Exploring Factory Track Software for Manufacturing Success
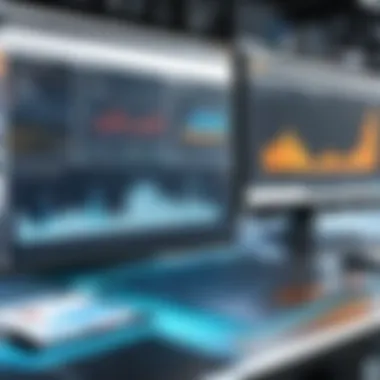
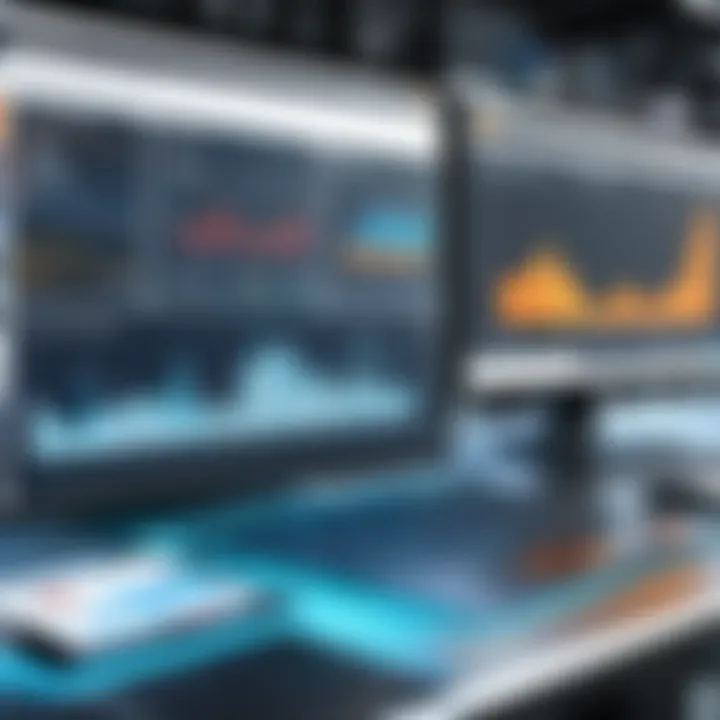
Intro
In today's manufacturing landscape, staying ahead of the curve requires more than just hard work and determination; it necessitates leveraging technology that can enhance operations. Factory track software stands at the forefront of this evolution, providing manufacturers with tools necessary to optimize their processes. As the saying goes, "Time is money," and in the manufacturing world, minutes can equate to significant financial implications. This discussion aims to highlight the essential components of factory track software, elucidating its core functionalities and the value it delivers.
Key Features and Functionalities
Factory track software is not just a luxury; it’s increasingly becoming a necessity for industries aiming for efficiency and precision. Understanding what these systems offer can greatly inform the decision-making process for those considering implementation.
Comprehensive Overview
At the heart of factory track software lies an array of features designed to streamline manufacturing operations. From inventory management to production scheduling, these systems can cover a wide range of functionalities. The ability to track equipment usage and gather real-time data is invaluable. Imagine a scenario where a machine breakdown interrupts production. With proper software, alerts can be generated immediately, minimizing downtime and ensuring a swift response. Here are some common features:
- Real-time Tracking: Monitors various aspects of production, ensuring optimal utilization of resources.
- Data Analytics: Accumulates data that provides insights into production efficiency, helping managers make informed decisions.
- Inventory Management: Automates stock tracking, which reduces waste and ensures that materials are available when needed.
- Integration Capabilities: Works smoothly with other existing systems, enhancing overall functionality and user experience.
Target Users
The spectrum of users for factory track software is broad and varied. On one hand, you have production managers who need to oversee operations, ensuring efficiency translates to output. On the other, IT professionals require robust systems to fit into a larger digital ecosystem. Entrepreneurs, particularly those in startup environments or established firms, also benefit from deploying these technologies effectively to optimize productivity. Each group's needs differ, illustrating the importance of customized solutions that can adapt to various manufacturing contexts.
Pricing Models and Cost Analysis
Considering the financial implications of software implementation is crucial. Not only does it involve upfront investment, but ongoing costs must also be taken into account.
Breakdown of Pricing Tiers
Factory track software typically follows tiered pricing models. This structure allows businesses to choose an option that best aligns with their size and operational needs. Smaller firms might opt for basic packages that cover essential features, while larger enterprises may seek enterprise-level solutions with more advanced capabilities.
