Creating an Effective Inventory Management System
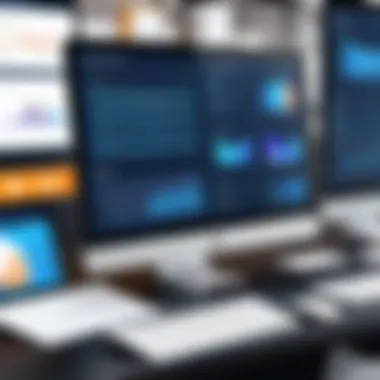
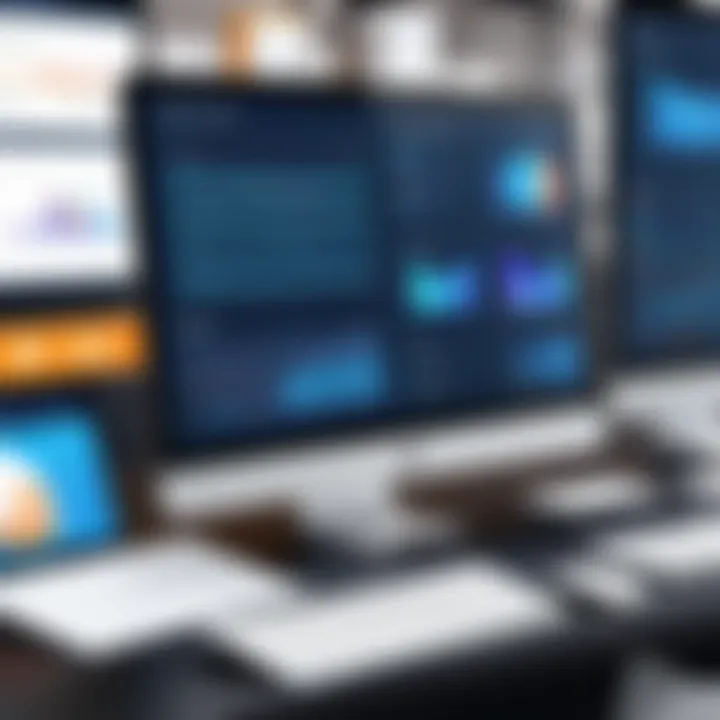
Intro
An effective inventory management system is crucial for any organization that deals with stock and inventory. The ability to monitor and control inventory levels directly affects profitability, efficiency, and customer satisfaction. As the market changes, businesses must evolve, adapting their systems to meet new demands. This article explores the foundational elements of building an effective inventory management system tailored to specific organizational needs. Readers will gain insights into necessary components, methodologies, technologies, and the integration required for smooth operations. Ultimately, the aim is to leave decision-makers equipped to implement strategies that enhance their inventory processes.
Key Features and Functionalities
Comprehensive Overview
An effective inventory management system integrates various functionalities that directly influence inventory control. The essential features typically include:
- Inventory Tracking: Real-time tracking of stock levels to prevent shortages or overstock.
- Order Management: Keeping track of orders, ensuring timely fulfillment and dispatch.
- Reporting and Analytics: Analyzing inventory data to make informed decisions, identify trends, and forecast future needs.
- Supplier Management: Managing relationships with suppliers to streamline reordering processes and maintain product availability.
Integrating these features promotes a cohesive system that enhances operational efficiency. Organizations benefit from fewer mistakes, optimized stock levels, and ultimately, a boost in profitability.
Target Users
The target users of an inventory management system usually fall into various categories. These include:
- Retailers: Businesses that sell goods directly to consumers often need sophisticated systems for tracking sales and stock.
- Manufacturers: They require detailed reports on raw materials and finished goods to maintain production flow.
- E-commerce Platforms: These businesses need to manage inventory across multiple channels.
Understanding the specific needs of these user segments ensures the development of a system that addresses their unique challenges.
Pricing Models and Cost Analysis
Breakdown of Pricing Tiers
When evaluating options for an inventory management system, costs will vary depending on features and complexity. Pricing models often include:
- Software as a Service (SaaS): Monthly subscription fees based on usage.
- One-time Purchase: Initial payment for software installation with potential annual maintenance fees.
- Tiered Pricing: Different levels of service or features at escalating price points.
Understanding these models is important for budgeting and decision-making.
Additional Costs to Consider
Apart from direct costs, organizations should consider other expenses related to the implementation of an inventory management system:
- Training Costs: Ensuring users understand how to operate the system effectively.
- Integration Fees: Connecting the new system with existing software and platforms can incur additional costs.
- Maintenance and Support: Continuous support and optional upgrades.
"Investing in an inventory management system extends beyond initial pricing; ongoing costs can affect your budget and operational success."
Ultimately, a tailored inventory management system can be a game changer for businesses, enabling them to maintain control over their assets, streamline processes, and enhance customer satisfaction. Implementing the right features for your needs sets a strong foundation for future growth and efficiency.
