Implementing Statistical Process Control in Manufacturing
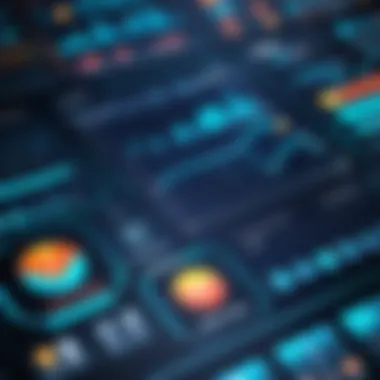
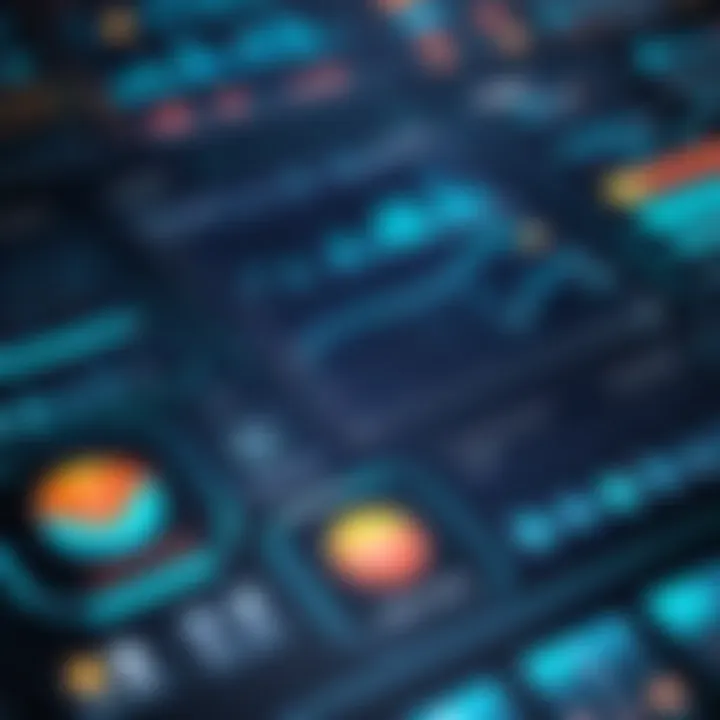
Intro
Statistical Process Control (SPC) is a powerful toolbox that allows manufacturers to monitor and control production processes. At its core, SPC utilizes statistical methods to analyze data collected during production, helping to identify variations that may lead to defects or inefficiencies. This guide aims to furnish you with a robust understanding of how to implement SPC in your manufacturing operations effectively.
The foundations of SPC lie in its ability to harness data, transforming it into actionable insights. This data-driven approach empowers decision-makers to stay proactive rather than reactive, ultimately fostering an environment of continuous improvement.
Why is SPC Relevant?
In an era where consumer expectations are ever-increasing, businesses must ensure their products are not only high-quality but also delivered consistently. SPC is not just a methodology; it's a philosophy that encompasses a commitment to quality assurance and process optimization, appealing directly to decision-makers, IT professionals, and entrepreneurs alike.
"Quality is not an act, it is a habit." β Aristotle
With SPC, this habit can be cultivated through diligent data collection and analysis.
Understanding Statistical Process Control
Implementing Statistical Process Control (SPC) is a strategic move for any manufacturing enterprise keen on enhancing efficiency and quality. Understanding SPC provides the groundwork for making informed decisions that can significantly impact production outcomes. The importance of this understanding goes beyond mere numbers; it encompasses a vision for continuous improvement. Itβs not just a tool; itβs a philosophy that encourages organizations to scrutinize their processes through a statistical lens.
Definition and Overview of SPC
Statistical Process Control refers to the method of monitoring and controlling a process through the use of statistical tools. The main objective of SPC is to ensure that a manufacturing process operates efficiently, producing more specification-conforming products with less waste. At its heart, SPC embodies a proactive approach to quality management, seeking to identify issues before they can disrupt operations.
In practice, SPC employs control charts to analyze process behavior over time. This analysis aids in determining whether a process is in a state of control, meaning it produces consistent results within pre-defined limits. For many organizations, SPC is not just about meeting specifications but creating an environment where quality becomes a habit, integrated into daily operations.
Principles of Statistical Process Control
SPC isnβt simply about collecting data; it hinges on key principles that govern effective application. Here are the fundamental principles:
- Variability Management: Every process can be subject to variations, be it in materials, methods, or environments. The first step is understanding this variability and differentiating between common causes (natural variations) and special causes (unexpected events).
- Data-Driven Decisions: Decisions in SPC are based on statistical analysis rather than intuition. This rigorous approach allows for identifying trends and patterns that might otherwise go unnoticed, fostering a robust decision-making framework.
- Continuous Improvement: The essence of SPC lies in its focus on process improvement. Techniques like root cause analysis are utilized to address underlying issues, continually refining processes.
- Engagement of Employees: For successful implementation, itβs crucial that everyoneβfrom management to floor workersβis on board and understands the significance of their role in maintaining process quality.
βQuality is not an act, it is a habit.β
β Aristotle
By embracing these principles, organizations not only enhance their output quality but also create a culture of accountability and ownership among their workforce, driving them towards collective excellence.
