Handheld Scanner Inventory System: A Detailed Overview
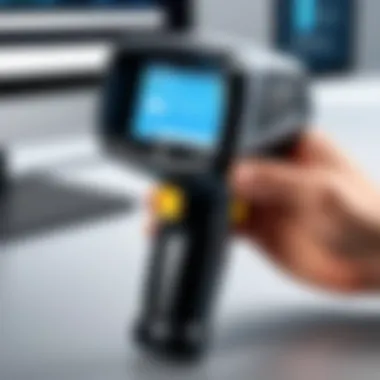
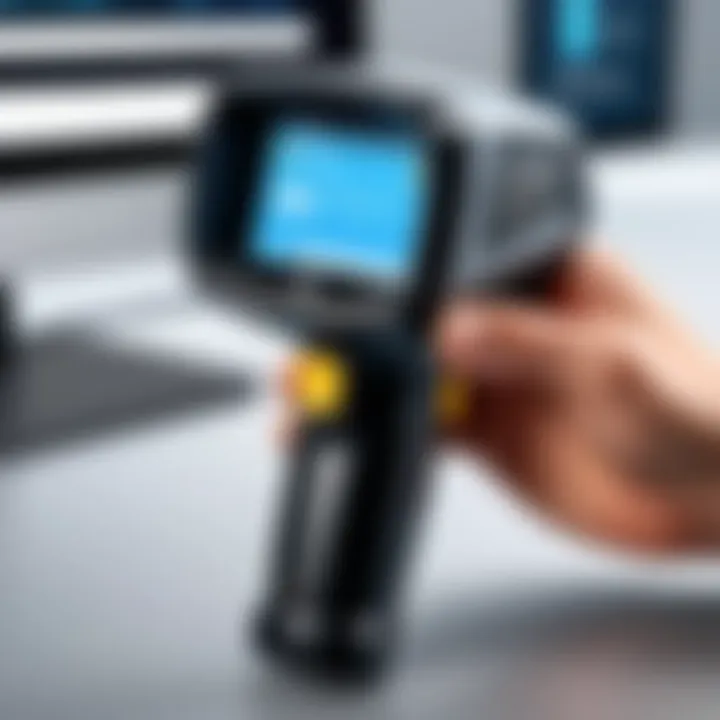
Intro
In today’s fast-paced business environment, streamlined inventory management plays a vital role in the operational efficiency of organizations. Handheld scanner inventory systems stand as a beacon of modern solutions, designed to tackle various challenges associated with traditional stock-taking methods. By digitizing inventory processes, these systems not only enhance accuracy but also reduce the time needed for inventory reconciliation. Essentially, they act as a bridge between manual efforts and ergonomic technology, allowing businesses of all sizes to capitalize on better data visibility and ultimately improve their bottom line.
This article delves into the intricate world of handheld scanner inventory systems, offering a comprehensive exploration of their essential features and functionalities, practical applications across different industries, and the considerations necessary for effective implementation. With the advent of these scanning devices, inventory management has evolved from tedious manual entries to a robust, streamlined, and data-rich process.
Among the myriad benefits these systems offer, their flexibility to adapt to various business environments makes them invaluable. Whether it’s a warehouse, retail store, or service industry, understanding and utilizing a handheld scanner inventory system can lead to substantial improvements in accountability, efficiency, and profitability.
Key Features and Functionalities
Comprehensive Overview
Handheld scanner inventory systems come equipped with a multitude of features that enhance their practicality and effectiveness. A few hallmark functionalities include:
- Barcode scanning: Essential for quick and accurate stock identification. This makes item tracking a breeze, allowing users to simply point and scan.
- Real-time data synchronization: Accurately tracks inventory levels, enabling businesses to make immediate decisions regarding stock replenishment, thus reducing the likelihood of overstocking or stockouts.
- User-friendly interface: Many systems feature touch-screen technology which offers a familiar interaction method for users, minimizing the learning curve and promoting ease of use.
- Integration capabilities: Handheld scanners work well with various ERP and inventory management software, creating an interconnected web of data that can be accessed from multiple locations.
These features synergize to forge a comprehensive inventory management solution that prioritizes efficiency and accuracy. It’s crucial for decision-makers to understand how these functionalities translate into everyday operational benefits.
Target Users
The scope of handheld scanner inventory systems is vast, catering to a diverse range of users across several sectors. Key target audiences include:
- Retail businesses: Retailers utilize these systems to maintain accurate stock levels, track sales trends, and optimize floor space utilization.