- Basic Tier: Suitable for small to medium-sized operations, focusing on core functionalities such as inventory management and basic reporting.
- Pro Tier: Aimed at mid-sized firms that require enhanced analytics and real-time monitoring systems.
- Enterprise Tier: Comprehensive solutions designed for large organizations needing extensive customization and integration.
Additional Costs to Consider
Beyond the primary costs associated with purchasing software, there are several ancillary expenses worth noting.
- Training: Implementation may require staff training to ensure effective usage.
- Maintenance Fees: Continuous updates and maintenance can incur ongoing costs.
- Customization: Tailoring the software to meet specific operational needs can take additional time and money.
Investing in factory track software can drive significant returns in efficiency and productivity when each of these components is carefully weighed. Each decision made today has the potential to shape the future of manufacturing operations for years to come.
Preface to Factory Track Software
Factory track software has become a linchpin in the world of modern manufacturing. It plays a crucial role in how industries streamline their processes, manage their resources, and ultimately enhance their competitive edge. In an age where time is often likened to money, being able to track production accurately can make or break a business. This software serves not just as a tool but as an integral part of a manufacturer’s ecosystem, providing a bird's-eye view of operations from start to finish.
Definition and Purpose
At its core, factory track software is designed to monitor and optimize the manufacturing process. This involves everything from tracking inventory levels to scheduling production runs and managing labor resources. Think of it as the nervous system of a factory: it sends signals, collects data, and responds to various stimuli, helping decision-makers stay informed and proactive.
Businesses leverage this technology for several key purposes:
- Efficiency: By automating routine tasks, organizations can devote their human resources to more strategic initiatives.
- Visibility: Real-time tracking provides a clear view of production status, allowing managers to make informed decisions promptly.
- Accountability: Every component in the process can be traced, which helps in identifying bottlenecks or issues when they arise.
Simply put, without effective tracking software, manufacturing operations can be as chaotic as a bull in a china shop. The software organizes operations, ensuring that everything runs smoothly and efficiently.
The Evolution of Factory Tracking
The journey of factory tracking begins long before the advent of sophisticated software. Initially, factories relied heavily on manual processes that were prone to error and inefficiency. Think about it: back in the day, tracking inventory was often done with nothing more than a pen and paper, leading to discrepancies and frustrations.
As technology advanced, so did the methods for tracking manufacturing processes.
- Initial Changes: The introduction of barcodes and scanners was revolutionary in the late 20th century. It allowed for quicker data acquisition, though it still involved much manual labor.
- The Digital Shift: The rise of computers and digital databases facilitated a more sophisticated approach, where inventory could be tracked digitally, offering better accuracy.
- Modern Solutions: Today, factory track software incorporates features like IoT (Internet of Things) sensors that automatically update data in real-time, allowing businesses to react almost instantaneously to changes in the production line.
This evolution demonstrates a clear trend toward increased efficiency and integration. The tools that once seemed futuristic are now standard practice, and companies that lag in adopting such technology find themselves at a distinct disadvantage.
"The past informs the future, and the evolution of factory tracking is no exception; it showcases how technology transforms challenges into solutions."
For decision-makers, understanding the evolution of factory tracking is vital for grasping its current capabilities and potential. As the landscape continues to change, remaining at the forefront of innovation becomes a necessity, not just an option.
Core Features of Factory Track Software
The landscape of manufacturing is undergoing unprecedented change, and Factory Track Software is at the heart of this transformation. Its core features not only streamline operations but also play the pivotal role of ensuring businesses can effectively adapt to fluctuating market demands. Investors and decision-makers need to grasp these key functionalities to harness their full potential. Let’s delve into these essential components that make Factory Track Software vital for today’s industrial environment.
Real-Time Inventory Management
In the manufacturing game, having a finger on the pulse of inventory can mean the difference between success and a costly halt. Real-time inventory management is like having a hawk's eye on stock levels, ensuring that every component is tracked as it moves from the warehouse to the production line and beyond. This feature drastically reduces the chances of overstocking or stockouts, optimizing resources.
