AWS IoT Predictive Maintenance for Asset Management
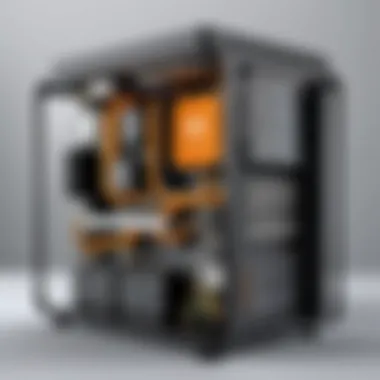
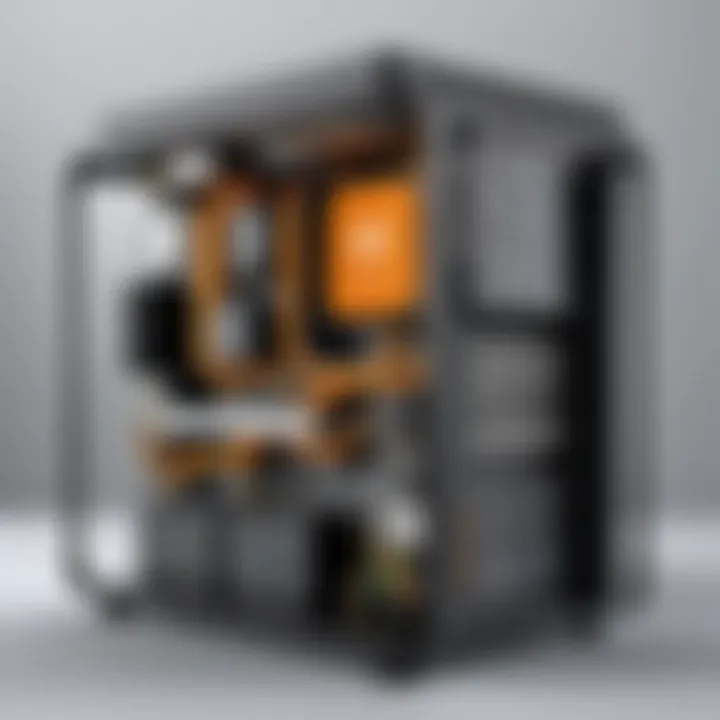
Intro
In a world where technological advancements occur at an unprecedented pace, industries face immense challenges in asset management and maintenance. AWS IoT stands out as a transformative solution for predictive maintenance, offering organizations the ability to leverage data analytics and machine learning for enhanced operational efficiency. This article delves into the pivotal role that AWS IoT plays in predictive maintenance, exploring its key features, functionalities, and practical applications across various sectors.
As companies increasingly rely on connected devices, the significance of real-time data cannot be overstated. Predictive maintenance powered by AWS IoT not only minimizes downtime but also fosters a proactive approach to asset management. By optimizing maintenance schedules, organizations can reduce operational costs and extend the lifespan of critical assets.
The journey through this article will cover a comprehensive overview of AWS IoTβs framework, its capabilities in generating insightful data, and the integration of machine learning into predictive maintenance strategies. Furthermore, we will analyze real-world case studies to demonstrate the effectiveness of these technologies, address potential challenges, and highlight future trends in this evolving arena.
The intended audience includes decision-makers, IT professionals, and entrepreneurs, all of whom can benefit from understanding the impact of AWS IoT in reshaping predictive maintenance and asset management.
Preface to AWS IoT
The realm of the Internet of Things (IoT) is transforming industries by connecting devices and enabling seamless communication. AWS IoT is at the forefront of this revolution, offering a robust platform to manage the multitude of devices in an interconnected ecosystem. This section delves into the definition of AWS IoT and its significance in various industrial applications, laying the groundwork for understanding its role in predictive maintenance.
Definition of AWS IoT
AWS IoT, or Amazon Web Services Internet of Things, is a service that facilitates the connection of IoT devices to the cloud. This service allows devices to collect data, share information, and communicate with each other and backend systems efficiently. Leveraging AWS IoT, companies can create applications that monitor, control, and secure their IoT devices. The platform supports a range of protocols, ensuring compatibility with different devices.
Moreover, AWS IoT services include AWS IoT Core, AWS IoT Analytics, and AWS IoT Greengrass, each serving distinct purposes. For instance, AWS IoT Core connects devices securely and enables data processing in real-time, while AWS IoT Analytics provides tools to analyze the data generated from these devices effectively.
