Understanding the Manufacturing Business Process
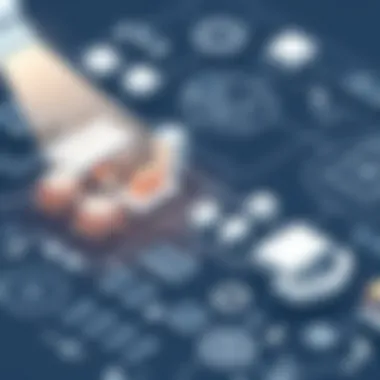
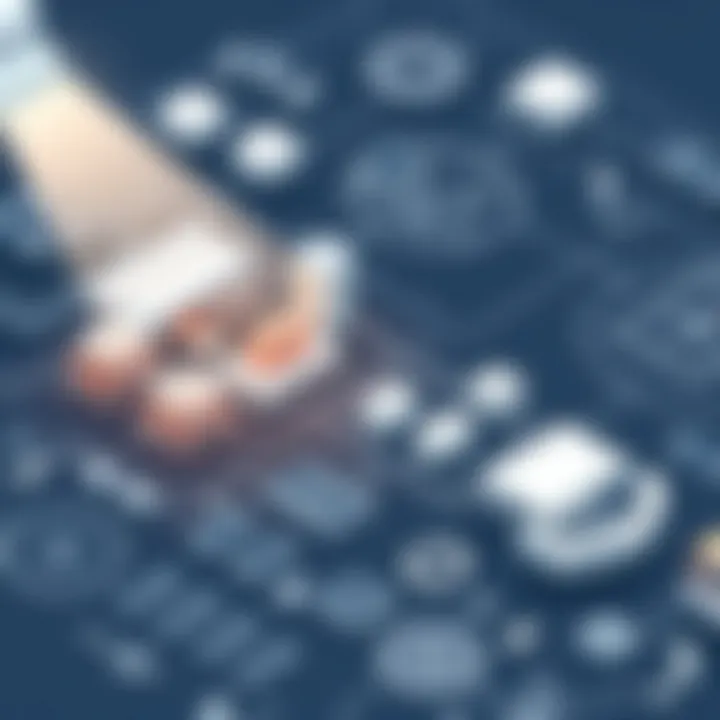
Intro
Manufacturing holds a significant place in the global economy, providing jobs and driving innovations. Understanding how the manufacturing business process works is not just for industry insiders but is also crucial for decision-makers, IT professionals, and entrepreneurs looking to carve out success in an increasingly competitive landscape. The complexity of this process involves various stages, beginning from the initial concept down to the final production. Each step has its own challenges and requires a blend of strategy, technology, and resource management to achieve efficiency and adaptability.
This exploration aims to untangle these intricacies, offering insights into best practices and methodologies that can elevate manufacturing operations.
Key concepts like strategic planning, resource allocation, and the integration of modern technology come into play throughout this dialogue. Let's delve deeper to illuminate how these elements mesh into a cohesive workflow that not only supports manufacturing but also propels it forward in a dynamic market.
Preamble to Manufacturing Business Processes
Manufacturing is at the heart of many economies around the world, acting as the engine that drives innovation and job creation. Understanding manufacturing business processes is not just about knowing how products are made; it's about grasping how these intricate steps influence overall productivity, cost efficiency, and market adaptability. As industries evolve, especially with the whirlwind pace of technological advancement, it's become increasingly important for decision-makers to grasp the comprehensive narrative of manufacturing.
In this article, we will explore:
- The stages involved in manufacturing processes
- The role of technology and data management in improving efficiencies
- Strategic management techniques that guide production
- Challenges faced and future trends impacting the sector.
By delving into these elements, this article aims to provide a foundational understanding of how a cohesive manufacturing process operates and the significance of each stage in the greater industrial ecosystem. For entrepreneurs and IT professionals alike, recognizing these components is crucial for informed decision-making and operational efficiency.
Defining Manufacturing Business Processes
A manufacturing business process can broadly be defined as the series of steps that turn raw materials into finished products. These processes encompass everything from design and planning to production and delivery. Each stage is interconnected and can significantly impact quality and delivery times.
Key Components:
- Input: This includes the materials, machinery, labor, and technology required to create a product.
