Understanding Stock Keeping Systems: Key Insights
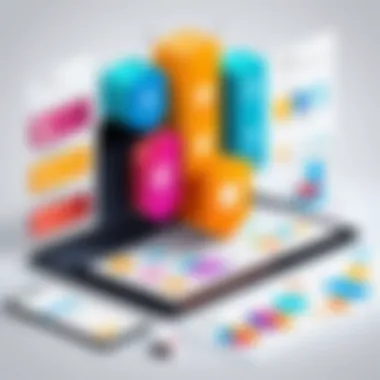
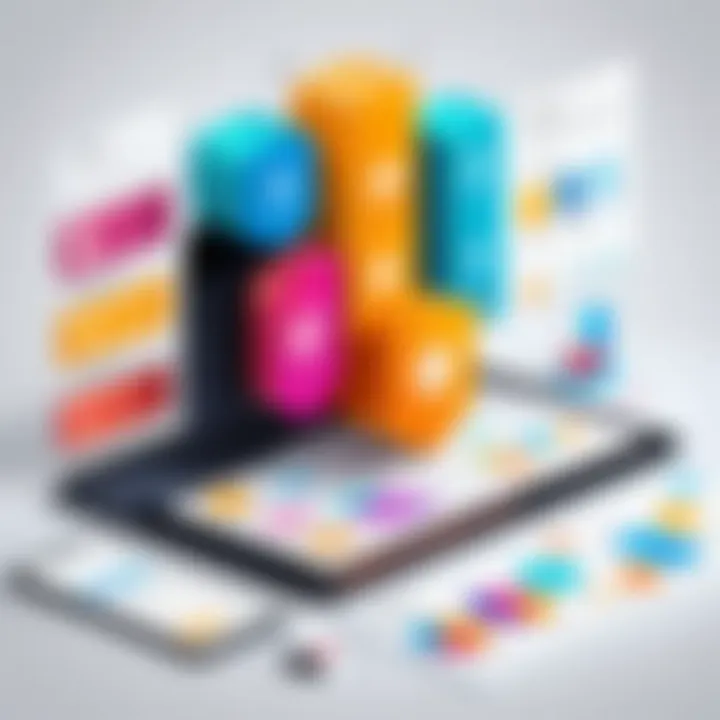
Intro
In today’s ever-evolving marketplace, stock keeping systems have emerged as a vital component for businesses wanting to thrive. Without an effective inventory management system, companies risk overstocking, stockouts, or mismanaging resources, all leading to financial detriment. This article serves as a detailed guide to understanding stock keeping systems, exploring their core functionalities, methodologies involved, and the software solutions available. It also outlines best practices and identifies the challenges organizations face in optimizing their inventory.
Key Features and Functionalities
An effective stock keeping system acts as the backbone of successful inventory management. Let’s explore some of the key features that this system offers:
- Real-time Inventory Tracking: Keeping tabs on stock levels in real-time ensures businesses can respond promptly to demand fluctuations. This feature minimizes the risk of stockouts or excess inventory.
- Automated Reordering: A robust system can automatically trigger reorder notifications when stock reaches a pre-defined threshold. This allows for seamless restocking efforts without human intervention.
- Barcode Scanning: Integrating barcode technology streamlines the process of tracking inventory, minimizing human error and speeding up stock management operations.
- Reporting and Analytics: The ability to generate detailed reports provides insights into sales trends, inventory turnover rates, and other vital metrics. This data-driven approach enables more informed decision-making.
- Multi-Location Support: For businesses operating in several locations, tracking stock across different sites becomes imperative. A capable stock keeping system can manage inventory at all these points effortlessly.
Comprehensive Overview
Every business has unique needs. Some may require advanced functionalities like demand forecasting, just-in-time inventory, or supply chain integrations. The choice of a system hinges on understanding these needs thoroughly and ensuring that it aligns with business objectives.
Target Users
The primary users of stock keeping systems are:
- Retail Managers: They monitor stock levels to ensure that popular products are always available.
- Warehouse Operators: These professionals depend on organized inventory systems for efficient operation.
- Supply Chain Coordinators: They need accurate data for planning and optimizing supply flows.
- Small Business Owners: Many entrepreneurs seek private or cloud-based solutions that fit within budget constraints, yet provide essential features.
Pricing Models and Cost Analysis
Understanding the financial implications of adopting a stock keeping system is crucial. Here’s a breakdown:
Breakdown of Pricing Tiers
Most stock keeping systems offer various pricing models:
- Subscription-Based: These systems charge a monthly or annual fee based on the number of users or features required. This is becoming a popular choice for startups and small businesses.