Importance of IoT in Industrial Applications
The infusion of IoT in industrial settings is paramount. This technology enhances operational efficiency, drives innovation, and facilitates real-time decision making. With IoT, organizations can gather insights from machinery, monitor performance, and predict equipment failures before they occur. Some key benefits include:
- Reduced Downtime: Through continuous monitoring and early fault detection, AWS IoT minimizes equipment failures.
- Cost Savings: Predictive analytics enable organizations to optimize maintenance schedules, saving on unnecessary repairs and downtime costs.
- Data-Driven Decisions: The ability to process vast amounts of data in real time allows companies to make informed decisions on resource allocation and operational adjustments.
"Implementing IoT solutions can result in significant improvements in productivity and efficiency for industries."
Concept of Predictive Maintenance
Predictive maintenance is a crucial concept for modern industries, representing a shift from traditional methods that often rely on scheduled maintenance. In an era where downtime can lead to significant financial losses, predictive maintenance offers a proactive approach. It not only helps in minimalizing the operational risks but also enhances the overall efficiency of asset management. This section is essential as it lays the groundwork for understanding how AWS IoT can refine maintenance strategies.
Understanding Predictive Maintenance
Predictive maintenance is an intelligent strategy designed to anticipate equipment failures before they occur. By using data from various sensors, maintenance teams can identify patterns that indicate potential issues. This proactive approach allows for repairs or replacements to be scheduled at optimal times, rather than reacting to failures. The key element is the integration of data-driven insights. With the right data, organizations can tailor their maintenance activities to specific asset conditions, therefore reducing unexpected downtime and maintenance costs.
Moreover, predictive maintenance emphasizes the importance of continuous monitoring. It requires a combination of hardware, software, and analytical processes. By continuously collecting data, organizations can develop a better understanding of their equipment's health, which ultimately leads to improved decision-making. This is especially significant in sectors where equipment reliability is critical, like manufacturing, energy, and transportation.
Comparison with Traditional Maintenance Approaches
Traditional maintenance approaches generally fall into two categories: reactive and preventive maintenance. Reactive maintenance is performed after a failure occurs; it's often a costly and inefficient way to manage assets. Preventive maintenance, on the other hand, is scheduled based on time intervals or usage metrics. While this can help reduce failures, it does not account for real-time asset conditions.
In contrast, predictive maintenance leverages real-time data to perform maintenance only when necessary. This method provides several benefits over traditional approaches:
- Cost Efficiency: By reducing unplanned downtime and optimizing maintenance schedules, companies can save significantly on costs associated with repairs and lost productivity.
- Resource Optimization: Maintenance resources are allocated more effectively, as technicians are called to action only when needed.
- Improved Equipment Lifespan: Regular monitoring and timely interventions can extend the lifespan of equipment, thereby maximizing the return on investment.
- Data Utilization: Predictive maintenance utilizes historical and real-time data, turning raw data into actionable insights that enhance operational decision-making.
In summary, the concept of predictive maintenance is vital for understanding the transformative potential of AWS IoT in asset management. By embracing predictive strategies, organizations can elevate their operational practices and become more resilient in an unpredictable environment. The shift from traditional maintenance approaches signifies a landmark change in managing assets with greater precision and foresight.
Why AWS IoT for Predictive Maintenance
The implementation of predictive maintenance using AWS IoT is increasingly critical for modern industries. This shift is driven by the need to optimize asset management and improve operational efficiency. Above all, AWS IoT provides tools and services to harness data effectively from interconnected devices. This capability facilitates better decision-making, ultimately leading to reduced downtime and operational costs.
Integration of AWS IoT with Predictive Maintenance
Integrating AWS IoT into predictive maintenance strategies involves utilizing its ecosystem to gather, analyze, and manage vast amounts of data from various sources. This integration streamlines processes and enhances the accuracy of maintenance predictions.
Key components in this integration include:
- Real-time Data Collection: AWS IoT enables devices to send data to the cloud in real-time. This allows for ongoing monitoring of equipment performance and immediate identification of potential issues.
- Data Processing: The robust processing capabilities of AWS help in storing and analyzing this data efficiently. Services like AWS Lambda and AWS Glue can automate workflows, preparing data for analysis without extensive manual intervention.
- Machine Learning Capabilities: AWS offers various machine learning tools such as Amazon SageMaker, which can be used to develop predictive models tailored to specific maintenance needs. By analyzing historical data patterns, these models can foresee equipment failures, enabling timely interventions.
This well-rounded integration ensures that organizations stay ahead of potential failures, significantly improving their maintenance schedules and reducing costs associated with unexpected breakdowns.
Scalability of AWS IoT Solutions
The scalability of AWS IoT solutions is another significant factor that makes it suitable for predictive maintenance. Industries, regardless of size, need systems that can grow with them. AWS solutions provide this flexibility by allowing organizations to scale their IoT infrastructure based on their evolving needs.