- Process: Refers to the various methods employed throughout production, like machining, assembly, and quality control measures.
- Output: The final products that emerge from these processes, ideally meeting specific quality and design criteria.
Understanding how to manage these three components effectively can lead to smoother operations and less waste.
Importance in Today's Economy
Manufacturing today has taken on new dimensions in an increasingly competitive global market. It plays a pivotal role in economic stability, job creation, and technological advancement. Here are some crucial aspects of its importance:
- Economic Contributions: Manufacturing contributes significantly to GDP, particularly in developing countries. A strong manufacturing base often correlates with robust economic growth.
- Job Creation: The sector employs millions, providing not only jobs but also skills training that can elevate communities.
- Innovation and Technology Adoption: Modern manufacturing heavily integrates new technologies. This adoption plus its focus on R&D fosters innovation that spills over into other sectors, enhancing competitiveness.
- Global Supply Chains: Understanding manufacturing processes helps companies navigate complex supply chains that are often impacted by international trade policies.
"Manufacturing processes are like the arteries of an economy; they help circulate goods and services that fuel growth."
In summary, not grasping the intricacies of manufacturing processes can put businesses at a disadvantage in terms of efficiency and effectiveness, which, in turn, resonates with their market positioning and profitability.
Stages of Manufacturing Process
The stages of the manufacturing process form the backbone of production efficiency, laying down the groundwork for how products evolve from an idea to a finished good. Each stage involves strategic decisions that can significantly impact costs, quality, and time-to-market. The importance of these stages cannot be understated, as they help streamline operations and enhance overall productivity.
From conceptualization to distribution, a clear understanding of these steps gives manufacturers the edge needed to adapt to changing market demands. The stages not only emphasize the intricate nature of manufacturing but also highlight the role of each component in achieving a cohesive workflow.
Concept and Design
This initial phase is where ideas take shape. The focus here is not only on what the product will look like but also on functionality and market demands. Collaborative efforts of engineers, designers, and marketers create prototypes that serve as blueprints for production. Considerations during this stage include consumer needs, technological capabilities, and aesthetic appeal. Ultimately, a solid design can save on costs and time later down the line.
Material Sourcing
Sourcing the right materials is akin to laying a strong foundation for a house. Quality raw materials impact the durability and effectiveness of the final product. Manufacturers must evaluate suppliers based on quality, cost, delivery time, and sustainability. Finding the right balance here ensures that production runs smoothly without unexpected hitches due to inadequate supplies or inferior materials.
Production Planning
Planning for production involves strategizing the how and when. A robust plan includes aspects such as lead times, resource allocation, and workflow optimization. Key considerations range from manpower resources to machinery availability. A well-structured production plan can spell the difference between timely deliveries and bottlenecks that hold everything up.
Manufacturing Techniques
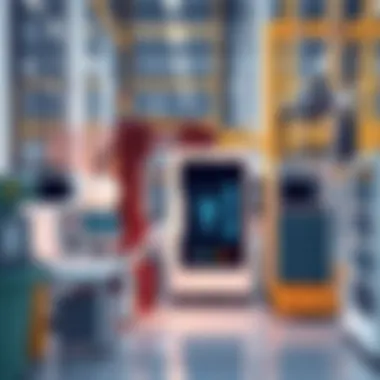
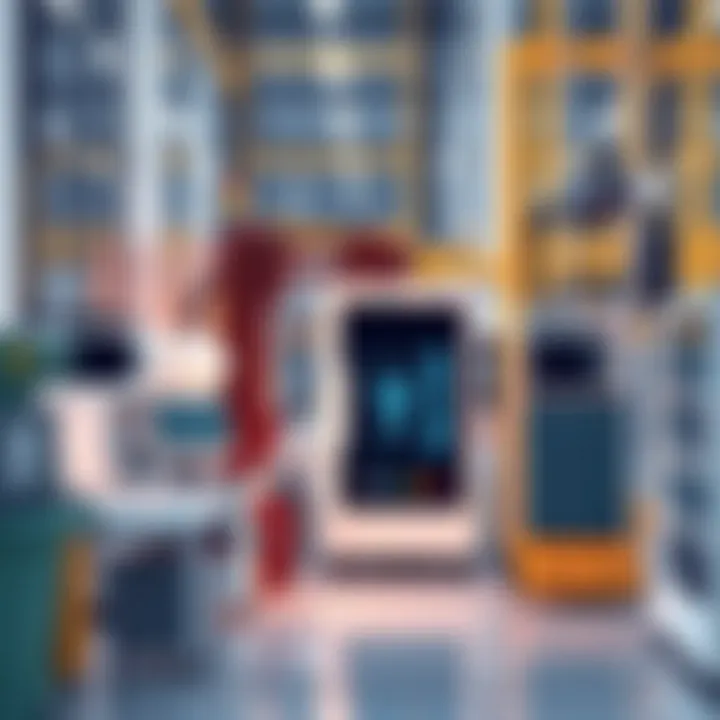
Different manufacturing techniques can significantly shape production efficiency and cost-effectiveness. Let's explore a few prevalent methods:
Lean Manufacturing
Lean manufacturing prioritizes waste reduction while maximizing productivity. Key characteristic? It's all about creating more value for customers without increasing costs. Lean focuses on continuous improvement and efficiency, making it a favored choice in various industries. Unique feature: Just-in-time resource allocation minimizes excess inventory, reducing overhead costs. While advantageous, lean practices can be challenging to implement effectively if workforce inertia exists.