- Warehousing and logistics companies: In these environments, every second counts. Rapid scanning facilitates swift stock movement, thus enhancing logistic workflows.
- Manufacturing units: These facilities require precise inventory tracking to ensure a smooth production line, avoiding downtime due to material shortages.
- Healthcare providers: Hospitals and clinics rely on these systems to track medications and supplies, ensuring critical items are within reach at all times.
From entrepreneurs just starting out to seasoned IT professionals overseeing complex networks, the adaptability of handheld scanner inventory systems makes them essential tools in achieving operational excellence.
Pricing Models and Cost Analysis
Breakdown of Pricing Tiers
Investing in a handheld scanner inventory system involves considering various pricing tiers. Depending on features and capabilities, costs can vary significantly:
- Basic models: Typically start around $150 - $400 per device. Ideal for small businesses needing basic scanning features.
- Mid-range solutions: Generally range between $400 - $1,000, offering enhanced functionalities and better build quality suitable for moderate usage.
- High-end scanners: These can go from $1,000 to $3,000, equipped with advanced features like real-time data capabilities and rugged designs for heavy-duty use.
Additional Costs to Consider
Beyond the initial purchase price, additional expenses can creep in:
- Software licensing fees: Monthly or yearly subscriptions can add to overall costs, particularly with cloud-based systems.
- Training expenses: Ensuring staff is adequately trained could entail extra costs, especially for sophisticated systems.
- Maintenance and support: Some vendors charge for ongoing support and repairs which should be factored into a long-term budget.
Taking a comprehensive view of these factors is crucial for decision-makers to allocate resources effectively and ensure they get the best bang for their buck.
Preamble to Handheld Scanner Inventory Systems
Handheld scanner inventory systems represent a crucial advancement in how businesses manage their stock and asset tracking. As industries evolve, the need for precise and swift inventory control becomes paramount. These systems not only streamline operations but also significantly reduce human errors that can arise from traditional inventory methods. When it comes to modern logistics and inventory management, leveraging technology like handheld scanners is not just an option anymore; it’s a necessity.
Defining Handheld Scanners
At their core, handheld scanners are portable devices equipped with advanced scanning technologies, allowing users to capture data quickly and efficiently. They typically utilize laser or image-based scanning mechanisms to decode barcodes and QR codes embedded on products. This functionality translates into the ability to scan items in various environments, from bustling retail stores to expansive warehouse settings.
With a handheld scanner, users can record product details including identifiers, quantities, and condition with just a swift swipe. The versatility of these devices also lends itself to different sectors, from healthcare facilities managing medical supplies to manufacturers tracking components on assembly lines. Without a doubt, handheld scanners make the job of inventory management far less cumbersome and more accurate than manual counting or data entry methods.
Purpose and Importance
The purpose of employing handheld scanner inventory systems extends beyond mere convenience. For businesses, these systems epitomize efficiency, reducing the time spent on stock-takes and improving turnover rates. By utilizing handheld scanners, companies can achieve:
- Enhanced Accuracy: Automation minimizes the risk of human error, ensuring that inventory records are precise and up-to-date.
- Time Savings: Quick scanning means that routine tasks can be performed in a fraction of the time, increasing operational efficiency.
- Better Data Visibility: With real-time data access, businesses can monitor stock levels continuously, making informed decisions about restocking and inventory control.
- Resource Optimization: Prevents excess stock and enhances the effectiveness of supply chains.
"With the right hand-held technology, inventory management can transform from a logistical nightmare into a streamlined operation."
The significance of handheld scanner inventory systems is not only confined to their operational benefits but also encompasses strategic advantages. In a world where customer demands are ever-increasing, being equipped with an effective inventory solution can determine a company’s success in meeting those demands promptly. Furthermore, as businesses face growing pressures to refine their processes, adopting such innovative solutions becomes imperative to stay competitive.
How Handheld Scanner Inventory Systems Work
Understanding how handheld scanner inventory systems operate is paramount to grasping their efficiency and relevance in modern inventory management. These systems combine hardware and software components to streamline the tracking, storing, and processing of inventory data. By integrating scanning mechanisms, data storage, and connectivity options, these systems lead to significant improvements in inventory operations, yielding a more accurate and responsive method for managing stock.