Understanding Inventory Management
Inventory management is more than just tracking stock. It involves a comprehensive approach that addresses the acquisition, storage, and distribution of goods. Understanding this concept is crucial for organizations aiming to optimize their operations. By having a solid grasp of inventory management, businesses can streamline processes, enhance customer satisfaction, and increase overall profitability.
Effective inventory management directly contributes to meeting customer demand without excess production. It minimizes holding costs and improves cash flow, making it essential for financial stability. Companies that neglect inventory management may face stockouts or overstock situations, leading to lost sales or wasted resources. Thus, recognizing its importance is the first step towards an effective system.
Definition and Importance
Inventory management refers to the discipline of overseeing and controlling the ordering, storage, and use of components within a company's inventory. This includes managing raw materials, components, and finished products to ensure that the right items are in the right location and at the right time.
The significance of effective inventory management cannot be overstated. It facilitates operational efficiency by balancing supply with demand. With accurate inventory data, firms can respond quickly to changing customer needs, thus fostering loyalty. Additionally, good inventory practices mitigate risks related to inventory loss or inefficient utilization of resources. In an age where customer expectations are high, proper inventory management supports timely delivery and quality service.
Key Objectives
The objectives of inventory management are multi-faceted and designed to improve efficiency. Key objectives include:
- Better forecasting: Accurate inventory management aids in predicting future demand based on past sales data.
- Cost reduction: By optimizing stock levels, businesses can reduce costs associated with storage, maintenance, and spoilage.
- Minimizing stockouts: Ensuring that customer demands are met prevents potential sales losses.
- Enhancing inventory turnover: Increasing the frequency with which inventory is sold and replaced can lead to higher profits.
- Improving compliance: Adherence to industry regulations regarding the storage and tracking of inventory can be better maintained with detailed management practices.
A well-designed inventory management system aligns closely with overall business strategy and objectives.
Analyzing Business Requirements
Analyzing business requirements is a crucial phase in developing an effective inventory management system. This process involves understanding what specific needs the organization has, as well as evaluating the current state of inventory management practices. By conducting this analysis, businesses can tailor their systems to meet precise demands, ultimately leading to better efficiency and productivity.
Identifying Specific Needs
This step is about recognizing the unique characteristics and challenges that a business faces. Each organization operates differently, influenced by elements such as size, industry, and inventory types. Identifying specific needs involves several tasks:
- Stakeholder Consultation: Engage with key personnel, including managers and employees who interact with inventory. Their insights will shed light on daily challenges and must-have features.
- Defining Goals: What do you want to achieve with inventory management? Goals may include reducing stock levels, minimizing waste, or improving order accuracy.
- Establishing Priorities: Determine which needs are most urgent. A small business might prioritize basic tracking, while a larger enterprise may focus on complex reporting features.
The emphasis on specificity ensures that the system built will not only be functional but also relevant to the users.
Assessing Current Inventory Processes
After identifying needs, it is imperative to assess existing inventory processes. This evaluation looks at how your current practices align with your goals.
- Mapping Current Workflow: Provide a detailed overview of how inventory flows in and out of the organization. Identify bottlenecks and inefficiencies.
- Technology Utilization: Check what tools and systems are currently used for inventory management. Are they sufficient, or are there gaps?
- Performance Metrics: Review key performance indicators. Metrics such as stock turnover rates and order fill rates provide valuable insights into the efficiency of current processes.
Through this assessment, businesses gain a comprehensive view of their existing capabilities and pitfalls. By understanding current practices, it becomes easier to devise a new plan that is informed, relevant, and directly aligned with business objectives.
"Effective inventory management begins with a clear understanding of business needs and current processes."
Taking these steps not only provides clarity but also sets the foundation for effective decision-making in the subsequent phases of developing a tailored inventory management system.
Choosing the Right Inventory Management Method
Selecting the right inventory management method plays a crucial role in achieving operational efficiency. Without a tailored approach, businesses may face issues such as increased costs, stockouts, or excess inventory. When considering various methods, it is essential to align them with specific business needs, industry requirements, and operational capabilities. Each method has distinct characteristics, advantages, and constraints. Decision-makers should carefully evaluate these methods to ensure they complement their overall strategy and enhance their inventory management processes.
Just-in-Time Inventory
Just-in-Time (JIT) inventory management aims to minimize inventory levels by receiving goods only as they are needed in the production process. This method reduces holding costs and minimizes waste, especially in manufacturing environments. Businesses that implement JIT benefit from improved cash flow and efficient use of storage space. However, reliance on suppliers for timely deliveries is critical, as any delays can disrupt operations.