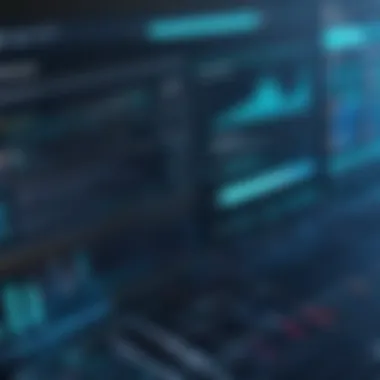
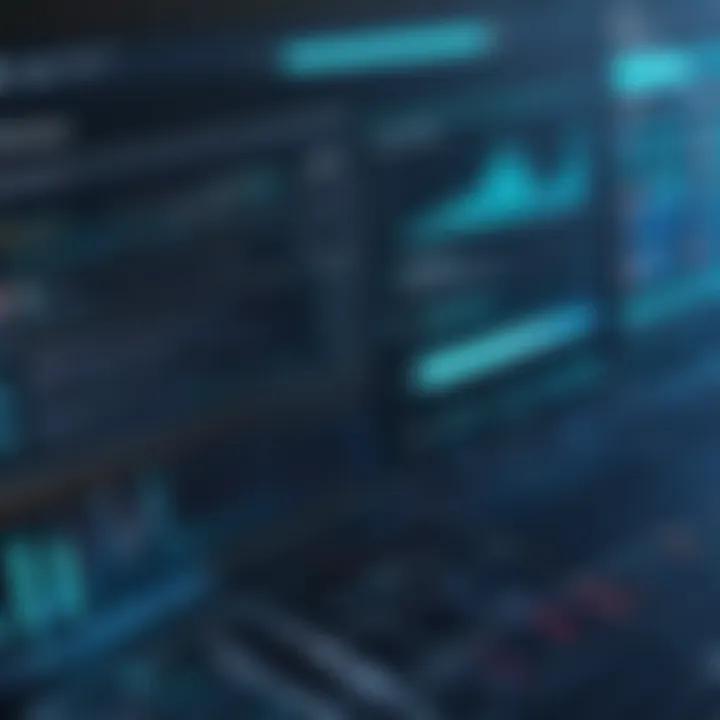
With a well-implemented system:
- Decision-makers can adjust orders on-the-fly.
- Supply chain disruptions can be managed swiftly.
- Accuracy improves, leading to better financial forecasts and reduced waste.
Organizations utilizing real-time tracking often report higher customer satisfaction levels, as they can deliver products without delays. Manufacturers facing tight deadlines find this feature particularly advantageous, as it assists in maintaining workflow without compromises.
Production Scheduling and Planning
Picture a symphony orchestra. Each musician must play their part at the right time to create harmony. Similarly, production scheduling aligns different processes within a factory, ensuring that everything operates seamlessly. Factories employing these sophisticated scheduling tools can confidence tackle the nuances of variable production rates and machine maintenance periods.
Important aspects include:
- Optimized utilization of machines: Knowing when to run which machine at peak efficiency saves money.
- Flexibility in production runs: Changes in demand can be swiftly addressed, adjusting schedules to reduce downtime.
- Capacity planning: Aligning production output with demand forecasts can prevent bottlenecks, ensuring optimal flow.
By embracing smart scheduling, production managers can navigate complexities with ease, enabling them to meet customer expectations while enhancing operational efficiency.
Workflow and Task Management
Implementing factory track software goes beyond just inventory and production speed. Workflow and task management can reshape how teams operate day-to-day. This feature breaks down the workflow into manageable tasks, assigning responsibilities without chaos ensuing.
Consider the benefits:
- Clarity in roles prevents overlap and confusion.
- Efficient task assignment means that employees can work on priorities rather than getting lost in the shuffle.
- Progress tracking ensures that targets are met consistently.
"A project timeline is only as good as the ability to stick to it. Workflow management is the backbone that supports delivery."
Therefore, companies focused on improved task management often see significant enhancements in productivity, leading to quicker turnaround times and ultimately, improved profit margins.
Data Analytics and Reporting
In today's data-driven world, insights derived from production processes are invaluable. Data analytics and reporting empower manufacturers to understand patterns in their operations, thus supporting informed decision-making.
Benefits of this feature include:
- Trend identification: Analyzing historical data reveals inefficiencies that need addressing.
- Actionable insights: Real-time dashboards can show where attention is needed immediately.
- Performance metrics: Track KPIs to align operational strategies with business goals.
With a robust analytics framework, organizations can pivot strategies based on evidence rather than intuition. This accuracy not only refines processes but also aligns closely with customer needs and market trends. Companies are able to forecast production needs more effectively by understanding the ebb and flow of their operations, which ultimately protects the bottom line.