Basic Components
The backbone of any handheld scanner system lies in its basic components. These elements may seem straightforward, yet they play crucial roles in enhancing inventory practices.
Scanning Mechanism
The scanning mechanism represents the vital interface between the physical world of inventory items and the digital realm where data is analyzed. At its core, this mechanism swiftly reads barcodes or QR codes, translating these into useful information. A prominent characteristic of scanning mechanisms is their speed. Devices like laser and imaging scanners can perform readings in a fraction of a second, significantly reducing the time staff spends on inventory tasks.
A unique feature of this scanning technology is its versatility. For instance, laser scanners excel in environments with high glare, while imaging scanners can read multiple codes at once, enabling bulk processing of items. However, one must consider the initial investment costs as high-end scanners can be pricey, affecting budget constraints in small enterprises.
Data Storage
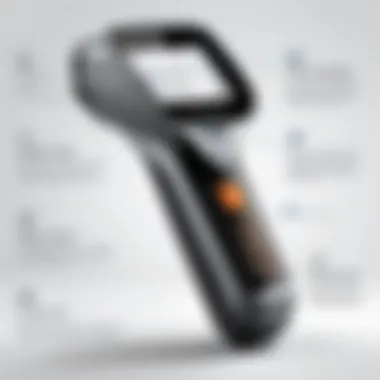
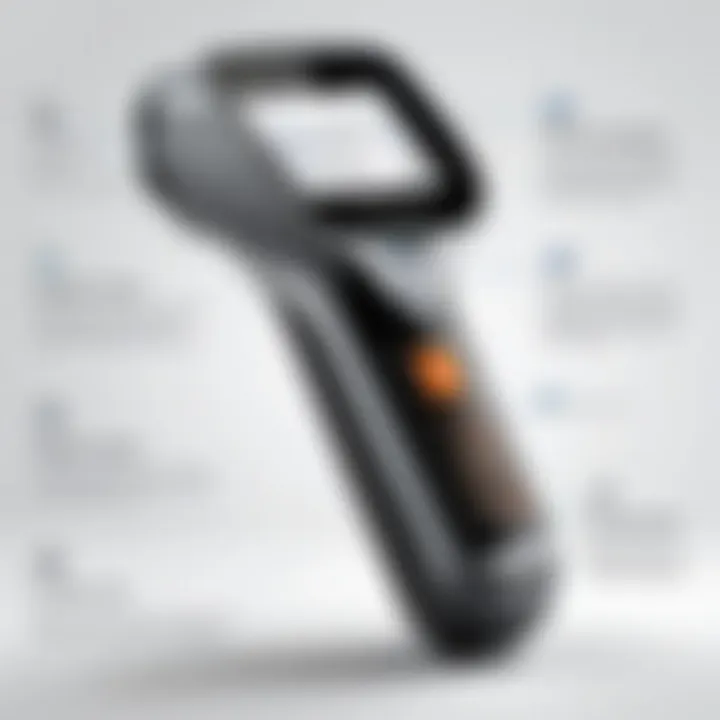
Next, data storage is another crucial aspect of handheld scanner systems that facilitates effective tracking and management of inventory. What stands out with data storage solutions is their ability to retain vast amounts of information in real-time. This characteristic ensures that inventory data remains current, reducing the risks of stock discrepancies.
Among data storage options, cloud storage has gained traction due to its accessibility. It allows multiple users to access inventory data from various locations, improving collaboration. However, one drawback might be the reliance on internet connectivity, which could hinder operations in areas with limited access.
Connectivity Options
Connectivity options are the threads that link handheld scanners to broader systems. These determine how scanner data is transmitted for analysis and reporting. Notably, options like Bluetooth and Wi-Fi afford ease of use; scanning can occur anywhere without needing cables.
A highlight of these connections is their ability to facilitate real-time updates. Staff members can immediately see inventory changes, which is a game-changer for businesses, especially in fast-paced environments. Still, there is a consideration with connectivity stability; connectivity drops could lead to data loss or outdated information being utilized, which needs to be managed vigilantly.
Integration with Software Solutions
For handheld scanners to realize their full potential, integration with software solutions is essential. This harmony enhances the usability and effectiveness of the entire system.
Inventory Management Software
Inventory management software acts as the control center for the data collected by handheld scanners. By centralizing inventory information, it allows users to track stock levels, complementing physical scans with insightful analytics. A strong point of these software applications is their capacity for customization, catering to specific industry needs.