Some key elements of JIT include:
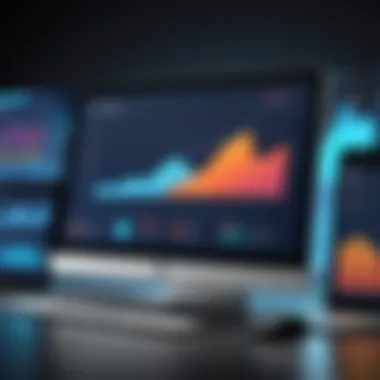
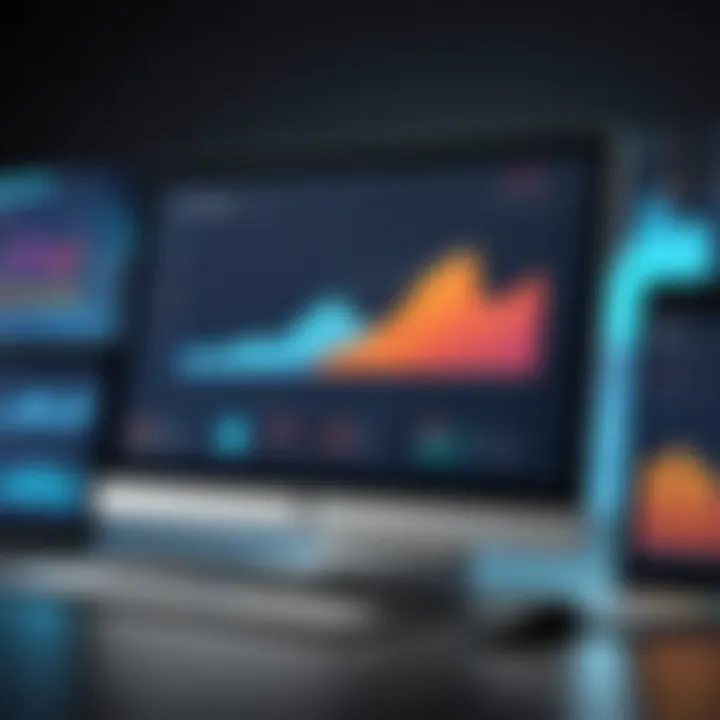
- Demand forecasting: Accurate forecasting is essential to predict customer demand and align inventory purchasing accordingly.
- Supplier relationships: Strong collaboration with suppliers ensures timely delivery and quality compliance.
- Flexibility: Organizations must be agile enough to adapt to demand changes while managing inventory effectively.
FIFO and LIFO Strategies
FIFO (First In, First Out) and LIFO (Last In, First Out) are both inventory valuation methods that impact financial reporting and tax obligations.
- FIFO: This method assumes that the oldest inventory items sell first. It is beneficial during inflationary periods as it results in lower cost of goods sold, leading to higher tax liability. Additionally, FIFO helps to reduce the risk of stock obsolescence.
- LIFO: In contrast, LIFO assumes that the most recent inventory items sell first. This approach can provide tax benefits in inflationary times due to higher cost of goods sold being recorded. However, it may lead to obsolescence of older inventory and is not widely accepted under international accounting standards.
Businesses should carefully consider the accounting implications and operational impacts when choosing between FIFO and LIFO.
ABC Analysis
ABC Analysis is a method of categorizing inventory items based on their importance and value. It divides inventory into three categories:
- A items: High-value items with significant impact on overall inventory cost. These require tight control and frequent inventory reviews.
- B items: Moderate value items that are important but not as critical as A items. They should be monitored regularly but may not need as stringent controls.
- C items: Low-value items that constitute a large portion of inventory. These may require less oversight and can often be managed with simplified processes.
Implementing ABC Analysis helps organizations prioritize their management efforts and resources effectively, ensuring that high-impact items receive appropriate attention while maintaining efficiency across all inventory levels.
Designing the System Architecture
Designing the system architecture is crucial for establishing a solid foundation for any inventory management system. It encompasses the organizational structure and technology framework that support the flow of information and decision-making processes related to inventory. An effective system architecture not only promotes efficiency but also ensures scalability and flexibility as business needs evolve. This design phase should prioritize the integration of key components and seamless data flow, which are critical for operational success.
Defining Core Components
In this phase, it is essential to identify the core components that will make up the inventory management system. These elements typically include inventory tracking features, user interfaces, reporting capabilities, and data storage solutions. Each component should reflect the unique requirements of the business.
Popular core components include:
- Inventory Tracking: This allows real-time visibility of stock levels, locations, and movements.
- User Interface: A user-friendly interface simplifies interaction, improving efficiency among users.
- Reporting Tools: Effective analytics and reporting tools enable data-driven decision-making for optimizing inventory levels.
- Database Management: A robust database is needed to ensure data integrity and availability.
Outlining these components is imperative for aligning technical capabilities with business strategies. An integrated approach ensures that every aspect of the inventory management cycle is connected, ultimately improving productivity and reducing operational costs.
Establishing Data Flow
Establishing a clear data flow within the system is vital for effective inventory management. This involves mapping the path that data will take from input to reporting. Data flow defines how information moves between components and how it can be accessed by users at different levels.
Consider these factors when establishing data flow:
- Input Sources: Identify where data originates, such as suppliers, sales channels, or internal transactions.