- One-Time Purchase: Some solutions are bought outright, providing a good option for larger firms that prefer to capitalize on their investment without recurring fees.
Additional Costs to Consider
Besides the base pricing, a company should be mindful of:
- Training and Support Fees: Typically, user training can incur additional costs, as well as ongoing support.
- Integration Costs: If the system is to integrate with existing software, there could be extra fees involved in the setup.
- Maintenance Costs: Regular maintenance often leads to minor but accumulating costs, so budgeting for this is key.
A well-chosen stock keeping system can significantly enhance operational efficiency and contribute to long-term growth.
In summary, a deep dive into stock keeping systems reveals their layers of functionality, pricing complexities, and the necessity for thoughtful implementation in the context of a business’s unique ecosystem. Grasping these essentials empowers decision-makers with the knowledge needed to navigate this indispensable aspect of inventory management.
Intro to Stock Keeping Systems
Every successful business, whether it's a bustling e-commerce store or a brick-and-mortar retail shop, hinges on effective stock management. Without the right stock keeping system, even the most robust operations can falter. A well-structured approach to stock keeping not only streamlines inventory management but also directly influences customer satisfaction and overall operational efficiency.
Modern businesses face a myriad of challenges when it comes to maintaining inventory. The evolution of consumer behavior, coupled with the shifting dynamics of supply chains, makes it imperative for organizations to adopt a honing steadfast stock keeping system that adapts to their specific needs. The introduction of these systems marks the beginning of a transformative journey where businesses can harness the power of accurate stock management tools.
Definition and Importance of Stock Keeping
Stock keeping refers to the accurate tracking and management of stock levels within a business. It's all about ensuring that the right products are available at the right time, without tying up unnecessary capital in surplus inventory. The importance of stock keeping cannot be overstated; it's the backbone of efficient operations. A clear definition can sprinkle clarity on this topic:
- Stock Keeping: The process of managing inventory levels, overseeing incoming and outgoing products, and ensuring accuracy in stock records.
This concept underscores the necessity for businesses to have a reliable stock keeping system in place. It directly impacts cash flow, operational costs, and can even make or break customer relationships.
Moreover, when stock levels are meticulously tracked, businesses can anticipate demand fluctuations and adjust their purchasing strategies accordingly. This precision helps in maintaining optimal inventory levels and contributes to risk management expertise.
Overview of Inventory Management
Inventory management is the ensemble of processes and systems that businesses use to keep track of stock levels, orders, sales, and deliveries. At its core, it strives to maintain a balance between supply and demand. Effective inventory management encompasses various methodologies and technologies, ensuring that stock levels align with market trends and customer demands. To explore this concept, it's beneficial to consider several key components:
- Tracking: The ability to monitor stock levels in real-time.
- Ordering: Establishing timely reordering practices that align with sales forecasts.
- Storage: Efficient organization of stock to reduce retrieval times and avoid excess storage costs.
"Inventory management is not just about having the right items on hand; it involves a strategic approach that optimizes the entire supply chain."
In today’s fast-paced market, organizations that invest in robust inventory management practices find themselves equipped to handle complexity with agility. The integration of advanced technologies aids in heightening accuracy and efficiency, allowing for better-informed decisions and enhanced profitability.
As we delve deeper into stock keeping systems, it’s crucial to recognize that these elements are interlinked; the success of one often relies on the effectiveness of another. Through a thorough understanding of stock keeping and inventory management principles, businesses can thrive and keep their customers coming back for more.
Understanding the Components of Stock Keeping Systems
A stock keeping system is the backbone of inventory management in any business. When it comes down to it, understanding the components of these systems is crucial. This knowledge can make a huge difference in how effectively a business runs, ultimately impacting its bottom line. Each component plays its part in forming a comprehensive overview of how stock is managed, tracked, and cycled through an organization.
Core Features of Stock Keeping Systems
Inventory Tracking
The heart of any stock keeping system is inventory tracking. This aspect ensures that each item is monitored from when it enters the warehouse to when it is sold. The primary characteristic of effective inventory tracking is real-time data updates. This immediacy allows businesses to avoid stockouts or overstock situations—which can both be costly.
A unique feature of inventory tracking is its integration with barcode or RFID technology. With these tools, businesses can gain insights into their stock levels quickly and efficiently. However, while it's a powerful choice, it can come with disadvantages as well. If the system fails or data inaccuracies arise, it can lead to chaos in stock management.