Benefits of Implementing Factory Track Software
In the ever-evolving landscape of manufacturing, factory track software emerges as a key player in enhancing operational efficiencies and driving productivity. Its implementation can significantly alter how businesses approach manufacturing processes. This section delves into the tangible advantages of these tools, shedding light on their profound impact on day-to-day activities and long-term outcomes.
Enhanced Productivity
The primary advantage that comes bundled with factory track software is enhanced productivity. With real-time data access, operators no longer have to rely on anecdotal evidence or guesswork. This software enables better resource allocation, ensuring that the right materials and labor are in the right place at the right time. According to a study published on britannica.com, companies that have integrated such technologies report efficiency increases of up to 30%.
Enhanced productivity also arises from automated processes that reduce manual interventions. Workers can channel their energies from repetitive tasks to activities that require critical thinking or creativity. A case in point involves a manufacturing firm that integrated factory tracking solutions and subsequently observed a marked decrease in product lead times by nearly 20%. When production bottlenecks are mitigated effectively, overall throughput skyrockets, leading to a healthier bottom line.
"The secret to success in manufacturing lies in leveraging smart technologies to streamline operations."
— Industry Expert
Improved Accuracy in Operations
When it comes to manufacturing, accuracy is non-negotiable. Factory track software plays a pivotal role in reducing errors that can arise from manual data entry or miscommunication among teams. Often, mistakes can snowball into significant issues, potentially costing both time and money. The software ensures that information flows seamlessly across different departments, from inventory management to order fulfillment.
With precise tracking of materials and processes, companies gain insights that foster better decision-making. For instance, if an organization uses barcodes or RFID tags, they can keep tabs on inventory levels in real-time. This eliminates the risk of stockouts or overstock situations. Imagine a business that regularly experiences discrepancies in inventory counts; implementing this software can cut those inaccuracies by half, as several reports and testimonials corroborate.
Cost Reduction Over Time
Cost-saving is often the golden carrot that tempts many businesses into adopting new technologies. The truth is, once set up correctly, factory track software can lead to substantial reductions in operational costs. While the initial investment may seem hefty, the long-term savings can easily outweigh the early expenditures.
Such systems can curtail wastage through proactive inventory management. By ensuring that materials are ordered and utilized efficiently, businesses can minimize excess spending on raw materials. Additionally, by reducing downtime through better scheduling and workflow management, companies can maximize their existing resources.
Several firms have reported a reduction in operational costs by as much as 25% within the first year of implementing these solutions. Moreover, an intelligent system can adapt and evolve with the business, continuously identifying areas for cost savings. This allows for a more sustainable business model that empowers growth without unnecessary expenditures.
Challenges in Adopting Factory Track Software
Implementing factory track software isn't all sunshine and rainbows. While the potential benefits of enhancing efficiency and boosting productivity are enticing, there are substantial roadblocks that organizations often encounter along the way. Understanding these challenges is paramount, as it can provide invaluable insights for decision-makers and stakeholders. By addressing these difficulties head-on, businesses can navigate the tricky waters of software adoption with greater ease.
Implementation Costs
When it comes to factory track software, the initial financial outlay can feel like a hefty chunk taken out of the budget. Many decision-makers are faced with the daunting task of justifying these costs against potential long-term savings. The costs aren't just about the software itself; additional expenses may include:
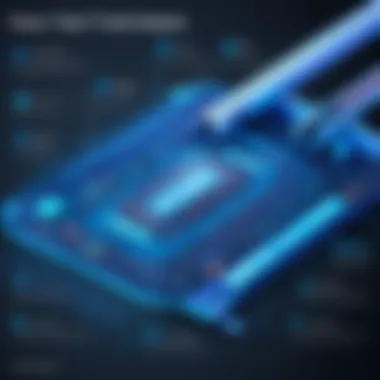
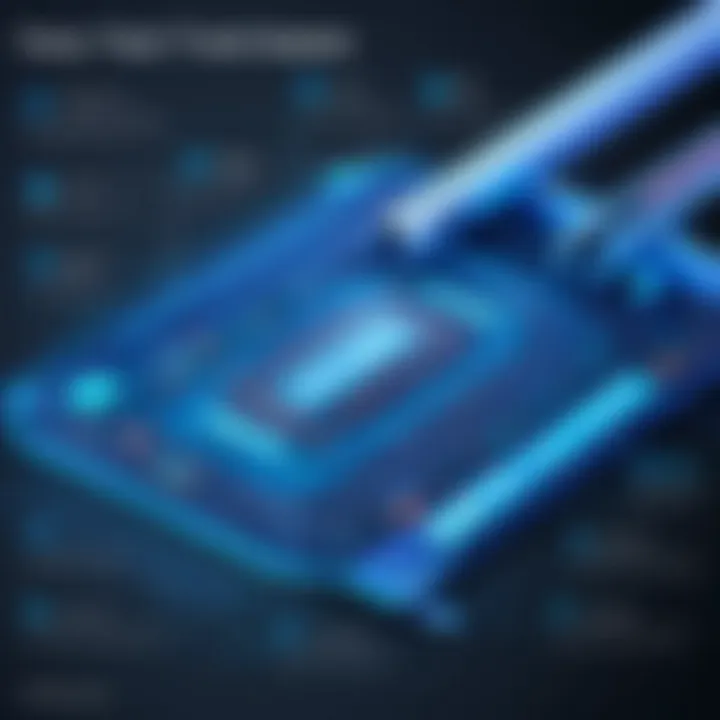
- Training: Ensuring that staff members are well-versed in operating the new system can take time and resources. This may mean investing in training programs or hiring consultants.