In essence, understanding SPC lays the foundation for effective implementation. It allows for better identification of strengths and weaknesses in production processes, paving the way for informed interventions that can lead to substantial cost savings and improved product quality over time.
The Importance of SPC in Manufacturing
Statistical Process Control (SPC) plays a vital role in modern manufacturing. It offers a systematic way to monitor and control processes through data analysis, allowing companies to maintain quality while driving efficiency. The essence of SPC lies in its ability to pinpoint variations in processes, making it crucial for manufacturers aiming to boost productivity and ensure the highest standard of output.
In a world where manufacturing deadlines are tight and competition is fierce, the importance of SPC cannot be overstated. Firms that harness this methodology stand out from their competitors. By establishing a proactive approach rather than a reactive one, organizations can avoid costly defects and wastage. The implementation of SPC can steer a company towards remarkable improvements, enhancing not just product quality but also operational clarity.
Benefits of Implementing SPC
When manufacturers adopt SPC, they unlock a treasure trove of benefits that extend well beyond just monitoring processes. Some key advantages include:
- Improved Quality Control: By continually assessing and monitoring process variations, SPC leads to both immediate collision with defects and long-term quality enhancement.
- Enhanced Productivity: Elimination of waste and inefficiencies boosts overall productivity, allowing production lines to operate close to their maximum potential.
- Data-Driven Insights: Informed decisions arise from empirical dataβnot from guesswork, leading to substantiated strategic trajectories.
- Regulatory Compliance: Many industries face stringent compliance requirements; SPC places organizations in a strong stance to meet these and avoid penalties.
Overall, implementing SPC cultivates a culture of continuous improvement within teams, embedding a quality-first mindset in every operation.
Impact on Product Quality
At the heart of every successful manufacturing strategy is product quality. SPC functions as a guardian β ensuring that every item rolling off the production line meets the necessary standards. Defects, whether subtle or glaring, can lead to costly recalls and tarnish a companyβs reputation. With SPC:
- Real-Time Monitoring: Facilities can track defects or deviations in real time, allowing for swift remediation before products are finished.
- Consistency Across Batches: Every batch receives the same high level of scrutiny, ensuring that product quality remains consistent.
- Root Cause Analysis: Identifying the source of quality issues becomes simpler with SPC's analytical tools, helping to adjust processes effectively and sustainably.
By embedding quality checks throughout the manufacturing process, SPC not only reduces defect rates but amplifies customer satisfaction, leading to repeat business and elevated brand loyalty.
Role in Cost Reduction
In manufacturing, keeping costs under control is as crucial as maintaining quality. Implementing SPC lays the groundwork for gradual cost reduction. Hereβs how:
- Minimized Waste: By identifying and controlling variations promptly, businesses can reduce waste concerning materials and time, optimizing resource use.
- Lowered Rework Costs: Detecting issues early means less need for rework, which can drain resources and time.
- Informed Process Optimization: Companies gain insights into where inefficiencies lie, allowing for targeted adjustments that ultimately save money.
SPCβs approach provides a data-centric view, enabling organizations to make precise decisions that influence the bottom line positively.
"Quality is never an accident; it is always the result of intelligent effort."
With SPC, organizations leverage intelligent insights to manifest long-term profitability.
Preparing for SPC Implementation
Preparing for Statistical Process Control (SPC) implementation is akin to laying a solid foundation before erecting a skyscraper. It's a critical phase that ensures the success of this sophisticated method of quality control. This section will explore the core elements of preparation, emphasizing that taking the right steps beforehand can yield substantial dividends in process efficiency and product quality.
Assessing Your Current Processes
Before embarking on the SPC journey, it's essential to evaluate your current manufacturing processes. This assessment isn't merely a checklist; it's a comprehensive review of your operations. Start by gathering as much data as possible about your product quality, defect rates, and process variations.
A thorough analysis may involve:
- Identifying bottlenecks: Where are the slow spots in your production? Is it the material supply, machinery limitations, or labor inefficiencies?
- Collecting historical data: Review your quality reports, production logs, and maintenance records. This backstory acts as a compass for your future endeavors.
- Engaging employees: Sometimes, the best insights come from those working on the shop floor. Ask about recognition of recurring issues or concerns they observe daily.
Like digging deep for treasure, this foundational step can reveal the unique challenges and strengths of your current workflow.
Defining Clear Objectives
Once you have assessed where you stand, it is paramount to define clear objectives for implementing SPC. This step not only aligns your teamβs efforts but also sets the stage for measurable success. Objectives should be Specific, Measurable, Achievable, Relevant, and Time-bound (SMART). Here are some objectives you may consider:
- Reduce defect rates by a specific percentage within a defined time frame.
- Improve production efficiency by minimizing variability in key processes.
- Enhance customer satisfaction by delivering consistently high-quality products.