- Data Processing: Determine how data is processed, including calculations for stock levels and forecasting.
- Output Channels: Define how information will be reported to end-users, which could be through dashboards or periodic reports.
By creating a well-structured data flow, organizations can enhance communication between departments and ensure that decision-makers have timely access to relevant information. This transparency aids in reducing errors and accelerates response times to market changes.
Effective system architecture leads to an agile inventory management process, enabling businesses to respond swiftly to market dynamics and customer needs.
Selecting Appropriate Software Solutions
Selecting the right software solutions for inventory management is crucial for optimizing operational efficiency. The software acts as the backbone of any inventory system, enabling organizations to streamline processes, reduce errors, and enhance decision-making. When choosing software, businesses must consider multiple factors, including functionality, scalability, and integration capabilities. A well-integrated system ensures that different business arms work harmoniously, which is vital for maintaining accurate inventory levels and meeting customer demand.
Evaluating Off-the-Shelf Options
Off-the-shelf inventory management software offers a convenient alternative for many businesses. These solutions come pre-packaged with features that can address common inventory challenges, making them a cost-effective choice for small to medium-sized enterprises. When evaluating off-the-shelf options, look for features like:
- User-friendly interfaces: The ease of use can affect training time and overall staff productivity.
- Scalability: As your business grows, the software should be able to handle increased transaction volumes.
- Customization potential: While they come ready-made, some off-the-shelf options allow limited customization, which may be beneficial for unique business needs.
- Integration capabilities: They should mesh well with existing systems such as accounting or e-commerce platforms.
Readily available examples like Shopify and QuickBooks present strong cases for off-the-shelf solutions. However, businesses should assess whether these fit their specific requirements. Missing features or functionalities could lead to inefficiencies, which negates the benefits of using such software.
Considering Custom Development
In contrast, custom developed software offers a tailored solution to meet specific operational needs. This option may be more time-consuming and costly, but it can yield significant returns if done correctly. Custom development ensures that all features align precisely with business processes. Important considerations include:
- Initial Investment vs. Long-term Savings: The initial cost might be higher, but the long-term benefits can outweigh this investment through improved efficiencies.
- Business-Specific Features: Custom solutions can incorporate unique workflows, automation, and reports tailored to specific industry needs.
- Flexibility for Changes: As the business evolves, custom software can be updated to accommodate new requirements without the limitations often found in off-the-shelf products.
Before committing to a custom solution, conduct a thorough cost-benefit analysis. Engage with software development firms that specialize in your sector to get insights into potential ROI and maintenance costs.
"Choosing the right software solution can make or break the efficiency of your inventory management system."
By focusing on both off-the-shelf and custom-developed software options, organizations can make informed decisions that align with their strategic goals. The right choice directly impacts inventory flows, overall productivity, and ultimately, customer satisfaction.
Integration with Existing Systems
Integrating an inventory management system with existing systems is crucial for successful operations. An effective integration not only enhances data coherence but also maximizes the utility of both new and legacy systems. Organizations rely on various platforms for finance, sales, and supply chain management. Therefore, an integrated approach can streamline workflows and improve overall productivity.
Identifying Integration Points
To achieve a seamless integration, it is important to identify key integration points. This involves understanding where the new inventory system will interact with current systems. Common integration points include:
- ERP Systems: These systems manage critical business processes. Integration here allows for real-time inventory data sharing.
- CRM Software: This integration supports accurate inventory levels reflected in customer interactions, improving service quality.
- E-commerce Platforms: For businesses selling online, connecting inventory ensures that stock levels are updated automatically.
Take time to map out business processes to pinpoint these integration areas. Skipping this analysis may lead to inefficiencies or data silos.
Data Migration Strategies
Data migration is another vital aspect of integration. This process involves transferring data from existing systems to the new inventory management system. Proper planning can prevent data loss and ensure accuracy. Here are effective data migration strategies to consider:
- Data Cleansing: Ensure that the data is accurate and relevant before migration. Eliminate duplicates and outdated information.
- Phased Migration: Transfer data in phases rather than all at once. This approach allows for adjustments and troubleshooting along the way.
- Testing Migration: Conduct tests using a small dataset to ensure that the migrated data is correctly formatted and functioning within the new system.
"A well-planned migration strategy can save time and reduce future complications."
It is essential to document each step during the migration process. Proper documentation helps for future updates and enhancing compliance with data regulations.
Implementing Inventory Control Techniques
Implementing inventory control techniques is vital for maintaining an efficient inventory management system. It encompasses various strategies that allow businesses to manage stock levels effectively, minimize costs, and ensure products are available when needed. The techniques help in balancing supply and demand while reducing excess stock, which can become a financial burden. Organizations that implement these techniques can expect improved operational efficiency, better cash flow, and enhanced customer satisfaction.
