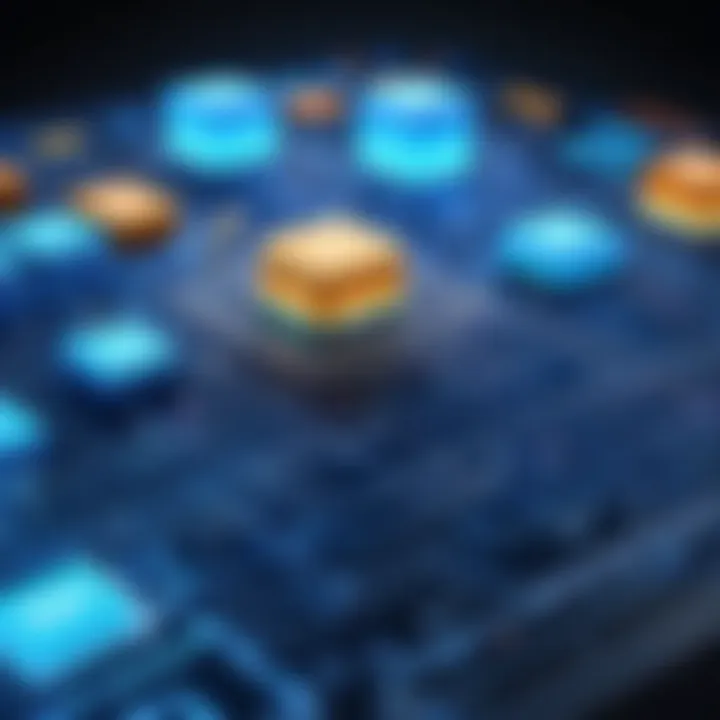
Today's consumers demand transparency—where their products come from, how they’re made, and who’s involved in the journey. This scrutiny doesn’t just apply to retailers; manufacturers too must rise to the challenge. Traceability software provides visibility across the supply chain, making it easier for companies to share critical information with stakeholders, including end-users.
When all parties have access to an accurate history of products—from supplier to delivery—trust builds. Consumers can verify claims made about a product, like "organic" or "locally sourced," without diving into a rabbit hole of confusing paper trails. For instance, if a food manufacturer uses traceability solutions, they can quickly provide proof of compliance with safety standards, which is vital in sectors like food and pharmaceuticals. This transparency not only fulfills compliance duties but also elevates brand credibility in a market where such factors weigh heavily in purchasing decisions.
Overall, implementing traceability software can provide myriad benefits. Enhanced quality control, increased operational efficiency, and improved supply chain transparency form the bedrock of a robust manufacturing framework, leading to better accountability, informed decision-making, and ultimately, a firmer grip on marketplace dynamics.
Companies looking to harness these advantages must recognize that traceability is not merely about following products; it’s about fostering a culture of excellence and accountability that extends to every aspect of their operations.
Regulatory Compliance and Standards
Regulatory compliance in manufacturing is not merely a box to tick; it is a vital component ensuring that products meet all necessary legal and safety standards. These regulations protect consumers and foster a competitive marketplace. Understanding the regulations that govern manufacturing practices is crucial for businesses aiming to implement traceability software. This software assists in tracking materials and processes throughout production, ensuring adherence to regulations and maintaining high-quality standards.
Industry-Specific Regulations
Different industries are subject to unique regulatory frameworks designed to safeguard public health and safety, which directly influences the design and implementation of traceability software.
For example, the food and beverage industry must follow stringent guidelines dictated by the Food and Drug Administration (FDA) in the United States. These regulations focus on food safety and require that manufacturers quickly identify the source of contamination during recalls. Effective traceability software provides complete visibility into the supply chain, enabling companies to pinpoint contaminated batches without delay. Similarly, the automotive industry is governed by regulations such as ISO/TS 16949, which emphasizes quality management and requires detailed records of components from suppliers. Here, traceability software supports manufacturers in maintaining compliant documentation and ensures accountability across the supply chain.