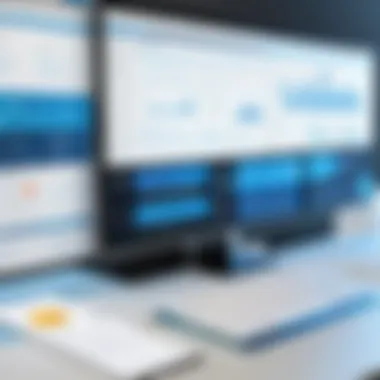
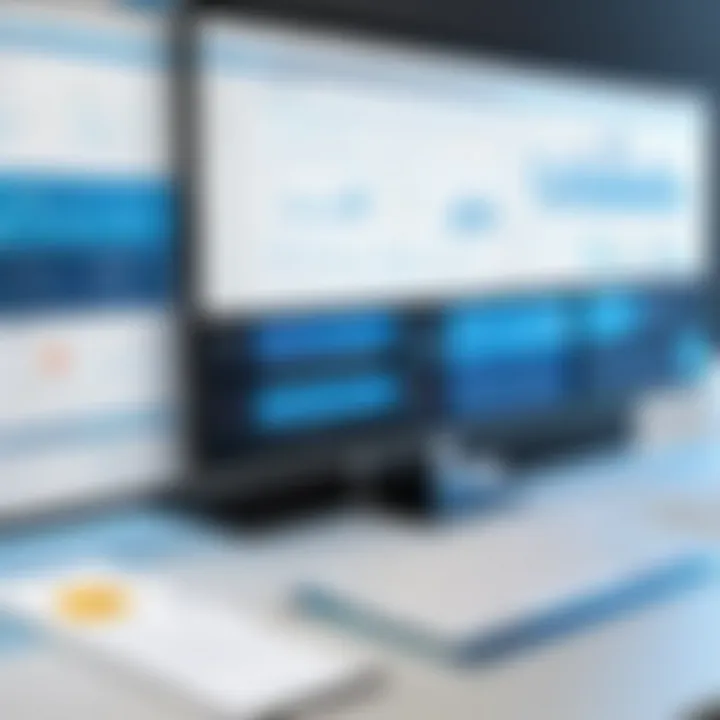
Order Management
Order management within a stock keeping system deals with processing customer orders efficiently. Keeping track of all incoming and outgoing orders can make or break a company’s reputation. An important characteristic here is workflow automation. It streamlines operations and reduces human error, minimizing delays.
One notable feature of order management systems is predictive analytics—tools that can forecast order volumes based on historical data. This predictive capability can be beneficial, but it requires a considerable initial investment and ongoing maintenance, which could deter some businesses from adopting it.
Supplier Management
Supplier management concerns the relationships a business has with its stock suppliers. Effective supplier management is essential because a reliable supplier helps control stock flow and maintain consistency. A key characteristic is collaboration tools that allow seamless communication with suppliers.
This aspect shines due to its capability to manage reorder points and negotiate better terms based on supplier performance. Yet, it can present challenges if the relationship with a supplier goes sour, directly impacting stock levels and customer satisfaction in the long run.
Report Generation
An often overlooked component of stock keeping systems is report generation. This feature enables insights into stock levels, sales patterns, and operational efficiency. The key trait here is its analytical capabilities, allowing businesses to make informed decisions based on solid data.
The unique aspect of report generation tools is their ability to create customized reports, making it easier for decision-makers to pinpoint issues. However, the downside is that generating these reports can be time-consuming without the right software or expertise.
Types of Stock Keeping Systems
Manual Systems
Manual systems are the traditional way of keeping track of stock. While they may seem outdated, many small businesses still find them useful. A defining characteristic of manual systems is simplicity; it’s straightforward for anyone to jot down stock levels on a ledger.
However, this simplicity has its downsides. The chance for human error is significant with manual entries, leading to inaccurate stock records. That could eventually turn a flourishing business into a struggling one if not handled carefully.
Automated Systems
In contrast, automated systems employ technology to manage stock, offering real-time visibility and efficiency. A noteworthy feature is integration with other business tools, such as accounting and CRM software.
These integrated systems enhance communication and speed up processes, making them a popular choice for growing businesses. However, the downside is that they can be expensive upfront, requiring a robust budget and technical know-how.
Cloud-based Systems
Cloud-based systems represent a modern evolution in stock keeping. They not only allow access from any location but also offer scalability as businesses grow. One major advantage is automatic updates, which alleviate the burden of software maintenance.