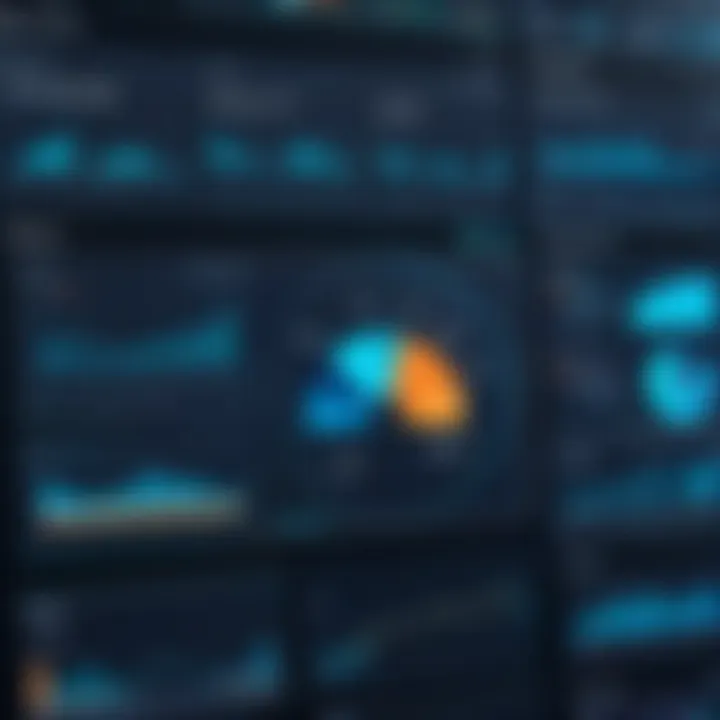
Having clear objectives acts like a map guiding your SPC implementation, providing clarity amidst the potential chaos of change.
Engaging Stakeholders
Engagement of stakeholders is a pivotal aspect in the preparation phase. Ignoring the perspectives of key personnel can jeopardize the entire SPC initiative. Stakeholders may include upper management, floor supervisors, quality assurance teams, and even frontline workers. Their buy-in can make or break the entire process.
To foster engagement, consider:
- Communicating the vision: Clearly articulate why SPC is vital for the organization's future. When stakeholders understand the 'why,' they're more likely to embrace the 'how.'
- Involving them in the process: Solicit input during the planning phase, ensuring that their concerns and suggestions are front and center. This not only enhances the plan but also strengthens their commitment.
- Regular updates: Keep the lines of communication open. Stakeholders should know whatβs happening at every stage. Frequent updates can transform potential resistance into proactive support.
Engaging the right people early in the game can smooth the bumps in the road once implementation begins, creating a stronger, united front against any challenges that may arise.
In summary, properly preparing for SPC implementation involves a meticulous assessment of existing processes, a commitment to defining clear objectives, and an inclusive approach to engaging stakeholders. Each piece intertwines with the others, creating a web of support that is crucial for successful adoption. By investing time and effort in this stage, organizations can ensure a more effective and sustainable SPC implementation.
Data Collection and Analysis
Data collection and analysis sit at the heart of Statistical Process Control (SPC). It's not just about gathering a heap of numbers; it's about making sense of what those numbers truly mean for manufacturing outcomes. In this section, we will peel back the layers of why the right data matters, how to select the key metrics, and methods of data collection. We will then look into the nitty-gritty of analyzing this data to spot trends, ultimately allowing for informed decision-making.
Identifying Key Metrics
When venturing into SPC, the first step is figuring out which metrics really matter. Key metrics, or key performance indicators (KPIs), should align with your production goals. These metrics are the benchmarks against which performance can be judged. Common examples include:
- Cycle time: How long it takes to complete one cycle of the production process.
- Defect rate: A measure of the amount of defective products produced.
- First pass yield: The percentage of products manufactured correctly without any need for rework.
Selecting the right metrics can feel a bit like searching for gold nuggets in a mountain of rocks. Itβs crucial to hone in on a few specific ones that effectively encapsulate your process performance. Focus on metrics that reveal insights about efficiency, quality, and production costs. Balancing relevance with measurability is key here, as it's pointless to track what cannot be accurately quantified.
Methods for Data Collection
Collecting data isnβt a one-size-fits-all approach. The methods vary widely and can directly influence how reliable and actionable your data will be. Here are a few commonly used methods:
- Manual recording: Though labor-intensive, it allows for precise tracking of specific issues in real-time. Workers can jot down observations on the shop floor.
- Automated data capture: Using sensors or software to automatically gather data can speed things up and reduce human error. This can include things like machine output metrics or environmental conditions.
- Surveys and feedback: While often overlooked, feedback from operators or stakeholders lends crucial context to quantitative data. Understanding how the process feels on the ground can reveal subtleties data alone may not show.
Whichever method you choose, consistency and accuracy should be your guiding principles. When the foundation is solid, the analysis can stand tall.
Analyzing Data for Trends
So, you've got your metrics sorted and data collected, what's next? It's time to roll up your sleeves and dive into the analysis. Analyzing data ins't just about crunching numbers; it's about telling a story. You want to look for patterns that can lead to actionable insights. Some strategies for effective analysis include:
- Using statistical software: Tools like Microsoft Excel or more advanced options like Minitab can streamline the process of analyzing large datasets. These can help you easily create charts, graphs, and control charts that illustrate trends over time.
- Grouping data: Cluster your data by day, week, or production batch to help identify fluctuations and their causes. Looking at broader trends often reveals issues masked by daily variability.
- Comparing against historical data: A retrospective look can illuminate whether improvements are on track, or if issues are resurfacing. Setting performance baselines creates context for understanding current performance.
The key to successful analysis is a continuous loop of observation and adjustment. That's how you refine processes over time.