Moreover, the pharmaceutical sector faces complex regulations that involve Good Manufacturing Practices (GMP) and track-and-trace requirements. These regulations necessitate strict adherence to protocols that ensure drug safety and efficacy throughout distribution. In this arena, effective software solutions can simplify compliance by automating data capture and enabling seamless tracking of products from manufacturing to the pharmacy.
Global Standards Influencing Adoption
Beyond local regulations, global standards are increasingly shaping how manufacturers integrate traceability software into their processes. The International Organization for Standardization (ISO) sets forth various standards that promote best practices across industries. For instance, ISO 9001 focuses on quality management systems, pushing businesses to monitor and analyze operations closely.
Additionally, the adoption of standards like GS1 allows manufacturers to standardize barcodes, enhancing traceability capabilities and improving data accuracy. These standards support interoperability among systems, enabling easier data sharing across different platforms and making it simpler for companies to fulfill global trading requirements. It is vital that manufacturing businesses stay abreast of these evolving standards. A lack of compliance not only risks regulatory penalties but can also diminish consumer trust.
"Traceability isn't just about accountability; it's about weaving a fabric of trust between suppliers, manufacturers, and consumers."
Integration with Existing Systems
Integrating traceability software with existing systems serves as a linchpin in enhancing the overall efficiency and effectiveness of manufacturing operations. The seamless interaction between new traceability tools and legacy systems can significantly amplify data accuracy, streamline processes, and enable better decision-making. When organizations recognize the potential pitfalls of poorly integrated systems, they understand that a robust traceability solution should not exist in isolation; rather, it must be closely intertwined with other operational platforms such as Enterprise Resource Planning (ERP) systems.
With the right integration, businesses can facilitate real-time data flow, reduce the need for manual data entry, and cut down on human errors. In this context, understanding and adapting to the nuances of existing systems becomes vital. Companies need to assess the technological landscape they operate in to truly appreciate how traceability solutions can complement and enhance those systems.
ERP Systems and Traceability Solutions
ERP systems are quite common among manufacturing firms, bringing together various business processes under a single umbrella. By integrating traceability software with ERP systems, a business can achieve a holistic view of its operations. This integration not only helps in monitoring production processes but also allows for tracking raw materials, components, and finished goods across the supply chain.
- Real-Time Updates: Integrated systems provide up-to-the-minute information, which aids in timely decision-making.
- Streamlined Operations: When the traceability software interacts with the ERP system, it automates many manual processes, reducing redundancy and freeing up employee time.
- Enhancing Accountability: Integration fine-tunes tracking capabilities, allowing for clearer accountability regarding product recalls or quality issues.
However, while the benefits are compelling, organizations must ensure the integration process is well-planned and executed.
Challenges in System Integration
Data Synchronization
Data synchronization stands out as a critical aspect of integrating traceability software and existing systems. It ensures that all systems are working with the same set of data, vital in manufacturing where the nature of operations can change rapidly. One key characteristic of data synchronization is its ability to update information across various platforms automatically.
- Real-Time Data Exchange: The synchronization allows for immediate updates across all systems, which is beneficial for maintaining the consistency of information.
- Accuracy and Reliability: With proper synchronization, organizations can mitigate the risk of errors that typically arise from manually entering data into separate systems.
Nevertheless, data synchronization comes with its own share of challenges. The complexity involved in mapping different data formats can lead to a painstaking implementation process. Additionally, teams must also deal with the potential for data conflicts when systems are not aligned properly.
User Training
User training is another pivotal aspect of effective integration. Even if the technology aligns perfectly, without properly trained personnel, the implementation can fall flat. A key characteristic of user training is its focus on enhancing familiarity with new systems and processes.
- Increased Adoption Rates: Well-trained users are likely to embrace the new software, thus making the integration more successful.
- Risk Reduction: Training helps in reducing user errors, which can otherwise lead to costly misunderstandings and operational hiccups.
That said, the unique feature of user training is that it requires ongoing effort. Organizations cannot just conduct a single training session and expect proficiency. Continuous support and refreshers are often needed to keep users updated and confident in utilizing the system.