The distinctive aspect of these systems is their ability to handle vast amounts of data without a hitch. However, businesses must be cautious about the risks related to data security in the cloud and ensure they have a solid backup plan.
Understanding these components equips decision-makers and IT professionals with the tools to evaluate their stock management needs effectively. Identifying the right system suited for an organization can lead to enhanced efficiency, reduced costs, and greater overall satisfaction in the long run.
Methodologies for Stock Management
The realm of stock management isn't just about keeping track of products—it's a strategic endeavor that can make or break an organization. Understanding methodologies for stock management is crucial for optimizing inventory levels, reducing costs, and enhancing overall efficiency. In this section, we'll take a closer look at three prominent methodologies: Just-in-Time (JIT) Inventory, Economic Order Quantity (EOQ), and ABC Analysis. Each of these methodologies offers unique advantages, and they cater to different business needs.
Just-in-Time (JIT) Inventory
Just-in-Time inventory is a lean management strategy that focuses on maintaining minimal inventory levels. The fundamental premise is to receive goods only as they are needed in the production process, which reduces waste and increases efficiency.
The main benefits of JIT include:
- Reduced Inventory Costs: By keeping stock levels low, businesses can save on storage costs and insurance.
- Increased Efficiency: This approach encourages a streamlined production process, as products arrive only when needed.
- Improved Cash Flow: With less money tied up in inventory, businesses can use profits for other essential operations.
However, JIT isn't without its challenges. Supply chain disruptions—be it a natural disaster or unforeseen demand spikes—can cripple operations that rely heavily on this method.
Economic Order Quantity (EOQ)
The Economic Order Quantity model helps determine the ideal order quantity that minimizes total inventory costs. This classic formula balances ordering costs and holding costs through an analytical approach. The benefits of EOQ include:
- Cost Efficiency: Optimizes the amount spent on ordering and storing inventory.
- Minimized Stockouts: Helps ensure that products are available when customers demand them, enhancing reliability.
- Streamlined Ordering Process: Provides a clear framework for regular ordering schedules, aiding in organizational planning.
A key consideration when implementing EOQ is understanding the underlying demand and cost variables, as inaccurate inputs can lead to suboptimal results.
ABC Analysis
ABC Analysis categorizes inventory into three distinct categories based on their importance:
- A Items: High-value items with low sales frequency. These require tight control and monitoring.
- B Items: Moderate value and moderate sales frequency. These are managed with a balanced approach.
- C Items: Low-value items with high sales frequency. These require less oversight but still contribute to overall revenue.
The advantages of ABC Analysis include:
- Focused Resource Allocation: Attention and resources can be directed where they are needed most, ensuring efficient management.
- Priority Management: Managers can address items based on their importance, enhancing decision-making processes.
- Enhanced Forecasting: This methodology helps in predicting sales trends and managing inventory levels accordingly.
While ABC Analysis brings structure to inventory management, it requires periodic review to adjust categories as market conditions change.
"Understanding stock management methodologies isn’t just a matter of choice; it’s about fitting the right method to your business model and goals. Each methodology shapes inventory control practices in its own right.
By mastering these methodologies, organizations can develop robust stock management practices that not only shield against potential pitfalls but also set them up for long-term success.
Software Solutions for Stock Keeping
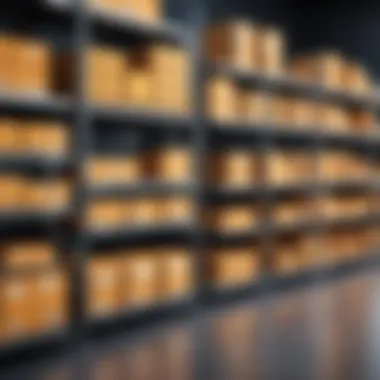
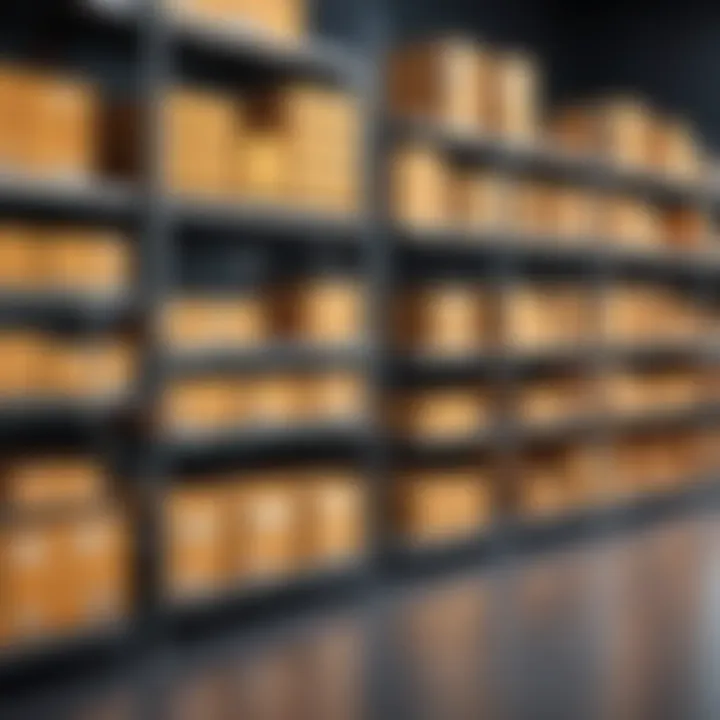
In the realm of stock management, the software solution you choose can make or break efficiency. Stock keeping systems have evolved profoundly, and the right software serves as the backbone of accurate inventory control. Selecting appropriate software isn’t just about convenience; it’s about setting the stage for operational success. Between cloud options, on-premises setups, and even open source alternatives, each type offers diverse benefits that cater to various business models.