Setting Reorder Levels
Setting reorder levels is the fundamental step in effective inventory control. A reorder level indicates the minimum amount of stock at which a new order should be placed to prevent stockouts. This technique considers factors such as lead time, average demand, and safety stock.
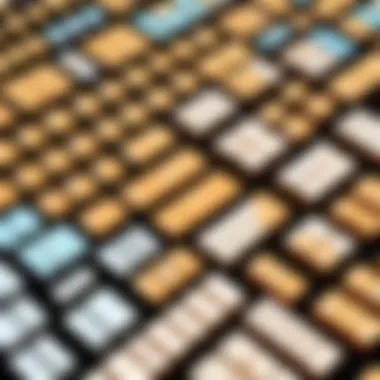
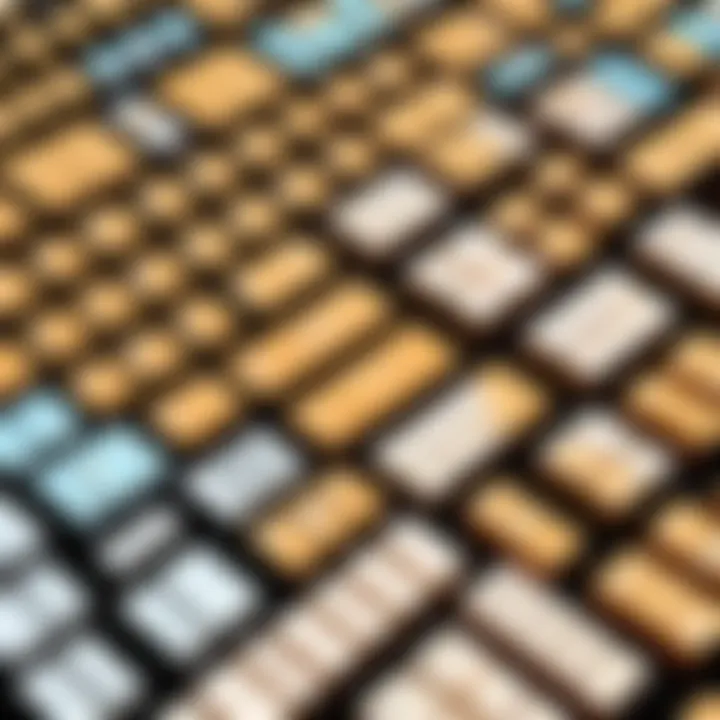
- Determine Lead Time: The time it takes for new stock to arrive after placing an order is crucial. A reliable supplier should be chosen to ensure predictability.
- Calculate Average Demand: Understanding the daily or weekly consumption of inventory helps in making informed decisions.
- Establish Safety Stock: Unexpected demand fluctuations can happen. Maintaining safety stock acts as a buffer.
These factors combine to form an effective reorder level that varies according to specific needs and market conditions. An appropriate reorder level minimizes the risk of excess inventory while ensuring that products are readily available for customers.
Tracking Inventory in Real-Time
Tracking inventory in real-time is another essential component of inventory control techniques. This process employs technology to monitor stock levels continually. Real-time tracking offers several benefits that can significantly enhance inventory management.
- Improved Accuracy: By using automated systems, the chances of human error are considerably reduced. Accurate records facilitate better decision-making.
- Prompt Replenishment: Real-time visibility allows businesses to place orders immediately when stock levels fall below the reorder point, ensuring availability.
- Enhanced Reporting: Access to up-to-date data aids in generating reports that reflect inventory health, turnover rates, and sales trends, leading to informed strategy adjustments.
Implementing real-time tracking tools like RFID or barcode systems can provide clear and actionable insights, which ultimately supports lean inventory management and efficient operational practices.
"Effective inventory control is a blend of art and science. Getting the timing right is crucial to sustain operations efficiently."
Monitoring and Reporting
Monitoring and reporting serve as integral components in an effective inventory management system. They provide insights into stock levels, turnover rates, and overall inventory health. By focusing on these aspects, organizations can make informed decisions that enhance operational efficiency. Implementing robust monitoring systems ensures that businesses can track inventory movements in real-time and align their inventory levels with demand forecasts. This not only minimizes excess stock but also reduces the risk of stockouts, which can lead to lost sales and customer dissatisfaction.
A well-structured reporting system brings additional clarity to inventory management. Through detailed reports, decision-makers can visualize trends, evaluate performance against KPIs, and identify areas for improvement. The benefits of effective monitoring and reporting extend beyond mere tracking; they enable proactive management by providing actionable insights that inform purchasing decisions and resource allocation.
One must consider the technology and methodologies employed in tracking and reporting inventories. These tools should be integrated with existing systems for seamless data flow. Integration provides a comprehensive view of operations, ensuring decisions are based on accurate and timely information. The implementation of automated reporting tools can alleviate manual errors and enhance data reliability, providing greater confidence in decision-making.
Establishing KPIs for Inventory Management
Key Performance Indicators (KPIs) are quantifiable measures that help businesses evaluate their inventory management effectiveness. They provide a clear framework for assessing performance against strategic objectives. An organization should establish specific KPIs tailored to its unique inventory management goals.