Case Studies in Various Industries
Case studies play an essential role in illustrating the practical applications and advantages of traceability software in real-world settings. They serve as powerful examples of how various industries leverage these tools to enhance product quality, optimize processes, and ensure compliance with regulatory standards.
The importance of case studies extends beyond mere anecdotal evidence. They provide concrete data, showing measurable outcomes that organizations have achieved exclusively through the implementation of traceability systems. By examining these cases, decision-makers, IT professionals, and entrepreneurs can glean insights into best practices, potential pitfalls, and the adaptive strategies employed by different sectors.
Through these narratives, we can see the interplay between technology and industry demands, helping stakeholders to appreciate the depth and breadth of traceability software in a practical context.
Automotive Industry Applications
The automotive industry serves as a prime example of how traceability software can revolutionize operations. Manufacturing vehicles involves multiple suppliers, intricate supply chains, and strict quality assurance protocols. Companies like Toyota have integrated advanced traceability solutions to monitor components from the supplier's factory to the assembly line. This meticulous tracking helps in identifying defects quickly, ensuring that any faulty parts can be traced back through the supply chain, dramatically reducing the risk of recalls.
By adopting traceability software, manufacturers can also comply with various regulations, such as the ISO/TS 16949 standard. This compliance not only enhances quality control measures but also builds trust with consumers who increasingly prioritize safety and accountability in their vehicle purchases. Furthermore, the system allows for the optimization of production lines by providing data-driven insights into bottlenecks or inefficiencies, ultimately leading to improved operational performance.
Food and Beverage Sector Implementation
In the food and beverage sector, traceability is not just a best practice; it's a necessity driven by consumer safety and regulatory compliance. The infamous E. coli outbreaks have underscored the importance of tracking food ingredients from farm to table. Companies like Nestlé have implemented robust traceability solutions that allow them to oversee product safety and supply chain transparency effectively.
With the help of traceability software, organizations can ensure that every ingredient is documented from its source, processed precisely, and distributed safely. This system includes tracking batch production and monitoring expiration dates, which can help avoid spoilage and foodborne illnesses. Moreover, these systems facilitate quick responses in the case of product recalls.
Investing in traceability solutions not only elevates quality assurance but also boosts the brand’s image among consumers who know their food is safe from farm to fork.
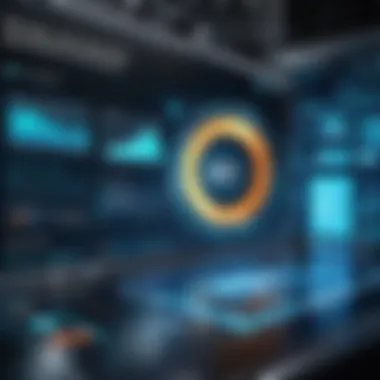
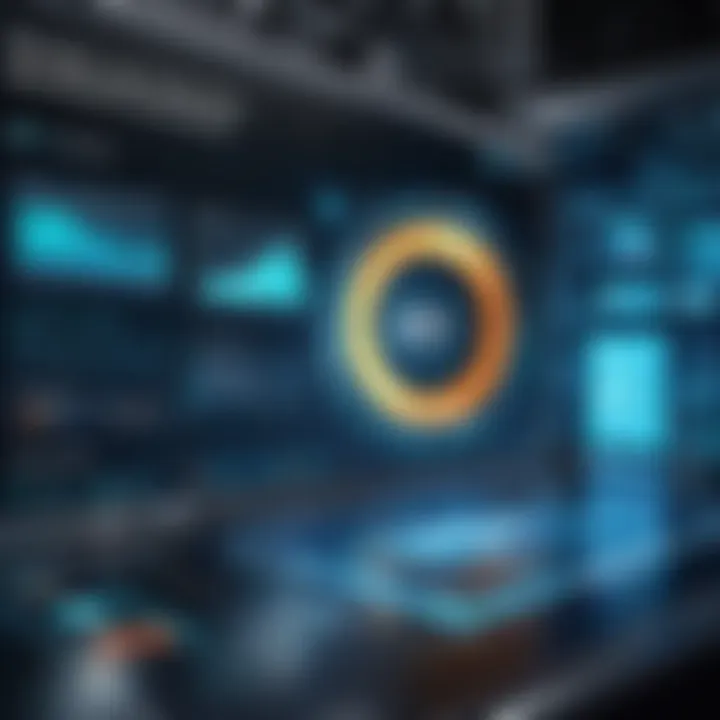
Pharmaceuticals and Healthcare Examples
The pharmaceutical industry stands at the forefront when it comes to stringent regulations concerning product integrity, safety, and traceability. Companies like Pfizer and Johnson & Johnson have employed traceability software to comply with the Drug Supply Chain Security Act (DSCSA), which mandates that all drugs in the supply chain must be verifiable.