One particularly useful feature is reporting functionalities that enable businesses to analyze trends over periods. This helps in decision-making, especially when forecasting future stock needs. However, users must remain vigilant regarding the complexity of some software, as a steep learning curve may deter less tech-savvy employees.
Cloud Storage Solutions
Cloud storage solutions further enhance the functionality of inventory systems, providing a scalable way to back up and manage data. A key characteristic is the ease of access, where users can securely log in from anywhere. This flexibility is crucial for businesses operating in multiple locations or with remote work arrangements.
The unique selling point of cloud storage is its automatic updates. Users are ensured that their data remains protected and reflects the latest changes without manual intervention. However, consideration should also be given to data security, as reliance on external servers introduces vulnerabilities that require robust protection measures.
Benefits of Using Handheld Scanners for Inventory Management
Handheld scanners have revolutionized how businesses approach inventory management. The integration of this technology brings a slew of advantages that can drastically improve efficiency and accuracy in storing and tracking items. For decision-makers, IT professionals, and entrepreneurs, understanding the positive impacts of handheld scanners is not just beneficial but essential for modern operations. The key benefits include notable improvements in efficiency and accuracy, access to real-time data, and enhanced cost-effectiveness that can lead to significant bottom-line benefits.
Efficiency and Accuracy Improvements
Using handheld scanners dramatically improves the efficiency of inventory management processes. Compared to traditional manual methods of counting and tracking inventory, which can be prone to human error, handheld scanners allow for quick and accurate scanning of barcodes. This minimizes discrepancies between physical counts and recorded data, leading to a cleaner, more synchronized lifecycle of stock management.
Moreover, the speed of data entry is noticeably faster. Imagine an employee scanning items at a rapid pace, seamlessly updating inventories without having to jot things down on paper or enter data manually into a system. The workflow becomes streamlined, leading to less time spent on mundane tasks and freeing staff to focus on value-adding activities.
Real-Time Data Access
In today's fast-paced business environment, having real-time access to data is invaluable. Handheld scanners facilitate immediate updates to inventory counts, meaning that managers can monitor stock levels as they happen. This ability to access current information allows for better decision-making, reducing the chances of stockouts or overstock situations. Sometimes, it is all about being one step ahead of the competition, and real-time access empowers businesses to do just that.
Best of all, this data can be integrated into larger inventory management software systems. The seamlessness of transferring data from the handheld scanner to a centralized software system enhances operational workflows across different departments.
"Real-time data access can save companies from the costs associated with stock discrepancies and inefficient processes, making it a crucial factor for enhancing profitability."
Cost-Effectiveness
While the initial investment in handheld scanner technology might raise eyebrows, the long-term savings can be substantial. Improved accuracy leads to less waste—think of unnecessary expenses incurred by overstocking or stockouts. Plus, the time saved on inventory tasks translates into lower labor costs. When employees can do more in less time, it allows for reallocation of human resources to other critical areas of the business.
Additionally, handheld scanners often require less maintenance compared to older inventory management systems, further reducing ongoing operational costs. In the end, having a more efficient and accurate system contributes to a healthier bottom line.
In sum, the benefits of using handheld scanners straddle efficiency, real-time insights, and cost-saving measures. For those who are still on the fence about integrating this technology, considering the long-term impacts might just tip the scales toward a more digitally enabled inventory management strategy.
Challenges in Implementing Handheld Scanner Systems
Implementing handheld scanner systems is no walk in the park. While they offer significant benefits, the road to successful integration has its fair share of bumps. Recognizing and addressing these challenges early can make a world of difference for organizations looking to streamline their inventory management. In this section, we will delve into some common hurdles faced by businesses that adopt handheld scanners, and provide insights on navigating these challenges effectively.
Initial Setup and Configuration
Getting the ball rolling with the initial setup of handheld scanner systems can be a daunting task. Installing hardware and configuring software isn’t just a plug-and-play scenario. Each device needs to be tailored to fit the unique workflow of the organization.
Every scanner has its own settings for scanning speed, data formats, and connectivity options. Decisions must be made about how the scanners will integrate with existing systems. This requires thorough testing to ensure compatibility, especially if the business is linking the scanners to warehouse management software or ERP systems. Any oversight at this stage may lead to long delays and operational inefficiencies.