Top Software for Inventory Management
Cloud-Based Inventory Solutions
Cloud-based inventory systems have skyrocketed in popularity. They provide all the bells and whistles needed for modern businesses to thrive in a digital atmosphere. One standout feature is the accessibility—users can manage inventory from anywhere, at any time, as long as they have an internet connection. This aspect is invaluable for businesses that require flexibility or have mobile services, like delivery fleets.
Moreover, these solutions often include real-time data updates, allowing for a seamless flow of information. However, security concerns lurk in the clouds; businesses must ensure their data protection measures are sound. In addition, regular internet outages or slow connections can hinder performance, which is a downside that should be weighed seriously.
On-Premises Inventory Software
On-premises software holds its ground firmly in numerous industries. What sets it apart is the control it gives users over their data. Firms that deal with sensitive information, such as healthcare or finance, might prefer this model since it limits exposure to external threats. The installation on local servers means fast access to data without dependency on internet connectivity, which is often a priority for traditional businesses.
That said, while it offers privacy and speed, the trade-off involves upfront costs and maintenance responsibilities, as firms need IT personnel to manage the software. Furthermore, scaling such systems can be cumbersome, and businesses must keep their hardware updated to leverage the software’s full capabilities.
Open Source Options
Open source inventory software provides an alluring blend of flexibility and customization. Unlike proprietary software, businesses can tweak the program to meet their specific needs, liberating them from the constraints of template-driven systems. The community support available often leads to robust enhancements and frequent updates. Importantly, these systems are usually more budget-friendly, an appealing factor for startups or smaller businesses.
However, the freedom that comes with open source can be a double-edged sword. The lack of formal support can lead to challenges during implementation or troubleshooting. Users often require a certain level of technical expertise to navigate and modify the software, which can impede less tech-savvy teams.
Selecting the Right Software for Your Needs
The decision-making process when it comes to selecting software is a critical one. It’s not just about what looks good on paper; it’s about aligning the software's features with your unique business requirements.
Evaluating Software Features
Before settling on software, evaluating its features should be exhaustive and targeted. Look for inventory tracking capabilities, integration with other systems, user friendliness, and customer support. A user-friendly interface can save time in training and day-to-day operations, thus enhancing productivity.
One unique aspect here is the ability to automate certain tasks. This gives an edge in efficiency, reducing the likelihood of human error. Still, be wary; software with too many features may come off as cluttered or complicated, leading to a steeper learning curve for employees.
Cost Considerations
The cost of inventory management software can vary like night and day. It’s essential to analyze the total cost of ownership, which includes licensing fees, maintenance costs, and hidden charges. A pricier software solution might not always translate to better functionality; it simply might offer additional features that aren't necessary for your operations.
Consider budgeting for ongoing costs, as updates, training, and potential upgrades can impact your finances. Go for a solution that provides good ROI, ensuring that the initial outlay brings tangible benefits down the line.
Integration Capabilities
Integration with other business systems can be pivotal. A system that integrates smoothly with your accounting, sales, or CRM tools means data flows seamlessly across departments. A robust integration capability strengthens the overall efficiency of stock management processes.
The unique feature here is the ability to centralize data management. This eliminates silos of information, enhancing visibility for managerial decision-making. On the flip side, be cautious—complex integration processes can lead to headaches during implementation and require extra resources.