Just-In-Time Production
Just-In-Time (JIT) production aims for high efficiency by scheduling materials and products to arrive precisely as they are needed. Key characteristic: It drastically cuts storage costs, allowing manufacturers to utilize funds more efficiently. Its focus on synchronized operations ensures that production lines are never idle. However, reliance on timely deliveries makes JIT vulnerable to supply chain disruptions.
Batch Manufacturing
Batch manufacturing produces goods in groups or batches rather than continuous flow. This approach provides flexibility in manufacturing different product types using the same equipment. Key characteristic: It allows for a variety of products to be made in smaller quantities. The unique feature is the ability to modify production processes based on demand shifts. While advantageous in terms of flexibility, it can lead to slower production rates compared to continuous methods.
Quality Control
Quality control is a continuous process that ensures products meet industry standards and customer expectations. This stage involves regular inspections and assessments throughout production. Adaptative quality management not only identifies defects but also fosters a culture of excellence. An investment in quality control can lead to a significant reduction in returns and increases in customer satisfaction.
Distribution and Supply Chain Management
Once products are ready, thoughtful distribution is crucial. This stage involves logistics and supply chain strategies to deliver goods effectively. Strong supply chain management ensures that products reach their destinations promptly, enhancing customer satisfaction and operational efficiency. With globalization, managing diverse suppliers and distribution channels becomes increasingly demanding, yet vital for operational success.
Understanding these stages of the manufacturing process allows companies to pinpoint inefficiencies and areas for improvement, promoting smarter decision-making for the future.
Role of Technology in Manufacturing
In the manufacturing sector, technology has carved out a fundamental role, blending seamlessly with age-old practices to elevate efficiency and quality. The reliance on cutting-edge tools and systems is not merely a trend; it's a necessity for survival in a landscape that's constantly shifting. Companies that grasp the significance of technology maintain a competitive edge, ensuring they adapt and respond to consumer demands in real-time.
Benefits of Integrating Technology
Embracing technology in manufacturing isn’t just about shiny gadgets; it’s about unlocking a multitude of advantages, such as:
- Increased Efficiency: Automating routine tasks allows employees to focus on more strategic aspects, which improves overall productivity.
- Enhanced Accuracy: Technologies like robotics minimize human error and ensure precision in tasks like assembly and quality checks.
- Data-Driven Decisions: Real-time data analytics enable manufacturers to make informed choices that directly impact the bottom line.
Yet, the integration of these technologies also comes with considerations that go beyond just installation costs. Organizations must think about team training, system compatibility, and ongoing maintenance. By weighing these factors thoughtfully, companies can expand their horizons within the manufacturing process.
Automation and Robotics
Automation and robotics stand as the vanguard of manufacturing technology. The rise of automated systems represents a seismic shift from conventional production methods. This shift allows for greater flexibility and output quality, addressing consumer needs with precision.
- Types of Automation: Manufacturers can choose between several forms, including:
- Benefits of Robotics: Incorporating robots goes beyond just speed; it also brings:
- Fixed Automation: Ideal for repetitive tasks, such as assembly line work.