Several aspects highlight the scalability benefits:
- On-Demand Resources: AWS operates on a pay-as-you-go model, which allows organizations to allocate resources as needed. Companies can expand their IoT deployment without the worry of upfront costs, making it financially viable to adopt advanced technologies.
- Global Reach: With cloud infrastructure across multiple regions, AWS IoT offers reliable connectivity and performance for devices situated anywhere in the world. This global presence supports multinational organizations seeking a cohesive solution for their predictive maintenance processes.
- Adaptability to New Technologies: As IoT technologies evolve, AWS continuously updates its services, ensuring clients can easily incorporate new tools. This adaptability promotes innovation, allowing businesses to leverage the latest advancements in predictive maintenance.
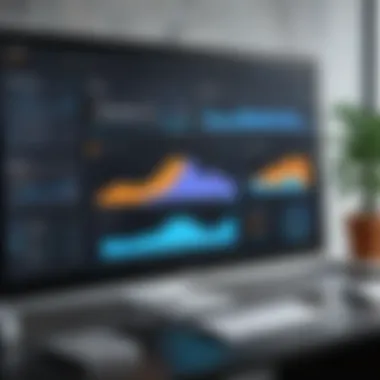
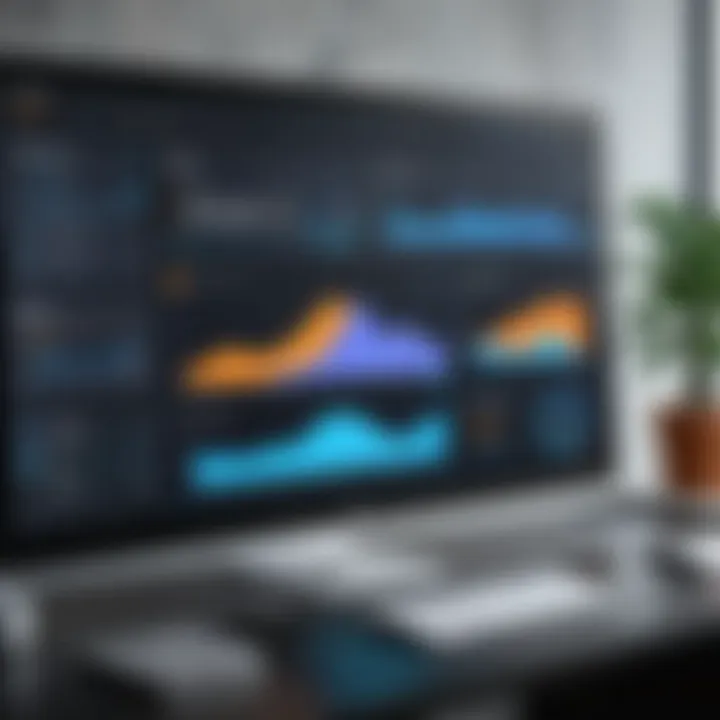
In summary, choosing AWS IoT for predictive maintenance not only enhances operational efficiency but also provides the flexibility needed to adapt to changing business landscapes. The seamless integration and scalability of AWS solutions empower companies to stay competitive in a fast-paced market.
Technical Framework of AWS IoT
Understanding the technical framework of AWS IoT is critical to grasping how predictive maintenance can transform asset management. This framework serves as the backbone for building IoT applications, enabling devices to connect, collect data, and leverage the power of cloud computing. Key elements within this framework include device management, connectivity, and data processing capabilities.
By providing a comprehensive architecture, AWS IoT facilitates seamless integration and interoperability between devices. This enables businesses to develop real-time monitoring systems, driving operational efficiency in diverse industries.
Core Components of AWS IoT
The core components of AWS IoT define how devices connect and communicate within the ecosystem. They include:
- AWS IoT Core: This service allows connected devices to communicate with each other and the cloud securely.
- AWS IoT Greengrass: This component extends AWS services to devices so they can act locally on the data they generate.
- AWS IoT Analytics: This service is vital for preparing and analyzing data from your IoT apps, which is crucial for predictive maintenance.
- AWS Lambda: A serverless computing service that runs code in response to events, minimizing management overhead.
Each of these components plays a significant role in ensuring that data generated from devices is processed efficiently, enabling timely insights and actions. The seamless integration of these components allows for scalable and flexible solutions tailored to organizational needs.
Data Collection Methods
Data collection is central to predictive maintenance, as it underpins the analytics and insights derived from devices. AWS IoT provides multiple methods of data collection to ensure comprehensive monitoring.