In the fast-paced world of business, selecting the right stock keeping software remains a fundamental task that influences how well an organization navigates its inventory challenges.
Benefits of Implementing a Stock Keeping System
Implementing an effective stock keeping system is like laying down a solid foundation for a building; without it, everything else can become shaky and unreliable. The benefits are not just about counting beans; they delve deeper into the operational aspects of a business. Here’s a closer look at what a robust system can mean for an organization.
Enhanced Operational Efficiency
When a company implements an efficient stock keeping system, it establishes a streamlined process for managing its inventory. This efficiency translates to better use of resources. Employees spend less time searching for products and more time focusing on core business activities. For instance, consider a retail store that knows exact stock levels at the click of a button. This immediacy allows for timely reorders and avoids overstocking, ensuring the shelves are never bare when customers walk in.
Furthermore, automated tracking reduces human error. Instead of relying on manual entries that are prone to mistakes, a digital system can automatically log transactions and update availability in real time. This not only improves accuracy but also saves money in labor costs, as fewer workers are needed to manage the same volume of inventory.
"Efficiency is doing better what is already being done."
Peter Drucker
Cost Reduction Strategies
One cannot overlook the impact of stock keeping systems on a company’s bottom line. With a well-implemented inventory management system, businesses are better positioned to reduce costs in several ways.
- Minimized Excess Inventory: By avoiding over-purchasing and ensuring that stock levels are aligned with demand, a business can free up cash flow tied in unsold goods.
- Decreased Waste: Perishable goods or items with a short shelf life benefit from close monitoring. Regular audits using a stock keeping system help prevent spoilage and obsolescence.
- Reduced Storage Costs: With optimized stock levels, companies can avoid the need for expansive warehousing facilities, thereby cutting down costs associated with rent, utilities, and maintenance.
To illustrate, a food distributor employing a stock keeping system might notice a significant decrease in expired goods, saving them thousands of dollars each month, directly contributing to increased profit margins.
Improved Customer Satisfaction
Ultimately, a stock keeping system serves the end customer. When inventory is managed well, the customer experience is paramount. For one, it ensures product availability, which directly correlates to satisfaction. A customer walking into a store and finding the product they want is far more likely to leave happy and spread positive word-of-mouth.
Moreover, better stock management leads to quicker order fulfillment. Whether a business operates online or offline, the ability to swiftly process orders ensures that customers receive their products on time. In an era when immediacy is highly valued, delays can lead to frustration and lost sales.
In summary, the implementation of a stock keeping system doesn't just bring advantages to the management side of things; it touches every aspect of a business, leading to a more efficient operation, cost savings, and, most importantly, satisfied customers.
Challenges in Stock Keeping Systems
When it comes to managing stock, the journey can be as tricky as navigating a winding road on a foggy night. Stock keeping systems are indispensable in maintaining operational flow, yet they come with their own set of challenges. These challenges can not only hinder the efficiency of operations, but can also lead to significant financial losses. It's absolutely vital for decision-makers to grasp these hurdles so they can strategize properly to mitigate risks and exploit opportunities.
Effective stock management is tied intricately to both customer satisfaction and overall business success. Without a robust understanding of common pitfalls and influencing factors, organizations may end up throwing good money after bad.
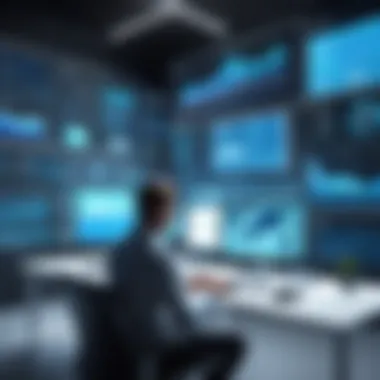
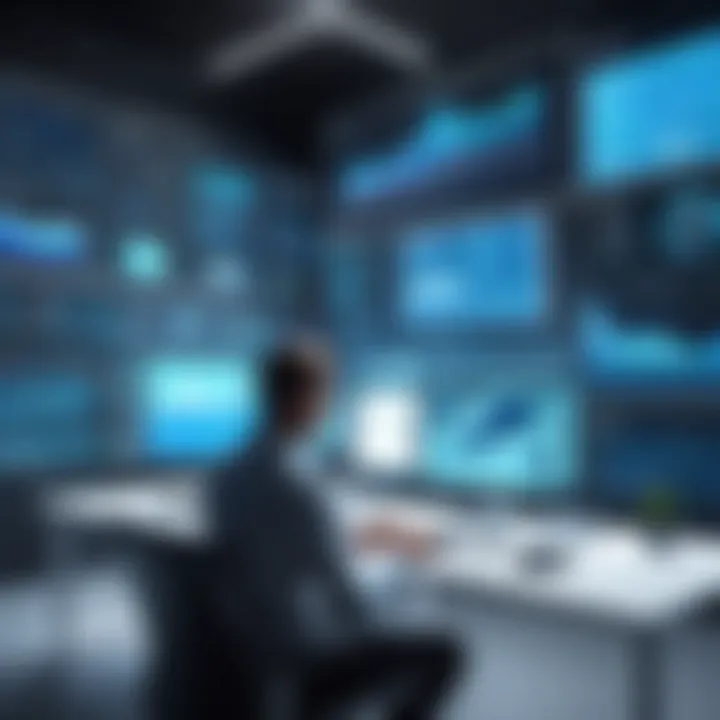
Common Pitfalls in Inventory Management
Inventory management can quickly turn into a quagmire if missteps occur. One common pitfall is the failure to maintain adequate stock levels. Imagine a retailer that runs out of popular items during peak season. The result? Customers turning to competitors because their needs are unmet.