A detailed implementation plan is crucial. Organizations often benefit from starting with a small pilot program to identify potential issues before rolling out the scanners on a larger scale. This approach allows for adjustments in both settings and processes, ensuring a smoother transition.
Employee Training Requirements
Once the scannrs are up and running, the next mountain to climb is employee training. Without proper training, even the most sophisticated technology can fall flat. Employees must not only learn how to operate the scanners but also understand how these devices integrate into their daily tasks.
Training sessions should be tailored to different roles within the organization. For example, warehouse staff might need hands-on practice with the devices, while management could benefit from insight into the data reporting features. A blend of instructional methods, such as hands-on training, video tutorials, and Q&A sessions, often proves effective.
Moreover, organizations should foster an environment of continuous learning. As updates roll out or new features are introduced, ongoing training can help employees stay up to speed. Identifying tech-savvy team members to lead by example can also ease the transition, creating a culture of support around the new system.
Maintenance and Upkeep
Lastly, maintenance and upkeep can’t be overlooked. Just like a car, handheld scanners need regular servicing to keep them running smoothly. This includes software updates, hardware cleaning, and troubleshooting any glitches.
Developing a maintenance schedule is essential for avoiding unexpected downtime. It’s important to designate specific team members responsible for routine checks, ensuring someone is always on the lookout for signs of wear and tear.
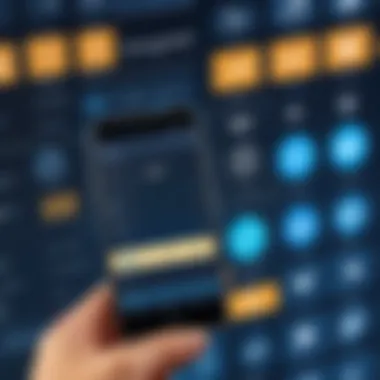
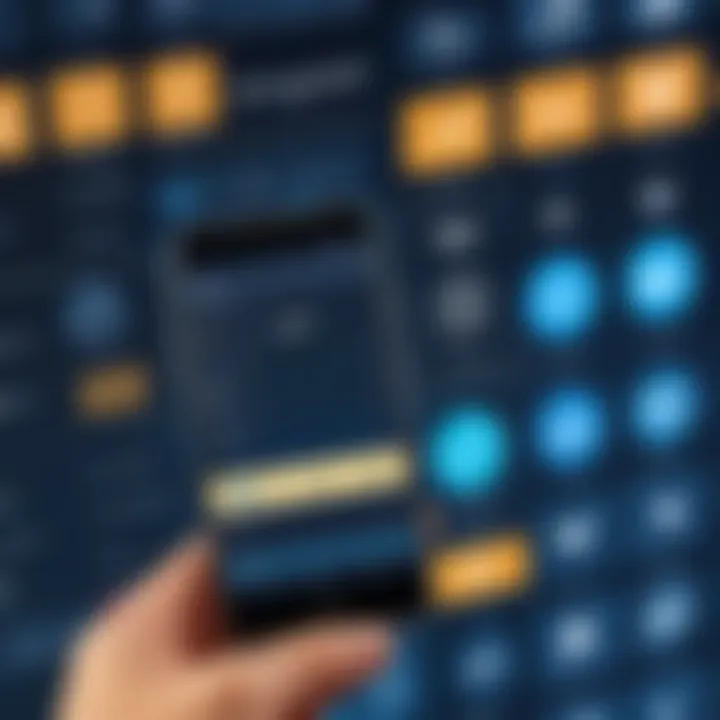
Additionally, choosing scanners with user-friendly interfaces and robust warranties can alleviate some of the long-term maintenance burdens. Companies should always consider the potential total cost of ownership when selecting scanners, factoring in not just the initial purchase price, but also the anticipated lifetime maintenance expenses.
"Anticipating challenges before they arise can ease the implementation journey."
While the challenges of implementing handheld scanner systems might feel overwhelming at first, with careful planning and execution, organizations can turn these challenges into opportunities for improvement.
Industry Applications of Handheld Scanner Inventory Systems
The realm of handheld scanner inventory systems extends far beyond merely scanning barcodes; it weaves seamlessly into various industries. Understanding the practical applications of these systems is vital for decision-makers and IT professionals looking to enhance operational efficiency. Each sector brings unique challenges and opportunities that can be addressed through tailored scanner solutions.