1. Device Data Generation: Devices equipped with sensors generate real-time data regarding operation conditionsβtemperature, pressure, etc. This raw data is the foundation for further analysis.
2. Message Queuing: AWS IoT utilizes protocols like MQTT and HTTPS for data transmission. This enables lightweight communication, suitable for IoT devices with limited resources.
3. Data Streaming: Streams enable continuous data flow from devices to the cloud for real-time processing. Using AWS Kinesis, businesses can handle large volumes of streaming data without latency.
4. Batch Data Processing: Certain scenarios require collecting data over a period before analysis. This batch method helps in managing costs while still offering valuable insights.
"The strength of predictive maintenance lies in its ability to anticipate failures before they occur, leading to significant improvements in operational efficiency."
By understanding these elements, decision-makers can leverage the full potential of AWS IoT to optimize their maintenance workflows and drive significant cost reductions.
Data Analytics in Predictive Maintenance
Data analytics plays a pivotal role in predictive maintenance. As industries adopt sophisticated IoT systems, the need for precise data collection and analysis becomes more critical. This ensures timely insights that can lead to proactive decision-making regarding asset management. Through the utilization of advanced analytics, organizations can transform raw data into actionable insights, ultimately enhancing operational efficiencies.
Predictive maintenance relies heavily on data analytics to foresee potential equipment failures before they occur. By analyzing data patterns, organizations can determine when maintenance should occur. This is a shift from traditional reactive maintenance strategies, which often lead to unexpected downtimes and increased costs.
Role of Data Analytics
Data analytics serves as the backbone of predictive maintenance initiatives. It enables organizations to digest vast amounts of data collected from various sensors and devices deployed on their equipment. By employing statistical analysis and machine learning algorithms, companies can identify trends and anomalies that signify potential maintenance needs.
Furthermore, data analytics helps in:
- Identifying failure patterns: Organizations can track historical performance data to detect markers that often precede equipment failures.
- Optimizing maintenance schedules: By understanding usage patterns, companies can create maintenance schedules that minimize downtime and extend equipment life.
- Reducing costs: Efficient data analysis can lead to significant savings by preventing over-maintenance and reducing emergency repairs.
Analysts usually utilize tools that can handle big data efficiently, ensuring that insights are derived quickly and accurately. This can include platform solutions like AWS Redshift or Apache Spark, both of which provide scalable solutions for data analysis.
Types of Data Analyzed
In predictive maintenance, various types of data are collected and analyzed to ensure a comprehensive understanding of asset health. This data can be categorized into the following types:
- Operational Data: This includes data on how equipment is functioning in real-time. Parameters could involve temperature, pressure, and vibration levels.
- Historical Data: Historical maintenance records provide context on past issues and repairs. Analyzing this data can reveal patterns and recurring problems.
- Environmental Data: Factors such as humidity or temperature can significantly impact equipment performance. This data can help contextualize operational metrics.
- User-generated Data: Feedback from operators can also be an invaluable source of insights. Human observations often provide qualitative data that help enhance quantitative analyses.
- Time-series data is often used to observe trends over time.
- Historical data helps in benchmarking performance and predicting future issues based on past occurrences.
- Keeping track of the environment can lead to more accurate predictive models.
- Understanding what operators notice in their daily work can fine-tune predictive capabilities.
By integrating various data types, organizations can create a more holistic view of their assets. This detailed analytics approach enables accurate predictions, ensuring timely interventions that enhance the overall productivity and lifespan of machinery.
Machine Learning and Predictive Maintenance
Machine learning plays a pivotal role in the field of predictive maintenance, leveraging vast amounts of data to inform decision making. As companies adopt AWS IoT, they unlock the ability to apply sophisticated algorithms to their operational data. This integration enhances the anticipation of maintenance needs, allowing for proactive strategies rather than reactive ones. The use of machine learning can significantly reduce downtime and extend the life cycle of critical assets.