Another fundamental issue is the reliance on outdated inventory processing methods. Sticking to archaic systems not only slows down operations but also affects the accuracy of data. This often translates into stock discrepancies – a financial hangover that nobody enjoys. Some of these pitfalls include:
- Overstock: Holding more inventory than necessary can lead to extra costs related to storage, insurance, and spoilage.
- Understock: On the tiny flip side, not having enough inventory can cause lost sales and decreased customer loyalty.
- Inaccurate Records: Manual entries prone to human errors can lead to a variety of inventory issues.
To sum up, taking a hard look at these pitfalls can reveal where an organization might be shooting itself in the foot. Awareness breeds proactive solutions, drawing a clear line between profitability and loss.
Factors Affecting Inventory Accuracy
Achieving inventory accuracy is like balancing on a tightrope; even a small misstep can lead to a catastrophic fall. Several factors can contribute to inaccuracies, but among the most detrimental is inadequate training. If team members are not educated on proper inventory practices, even the best systems can falter. Additionally, damage during transportation or storage can distort stock levels, derailing entire operations.
Here are the significant culprits affecting inventory accuracy:
- Human Error: Mistaken entries and mislabeling can distort actual counts.
- Complex Supply Chains: The more layers involved in the supply chain, the higher the risk of miscommunication or oversight.
- Technology Limitations: Outdated or incompatible software may not capture real-time data effectively.
"Accuracy in inventory management isn't just about numbers; it's the lifeline of customer satisfaction and peace of mind for business leaders."
So, recognizing these obstacles in stock keeping systems is key. Each hurdle presents its own set of challenges, but with thoughtful actions and informed decisions, one can pave the way for a more streamlined inventory management experience.
Best Practices for Efficient Stock Management
Efficient stock management serves as the backbone of operational success for businesses of all sizes. Applying best practices in this area not only ensures that inventory levels are maintained, but also promotes more accurate forecasting and reduces waste. A well-oiled stock keeping system hinges on consistently implementing strategies that enhance both flexibility and transparency.
Regular Stock Audits
Regular stock audits are vital for keeping an accurate pulse on inventory levels. These audits help businesses to identify discrepancies between recorded inventory and actual stock on hand. This process can vary, from a full physical inventory count to cycle counting, where only a portion of inventory is counted at scheduled intervals.
The key benefits of conducting regular stock audits include:
- Reduced Shrinkage: Finding mistakes early can help mitigate losses due to theft or mismanagement.
- Enhanced Accuracy: Regularly verifying counts against system records ensures that what's on paper matches reality, reducing errors in reordering and planning.
- Informed Decision-Making: With accurate data, decision-makers can forecast demand better, thus enabling efficient ordering processes.
Moreover, technology can play a big role here. For instance, companies using software such as Zoho Inventory or TradeGecko can automate aspects of the audit process, receiving notifications for stock that seems off.
Utilizing Technology for Inventory Control
As the digital landscape rapidly evolves, leveraging technology in inventory control becomes almost indispensable. Many organizations now rely on innovative software solutions that offer a range of features to optimize stock management. Here are key considerations:
- Real-Time Tracking: Automated systems can provide up-to-the-minute data on stock levels, allowing businesses to keep ahead of trends.
- Data Analytics: Modern systems often come with analytical tools that can deliver insights on sales patterns, helping businesses correlate stock levels with customer demand.