- Hardware Upgrades: Existing systems might require updates or replacements to fully integrate with the new software, further escalating costs.
- Ongoing Maintenance: Keeping the software running smoothly isn't a one-and-done situation; regular updates, troubleshooting, and maintenance can add to the financial commitment.
As the saying goes, "You have to spend money to make money," but making these expenses easier to manage is crucial for successful implementation.
Resistance to Change Within Organizations
Companies don’t just poof into new software like a magician's trick; there tends to be a natural skepticism when it comes to new ways of doing things. Staff members often get comfortable in their routines. New software can feel like trying to teach an old dog new tricks. Change can bring about anxiety, particularly if:
- Fear of Uncertainty: Employees may doubt whether the new system will actually simplify their workloads or if it’ll add more processes instead.
- Loss of Control: The introduction of software that automates certain functions may lead to feelings of displacement, causing resistance from those who fear job security.
- Cultural Barriers: Some organizations have a specific culture rooted in traditions that may conflict with the necessity of adopting modern technologies.
Overcoming resistance isn't merely a matter of announcing change. It often requires strategic communication, involving explaining the benefits, showcasing successful implementations, and offering support throughout the transition.
Integration with Existing Systems
One cannot simply throw a new tool into a toolkit filled with mismatched pieces; everything needs to fit together seamlessly. Integrating factory track software with existing systems can pose a formidable challenge. Many organizations run on legacy systems that lack compatibility with modern applications. The importance of this integration cannot be understated:
- Data Flow: Ensuring that all systems can communicate effectively to guarantee accurate and timely data flow is crucial for overall efficiency.
- Operational Disruptions: Poor integration can cause interruptions in daily operations, leading to frustration among employees and potential loss of revenue.
- Technical Challenges: Organizations may face hefty technical hurdles requiring significant investment in IT expertise to solve problems arising during integration.
To wrap up, avoiding the pitfalls in the adoption process comes down to a well-thought-out plan.
"Success is where preparation and opportunity meet."
Addressing costs, smoothing out resistance, and ensuring compatibility with existing systems will make the transition much more manageable, setting the stage for successful factory track software integration.
Criteria for Selecting Factory Track Software
Selecting the right factory track software is a critical step for any organization aiming to revamp its manufacturing operations. This choice can significantly influence productivity, accuracy, and ultimately, the bottom line of the business. In today's competitive landscape, the requirements differ vastly across industries, making tailored solutions essential. Hence, understanding the criteria for selecting the appropriate software is paramount.
Assessing Specific Business Needs
Before even considering options in the market, organizations must critically assess their own unique operational requirements. This involves looking at:
- Production Volume: How many units are typically produced? Larger volumes may necessitate more sophisticated tracking tools.
- Product Complexity: Do the products have intricate assembly processes? If so, software must accommodate intricate instructions and keep track of multiple components.
- Data Requirements: What type of data needs tracking? Determining whether simple inventory counts suffices or if detailed analytics on throughput is essential can shape the choice.
Gauging these needs will help organizations to narrow down options more effectively and ensure the ultimate software aligns with overarching business goals.