Machine Learning Algorithms for Predictive Maintenance
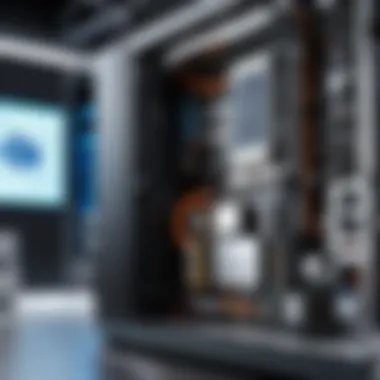
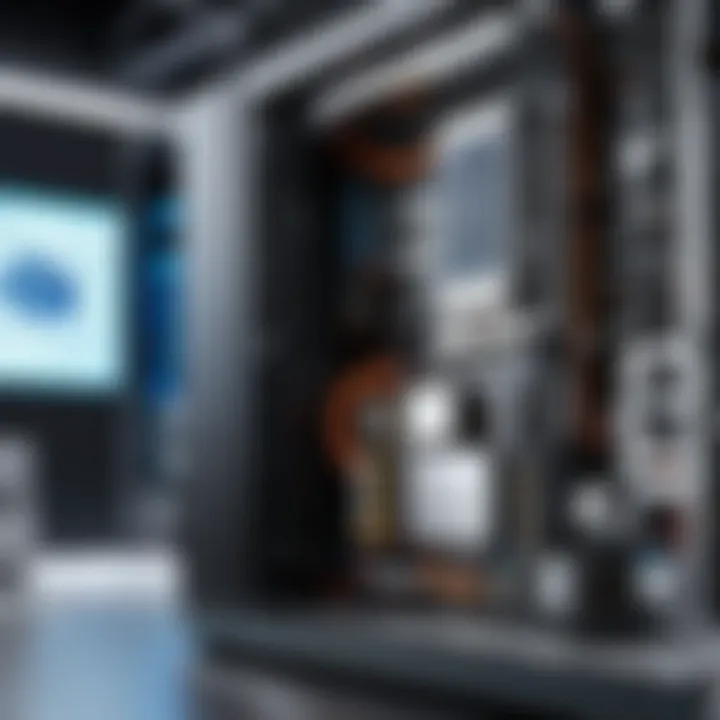
Applying various machine learning algorithms targets more precise predictions about equipment failure. Some common algorithms used include:
- Regression Models: These help in predicting continuous outcomes, like the remaining useful life (RUL) of machinery.
- Classification Algorithms: These are useful for categorizing equipment conditions. For instance, logistic regression may classify assets as functioning normally or about to fail.
- Anomaly Detection: Techniques like clustering can unearth abnormal patterns in data that often signal potential failures. This is crucial for identifying issues before they escalate.
- Time Series Analysis: This approach allows for analyzing data points collected at successive times. It is especially relevant for monitoring trends over time and forecasting future states.
The selection of the right algorithm depends on the specific operational scenario and the type of data available. Companies must experiment with multiple models to find the best fit for their unique requirements.
Training Data Requirements
The effectiveness of machine learning in predictive maintenance is heavily reliant on the quality and quantity of training data. Having diverse and robust datasets is essential for training algorithms accurately. Here are some key aspects to consider:
- Historical Data: Past maintenance records and equipment performance data are vital. They help algorithms learn patterns associated with failures and normal operations.
- Real-Time Data: Continuous data from sensors and devices provides ongoing input that enables real-time predictions and adjustments.
- Feature Engineering: Selecting the right features or variables for training is critical. Well-chosen features significantly impact the performance of models.
- Data Cleansing: Ensuring data is accurate and devoid of errors is crucial. Incorrect or noisy data can lead to mispredictions, undermining the reliability of the predictive maintenance strategies.
In summary, as organizations integrate AWS IoT with machine learning, they must pay careful attention to their training data requirements. A well-structured dataset leads to effective training of models, which translates into more reliable predictive maintenance outcomes.
Implementing Predictive Maintenance with AWS IoT
Implementing predictive maintenance with AWS IoT represents a critical strategy for businesses seeking to optimize asset management. As industries evolve, the integration of Internet of Things enabled devices becomes essential to anticipate failures and enhance the operational framework. With devices connected to the AWS IoT platform, companies can gather real-time data from their equipment, leading to informed decision-making based on predictive analytics. This step is crucial not only for improving uptime but also for extending the lifespan of assets.
Using AWS IoT, organizations can proactively address maintenance needs. By leveraging data analytics and machine learning algorithms, businesses can predict potential equipment failures before they occur. It streamlines operations and reduces maintenance costs, providing a strong argument for implementing such systems.
Key Steps in Implementation
The effective implementation of predictive maintenance through AWS IoT involves several key steps:
- Asset Identification: Identify which assets require monitoring and then choose appropriate sensors to capture relevant data.
- Data Integration: Connect the devices to AWS IoT and ensure data is correctly flowing into the AWS ecosystem for analysis.
- Analytics Setup: Use AWS services like Amazon QuickSight or AWS Lambda to analyze data. Create dashboards for real-time insights on asset conditions.
- Machine Learning Models: Implement machine learning models using tools such as Amazon SageMaker to predict failures based on historical data.
- Feedback Loop: Establish a system for continuous learning, updating models and strategies as new data is collected.
Following these steps allows organizations to create a strong foundation for predictive maintenance. Each step builds upon the previous one, leading to a more holistic approach to asset management.