- Integrations: Many technology platforms can seamlessly integrate with sales channels, ensuring a smooth transition of data across systems.
By incorporating technology into their stock management practices, businesses not only enhance organization but also gain a competitive edge in understanding market demands.
"Implementing technology in inventory management can transform a cumbersome process into a streamlined operation, saving time and reducing errors."
In essence, fostering best practices in stock management through regular audits and the use of innovative technologies creates a robust strategy that not only improves efficiency but also positions businesses for long-term success.
Future Trends in Stock Management
The landscape of stock management is constantly changing. As businesses evolve and customer expectations shift, staying updated on future trends becomes necessary to maintain a competitive edge. In the realm of stock keeping systems, these trends not only aim to enhance operational efficiency but also align with the broader digital transformation seen across industries. Understanding the future direction of stock management involves focusing on emerging technologies, adaptive methodologies, and strategic frameworks that could significantly enhance inventory handling.
Impact of Artificial Intelligence
Artificial Intelligence (AI) is no longer something that's just on the horizon; it’s already at play in stock management systems, and its influence is set to grow. The integration of AI can streamline processes such as inventory forecasting, demand planning, and automated replenishment. By leveraging large data sets, AI algorithms analyze trends and predict future inventory needs more accurately than traditional methods.
Several key advantages emerge from adopting AI in stock management:
- Improved Accuracy: AI can scrutinize historical data to forecast stock needs with greater precision, drastically reducing the chance of excess stock or shortages.
- Enhanced Decision-Making: With real-time analytics and insights, decision-makers can respond swiftly to market changes.
- Cost Efficiency: Automating routine tasks—like reordering and stock audits—means that staff can focus on more value-added activities.
Investing in AI-driven tools is not just about being on trend. It’s about gaining substantial operational efficiencies that can translate to improved profitability. AI will empower businesses to react proactively rather than being reactive, laying a foundation for more robust stock keeping strategies.
The Role of IoT in Inventory Tracking
The Internet of Things (IoT) is reshaping how stock management is viewed. IoT refers to the interconnected system of devices communicating over the internet. In stock management, sensors attached to items or shelves can transmit valuable data concerning stock levels, location, and condition.
This technology offers a range of benefits that have profound implications for inventory management:
- Real-Time Monitoring: Constant updates about inventory status ensure that businesses never lose sight of their resources. This continuous oversight can lead to proactive decision-making.
- Reduction of Human Error: Automated data collection from IoT devices minimizes the risk of discrepancies and inaccuracies often tied to manual entries.
- Optimized Supply Chains: IoT integration allows companies to better manage supply chains by sharing data across the network, leading to improved collaboration with suppliers and reduced delays.
In summary, both AI and IoT are not merely buzzwords; they represent critical components that are likely to revolutionize stock management in the coming years. As decision-makers adopt these technologies, the potential for increased accuracy, efficiency, and responsiveness becomes a tangible advantage in navigating complex inventory challenges.
Ending
The conclusion of this comprehensive overview serves as a pivotal point in understanding the intricacies of stock keeping systems. As we've delved into various facets—from methodologies to software solutions—the thread that connects these elements is their collective impact on the efficiency of inventory management. These systems are not merely tools; they are strategic assets that can significantly influence a company's bottom line.
Summarizing Key Insights
Throughout this discourse, we've explored key insights that underline the essence of robust stock keeping processes. Here are some of the main takeaways:
- Core Components: Effective stock keeping systems integrate inventory tracking, order management, and supplier oversight, all working in sync to enhance operational efficiency.
- Methodologies Matter: Whether it’s the Just-in-Time approach or ABC Analysis, choosing the right inventory methodology can optimize stock levels and reduce holding costs.
- Software Selection: The plethora of software options—from cloud-based solutions to on-premises software—offers businesses flexibility, but careful evaluation is necessary to align functionalities with specific needs.
- Future Horizons: The incorporation of AI and IoT in stock management shows great promise, making systems increasingly adaptive and responsive to fluctuating market demands.
These insights highlight the importance of not just having a system in place but ensuring it is aligned with the overall strategic goals of the organization.
Final Thoughts on Stock Keeping Systems
In the end, stock keeping systems are fundamental to the success of any business that deals with inventory. They create a backbone for logistical operations, ensuring that products are not only available when needed but also managed in a cost-effective manner. With the right stock keeping system, organizations do not just keep track of their inventory; they gain insights that can lead to improved decision-making, enhanced customer satisfaction, and ultimately, greater profitability.