Through these systems, pharmaceutical manufacturers connect with suppliers and distributors, documenting each step of a drug's journey. This connectivity ensures that counterfeit drugs can be identified and removed from circulation, which is crucial for patient safety.
Moreover, traceability systems enable the effective oversight of temperature-sensitive medications during transit. The ability to monitor conditions ensures that the efficacy of pharmaceuticals is never compromised. The data gathered also supports analytics, which can lead to improvements in inventory management and decision-making processes.
"With traceability, clarity in operations leads to dictated outcomes that elevate industry standards."
Data Analytics and Reporting
In today’s fast-paced manufacturing environment, the importance of data analytics and reporting cannot be overstated. These elements are not just added benefits; they're the backbone of making informed decisions that can affect quality, compliance, and operational efficiency. Traceability software collects an abundance of data at each stage of production. The real trick lies in turning that pile of data into actionable insights that can drive changes within the organization.
Leveraging Data for Decision Making
Data analytics empowers manufacturers to dive deeper than surface-level observations. When organizations employ traceability software, they can capture details on every component of the manufacturing process. This real-time data allows managers to identify trends that could signal underlying problems. For instance, if a specific machine frequently requires repairs, it might indicate a looming failure that, if not addressed, can halt production.
By analyzing historical data alongside real-time performance metrics, decision-makers can make verifiable predictions about future outcomes. They can develop a stronger grip on operational efficiencies or unearth ways to cut down waste. Equally vital is the ability to benchmark performance against industry standards or internal goals, providing clarity that can guide strategic initiatives.
Key Performance Indicators for Success
KPIs serve as the compass for navigating through complex data landscapes. These indicators help firms focus on what matters most. Here are some notable metrics that define success within traceability:
- Product defect rates
This tells how many products fail quality control checks, allowing for adjustments in production processes. - Cycle times
Measuring the time taken from production start to finish highlights bottlenecks or inefficiencies. - On-time delivery rates
A critical measure of a supplier's reliability, indicating how well the supply chain is functioning. - Cost per unit
This helps in understanding production costs and can guide pricing strategies for products.
"You can’t manage what you don’t measure."
This saying rings particularly true in manufacturing. Without relevant KPIs, firms can drift aimlessly instead of making informed, data-driven decisions.
Incorporating robust analytics within your traceability framework can offer a wealth of insights that lead to improved decision-making and ultimately boost competitiveness in the market. As manufacturing continues to evolve, those companies utilizing these insights effectively are likely to emerge as leaders, not just survivors.
Challenges of Traceability Software Adoption
The implementation of traceability software isn’t all smooth sailing. In fact, businesses often find themselves in turbulent waters when it comes to adoption. As companies look to enhance transparency and quality control within their manufacturing processes, they must navigate several challenges that often act as roadblocks. Understanding these obstacles is crucial for decision-makers and IT professionals, as it helps to forge a pathway toward successful implementation. Here, we delve into three primary challenges: high initial investment costs, resistance to organizational change, and ongoing maintenance and support issues.
High Initial Investment Costs
One of the most noticeable hurdles businesses face while adopting traceability software is the hefty price tag attached to initial investment. From software licenses to hardware upgrades, costs can soar, particularly for small to mid-sized enterprises. For instance, a complex solution tailored specifically for the automotive industry might come with a steep starting price, potentially reaching hundreds of thousands of dollars.
Moreover, the return on investment (ROI) might not be immediately clear.