Some common inventory KPIs include:
- Inventory Turnover Ratio: Measures how often inventory is sold and replaced over a period. A higher ratio indicates efficient sales processes.
- Days Sales of Inventory (DSI): Reflects the average number of days it takes to sell the entire inventory. Lower DSI signifies better inventory efficiency.
- Stockout Rate: Indicates how often stock is unavailable when needed. A lower stockout rate means improved customer satisfaction and retention.
- Carrying Cost of Inventory: Further assesses the total cost of holding inventory, encompassing storage, insurance, and depreciation.
By continuously measuring these KPIs, organizations can gain insight into performance levels, set benchmarks, and drive inventory optimization efforts.
Utilizing Reports for Decision-Making
Utilizing reports effectively plays a critical role in the decision-making processes of inventory management. Through well-structured reporting, decision-makers can access data that highlights not just current inventory status but also predictive insights that guide future strategies.
Reports can cover various aspects, including:
- Sales Trends: Understanding which products perform well can help prioritize stock levels and optimize purchasing strategies.
- Supplier Performance: Monitoring reports on suppliers can assist in evaluating their reliability and service quality.
- Seasonal Trends: Data on seasonal variations can inform stock preparations to meet peak demand periods.
Furthermore, decision-makers should ensure reports are accessible to stakeholders. This transparency aids communication across teams, aligning inventory strategies with broader business objectives. Structured reports, combined with real-time data, promote a culture of informed decision-making, ultimately driving business success.
Investing in effective monitoring and reporting systems not only streamlines inventory processes but also provides a competitive advantage in the market.
Training Staff and Stakeholders
Effective inventory management transcends merely having the right tools. It involves an essential human element: training the staff and stakeholders who will utilize the system. This component plays a significant role in achieving operational efficiency and ensuring that the system is leveraged to its full potential. Proper training enhances user confidence, promotes adherence to processes, and minimizes errors in inventory handling. Without it, even the most sophisticated systems can falter.
Developing Training Programs
Developing a robust training program is the cornerstone of any successful inventory management system. This program should be tailored to address various user roles, from warehouse staff to upper management. Here are some key considerations:
- Identify Training Needs: Assess the specific skills and knowledge gaps within your team. A thorough evaluation through surveys or interviews can provide insight into what areas require focus.
- Create Structured Content: Training materials should cover fundamental concepts of inventory management, the operations of the chosen system, and best practices. Incorporating a mix of visual aids, written guides, and practical exercises can enhance understanding.
- Utilize Technology: Consider using online learning platforms or software that allows for interactive training sessions. This approach can cater to different learning styles and promote engagement.
- Monitor Progress: Implement assessments to gauge the effectiveness of the training. Regular quizzes or practical tests can help ensure staff are absorbing the material.
Investing time and resources into developing comprehensive training programs leads to longer-term benefits, including increased efficiency, reduced turnover, and higher employee morale.
Establishing User Manuals and Documentation
User manuals and documentation are critical resources that often go overlooked during system implementation. By providing clear and accessible documentation, organizations can empower users to navigate the inventory management system with ease. Here are important aspects to consider:
- Clarity and Precision: Manuals should be written in straightforward language. Avoid jargon unless it is commonly understood by all users. This will help in making the documentation accessible to everyone involved.
- Step-by-Step Guidance: Include detailed, step-by-step instructions on how to perform key operations within the inventory system. Screenshots or diagrams can significantly aid comprehension.
- Frequently Asked Questions (FAQs): Anticipate common user issues and create a section dedicated to FAQs. This can serve as a quick reference and reduce the need for additional support.
- Regular Updates: The inventory system will evolve over time. It is essential to keep manuals up to date with the latest features and processes. Regularly reviewing and updating documentation ensures that users are always equipped with the most relevant information.
Ensuring Scalability and Flexibility
In an ever-evolving business environment, ensuring scalability and flexibility within an inventory management system becomes central to long-term success. Businesses often face rapid changes, driven by market demands, technological advancements, or customer preferences. Therefore, a static inventory system can hinder organizational growth and responsiveness. Having an adaptable inventory management system enables businesses to grow without drastic disruptions. It means that whether a company is expanding its product line or entering new markets, the inventory system can seamlessly adjust to these changes.
Planning for Future Growth
Future growth planning starts with defining a clear vision of where the business intends to go. It involves not just projecting sales but also understanding how inventory will need to scale. This often includes expanding warehouse spaces, enhancing software capabilities, or even adjusting inventory practices. Key actions in this planning phase include:
- Setting Scalable Goals: Define clear targets for potential growth over the next few years. This provides a reference point for what changes to make in the inventory management processes.
- Investing in Flexible Systems: Choose systems that can easily integrate additional features or modules as the business grows.