Best Practices for Implementation
To maximize the impact of predictive maintenance, consider the following best practices:
- Start Small: Begin with a pilot program for a limited number of assets. This allows for manageable implementation and easier troubleshooting.
- Focus on Data Quality: Ensure that the data collected is accurate and reliable. Poor data quality can undermine the predictive models.
- Leverage AWS Resources: Utilize AWS documentation and consult with AWS certified professionals during implementation to ensure best practices are followed.
- Ensure Scalability: Design the system with future expansions in mind, allowing for a seamless addition of more assets and sensors without significant overhauls.
- Regularly Reassess Needs: Periodic reassessment of equipment and technology needs is crucial. Adapt maintenance approaches and technology as the industry progresses.
Implementing predictive maintenance with AWS IoT is not just about technology; it requires a cultural shift within the organization. Stakeholders need to embrace data-driven decision making, ensuring alignment between operations and maintenance strategies. As businesses become increasingly reliant on technology, mastering predictive maintenance using AWS IoT will become a key differentiator.
Case Studies of AWS IoT Predictive Maintenance
Case studies offer concrete examples that illuminate the practical application of AWS IoT in predictive maintenance. These real-world scenarios demonstrate how different industries have successfully implemented AWS IoT solutions to optimize their asset management. The insights gained from these examples are invaluable for decision-makers and IT professionals looking to enhance operational efficiency.
In exploring the importance of case studies, one recognizes the benefits of learning from actual implementations. They reveal challenges faced, solutions adopted, and outcomes achieved. This information aids organizations in making informed decisions, mitigating risks, and accelerating their own implementations of predictive maintenance strategies using AWS IoT.
Industry-Specific Examples
Real-world applications of AWS IoT in predictive maintenance span multiple industries, each with unique requirements and challenges. Here are a few notable examples:
- Manufacturing Sector: A major automotive manufacturer incorporated AWS IoT to monitor machinery performance in real-time. By analyzing data from sensors attached to machines, the company identified potential failures before they occurred. This proactive approach reduced downtime by 25% and enhanced productivity.
- Oil and Gas Industry: A leading oil producer utilized AWS IoT to track the health of drilling equipment. Using predictive analytics, they forecasted maintenance needs, thus reducing the chance of catastrophic equipment failure. This shift resulted in a decrease in repair costs by 30%.
- Transportation and Logistics: A global shipping company adopted AWS IoT solutions to maintain its fleet of vehicles. By implementing predictive maintenance analytics, they improved route efficiency and lowered fuel costs. The outcome was a remarkable increase of 20% in on-time deliveries.
These examples underscore how sector-specific challenges can be effectively addressed through tailored AWS IoT predictive maintenance implementations.
Lessons Learned from Case Studies
Analyzing case studies provides insights into various lessons learned from implementing predictive maintenance using AWS IoT:
- Importance of Data Quality: High-quality data is critical. Poor data can lead to incorrect predictions and missed maintenance opportunities. Having robust data collection methods is essential.
- Stakeholder Involvement: Engaging all levels of staff is key to successful implementation. From management to users on the ground, aligning everyone on goals fosters a collaborative environment.
- Scalability Considerations: Successful implementations often start small but must be designed for scalability. Organizations learned the hard way that what works for one asset may not easily transfer across different operations.
- Continuous Learning: Implementations are rarely perfect from the start. Learning from initial trials allows organizations to refine and adapt their predictive maintenance frameworks, improving efficacy over time.
Through these lessons, companies can avoid common pitfalls and streamline their strategies for implementing AWS IoT predictive maintenance.
Benefits of AWS IoT Predictive Maintenance
The integration of AWS IoT within predictive maintenance frameworks presents significant advantages for organizations seeking to optimize asset management. Embracing this technology is essential for improving efficiency, cost management, and equipment reliability. This section emphasizes key benefits that organizations can achieve through the utilization of AWS IoT predictive maintenance.
Operational Efficiency and Cost Reduction
One of the most prominent benefits of AWS IoT predictive maintenance is the substantial enhancement in operational efficiency. By leveraging real-time data from connected assets, companies can monitor performance continuously. This enables organizations to detect anomalies early, thereby preventing potential failures before they escalate into costly downtimes.
- Real-time Insights: AWS IoT facilitates continuous data collection and analysis, offering decision-makers vital insights.
- Reduced Downtime: With predictive maintenance, maintenance schedules shift from reactive to proactive. This foresight reduces unplanned downtimes significantly, maintaining production throughput.
- Cost Savings: Reduced downtime directly correlates with cost savings. Organizations spend less on emergency repairs and can allocate maintenance budgets more effectively by planning interventions based on data.