Evaluating Software Features
Once the specific needs are identified, it’s time to take a closer look at the features offered by different software solutions. Not all factory track software is created equal, and certain features can make a world of difference. Consider the following key functionalities:
- Real-Time Tracking: The ability to monitor the status of inventory and production in real-time is invaluable. This provides organizations a clearer picture for decision-making.
- Integration Capabilities: The software should seamlessly integrate with existing systems, such as ERPs or inventory management tools, to provide a unified view of operations.
- Reporting Tools: Robust reporting features that allow for data manipulation and generating insights can help in strategic planning.
The right mix of features can provide a competitive edge, enabling not just day-to-day operations, but also long-term strategic benefits.
User Experience and Interface Design
The usability of factory track software shouldn't be overstated. Software with a convoluted interface can lead to inefficiencies and worker frustration. A good user experience encompasses:
- Intuitive Navigation: Users should be able to navigate through the software without requiring extensive training.
- Customizability: Since every factory has its own workflow, the ability to customize dashboards and reports can elevate user satisfaction and productivity.
- Mobile Accessibility: In an era where remote work and mobile capabilities are paramount, software should allow access from various devices, enhancing flexibility.
A friendly interface can lead to faster adoption rates and less downtime during the implementation phase, ensuring projects stay on track.
Vendor Support and Community Resources
The choice of vendor can be as crucial as the software's features. A company offering enduring support and resources can have an outsized impact on the successful implementation of the software. Consider:
- Availability of Support Channels: Is support available through various channels such as chats, emails, and phone? Responsive support can be a lifesaver.
- Training Resources: Does the vendor provide adequate training materials? Videos, manuals, and user tutorials can empower teams to use the software effectively.
- Community Engagement: Platforms like forums or social media groups can connect users, fostering a community for troubleshooting and sharing best practices.
Choosing a vendor that prioritizes customer engagement can alleviate many headaches during and after implementation.
Ultimately, finding the right factory track software isn't just about features; it’s about aligning with business goals, offering a superior user experience, and ensuring strong vendor support.
Case Studies: Successful Implementations
The significance of featuring case studies in the context of factory track software cannot be understated. These examples serve as tangible demonstrations of how the software has been implemented across various industries, showcasing the myriad ways it can enhance operational efficiency and productivity. Understanding these real-world applications offers decision-makers, IT professionals, and entrepreneurs a roadmap to navigate their own implementations effectively.
Manufacturing Sector Innovations
In the realm of manufacturing, factory track software has catalyzed innovations that have shifted paradigms and improved efficiency. For instance, consider the case of Siemens, a leader that implemented a robust factory tracking system to orchestrate their production lines. With integration of real-time data analytics, Siemens was able to identify bottlenecks and inefficiencies promptly. This allowed for immediate corrective actions, resulting in a 20% reduction in lead time and a 15% increase in overall production capacity.
Another noteworthy example comes from Boeing, which utilized factory track software in its assembly lines to achieve real-time status of components and materials. The visibility afforded by this software played a crucial role in streamlining their supply chain operations. By aligning their production schedules with inventory levels, they were able to enhance forecasting accuracy and minimize downtime. Such improvements underscore the importance of data-driven decision-making in manufacturing sector innovations.
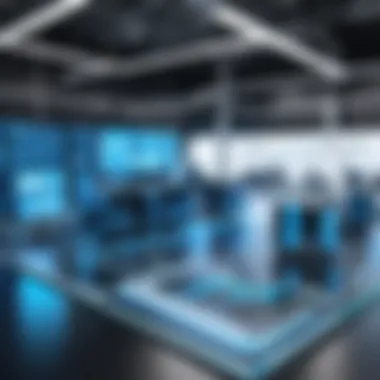
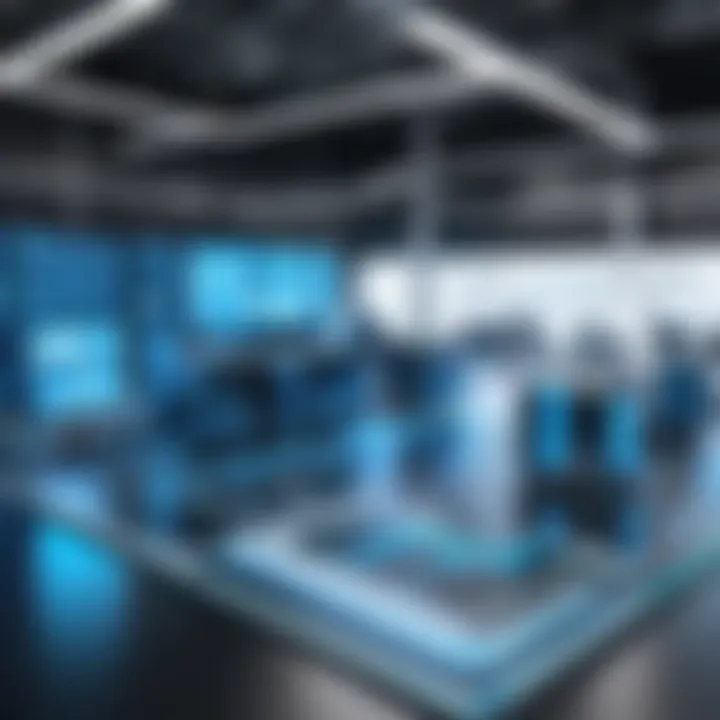
Impact on Small to Medium Enterprises