Real-time data collection, improved accuracy, and efficient inventory control are just a few advantages that handheld scanners furnish across different environments. In doing so, they transform how stocks are monitored, maintained, and replenished. Let’s delve into the specific realms where these systems shine.
Retail Environments
In retail, handheld scanners are invaluable. Picture a bustling grocery store where cashiers hustle through customer lines. A handheld scanner can streamline product checkouts and provide stock management insights. By scanning inventory directly from shelves, employees can quickly determine stock levels, increasing the speed of replenishing goods.
Moreover, handheld devices reduce human error, aiding in inventory accuracy. When paired with inventory management software, scanners can update stock levels in real time, ensuring that data is always up to date. This capability also supports loss prevention, enabling retailers to track sales alongside inventory movement.
Real-time tracking helps prevent overstock and stockouts, ensuring the right items are always available for customers.
Manufacturing Settings
In the manufacturing sector, handheld scanners work wonders. Manufacturers rely on precise inventory control for seamless operations. These devices allow operators to manage raw materials entering the production line and monitor finished goods moving out. By integrating handheld scanners with production systems, managers can track parts efficiently, reducing bottlenecks and increasing output.
Key considerations in this application include:
- Real-time data capture: Information retrieved via scanners can be immediately analyzed to make timely decisions.
- Quality control: By scanning products at different stages, manufacturers can ensure compliance with standards and mitigate defects.
Healthcare Facilities
In healthcare, accuracy and efficiency are paramount. Handheld scanners equipped with barcode reading capabilities assist in tracking patient records, medications, and supplies. This system reduces medication errors, ensuring that nurses and doctors administer the correct treatments at the right times. Additionally, it supports inventory management for medical supplies, which is crucial in high-pressure environments like hospitals.
Scanning also enhances data visibility across departments. With access to up-to-date supply information, healthcare staff can optimize ordering processes, thereby preventing critical shortages.
Warehouse Management
Warehousing represents one of the most critical applications of handheld scanner inventory systems. Here, the ability to perform real-time inventory updates is essential. By utilizing handheld scanners, warehouse personnel can track incoming and outgoing shipments, ensuring that stock levels are accurately recorded.
Benefits in a warehouse context include:
- Improved accuracy: Mistakes in stock handling are drastically reduced, promoting operational confidence.
- Efficiency gains: Tasks like picking orders or restocking shelves can be completed more quickly with scanner assistance.
Whether in retail, manufacturing, healthcare, or warehousing, handheld scanners play a pivotal role in the modern inventory landscape. Not only do they ensure accuracy and efficiency, but they also facilitate informed decision-making for managers and operators alike. In a world where information is king, these systems are the unsung heroes, providing a structured path to smarter inventory management.
Selecting the Right Handheld Scanner for Your Needs
Choosing the right handheld scanner can be a bit like picking the right tool from a toolkit. Depending on what you intend to do, you need something specific that can meet those needs efficiently. In the realm of inventory management, the right handheld scanner can make all the difference in streamlining processes and improving accuracy. It’s important to understand the various factors that contribute to an effective selection. This ensures that you not only get a scanner that meets your budget but also one that aligns with practical use in your industry environment.
Evaluating Features and Specifications
When it comes to handheld scanners, features matter a lot. You want to consider aspects like scanning speed, scanning range, and battery life. For instance, a scanner with a wireless connection might give you more flexibility in movement, especially in larger warehouses. Moreover, you need to check how well it can read different barcode types – some scanners work better with 1D barcodes, while others are designed for 2D or QR codes. It’s really about finding a balance that fits your specific needs.
Some key features to evaluate include:
- Scanning Mechanism: Look for laser versus imager options. Lasers are generally faster, but imagers offer more versatility in types of barcodes.
- Durability: If your operation is in a rough environment, consider rugged models that are resistant to drops or spills.
- Ergonomics: Comfortable handling can reduce fatigue during long shifts.
Here’s a tip: if possible, try out different models before making a purchase. Feeling the weight, grip, and functionality can provide insights that specs alone might not convey.
Assessing Vendor Reputation
Next up, vendor reputation plays a crucial role in your selection process. A brand that has established itself in the market typically has better support and service options. Check for reviews and seek out feedback from clients who've used the device in action. Forums such as Reddit are also valuable resources for uncovering real-life experiences. A reputable vendor often comes with advantages like readily available spare parts and reliable customer service, which can save you headaches down the line.
Some aspects to look into include:
- Customer Service: How responsive are they to inquiries and issues?