SPC Tools and Techniques
When thinking about the successful implementation of Statistical Process Control (SPC) in manufacturing, itβs crucial to consider the array of tools and techniques that facilitate this process. These are not just optional extras, but rather the backbone of an effective SPC strategy. Each tool serves a unique purpose and provides distinct benefits, enabling businesses to streamline their operations and enhance product quality. In essence, these tools empower organizations to transform their data into actionable insights.
Control Charts
Control charts are one of the fundamental tools in SPC. They visually represent how a process varies over time, offering a snapshot of performance. This visual aspect is key. Decision-makers can quickly assess whether processes are steady or if they are experiencing variations that could indicate underlying issues.
There are several types of control charts, including:
- X-bar and R charts: These are used to monitor the mean and range of process variations.
- P charts: Ideal for tracking the proportion of defective items in a process.
- C charts: Best suited for analyzing the number of defects per unit.
Utilizing control charts effectively depends on the context. For instance, a manufacturing facility making automotive parts might adopt X-bar and R charts to ensure that the dimensions of components remain within specified limits. The key benefit is that any deviations can be spotted in real time, allowing for immediate corrective action before defects escalate into larger issues. As one might say, a stitch in time saves nine.
"Control charts not only highlight variation but can also signal when to make adjustments, keeping the manufacturing process within desired limits.β
Process Capability Analysis
Process capability analysis is another essential tool. It assesses how well a process meets specific requirements. Essentially, it evaluates whether the inherent variability of a process falls within acceptable limits. This analysis is invaluable for understanding the capability of manufacturing processes, as it provides a statistical basis for evaluating their performance.
The core metrics used in process capability include:
- Cp (Process Capability Index): This measures the potential capability of a process.
- Cpk (Process Capability Index, adjusted): This accounts for how centered the process distribution is within the specification limits.
By conducting process capability analysis, a company can identify areas that need improvement. For example, a plant producing electronic components might find through Cpk analysis that its soldering process is consistently outside of specifications. This insight can lead to targeted interventions, thus minimizing waste and reducing rework costs, making operations more efficient.
Pareto Analysis
Pareto Analysis, rooted in the 80/20 rule, is another pivotal tool in SPC. This technique helps to identify the most significant factors affecting a process. In the manufacturing world, this means focusing on the few causes that lead to the majority of problems.
The steps for conducting a Pareto Analysis include:
- Data Collection: Gather data on defects or errors in the process.
- Identification of Issues: Classify these defects into categories.
- Charting: Create a Pareto chart that displays the frequency of each issue.
By applying Pareto analysis, manufacturers can prioritize their improvement efforts effectively. For instance, if a facility observes that 80% of defects arise from just two types of errors, it makes sense to focus on rectifying these issues first. This targeted approach not only streamlines problem-solving but also maximizes resource use, creating a more significant impact on overall quality.
Implementation Strategies
In the realm of Statistical Process Control (SPC), the implementation strategies chosen will profoundly impact overall success. Not just a technical aspect, the approach to rolling out SPC can determine how well it integrates with existing manufacturing processes, shaping not only productivity but also organizational culture. When stakeholders decide on the implementation pathway, it's critical to prioritize elements such as effective communication, defined goals, and the necessity of pilot projects.
Pilot Projects
Starting with pilot projects serves as a litmus test for SPC initiatives. These small-scale trials allow organizations to gauge the effectiveness of SPC tools and techniques before committing further resources. As manufacturing environments can vary significantly, testing a select process provides insights that direct larger scale changes.
- Benefits of Pilot Projects:
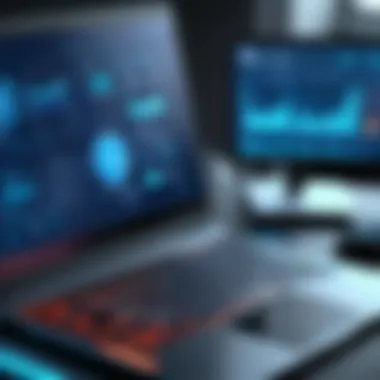
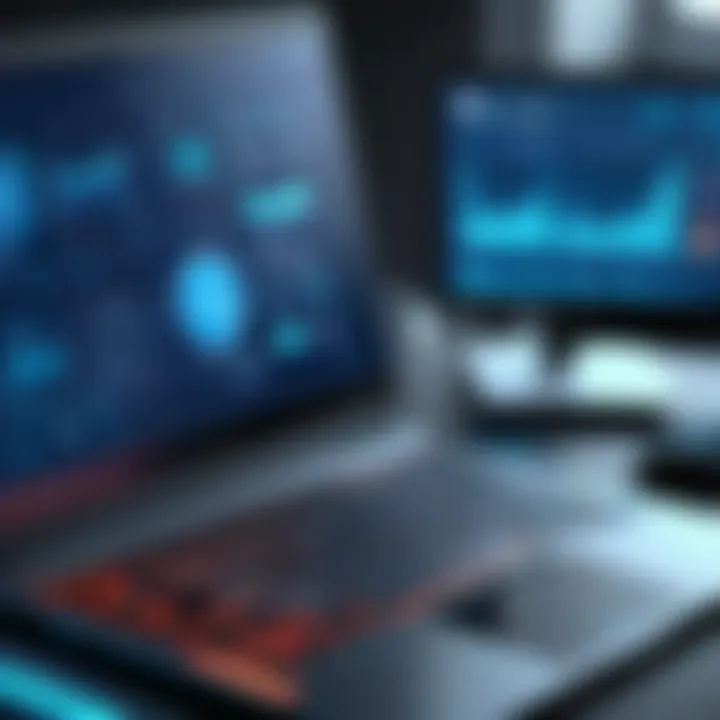
- Reduced Risk: By identifying potential pitfalls early, companies can sidestep costly mistakes later.