While larger corporations often dominate discussions about technology adoption, small to medium enterprises (SMEs) have also enjoyed significant benefits from factory track software. A case worth mentioning is that of Miller's Bakery, a mid-sized company that incorporated factory tracking solutions to manage their production workflow. Before this undertaking, Baker’s struggles with maintaining accurate inventory led to excess waste and customer dissatisfaction. With the implementation of this software, they made a remarkable turnaround.
By automating their inventory management and production scheduling, Miller's Bakery reduced excess waste by 30%, improving their profit margins. The software provided them not just with metrics, but actionable insights that empowered them to make informed decisions swiftly. Therefore, this case illuminates how SMEs can leverage technology to not only enhance operational efficiency but also respond better to market demands.
Lessons Learned from Failures
Not all stories of adopting factory track software carry a golden hue—some ended on a sour note, teaching valuable lessons. General Motors faced notable challenges during their integration of a new factory tracking system a few years back. Many employees resisted the change, which stemmed from a lack of adequate training and insufficient communication from leadership. The initial rollout failed to achieve the anticipated efficiency gains due to these hurdles, and it resulted in increased production delays.
However, this experience opened the door for introspective assessments. General Motors re-evaluated its change management strategy, leading to the conclusion that thorough training and emphasizing the benefits were essential for successful implementation. By adopting a more structured approach—investing in ongoing training sessions and creating a direct feedback loop—the company eventually rectified its initial mistakes.
This example emphasizes that the introduction of new technology must be accompanied by human-centered strategies. Failure to do so can lead to missed opportunities and investment losses.
"In technology adoption, correlation does not guarantee causation. The human element involved is the key to truly reaping the benefits in implementing innovations."
Through these case studies, it becomes clear that factory track software can significantly impact modern manufacturing settings, regardless of size. The lessons learned not only highlight the practical aspects of introductory changes but also serve as guiding principles for smoother transitions and successful implementations.
Future Trends in Factory Track Software
The landscape of factory tracking software is in a constant state of transformation, influenced by technological advancements and changing industry demands. As we gaze into the future, it’s paramount for decision-makers, IT professionals, and entrepreneurs alike to be attuned to these emerging trends. These developments not only shape how factories operate but also determine their competitiveness in an increasingly complex global market. To stay ahead of the curve, understanding deep-rooted changes like artificial intelligence, Internet of Things integration, and the push towards sustainability is critical.
Artificial Intelligence and Automation
Artificial Intelligence (AI) is not merely a buzzword; it’s becoming a cornerstone of modern factory tracking software. By harnessing AI, manufacturers can automate routine processes, thus freeing up human resources for more strategic efforts. For instance, predictive analytics can forecast production bottlenecks before they occur, enabling managers to nip issues in the bud and streamline operations.
Moreover, AI-driven algorithms can analyze vast amounts of data to identify inefficiencies. This leads to smarter decision-making based on real-time insights. Manufacturers that adopt AI are likely to see enhanced accuracy in their operations, reducing errors and ultimately lowering costs. As one expert put it:
"Without AI, factories are basically running with one hand tied behind their back."
Incorporating automation not only speeds up production schedules but also improves employee safety. Robots can handle hazardous materials while human employees focus on more intricate tasks. This not only promotes a safer working environment but also retains human creativity and problem-solving where it’s needed.
Integration with IoT Technologies
The integration of IoT (Internet of Things) technologies is another trend gaining momentum in factory track software. Sensors and smart devices can collect and disseminate data in real-time, creating a seamless flow of information across operations. This connectivity not only streamlines monitoring but also enhances reliability.