- Programmable Automation: Suitable for batch production where setup and reprogramming are possible.
- Flexible Automation: Facilitates varying product designs with quick changeovers.
- Consistency in Quality: Robots deliver uniform results, reducing variance and improving product quality.
- Workplace Safety: Automating dangerous tasks results in a safer environment, as robots can manage hazardous materials better than humans.
These advancements aren't happening in isolation. Industries are now actively looking to merge robotics with other technologies like AI to create a truly interconnected production sphere.
Industry Four Point Zero
Industry 4.0 signifies a significant leap in how manufacturing operates, where smart factories leverage the Internet of Things (IoT), big data, and cloud computing to redefine processes. It's more than upgrading machines; it's about fundamentally altering the framework of production.
- Interconnectivity: Devices communicate seamlessly, streamlining the flow of information throughout the supply chain.
- Real-Time Monitoring: Systems can be overseen remotely, enabling quick adjustments if issues arise, thus minimizing downtime.
- Customization: The factories of tomorrow can adjust production lines rapidly based on consumer feedback, fostering a more customer-centric approach.
Adoption of Industry 4.0 doesn’t just happen overnight. Companies delve into this transformation at their own pace, analyzing existing infrastructure and gradually integrating new tech without disrupting ongoing operations.
Data Analytics and Artificial Intelligence
Data analytics and artificial intelligence are increasingly intertwined in the manufacturing narrative. These elements allow businesses to harness vast amounts of information to streamline operations, enhance product development, and personalize services.
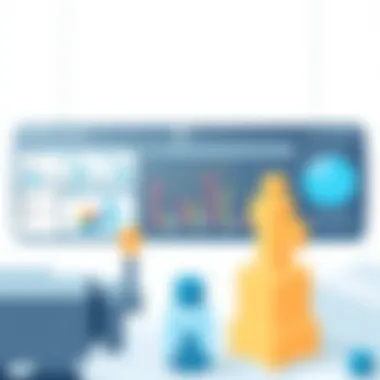
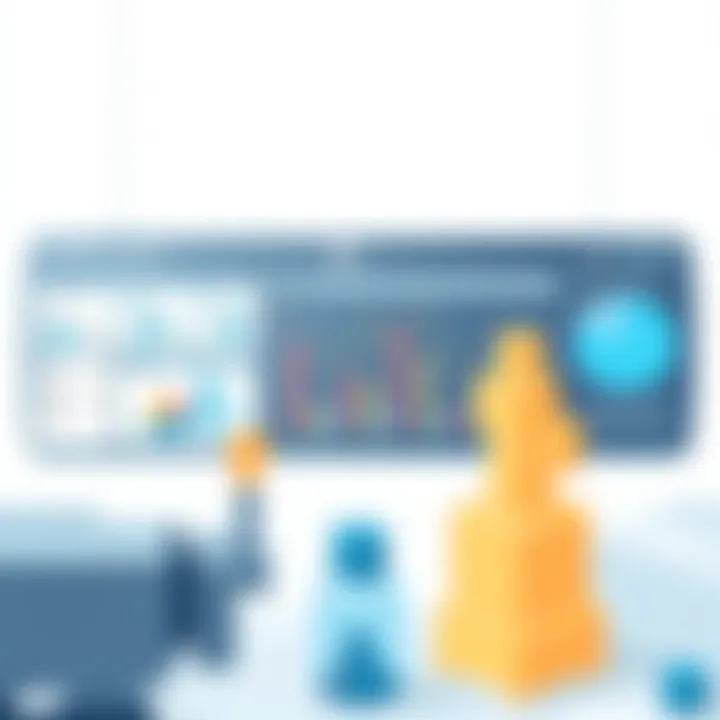
- Predictive Analytics: By analyzing historical data, manufacturers can anticipate trends and prepare accordingly, thus staying ahead of market demands.
- Smart Decision-Making: AI can help in decisions like inventory management or product design, using algorithms that analyze past outcomes to dictate best practices.
- Quality Control Automation: AI systems can monitor production outputs in real-time, detecting deviations and correcting them on the fly.
“Data is the new oil; it’s the lifeblood of informed decisions that propel growth.”