"When financial outlay dwarfs potential savings, many organizations hit the brakes on adoption."
It's essential for businesses to perform detailed cost-benefit analyses. This way, they can weigh how increased operational efficiency and enhanced quality control may ultimately offset the initial expenditures. Factors to consider include:
- Direct costs: Software purchase, hardware upgrades, installation fees.
- Hidden costs: Additional training, integrating with existing systems, and potential downtime during the transition.
- Long-term benefits: Reduced liability from compliance issues, enhanced tracking leading to fewer recalls, and improved customer satisfaction.
Resistance to Change Within Organizations
Humans are creatures of habit, and introducing new systems often meets with a certain degree of skepticism. Employees may resist traceability software due to fear of the unknown or disrupting comfortable routines. This resistance can stem from various factors:
- Fear of job displacement: Employees may worry that automation will render their roles obsolete.
- Lack of understanding: If employees do not grasp the benefits of the new software, they may see it as an added burden rather than a tool for improvement.
- Cultural barriers: Long-standing practices can create a culture entrenched in traditional methods, making shifts seem daunting.
To mitigate resistance, effective communication is vital. Organizations should engage employees early in the process, addressing concerns and highlighting benefits. Offering training sessions can also demystify the technology and promote a smoother transitional journey.
Ongoing Maintenance and Support Issues
Even after a successful launch, traceability software requires continuous maintenance and support. Companies may find themselves grappling with:
- Technical support availability: Sometimes, the vendor might not provide support outside business hours. This can leave teams stranded during critical operational hours.
- Software updates and upgrades: Regular maintenance might necessitate downtime, affecting production schedules.
- Adapting to regulatory changes: As regulations evolve, keeping the software compliant can place additional demands on resources and capacity.
It's important for organizations to plan for long-term support from the get-go, perhaps even considering options for having an in-house IT staff or outsourced solutions capable of addressing their unique needs.
In summary, while the challenges of adopting traceability software are significant, they are not insurmountable. By strategically addressing these concerns, businesses can unlock the full potential of traceability solutions and enhance their manufacturing processes for the better.
Future Trends in Traceability Software
As the tides of technology continue to ebb and flow, manufacturers are finding themselves in a sea of change. The future of traceability software is not just a blip on the radar; it's a paradigm shift that is reshaping how industries operate. This section explores the pivotal trends influencing traceability software, emphasizing technological advancements and shifting consumer demands.
Advancements in Technology
AI and Machine Learning
Artificial Intelligence and machine learning are redefining the landscape of traceability software, offering breakthroughs that enhance performance and decision-making. One of the most striking aspects of AI in this realm is its ability to learn from vast amounts of data. Instead of slogging through endless reports, businesses can harness machine learning algorithms to predict bottlenecks or quality issues before they arise. This predictive capability is a game-changer, allowing companies to address potential problems proactively, which translates into substantial cost savings.
However, while AI offers a robust toolkit, it is not without its challenges. The data required to fuel these systems must be clean and structured, or the insights can lead to misguided decisions. In addition, companies need to ensure personnel are adequately trained to work alongside these technologies. Simply adopting AI and machine learning is not enough; the context in which they are applied is critical to deriving benefits.
Blockchain Integration
Blockchain has emerged as a trailblazer in sectors demanding unprecedented accountability and transparency. In essence, it creates an immutable record of transactions and movements within the supply chain, addressing a critical need for reliability in traceability. This key characteristic of blockchain—its ability to provide an unalterable ledger—ensures that every step in the manufacturing process can be tracked and verified.
What sets blockchain apart in our discussion is its unique feature of decentralization. Information disseminated across a network of nodes means multiple parties can oversee and authenticate records. This reduces the risk of fraud and increases stakeholders' confidence in the information presented. However, the integration of blockchain brings forth its share of hurdles. The technology’s complexity can pose integration challenges. Additionally, companies must weigh the trade-off between enhanced security and the potential for increased costs of implementation.