- Focused Learning: Teams can concentrate their training and observation on specific areas, fostering a more nuanced understanding of SPC.
Moreover, these pilots can serve as a blueprint for larger implementations. When stakeholders see tangible improvements in quality or efficiency, they become more inclined to support full-scale adoption.
Training Employees
Training employees on SPC principles is indispensable for achieving targeted outcomes. Without a well-trained workforce, even the best methods can wither on the vine. Hence, investing in comprehensive training programs ensures every team member understands not only how to apply SPC but why it matters.
- Key Considerations for Training:
- Tailored Curriculum: Design training modules that fit the specific roles of personnel. For instance, operators may benefit more from hands-on sessions, while management might focus on strategic implications.
- Continuous Education: Making SPC training a recurring activity fosters a culture of continuous improvementβspotted deficiencies can be addressed swiftly.
Training cannot be an afterthought; it's vital. If employees donβt grasp SPC, they wonβt utilize it effectively, and the promised benefits may remain just thatβpromises.
Integrating SPC into Daily Operations
Once training is complete, integrating SPC practices into daily operations is the final stepping stone. Here, the challenge lies not only in application but in the adoption of SPC as a habitual part of the workflow. Organizations can utilize various strategies to facilitate this integration.
- Practical Steps for Integration:
- Simplified Processes: Streamline how SPC tools are incorporated into everyday tasks to lessen resistance from staff.
- Visualization Tools: Utilizing visual aids such as control charts can offer clarity and reinforce the importance of monitoring practices.
Implementing SPC isnβt merely about installing new software or dashboards; it is about weaving SPC into the very fabric of organizational culture. The goal should be to shift mindsets so that quality control becomes second nature, rather than an added task.
"The strength of a chain is its weakest link."
Monitoring and Continuous Improvement
Monitoring and continuous improvement are the linchpins of an effective Statistical Process Control (SPC) system in manufacturing. The essence of SPC lies not just in the initial establishment of processes but in the ongoing vigilance to ensure that systems operate as intended and adapt to changing conditions. As the manufacturing landscape evolves, having a mechanism in place to monitor performance continuously stands paramount for sustaining quality and efficiency.
Regular monitoring enables manufacturers to catch deviations and anomalies early, thereby minimizing potential disruptions. When considered with a mindset geared towards continuous improvement, this becomes a cycle where data informs decisions that lead to better outcomes across the board.
Setting Up Monitoring Systems
Setting up an effective monitoring system involves several crucial steps that create a framework for success:
- Define Performance Indicators: Establish specific metrics aligned with production goals. These could include cycle times, defect rates, or yield percentages. Each metric should provide insights into operational efficiency.
- Choose Appropriate Tools: Various software and tools exist for monitoring processes, from basic spreadsheets to advanced enterprise systems. Selecting suitable tools contributes to accessibility and fosters real-time analysis.
- Integrate With Existing Processes: The monitoring system should mesh seamlessly with current operations. This ensures that data is relevant and actionable. Operators should have the means to access and interpret this data easily.
"Continuous monitoring without depth of analysis is like running a race without knowing the finish line."
Responding to Deviations
Deviations are inevitable in any manufacturing process. What matters most is how these deviations are addressed. Fast and effective responses can not only mitigate problems but also lead to significant learning opportunities. Here are a few strategies to consider:
- Immediate Investigation: Treat any deviation as a potential signal of deeper issues. Investigate root causes before jumping to solutions. Utilize methods like the 5 Whys analysis, which digs deeper into issues until their core is identified.
- Engage Teams Quickly: Form cross-functional teams that can respond swiftly to these challenges. Mobilizing expertise from various domains often leads to innovative approaches to solve problems.
- Document Findings: Any insights gathered from these deviations must be documented for future reference. This helps in refining processes and can serve as a valuable resource for staff training.
Continuous Feedback Loops
Feedback loops form the backbone of continuous improvement. Establishing a culture where feedback is not merely collected but actively sought after and acted on leads to better engagement and innovation. Hereβs how to create effective feedback loops:
- Regular Reviews: Schedule routine discussions about performance metrics. Ensure that all team members understand these metrics and their implications for the production process.
- Employee Input: Encourage frontline employees to share their thoughts on the processes. They often have the most intimate understanding of what works and what doesn't. They can provide insights that automation or streamlined systems might overlook.
- Adapt and Evolve: Use the feedback gained to cultivate an adaptable environment. Make adjustments based on data and feedback. Continuous improvement is about evolution, so remain open-minded and flexible.
Each of these aspects reinforces the others. When monitoring systems are set up effectively, deviations are addressed promptly, and feedback loops foster an environment of constant growth, manufacturing processes can lead to unprecedented levels of quality and efficiency. This holistic approach ensures not just survival but thriving within the competitive manufacturing industry.