- Forecasting Demand: Employ data analytics to understand trends and prepare for seasonal fluctuations, ensuring that the inventory system can accommodate these changes.
When growth is anticipated, organizations should be proactive in their approach to adaptability. This means being ready to increase quantities and varieties of stock or adjust procurement strategies accordingly.
Adapting to Market Changes
Market changes can be swift and unpredictable. Thus, having an inventory management system that adapts to these changes is crucial for maintaining competitive advantage. Organizations must recognize that staying relevant often means adjusting inventory strategies based on shifts in consumer behavior, economic conditions, or new technological innovations. Here are steps to enhance adaptability:
- Regular Market Analysis: Conduct frequent reviews of market trends to inform inventory decisions. Keeping abreast of competitor strategies can also illuminate new opportunities.
- Dynamic Inventory Management: Use inventory management solutions that allow for real-time updates and adjustments based on stock levels and sales velocity. Adopting an agile approach helps in responding swiftly to both supply chain disruptions and consumer demand surges.
- Collaborative Supply Chain Relationships: Form solid partnerships with suppliers to create a more flexible supply chain. This can include forming agreements that allow for rapid restocking or special purchasing terms during crises.
Effective adaptability can turn potential disruptions into opportunities.
By building an inventory management system grounded in scalability and flexibility, companies position themselves to not only survive but thrive amidst change. This strategic foresight ensures that as demands fluctuate, the system complements the overall business strategy, paving the way for sustained growth.
Evaluating System Performance
One significant benefit of regular evaluation is to ensure that the system operates at optimal capacity. By assessing performance metrics, businesses can identify inefficiencies and bottlenecks in inventory management. This process also encourages a culture of transparency and accountability among the staff involved in inventory control. Regular evaluation allows businesses to remain competitive by adapting to changes in the market, technology, and operational practices.
Key considerations in evaluating system performance include:
- Setting clear performance metrics: Clearly defined key performance indicators (KPIs) are essential for measurement.
- Periodic assessments: Regular intervals should be set for evaluations, ensuring consistent monitoring.
- Incorporating feedback: Engage with users to gather insights about the system's functionality.
"Regular evaluation of inventory systems not only uncovers inefficiencies but also enables businesses to adapt swiftly to changes."
Overall, evaluating system performance is more than merely analyzing data; it is about making informed decisions to enhance overall productivity and responsiveness within the organization.
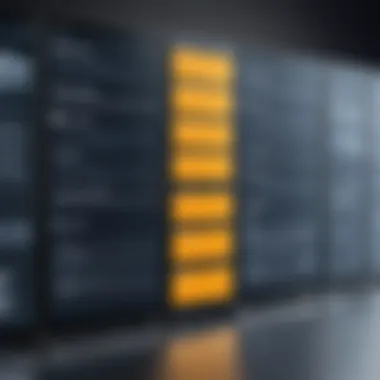
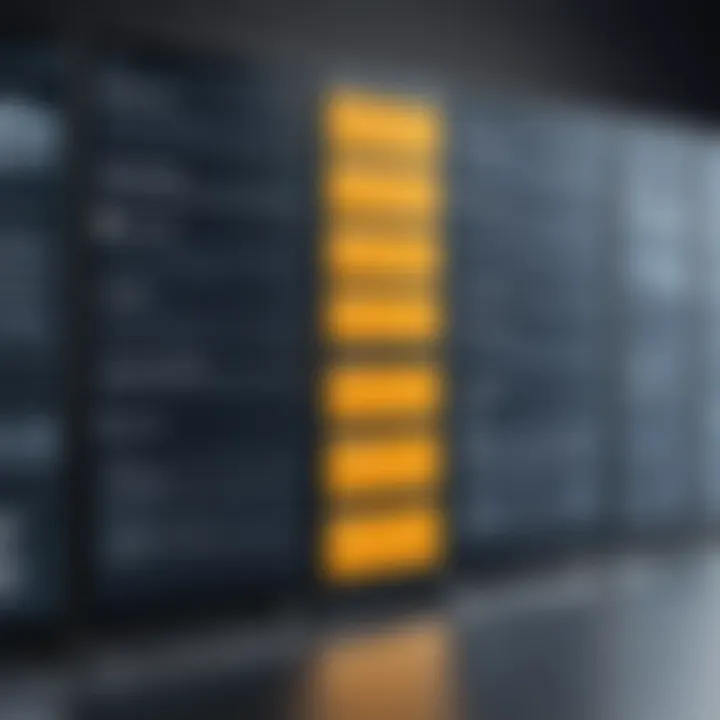
Conducting Regular Audits
Conducting regular audits is a foundational practice in truly effective inventory management. These audits serve to systematically assess both the physical inventory and the data records. A comprehensive audit reveals discrepancies between actual stock levels and recorded data, allowing businesses to rectify inaccuracies immediately.
The benefits of regular audits include:
- Accuracy in inventory records: Ensure that what is on file matches physical stock, avoiding stockouts or overages.