"Predictive maintenance can lead to a reduction in maintenance costs by 10-40% compared to traditional approaches."

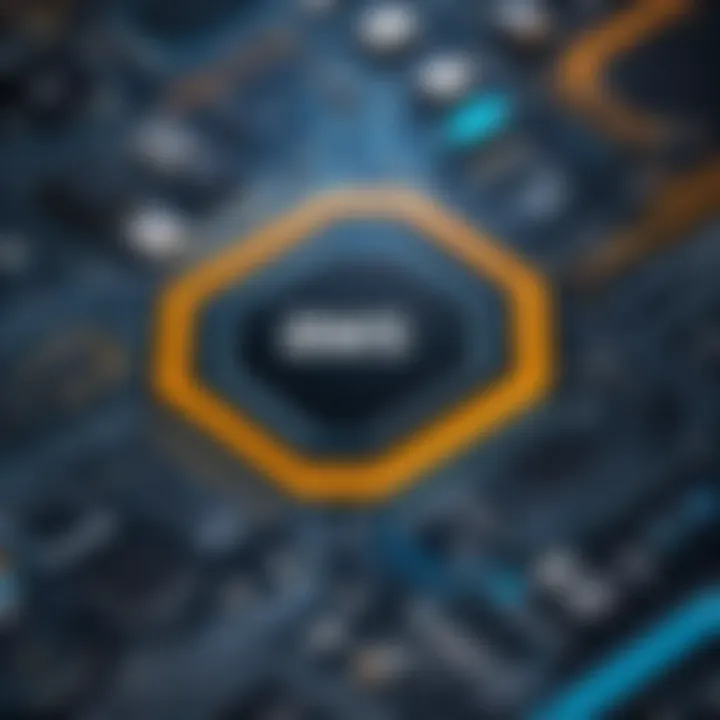
These factors converge to create an ecosystem where resources are employed more judiciously, resulting in overall lower operational costs.
Enhanced Longevity of Equipment
Another critical advantage of AWS IoT in predictive maintenance is the extended lifespan of equipment. Utilizing advanced monitoring tools allows organizations to understand the conditions their assets face over time. This analysis facilitates targeted maintenance practices focused on preserving equipment longevity.
- Condition-Based Maintenance: Assets can be assessed in terms of their actual condition, rather than relying solely on manufacturer-recommended schedules.
- Lower Wear and Tear: By addressing maintenance needs preemptively, organizations can reduce wear and tear on machines, leading to less frequent replacements.
- Improved Reliability: Equipment that is well-maintained operates more reliably, ultimately supporting better operational continuity and performance.
Adopting AWS IoT for predictive maintenance is not just about addressing immediate issues; it is about cultivating a management philosophy that fosters sustainable use of assets over their life cycle.
In summary, the benefits of AWS IoT predictive maintenance are substantial. From operational efficiency and cost reduction to enhanced equipment longevity, organizations that embrace this technology place themselves at a significant advantage in terms of productivity and sustainability.
Challenges in AWS IoT Predictive Maintenance
In the realm of AWS IoT and predictive maintenance, understanding the challenges is pivotal. These challenges can hinder the effectiveness and overall implementation of predictive maintenance initiatives. Addressing challenges can lead to improved outcomes, making this section crucial for stakeholders in industries utilizing AWS IoT.
Data Privacy and Security Concerns
Data privacy and security stand as major concerns in AWS IoT predictive maintenance. As data is collected from various devices, it becomes imperative to ensure that sensitive information is protected. The transmission and storage of data raise risks of unauthorized access.
Organizations must adhere to strict compliance regulations, which vary by region. Failure to meet these standards can lead to significant penalties. Moreover, customers are becoming increasingly aware of their data rights and privacy issues. This awareness means businesses must be transparent and take necessary precautions.
To mitigate these risks, implementing robust security protocols is essential. Strategies may include:
- Encryption of data at rest and in transit
- Employing multi-factor authentication for access control
- Conducting regular security audits to identify vulnerabilities
- Educating employees on best practices for data privacy
These measures help create a secure environment within which predictive maintenance can flourish, ultimately enhancing user trust and safeguarding organizational reputation.
Integration Challenges with Legacy Systems
Another significant hurdle in implementing AWS IoT predictive maintenance involves integration with legacy systems. Many organizations have existing systems that may not support modern IoT technologies. These older systems often lack the capabilities required for real-time data processing and analysis.