- Warranty and Return Policy: A good manufacturer will often provide a solid warranty along with a hassle-free return policy.
- Updates and Support: Ensure that the vendor keeps up with technological advancements and offers support for newer software requirements.
Cost Considerations
Price is always a factor when selecting equipment. While it might be tempting to choose the cheapest option on the shelf, skimping might cost you more in the long run, particularly if it leads to inefficiency or accuracy issues. Understand that you’re often paying for features, durability, and support when you opt for higher-end products. That said, it’s crucial to establish a budget that reflects your operational needs.
Consider categorizing your costs:
- Initial Purchase Price: This includes the scanner, any necessary accessories, and software.
- Operational Costs: Factor in things like batteries, maintenance, and any yearly subscriptions for software or updates.
- Long-Term Perspective: Think about what the scanner can save you—time, mistakes, and even potential losses from mismanagement.
In summary, selecting the right handheld scanner for your inventory needs is not just about price, but rather finding a model that complements your workflows, improves efficiency, and serves your business objectives. Think of it as an investment in the backbone of your operations. From evaluating features to assessing vendor credibility and understanding your cost structure, each step contributes to making a choice that’s not just good, but great.
Future Trends in Handheld Scanner Inventory Systems


The landscape of inventory management is in a constant state of evolution. As technology progresses, businesses must stay ahead of the curve to maintain an edge in efficiency, accuracy, and cost-effectiveness. Handheld scanner inventory systems are no exception; they too are adapting to new trends and innovations. Understanding future developments not only enhances operational capabilities but also helps in making informed strategic decisions. This section will delve into key trends shaping the future of these systems, focusing on technological advancements, integration with IoT, and enhanced data analytics capabilities.
Advancements in Technology
The pace of technological advancement in handheld scanners is nothing short of remarkable. Not too long ago, these devices served primarily as barcode readers, with fairly basic functionalities. Fast forward to today, and we have models equipped with high-definition cameras, faster processing units, and multifaceted scanning capabilities.
- Improvements in Battery Life: Modern handheld scanners are now being designed to last longer on a single charge, reducing downtime and maximizing productivity.
- AI Integration: The incorporation of artificial intelligence is transforming the way these devices function. For instance, AI can analyze scanning patterns and predict potential stock shortages.
- Ergonomic Designs: Companies are recognizing the need for comfort given that employees might spend long hours using these devices.
These technological strides not only streamline operations but also become a point of differentiation for businesses looking to enhance customer satisfaction.
Increasing Integration with IoT
The Internet of Things (IoT) phenomenon is all the rage, and its implications for inventory management can’t be overlooked. As more devices become interconnected, the potential to gather and analyze data on inventory levels in real time has never been more compelling.
- Remote Monitoring: Handheld scanners linked with IoT can allow managers to keep tabs on inventory as it moves. This is particularly useful for industries with dynamic supply chains, such as retail and manufacturing.
- Smart Alerts: Imagine your handheld scanner pinging you when stock is running low or alerting you to discrepancies between physical counts and system records. This level of responsiveness can save firms both time and money.
- Streamlined Delivery: Integrating these devices within a larger IoT framework can also speed up delivery timelines, as items are tracked seamlessly from warehouse to sales floor.
Through IoT integration, businesses augment their ability to make quicker decisions based on accurate, up-to-date information.
Enhanced Data Analytics Capabilities
Data is often likened to gold in today’s tech-driven environment, especially for inventory management. Handheld scanners are evolving into data collection hubs that provide invaluable insights.
- Predictive Analytics: Systems can analyze historical data to anticipate future inventory needs, enabling proactive supply management rather than reactive.
- Performance Metrics: Users can easily track key performance indicators such as turnover rates, shrinkage, and seasonal trends—all vital for strategic adjustments.
- Custom Reports: Many modern systems allow for customizable reports that can be tailored to specific needs, providing actionable insights to decision-makers.
In sum, as data analytics capabilities improve, inventory management will not only become more efficient but also strategically focused, allowing businesses to thrive in increasingly competitive environments.
"The future isn’t just something that happens; it’s something we actively shape with technology and data."
The trends discussed here indicate a clear trajectory towards more intelligent and integrated inventory systems. Staying informed and adapting to these changes will be crucial for any business wishing to leverage handheld scanner technology effectively.