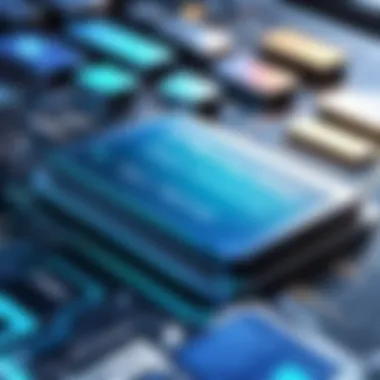
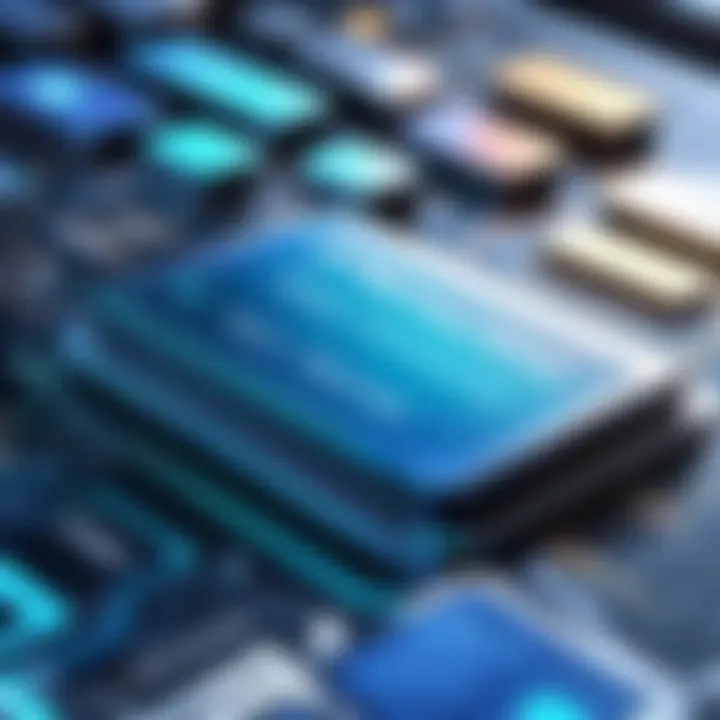
Changing Consumer Expectations
Gone are the days when consumers accepted products at face value. Today's customers are keen to understand the story behind their purchases. The demand for transparency is on the rise. They want to know where materials come from, how products are manufactured, and what safety measures are in place. Traceability software must adapt to these expectations, evolving into an indispensable tool for providing clarity.
This shift necessitates a more customer-centric approach to manufacturing, where businesses must not only track products effectively but also present this information clearly to consumers. Those who embrace this change are better positioned to cultivate trust and loyalty, fostering long-lasting relationships that benefit both parties.
"In an age where information is readily available, transparency is no longer a luxury; it’s a necessity."
In summary, future trends in traceability software are intricately tied to advancements in technology like AI and blockchain, and they reflect changing consumer expectations focusing on transparency and accountability. By staying ahead of these trends, businesses can not only bolster their traceability efforts but also enhance their overall operational resilience.
Selecting the Right Traceability Software
Choosing the right traceability software is like finding a key that fits a specific lock. It’s critical for ensuring operational excellence and quality assurance in manufacturing. With so many options available, selecting the most suitable solution demands careful consideration. The stakes are high given that the wrong choice not only wastes money but can also lead to compliance issues and inefficiencies. Therefore, understanding the elements involved in making this decision is vital for anyone leading a manufacturing operation.
Key Considerations for Buyers
When it comes to selecting traceability software, a few key aspects should take precedence:
- Understanding Organizational Needs: Before diving into vendor options, assess your company's unique requirements. What level of traceability is required? Does your operation involve complex supply chains, or is it more streamlined? This will guide you in understanding what features you actually need.
- Feature Set: Look for essential features like data capture, compliance reporting, and integration capabilities. A good software solution should be able to handle these aspects seamlessly. Make a checklist alongside your requirements and cross-compare features offered by various vendors.
- User-Friendliness: It's imperative that the software is intuitive and simple enough for your team to adopt without a steeper learning curve. If your employees find the system cumbersome, productivity could take a hit.