Challenges and Solutions in SPC Implementation
Implementing Statistical Process Control (SPC) isnβt always a walk in the park. For manufacturers, wrestling with the intricacies of data collection, process evaluation, and the constant push for quality can be daunting. That said, recognizing and addressing the challenges inherent in SPC implementation is half the battle. An effective approach not only enhances the robustness of production processes but also reinforces a companyβs commitment to quality and efficiency.
Common Obstacles
Manufacturers frequently run into one or more hurdles when initiating SPC. Understanding these obstacles makes it easier to navigate and avoid potential pitfalls:
- Lack of Understanding: Often, teams struggle to fully grasp what SPC entails. This knowledge gap can stem from insufficient training or resources. Many may see SPC as another buzzword, leading to hesitance in applying its principles properly.
- Resistance to Change: Change is hard, especially in environments where practices are deeply rooted. Employees may resist adopting new methods due to familiarity with current practices, even if those practices are flawed.
- Inadequate Data Collection: At times, the underlying data may be riddled with errors or inconsistencies. Inaccurate data can lead to misguided decisions, undermining SPC efforts before they even start.
- Limited Resource Allocation: Implementing SPC can require investmentβboth financially and in terms of manpower. Small or mid-sized manufacturers might lack the resources for extensive setup and maintenance of SPC systems.
- Poor Management Support: If the higher-ups donβt believe in SPC, it can spell trouble. Leadership plays a critical role in fostering an environment where SPC can thrive. Without their backing, initiatives may struggle to gain traction.
Effective Mitigation Strategies
To overcome the aforementioned challenges, manufacturers can employ various strategies. Each strategy aligns with a specific obstacle, creating a robust framework for successful SPC implementation:
- Education and Training: Conduct workshops and training programs to bolster employees' understanding of SPC principles. Knowledge-sharing sessions can demystify statistical concepts, transforming skepticism into confidence.
- Change Management Initiatives: To ease resistance, engage employees from the get-go. Encouraging input and feedback can foster a sense of ownership among staff. When employees play a role in the change process, theyβre more likely to embrace it.
- Rigorous Data Protocols: Establish strict data collection procedures. Regularly validate data for accuracy and completeness to ensure that decisions made using the data are sound. You might consider using software tools to streamline data tracking.
- Invest in Resources Wisely: Carefully weigh the benefits of SPC against the resources required. Small adjustments in staffing or technology can lead to significant improvements. Consider incremental changes instead of an all-or-nothing approach.
- Executive Sponsorship: Secure buy-in from top management early on. Executive sponsors can champion SPC initiatives, offering resources and ensuring alignment with broader operational goals.
No challenge is insurmountableβeach obstacle presents an opportunity for improvement. Embracing the bumps along the way is vital to the success of SPC.
By recognizing these challenges and employing thoughtful mitigation strategies, manufacturers can not just implement SPC but thrive in their continuous quality improvement journey. This pragmatic approach ultimately leads to better product outcomes and operational efficiency.
Real-World Case Studies
Real-world case studies play a crucial role in understanding the practical application of Statistical Process Control (SPC) within various manufacturing sectors. They serve as a bridge between theoretical concepts and their execution in actual production environments. By examining these case studies, decision-makers and industry professionals can grasp the tangible benefits and potential challenges associated with SPC implementation.
One of the significant advantages of real-world examples is that they offer proof of concepts. For those skeptical about SPC's effectiveness, seeing how it positively impacted production processes, quality, and cost reductions in other companies can sway their perspective. Moreover, these case studies allow manufacturers to identify best practices and adapt them to their specific contexts.
When analyzing case studies, itβs essential to consider factors such as the industryβs unique demands, the scale of operations, and the specific SPC tools utilized. This exploration not only aids in understanding the variety of applications but also underscores the versatility of SPC across different manufacturing scenarios.
"The road to implementation can be rocky; however, the lessons from those who've walked it before light the way for us to follow."
Case Study: Automotive Industry
The automotive sector is often heralded as a beacon for SPC implementation, largely due to its emphasis on quality and precision. Major manufacturers like Toyota have utilized SPC to ensure that every vehicle produced meets stringent quality standards. This meticulous focus on data-driven decision-making has led to substantial improvements in product reliability and customer satisfaction.