Integrating new AWS IoT solutions with these aged systems can be complex. Potential issues include:
- Lack of interoperability, which means newer devices may not communicate effectively with older infrastructure
- High costs associated with system upgrades or replacements
- A steep learning curve for employees accustomed to outdated processes
- Potential downtime during the integration process
To successfully navigate these challenges, organizations might consider adopting hybrid systems or gradual integration strategies. This approach allows businesses to leverage existing assets while progressively upgrading their infrastructure. Close collaboration with IT teams and vendors is also beneficial in streamlining the integration process, thus fostering a more effective predictive maintenance strategy.
Future Trends in Predictive Maintenance
Predictive maintenance is shifting rapidly as new technologies emerge and industries adapt. Understanding these future trends is crucial for businesses seeking to enhance operational efficiency through AWS IoT. These trends offer various advantages, including better efficiency, sustainability, and adaptive asset management. Each industry will benefit from tailored solutions, but adaptability remains the common thread for all organizations.
Evolving Technologies and Innovations
New technologies are driving predictive maintenance toward smarter solutions. The integration of advanced sensors, artificial intelligence, and edge computing shapes a robust predictive maintenance framework.
- Smart Sensors: These devices collect real-time data from equipment, enabling immediate analysis and quicker decision-making.
- Artificial Intelligence: AI enhances the analysis of large datasets, recognizing patterns that can signal potential failures.
- Edge Computing: This technology processes data closer to the source, reducing latency and enabling faster responses.
The convergence of these technologies facilitates more accurate predictions and reduces downtime. For instance, a manufacturing plant can implement AI models that learn from previous maintenance records. As a result, it can anticipate when machinery might fail, allowing for timely interventions.
Predictions for Industry Standards
As predictive maintenance evolves, so do the industry standards that govern its implementation. These predicted standards will likely focus on data security, interoperability of devices, and compliance with various regulatory environments.
- Data Security: As businesses collect and analyze vast amounts of data, securing this information will be paramount. Expect stricter standards around data privacy and protection, particularly in industries like healthcare and finance.
- Interoperability: Predictive maintenance solutions will require devices from multiple vendors to work collaboratively. Future standards will streamline compatibility to facilitate smoother integration.
- Regulatory Compliance: Each industry must stay aligned with regulations that affect operations. Adapting predictive maintenance solutions to comply with these regulations will ensure sustainable practices and foster trust.
The End
The conclusion of this article encapsulates the significant findings and insights related to AWS IoT and its role in predictive maintenance. As industries increasingly face challenges such as operational inefficiencies and unplanned downtime, the implementation of AWS IoT offers a potent solution. It enhances asset management by facilitating data-driven decision-making, improving equipment longevity, and decreasing maintenance costs. AWS IoT enables organizations to monitor their assets in real time, thus predicting issues before they escalate into costly repairs.
In this article, we found that predictive maintenance not only streamlines operations but also aligns with core business objectives by maximizing productivity and reducing undue expenses. While there are obstacles to be navigated, including data privacy, security concerns, and integration with existing systems, the long-term benefits of adopting AWS IoT technology are undeniable.
"The deployment of cloud-based IoT solutions like AWS can be transformative, providing unprecedented insights into asset health and performance."
The discussion highlighted key elements such as the integration of machine learning algorithms, which assist in analyzing historical data to prevent failures. Additionally, we explored several case studies demonstrating the pragmatic advantages that various industries have reaped through proactive maintenance strategies.
In summary, AWS IoT predictive maintenance stands as a cornerstone for modern asset management strategies, offering organizations the tools to foster not only efficiency but also innovation in operational practices.
Recap of Key Points
- Importance of Predictive Maintenance: Enhances operational efficiency and minimizes downtime.
- AWS IoT Capabilities: Integration of real-time data collection and analytics, fostering informed decision-making.
- Machine Learning Integration: Critical for analyzing complex datasets, predicting equipment failures before they occur.
- Case Studies Impact: Real-world examples demonstrate tangible benefits across multiple sectors.
- Challenges Faced: Addressing security and integration with legacy systems remains vital for successful implementation.
Final Thoughts on AWS IoT and Predictive Maintenance
The ever-evolving landscape of technology necessitates organizations to adapt and innovate. AWS IoT predictive maintenance is not merely a technological advancement; it is a strategic initiative that enables companies to position themselves competitively in their respective markets. By leveraging data, machine learning, and IoT, businesses can cultivate a proactive maintenance culture that not only saves costs but also extends the life of their assets.
The future of predictive maintenance appears promising as advancements in AI and IoT technologies continue to unfold. As industries embrace these innovations, organizations must remain vigilant and prepared to harness the capabilities of AWS IoT to fully realize its potential. The crucial takeaway is that adopting AWS IoT predictive maintenance offers a transformative path toward enhanced asset management, thereby driving significant long-term benefits.