Strategic Management in Manufacturing
Strategic management in manufacturing is the backbone of operational success. It encompasses decision-making that aligns resources and capabilities with industry demands and market conditions. The importance of strategic management cannot be overstated, as it enables manufacturers to navigate through challenges and seize opportunities in an ever-shifting landscape. From supply chains to technological adoption, strategic management informs every aspect of the manufacturing process.
Strategic management in this sector involves meticulous planning and execution, empowering businesses to optimize production processes, enhance product quality, and ultimately drive profitability. Focused strategic initiatives increase efficiency, lower costs, and promote innovation which is essential in maintaining competitiveness within the industry.
Factors to consider in strategic management include market trends, consumer preferences, and regulatory environments, which all play pivotal roles in a company’s success. With the modern manufacturing ecosystem being as dynamic as it is, keeping an eye on these factors is not just advisable but critical.
Supply Chain Strategy
The supply chain strategy is a critical component of strategic management in manufacturing. A well-defined supply chain strategy ensures a synchronized flow of goods and information, thereby reducing lead time and increasing productivity. This involves selecting the right partners, establishing efficient logistics, and utilizing advanced information systems. Here's why it matters:
- Cost Efficiency: Streamlining the supply chain reduces operational costs.
- Flexibility: Adaptable supply chains respond better to fluctuations in market demand.
- Quality Assurance: Strong supplier relationships help ensure quality end-products through consistent sourcing of materials.
An effective supply chain strategy also benefits from technology such as data analytics and automation, enabling better demand forecasting and inventory management.
Risk Management
In the manufacturing realm, risk management is essential to sustain operations and mitigate threats that can disrupt production. This can encompass a range of risks, from supply chain disruptions to regulatory changes. Strategic risk management involves:
- Identification of Risks: Recognizing potential risks early can provide a foothold in adapting strategies.
- Risk Analysis: Understanding the probability and impact of risks helps prioritize which ones require immediate action.
- Response Planning: Developing contingency plans to address potential disruptions ensures the resilience of operations.
By actively managing risk, manufacturers are not only safeguarding their assets but also securing their long-term viability in the marketplace.
Sustainability Practices
Sustainability has become a hot topic in every industry, and manufacturing is no exception. The strategic implementation of sustainability practices doesn’t just align with corporate social responsibility goals; it adds substantial value in various ways. For instance:
- Cost Savings: Efficient energy use and waste reductions can significantly lower production costs.
- Brand Reputation: Companies committed to sustainability tend to earn greater customer loyalty.
- Regulatory Compliance: Proactively adopting sustainable practices can keep companies ahead of regulatory requirements, avoiding potential fines and disruptions.
The transition towards sustainable manufacturing often involves investing in cleaner technologies and materials, optimizing processes to minimize waste, and promoting ethical sourcing. This holistic approach not only supports the environment but also enhances the overall strategic positioning of a manufacturing firm, enabling it to thrive amidst increasing consumer awareness and demand for eco-friendly practices.
"A firm that strategically integrates sustainability into its processes doesn’t just adapt; it leads."
In summary, embracing robust strategic management principles in manufacturing is essential for addressing today's challenges. From a tuned supply chain strategy to rigorous risk management and impactful sustainability practices, the scope of strategic management remains vast and crucial for industry growth.
Challenges in the Manufacturing Sector
In an industry that hinges on precision, efficiency, and profitability, the challenges faced by the manufacturing sector are multifold. They can induce shifts in the operational landscape, affecting everything from productivity to financial performance. This section digs deep into the difficulties that manufacturers grapple with today, highlighting their implications and the essential strategies for overcoming them. Addressing these challenges is not merely an option; it’s a necessity for maintaining a competitive edge in an ever-evolving marketplace.
Adapting to Market Changes
The manufacturing sector is akin to a chameleon; it must adapt swiftly to the changing colors of market demand and consumer preferences. In recent years, shifts have been rapid due to technological advancements and evolving consumer needs. Companies that recognize and respond to these changes typically enjoy better outcomes.
"Adapt or perish, now as ever, is nature’s inexorable imperative."