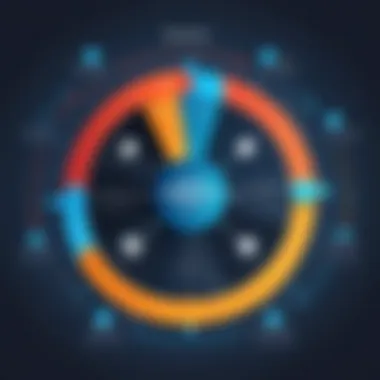
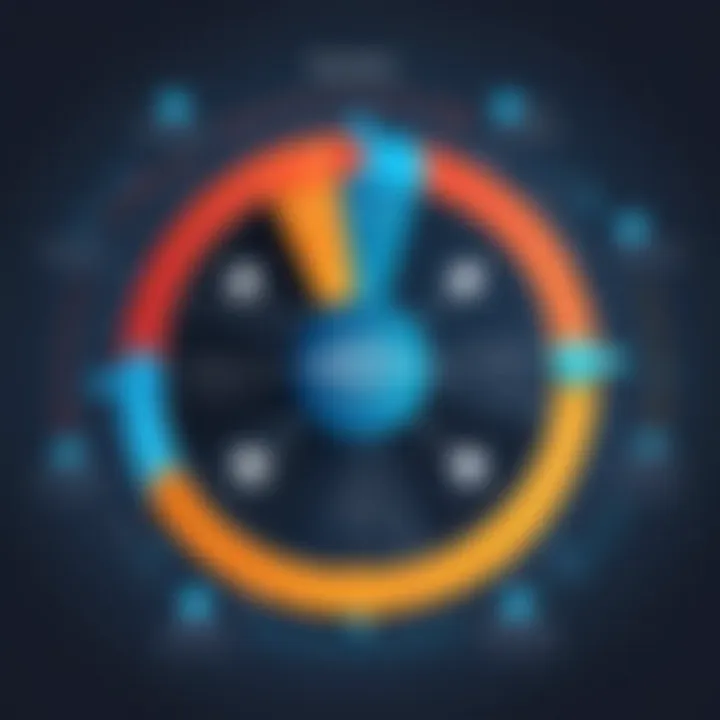
For instance, Toyota implemented a robust system that monitored production lines in real time through control charts. By consistently evaluating performance data, they could identify patterns indicative of potential defects before they escalated into larger issues. This proactive approach not only saved costs associated with recalls but also fortified their reputation in the market. Additionally, tracking process capability allowed them to understand and fine-tune operations with impressive accuracy, driving efficiency and reducing waste.
Benefits observed in the automotive industry due to SPC include:
- Enhanced product quality and reliability.
- Reduction in waste and cost of defects.
- Increased employee engagement through a culture of continuous improvement.
- Improved customer satisfaction ratings and loyalty.
Case Study: Electronics Manufacturing
On the flip side, the electronics manufacturing industry illustrates another dimension of SPC application. Companies such as Intel have leveraged SPC to combat the complexities associated with producing intricate electronic components. Given the rapid pace of technological advancements, maintaining a high level of quality while compressing lead times becomes imperative.
Intel's approach to SPC involves using advanced statistical methods to analyze data collected from their production lines. They have deployed sophisticated software tools that track various metrics, such as yield rates and defect levels. This data-driven culture enables them to respond quickly to any deviations from expected performance, ensuring they capture issues before they impact overall production.
Noteworthy benefits in the electronics sector, as seen through case studies like Intel's, comprise:
- Significant improvements in yield and reduction in defects.
- Heightened agility in production processes, allowing for rapid response to market changes.
- Overall cost savings attributed to minimized rework and waste.
- A solid foundation for innovation by freeing up resources otherwise spent on resolving quality issues.
Evaluating Success of SPC
Evaluating the success of Statistical Process Control (SPC) is crucial in a manufacturing environment. It not only determines how well SPC initiatives are meeting their objectives but also highlights the areas where improvements can be made. Success metrics provide tangible evidence of progress, enabling organizations to make informed decisions based on solid data.
A well-structured evaluation process can yield numerous benefits. For instance, it fosters a culture of accountability within teams. Employees become more engaged when they're aware that their contributions are being assessed and recognized. Furthermore, proper evaluations can also help in aligning SPC efforts with broader company goals, ensuring that everyone is on the same page.
Considerations when evaluating SPC success include the relevance of selected metrics, the frequency of assessment, and the methods used for analysis. Furthermore, one must also factor in the variability of the manufacturing process itself; what works well in one context may not be applicable in another. Thus, the evaluation landscape must be tailored to the specific environment, taking into account both internal and external factors.
"Successful SPC is not an endpoint, but a continuous journey of improvement and learning."
Key Performance Indicators
Key Performance Indicators (KPIs) are essential to gauge the effectiveness of SPC strategies. These indicators serve as a bridge between high-level objectives and the day-to-day realities of manufacturing operations. A few critical KPIs include:
- Defect Rates: Measures the percentage of defective products produced. A lower defect rate indicates effective SPC implementation.
- Process Capability Indices (Cp, Cpk): These indices reflect how well a process operates within specified limits. A higher value suggests better process performance.
- Cycle Time: Tracking the time it takes to complete a production cycle can help spot inefficiencies. Reducing cycle time can lead to greater throughput.
- First-pass Yield: This metric indicates how many products meet quality standards without rework. High first-pass yield signifies effective process controls.
Incorporating these KPIs into regular assessments allows for timely adjustments to be made. While evaluating these indicators, itβs crucial to analyze trends over time rather than isolated data points. A single snapshot may not reveal the real story behind the numbers.
Feedback from Staff and Management
Feedback is a vital cog in the machine of SPC evaluation. Collecting insights from both staff and management provides a multi-faceted view of how SPC practices are perceived and their effectiveness in real-world scenarios. Management's perspective often sheds light on strategic alignment and operational efficiency, while frontline employees offer a ground-level view of the processes at work.
Regular feedback sessions can help identify gaps in knowledge or resources. Employees are likely the first to notice areas that may need attention, such as bottlenecks, inefficiencies, or lapses in adherence to SPC guidelines. On the management side, feedback can provide insights into resource allocation and the effectiveness of training programs.
Methods for gathering feedback can include surveys, focus groups, or one-on-one interviews. By creating an open environment where team members feel comfortable voicing their experiences, organizations can cultivate a culture of continuous improvement.