Case Studies of Successful Implementation
In the realm of handheld scanner inventory systems, real-world examples provide tangible proof of their effectiveness. Case studies not only illuminate the practical benefits of these systems but also highlight the specific strategies adopted by different industries. By delving into successful implementations, decision-makers can draw parallels to their own situations, initiatives, and product choices.
Through these studies, we can explore the nuances involved, such as unique challenges faced, user feedback, and, most importantly, the measurable outcomes resulting from system integration. A closer look at two key sectors—retail and manufacturing—reveals both the critical considerations and vast potential of handheld scanners in day-to-day operations.
Retail Case Study
A large retail chain, known for its expansive product range and high customer traffic, sought to enhance inventory accuracy and reduce stock discrepancies. Before the implementation of handheld scanners, inventory counts were often laborious and prone to human errors.
Project Scope:
- A planned rollout of handheld scanners equipped with real-time data syncing capabilities.
- Integration with a comprehensive inventory management system.
By employing ruggedized devices capable of scanning barcodes, the retailer streamlined its stock counting processes. Employees, fully trained on scanner usage, found it far easier to record items and access real-time inventory metrics. Stock levels dropped sharply, leading to decreased overstock situations.
"The changeover was smoother than expected, and results were almost instantaneous. We've seen a stock accuracy improvement of 30% in just three months!"
— Inventory Manager, Retail Chain
Results Achieved:
- Efficiency: Reduced time spent in inventory audits by 40%.
- Cost Savings: A significant reduction in losses from misplaced or mis-scanned items, equating to savings in the thousands.
- Customer Satisfaction: Faster restocking led to better product availability resulting in fewer customer complaints.
Manufacturing Use Case
In a mid-sized manufacturing facility specializing in assembly line production, there was a pressing need to oversee components' inventory with precision. Outdated manual methods rendered the process slow and error-prone, contributing to production halts.
Project Scope:
- Implementation of handheld scanners integrated with manufacturers’ ERP system.
- Focus on employee training to familiarize them with the new technology.
The scanner system was implemented to track the movement of raw materials and finished goods along the production chain. With hand-held scanners, workers could now verify every stage of the manufacturing process manually. Access to updated data not only helped in maintaining inventory levels but also ensured efficient resource allocation.
Results Achieved:
- Manufacturing Efficiency: Production time improved by 25% due to better inventory tracking.
- Quality Control: Early detection of quality issues thanks to immediate feedback from scanner data.
- Employee Engagement: Increased accountability and satisfaction among employees as they became integral to the enhanced process workflow.
Closure
Understanding the role of handheld scanner inventory systems in today’s fast-paced market is paramount. This article has explored not just the mechanics behind these systems but also the wide array of benefits they bring to different industries. When you step back and look at the complete picture, it’s these systems that can transform the way organizations manage their resources. They simplify processes, cut down on errors that can stem from manual entry, and provide real-time insights that are invaluable in decision-making.
Summarizing Key Insights
To distill the essence of our discussion:
- Handheld scanners act as crucial tools in inventory management, reducing the labor needed for tracking and counting items.
- They integrate seamlessly with various software solutions, enabling smoother operations across different departments.
- The benefits extend beyond efficiency; cost-effectiveness and real-time data access are also significant advantages.
- Although there are challenges in implementation, the long-term gains in productivity and accuracy far outweigh the initial hurdles.
As businesses navigate recovery and growth phases, especially post-pandemic, reliance on precise inventory management will only intensify. Enhancing inventory systems with handheld scanners can provide a competitive edge.
Looking Ahead: Navigating the Future of Inventory Management
The future of inventory management is undeniably tied to technology. Innovations are happening at an astonishing rate, pushing the boundaries of what we thought possible. Key trends to be on the lookout for include:
- Advancements in Technology: As hardware improves, we’ll see scanners becoming faster and more capable, enabling them to handle a wider range of tasks.
- Integration with IoT: The Internet of Things is already influencing how devices interact. Imagine scanners that communicate directly with inventory management systems, automatically updating stock levels as goods move.
- Enhanced Data Analytics Capabilities: With big data's rise, the potential for deep insights into inventory trends is on the horizon. Businesses that leverage this can anticipate demand more accurately, optimizing operations ahead of time.
Those looking to implement or upgrade their systems must keep these developments in mind. Balance must be struck between adopting cutting-edge solutions and ensuring operational continuity. Remember: it’s not about using the latest tools but finding the right fit for your specific needs and circumstances.