- Scalability: Consider your future. You don't want to be locked into a system that won't grow with your business. Opt for a solution that can scale up or down depending on demand.
- Vendor Support: Post-purchase support can make or break your experience. Research vendor reputations regarding customer service. Are they quick to respond to queries? Do they provide adequate training?
Vendor Evaluation and Comparisons
The process of evaluating vendors can feel like searching for a needle in a haystack, especially when so many options are on the market. Therefore, organizing the information and conducting thorough comparisons is crucial. Here are a few strategies for evaluating potential candidates:
- Request Demos and Trials: Many vendors offer free trials or demonstrations. Utilize these opportunities to gauge functionality and user experience. This hands-on approach can reveal more than brochures or marketing materials.
- Consider Reputation and Track Record: Look into reviews and testimonials. Satisfied users vouching for the software’s effectiveness adds credibility. Check platforms like Reddit or industry forums to gather insights from current users.
- Cost Analysis: Don't just focus on the sticker price. Calculate the total cost of ownership, including implementation fees and ongoing support costs. Compare these figures across different vendors for clarity.
- Customization Options: Some businesses may require bespoke features that fit their specific needs. Evaluate how customizable each software is. Flexibility can be a game-changer, particularly for unique operational requirements.
- Integration Capabilities: Your traceability software will likely need to work alongside other systems such as ERP solutions. A good piece of software should offer easy integration with existing systems and reduce the need for crippling disruptions during the adoption phase.
"Finding the right software is not just about features. It’s about aligning the tool with your strategic goals."
These careful considerations and evaluations will ensure that you are not just throwing darts in the dark when selecting traceability software. Every decision counts; making the right choice sets the stage for improved efficiency and accountability across your manufacturing processes.
Impact on Supply Chain Management
In today's fast-paced manufacturing landscape, the concept of supply chain management is fundamentally intertwined with traceability software. This intersection is not just crucial; it's vital for businesses aiming for efficiency, transparency, and compliance. Traceability software enhances supply chain management in a multitude of ways.
One of the most significant aspects is risk management. By employing comprehensive traceability systems, companies can quickly identify the source of defects, disruptions, or failures. Imagine a food manufacturing company that discovers a batch of products has been contaminated. With an effective traceability solution, the company can trace back to the specific supplier or production line, reducing the response time significantly. This pre-emptive capability not only mitigates risks but also protects the brand’s reputation.
Furthermore, traceability fosters an environment that promotes accountability. When all components and processes are documented and easily retrievable, it becomes simpler to hold suppliers and manufacturers accountable for their parts in the supply chain. This accountability often leads to better quality practices and a natural inclination towards excellence.
In addition to risk management, collaboration is another cornerstone of effective supply chain management. Traceability solutions break down silos between departments and external partners. Everyone involved—whether it's suppliers, logistics partners, or end retailers—can access relevant information, enabling smoother cooperation and integration. This shared access to data not only streamlines operations but enhances overall relationship dynamics among stakeholders.
"The goal of supply chain agility lies in facilitated connections and shared knowledge, which traceability software provides."
Among the other benefits included in the mix, one can also mention:
- Enhanced Decision-Making: With real-time data, organizations can make informed decisions quickly, adapting their strategies based on current conditions in the supply chain.
- Regulatory Compliance: Traceability software ensures adherence to industry standards and regulations, simplifying audits and inspections. This is not only about avoiding penalties but also ensuring consumer trust.
- Cost Reduction: By streamlining processes and preventing issues before they escalate, organizations can cut costs across various operations, from production to distribution.
As these elements weave together, the importance of traceability in shaping a resilient and agile supply chain becomes evident. Organizations that acknowledge this need position themselves ahead of the curve, effectively utilizing technology as a backbone for their supply chain management strategy.
Traceability and Risk Management
When we talk about traceability in the context of risk management, it's imperative to recognize the proactive stance it enables. By leveraging technologies that track and document materials throughout their lifecycle, manufacturers equip themselves with invaluable resources for identifying risk avenues. This encompasses not just quality control but also compliance with safety regulations, making it a multifaceted approach.