In summary, evaluating the success of SPC is not just about crunching numbers; itβs about creating a feedback loop and cultural narrative that aligns with the overall objectives of the manufacturing process. The collaboration between metrics and human insights ultimately fosters a more resilient, efficient, and quality-driven manufacturing environment.
Future Trends in SPC
As industries face ever-changing market demands and technological advancements, the future of Statistical Process Control (SPC) is evolving rapidly. Understanding these trends is vital for decision-makers to remain ahead of the game. New methodologies and advancements can enhance quality and efficiency, aligning manufacturing processes with modern expectations. Here, we will explore pivotal elements that shape the trajectory of SPC, emphasizing the significance of adapting to these changes.
Incorporation of AI and Machine Learning
The integration of artificial intelligence (AI) and machine learning in SPC represents a paradigm shift in how data is processed and analyzed. By leveraging algorithms that can learn from vast amounts of data, manufacturers can achieve a level of precision and efficiency previously unattainable.
- Predictive Analytics: AI can help in forecasting potential issues before they arise. Instead of reacting to defects after they occur, companies can predict them by analyzing historical production data. This proactive approach allows for adjusted operations to minimize waste and prevent costly recalls.
- Automated Control Systems: Machine learning can streamline process control by intermittently monitoring key variables. With systems that auto-adjust based on real-time data, manufacturers can maintain optimum performance without extensive human intervention. This leads to less fluctuation and greater consistency in production outcomes.
- Enhanced Decision-Making: AI-driven analytics provide deeper insights into process capabilities. By presenting data in easy-to-understand visual formats, decision-makers can make informed choices rapidly, enhancing agility within the manufacturing process.
As we navigate down this path, manufacturers should consider the training of their workforce to adapt to the changing paradigms brought on by AI. Building an adaptable culture focused on continuous learning is crucial in this rapidly evolving landscape.
Evolving Standards and Regulations
With the advent of new technologies comes the need for updated standards and regulations. The manufacturing sector is under constant scrutiny, and adhering to evolving guidelines ensures not only compliance but also enhances quality control.
- Global Standards: Organizations like ISO contribute to setting unified standards for SPC practices. Understanding these standards helps companies to align their processes with international expectations, fostering credibility and reliability in products.
- Data Privacy Regulations: As data collection becomes more integral to SPC, manufacturers must be aware of data protection laws such as GDPR. Ensuring compliance protects not just the company but also the customers, fostering trust and loyalty.
- Sustainability Practices: As environmental concerns grow, integrating sustainability guidelines into SPC processes is becoming mandatory. Adopting greener practices not only aligns with consumer values but also helps companies meet regulations that are increasingly focused on reducing waste and energy consumption.
In this shifting regulatory environment, organizations must stay updated and flexible. Engaging with regulatory bodies and industry groups can help manufacturers anticipate changes, positioning them advantageously from a compliance perspective.
Staying one step ahead means not only implementing SPC but also understanding the framework within which it operates.
By understanding and adapting to these trends, manufacturers can bolster their SPC efforts, ensuring they are well-prepared to tackle future challenges in the production landscape.
Epilogue
In this article, we have explored the intricacies of Statistical Process Control (SPC) and its paramount role in enhancing manufacturing processes. This method provides a systematic approach for managing and improving production quality by utilizing data analysis and control techniques. The significance of conclusion lies not just in summarizing content but in driving home the importance of continuous application of SPC strategies.
Key elements that stood out include:
- The ability of SPC to pinpoint deviations in processes before they escalate into costly mistakes.
- Importance of accurate data collection and proper analysis techniques which form the backbone of effective SPC systems.
- Stakeholder engagement as a critical component of successful implementations, ensuring alignment throughout the organization.
The benefits are clear; successful tailoring of SPC systems can significantly boost product quality, drive down costs, and create a culture of continuous improvement. By focusing on both implementation and evaluation, companies can utilize SPC not just as a tool, but as a framework for sustained excellence.
"Quality is never an accident; it is always the result of intelligent effort." β John Ruskin
In considering the factors surrounding SPC, it becomes evident that the effort needed for successful implementation can yield significant dividends. Sooner than later, organizations that embrace SPC into their daily operations will not only meet benchmarks but also thrive in a competitive landscape.
Summary of Key Takeaways
- SPC serves as an essential framework for enhancing process quality.
- Engaging stakeholders ensures collaboration and effective implementation.
- Adaptation of SPC tools like control charts and Pareto analysis aids in data-driven decision-making.
- Continuous monitoring and adjustment are necessary to maintain process stability.
Final Thoughts on SPC Implementation
As we look to the future of manufacturing, the integration of technology, particularly Artificial Intelligence, will shape how SPC evolves. Adopting modern tools and methodologies will not only streamline processes but also enhance data analysis capabilities.
Establishing a culture that prioritizes quality through SPC can transform organizations, pushing them beyond mere compliance towards true operational excellence. Preparing for potential challenges and emphasizing training will empower teams, fostering a resilient manufacturing environment.
Ultimately, SPC is not just a set of techniques but a mindset geared towards improvement and innovation. Mastering it will equip decision-makers, IT professionals, and entrepreneurs with the insights needed to steer their manufacturing processes effectively.