– H.G. Wells
For instance, a manufacturer of traditional goods might see a drop in demand as consumers lean toward sustainable or high-tech alternatives. Adapting to these market fluctuations means being attuned to trends, whether it’s enhancing product design or adopting new materials. Furthermore, agile manufacturing processes—capable of quick changes in production lines—become indispensable. The focus here should be on:
- Continuous Market Research: Staying ahead of trends through ongoing analysis.
- Flexibility in Production: Modifying production lines to pivot with market demands.
- Customer Feedback Loops: Implementing mechanisms to gather insights directly from consumers.
Workforce Management
People are the lifeblood of any manufacturing enterprise. Managing a diverse workforce can present unique challenges, particularly in balancing skills, cultural differences, and evolving roles due to automation. Ensuring that employees are both engaged and well-trained is critical. Furthermore, a well-managed workforce can lead to enhanced productivity and overall job satisfaction.
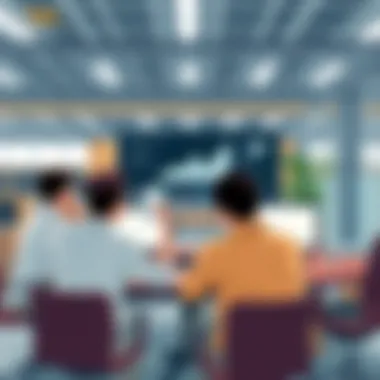
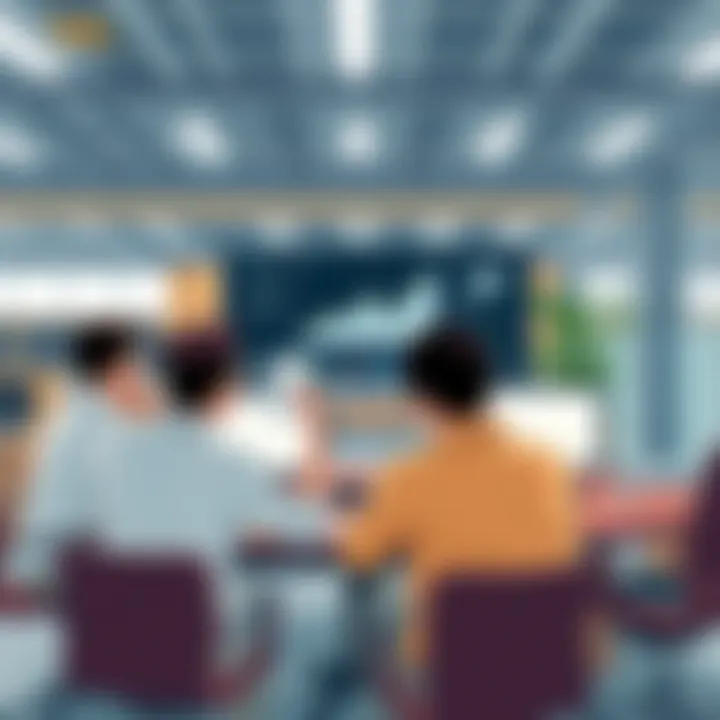
Addressing workforce challenges involves:
- Skill Development and Training: Ongoing investment in employee education to keep pace with technological changes.
- Effective Communication: Establishing open lines of communication to foster a collaborative environment.
- Retention Strategies: Implementing practices that promote employee satisfaction and reduce turnover.
Regulatory Compliance
Manufacturers operate in a realm governed by numerous regulations. Compliance is not just about avoiding penalties; it’s about ensuring product safety and quality. Regulations can vary widely across regions and can evolve quickly. Staying compliant can feel like navigating a minefield. One misstep, and the fallout could be significant.
The essential steps to maintain compliance include:
- Regular Audits: Conducting frequent reviews to ensure adherence to standards.
- Updated Training: Ensuring that all employees are aware of current regulations and practices.
- Engagement with Regulatory Bodies: Maintaining open lines with regulators to better understand upcoming changes.
Future Trends in Manufacturing
As the manufacturing landscape continues to shift and evolve, understanding the future trends in manufacturing becomes crucial for staying competitive. The industry is on the cusp of significant transformations, driven by emerging technologies, changing consumer preferences, and the effects of globalization. These elements not only influence production methods but also reshape strategic paradigms within organizations, pushing for advancements that can enhance efficiency and adaptability.