In the event of an incident such as a product recall, traceability allows organizations to efficiently track down affected supplies, minimizing potential fallout. A manufacturing company faced a recall situation found itself capable of isolating the tainted products among the hundreds sent out, demonstrating the practicality of such software. The ability to act swiftly can make a world of difference, both financially and regarding public perception.
Moreover, it provides a trail of transparency that can be critically examined, offering insights into areas needing improvement. This continuous feedback loop plays a huge role in refining processes and building better partnerships. In addition, risk management extends beyond internal operations—it includes the entire supply chain. Rich data provides stakeholders the ability to assess suppliers and their practices, warding off potential future risks at their source.
Enhancing Collaboration Across Stakeholders
Collaboration often stands as the linchpin of effective supply chain management, and traceability software strengthens this element considerably. With a dedicated platform that houses pertinent information, manufacturing businesses can foster deep connections with various stakeholders, from suppliers and logistics partners to customers.
For instance, when a manufacturing firm implements a traceability solution, they establish a shared database that all parties can access. This not only includes data on product status and quality indicators but encapsulates all the milestones achieved along the production process. When all stakeholders have visibility into this information, trust grows, and decision-making occurs more collaboratively.
Additionally, traceability tools facilitate joint problem-solving. Consider the case where logistics delays arise due to unforeseen circumstances. With accurate tracing of the status of goods, communication about delays or issues is open and timeout is reduced. Stakeholders can swiftly identify alternative routes or adjust production schedules to minimize the impact of disruptions.
To summarize, collaboration enhanced by traceability software leads to:
- Agility in the face of challenges.
- Informed decision-making, benefitting from collective insights.
- Fostering trust throughout the supply chain.
Ultimately, fostering collaboration among stakeholders through an effective traceability system positions manufacturing companies favorably in a competitive landscape. The cumulative benefits highlight a comprehensive approach to supply chain management, positioning organizations not just to survive but thrive.
Closure and Recommendations
The significance of wrapping up the discussion on traceability software can't be overstated. As manufacturers face increasing demands for quality, efficiency, and compliance, traceability software becomes a linchpin in meeting these challenges. In the final analysis, it’s about ensuring that every step of the manufacturing process is recorded, analyzed, and utilized to foster improved outcomes. The insights gathered from this exploration, together with the practical case studies, should provide a robust framework for decision-makers to level up their strategies.
Summarizing Key Takeaways
As this article has shown, the core of effective traceability software lies in several key components:
- Data Management: Adequate data capture methods ensure accuracy in tracking production from raw material to finished product. This minimizes errors and enhances the quality of the end product.
- Compliance: Understanding relevant regulations and maintaining standards is crucial. Non-compliance can lead to serious business repercussions, which makes a good grasp of these aspects critical for organizations.
- Integration: Seamless integration with existing systems like ERP means that businesses can avoid unnecessary disruptions. It also helps in maintaining data integrity and improving overall operational efficiency.
- Analytics: Using data analysis not only aids in improving current processes but also plays a role in predicting future needs and challenges. This proactive approach is invaluable.
To encapsulate, embracing traceability software offers substantial returns in quality, efficiency, and regulatory compliance.
Future Directions for Traceability Implementation
As industries evolve, so too must the technologies that support them. The future of traceability software appears influenced by several emerging trends:
- Artificial Intelligence: The growth of AI is poised to enhance data analysis capacities. Companies that can leverage machine learning will likely find themselves ahead of the curve, enabling predictive analytics.
- Blockchain Technology: Blockchain promises a revolutionary approach to data integrity and transparency. Its ability to provide a secure and immutable record could significantly refine traceability efforts, building consumer trust in the process.
- Consumer Expectations: Modern consumers are more informed and expect transparency in product sourcing and manufacturing processes. Companies need to adapt their traceability solutions to meet these expectations, enhancing their customer relationships along the way.
As we move forward, it’s paramount for businesses to stay abreast of these innovations and integrate them thoughtfully into their traceability strategies. The goal is not merely compliance but also the development of a more resilient and responsive manufacturing ecosystem.