For example, a factory equipped with IoT devices can monitor machinery conditions continuously. If an anomaly is detected, maintenance can be scheduled before an expensive breakdown occurs. By turning data into actionable insights, organizations can make more informed decisions that positively impact their bottom line.
The symbiosis between IoT and factory track software can facilitate remote monitoring and management, essential for firms that operate multiple locations. This integration paves the way for what some experts are calling "smart manufacturing," where machines communicate with one another to optimize production lines.
Sustainability and Efficiency Initiatives
Sustainability isn’t simply a corporate responsibility; it is increasingly becoming a business imperative. As environmental concerns gain traction, factory track software is evolving to embrace greener practices. Companies are recognizing that efficiency and sustainability go hand in hand.
By implementing effective tracking systems, manufacturers can minimize waste and enhance resource efficiency. For instance, software that can track material usage allows firms to identify surplus inventory and implement just-in-time strategies, significantly reducing waste.
Furthermore, sustainability initiatives can lead to cost savings in the long run. Energy-efficient processes are not only acceptable socially but also financially advantageous. Emphasizing green approaches can improve a company's image, making it more attractive to environmentally conscious consumers.
As these trends unfold, manufacturers must seek solutions that not only meet current operational needs but also anticipate future requirements. Staying attuned to these developments can make a notable difference in a manufacturer’s ability to adapt and thrive in an evolving market.
Culmination: The Role of Factory Track Software in Modern Manufacturing
The landscape of modern manufacturing pivots significantly on the efficacies introduced by factory track software. This technology stands as a cornerstone that shapes how operations are streamlined, resources are managed, and production is enhanced. Implementing such software changes not just the workflow, but the overall environment within manufacturing facilities, leading to heightened productivity and better resource allocation.
One key element highlighted throughout this article is the remarkable capability of factory track software to deliver real-time data. Decision-makers can utilize this information to make informed choices, ensuring that operations are as efficient as possible. The consequences of having accurate, instant insights into inventory levels, production schedules, and workforce capabilities cannot be overstated.
Furthermore, embracing this technology enhances transparency within the production process. With clear visibility into each stage of manufacturing, organizations can identify bottlenecks swiftly and apply corrective measures as the situation unfolds. This level of oversight cultivates an atmosphere where continuous improvement is both favored and easily achievable.
Benefits of Factory Track Software
- Enhanced Productivity: Significantly reduces downtime by allowing for quick adjustments based on real-time insights.
- Cost-Effective Solutions: Over time, these systems reduce waste and improve resource management.
- Employee Engagement: By streamlining tasks and clarifying responsibilities, staff morale can improve, as they appreciate a more organized environment.
The considerations brought forth in this discussion illustrate that manufacturers are not just investing in software. They are investing in a mindset that embraces innovation and accuracy. As organizations continually seek to improve their produciton processes, the adoption of factory track software emerges as a fundamental step towards achieving competitive advantage in the market.
Summarizing Key Insights
In summary, this article has elaborated on several pivotal themes regarding factory track software. First and foremost, the necessity for modern manufacturing solutions is underscored by their ability to manage complexities associated with production. The discussions on core features range from real-time inventory management to advanced data analytics, which have the potential to revolutionize how facilities operate. Each aspect outlined contributes uniquely to the ecosystem of manufacturing, creating a synergy that enhances overall output.
Moreover, the challenges facing the adoption of such technologies are not to be overlooked. From initial implementation costs to cultural pushbacks within organizations, the journey requires careful navigation and alignment of goals. Nonetheless, despite these hurdles, the long-term benefits often outweigh initial reluctances, making the case for factory track software compelling.
Final Thoughts for Buyers
For buyers contemplating the switch or integration of factory track software, the decision should be approached with thorough assessment. Start by evaluating specific business needs and the existing technological landscape—what works today, and how can new solutions complement it? Additionally, one must consider the user experience and interface design; software that is intuitive will see better buy-in from employees.
Engage with vendors and look for insights into their support capabilities. A strong vendor relationship can greatly affect the success of your implementation. Have reasonable expectations about timelines and potential disruptions during the transition phase.
As you digest this information, bear in mind the constant evolution of the manufacturing sector. Staying ahead means being prepared for changes—whether they come from advancements in AI, adaptations to sustainability practices, or integrations with IoT technologies. Choosing the right factory track software today positions your organization for resilience and adaptability in the future.