Emerging Technologies
In this era, technologies such as machine learning, Internet of Things (IoT), and additive manufacturing are carving a new path for the manufacturing sector. Machine learning aids in predictive maintenance, where systems can alert managers before equipment failures occur, thereby reducing downtime. The IoT facilitates real-time data analysis, allowing manufacturers to monitor production across various stages. Furthermore, additive manufacturing—commonly known as 3D printing—enables rapid prototyping, making the design process significantly more flexible and cost-effective.
- The integration of these technologies leads to:
- Enhanced operational efficiency
- Reduced production costs
- Faster time-to-market for new products
As manufacturers embrace these advancements, they not only boost their capabilities but also align more closely with sustainability efforts by minimizing material waste and energy consumption.
Shifts in Consumer Behavior
Today's consumers are increasingly concerned about sustainability and ethical manufacturing. Their preferences dictate that businesses must take into account not only the quality of the product but also the environmental impact. Conscious consumerism is on the rise, where buyers actively seek out products made with sustainable practices. This demand encourages manufacturers to:(
- Adopt eco-friendly materials
- Implement sustainable energy sources
- Improve transparency in the supply chain
)
Additionally, with the influence of social media, customer feedback loops have shortened. Companies must remain agile to adapt quickly to changing trends and preferences, which further propels the adoption of innovative practices.
Globalization Impact
Globalization has significantly altered how manufacturing operates, leading to a greater interdependence between markets. While this phenomenon has enabled companies to source materials and labor from various countries, it has also introduced complexity into the supply chains.
- Some critical considerations include:
- Trade policies that may affect sourcing decisions
- Currency fluctuations impacting cost structures
- Rising political tensions influencing global partnerships
However, globalization also brings opportunities, such as access to new markets and potential for reduced operational costs. Companies need to maintain a keen awareness of global trends for their strategies to be effective.
"Adapting to future trends is not merely an option for manufacturers; it is an imperative for survival in a highly competitive market." - Industry Expert
As the manufacturing sector progresses, those who recognize and adapt to these trends are better positioned to thrive. Embracing technology, responding to consumer behavior, and navigating globalization can collectively redefine success in manufacturing.
Finale
The conclusion marks the end of our journey through the complex world of manufacturing business processes. It serves as a moment to reflect on the critical insights gathered throughout the article, helping to solidify our understanding of why these processes matter. In today's fast-paced environment, manufacturing is not just about producing goods; it's about optimizing every facet from idea conception to delivery. With global competition increasing every day, companies must be sharp and adaptable to keep their edge.
Summarizing Key Insights
Throughout each stage detailed earlier, we discussed how technology, planning, and resource management play pivotal roles in shaping manufacturing success. Key points to take away include:
- Automation's Impact: It was emphasized how automation streamlines tasks, reduces mistakes, and quickens production. This is not merely a luxury; it is becoming a necessity.
- Supply Chain Management: A resilient supply chain is fundamental. Disruptions can lead to significant losses. Making strategic partnerships ensures companies can pivot quickly when challenges arise.
- Emphasis on Sustainability: Eco-friendliness is more than a trend—it's a customer expectation. Companies that adopt sustainable practices not only reduce their environmental footprint but also enhance their brand image.
Emerging technologies coupled with evolving consumer behavior push manufacturers to be innovative and responsive. Staying informed about these trends is crucial for decision-makers aiming for longevity in the sector, as these factors continually reshape the landscape of manufacturing.
Final Thoughts on Manufacturing Processes
In wrapping things up, it's crucial for leaders in the manufacturing realm to embrace a proactive mindset. Understanding these processes is not simply about knowing the steps; it’s about recognizing how every decision impacts the bigger picture.
From the early days of concept and design to the modern approaches of data analytics, the manufacturing sector is rapidly evolving. A solid grasp of these processes allows businesses to not only react to changes but to anticipate them, crafting a future aligned with both operational efficiency and customer satisfaction.
Remember, in manufacturing, the devil is in the details. Small tweaks in process management can lead to massive improvements in productivity and quality.
As we look ahead, it’s evident that those who adapt and innovate will thrive, while those who cling to outdated practices may find themselves left in the dust. The insights presented throughout this article can act as a roadmap, guiding decision-makers and professionals as they navigate the ever-changing landscape of manufacturing.