- Improved compliance: Aid in regulatory compliance and adherence to industry standards.
- Financial integrity: Contributes to more accurate financial reporting based on actual inventory value.
- Risk management: Identify shrinkage or theft issues and develop strategies to mitigate risks effectively.
Additionally, audits should be documented meticulously. This documentation will create a track record of all findings and corrective actions taken, which can be beneficial for future evaluations.
Analyzing User Feedback
User feedback is invaluable in assessing the performance of an inventory management system. Insights from actual users who interact with the system daily can highlight practical challenges and areas for improvement that senior management may overlook. Engaging with users allows a deeper understanding of their experiences, frustrations, and suggestions.
Key steps in analyzing user feedback include:
- Creating structured surveys: Gather input through surveys, focusing on questions regarding usability, features, and system performance.
- Conducting interviews: Engage with users directly for qualitative insights into their experiences.
- Maintaining an open feedback loop: Facilitate ongoing communication for continual improvement based on user observations.
- Prioritizing actionable items: Make decisions based on the frequency and impact of user feedback.
Analyzing this feedback promotes a user-centered approach, ultimately leading to system enhancements and greater user satisfaction. To sum up, a systematic approach to evaluating system performance through audits and user feedback provides businesses with the direction needed to enhance their inventory management efficiency.
Continual Improvement of the System
In today's fast-paced business environment, organizations must prioritize the continual improvement of their inventory management systems. This approach is not just beneficial but essential for maintaining a competitive edge. As markets evolve and consumer demands fluctuate, businesses need a system that adapts quickly. Continuous improvement ensures that the system remains efficient, effective, and aligned with the organization’s goals.
The benefits of continual improvement are numerous. Firstly, it allows businesses to streamline processes. Regular evaluation of inventory management practices can highlight inefficiencies. Recognizing these shortcomings paves the way for solutions that increase productivity. Additionally, this ongoing process fosters innovation. Organizations that embrace feedback are often at the forefront of new ideas, technologies, and methodologies, leading to enhanced customer satisfaction.
Implementing continual improvement requires specific considerations. It demands an organizational culture that embraces change. Staff at all levels must understand that improvement is a collective responsibility. Moreover, management needs to allocate adequate resources for training and tools to facilitate this process. Without proper backing, even the best intentions can fall short.
In sum, continual improvement of the inventory management system is vital, not just for survival but for growth. It positions a business to anticipate change and respond effectively. The next sections delve deeper into how to execute this by focusing on feedback loops and staying attuned to industry trends.
Implementing Feedback Loops
Feedback loops play a crucial role in driving continual improvement. They provide structured insights into the effectiveness of inventory management processes. In order to integrate feedback effectively, organizations should establish clear channels for collecting input from employees, suppliers, and even customers. This creates a holistic view of the inventory system’s performance.
The implementation process can start with surveys and suggestion boxes. This encourages team members to share their experiences and recommendations. Additionally, using performance metrics can help frame these discussions. For example, if inventory turnover is lower than expected, it may be time to reevaluate stocking strategies. Consider engaging in regular meetings that focus on inventory issues, which gives all voices a platform.
Feedback should not just be collected; it must also be acted upon. Prioritizing actionable insights is important. This can be achieved by grouping feedback into categories such as operational efficiency, customer experience, and technology usage. This method makes it easier to identify trends and implement changes that can drive improvement.
"The key to success lies in understanding the metrics that matter and listening to the voices that inform them."
Staying Updated with Industry Trends
Remaining cognizant of industry trends is another crucial component of continual improvement. Inventory management is not static; it is influenced by technological advancements, changing consumer behaviors, and shifts in global supply chains. Keeping up with these trends informs strategic decisions and helps organizations pivot when necessary.
To stay updated, businesses can engage in several practices. Participating in industry conferences and networking with peers offers valuable insights. Additionally, subscribing to relevant journals and online forums can keep decision-makers informed about cutting-edge practices. A good example is Reddit, which offers various threads and discussions on inventory management strategies.
Monitoring competitors is also advisable. Evaluating their successes and failures can yield lessons that inform your own inventory practices. For instance, if a competitor adopts a new software solution that increases efficiency, it may warrant further investigation for your organization.
In summary, continual improvement in inventory management systems is a key principle that organizations must adhere to in order to thrive. Implementing feedback loops and actively keeping pace with industry trends are two effective strategies in this endeavor. These elements not only enhance operational efficiency but also build a foundation for sustained growth.
Case Studies and Real-World Examples
Case studies and real-world examples play crucial roles in understanding how to build and implement successful inventory management systems. They provide concrete evidence pointing out what works effectively and what doesn't in practical scenarios. Using these examples, decision makers can make informed choices that align with their specific situations.
Benefits of using case studies in inventory management are numerous. First, they reveal insights into unique challenges faced by different businesses. Each company has its own inventory needs based on the industry, size, and operational model. By examining a real-world scenario, businesses can learn how to tailor their inventory systems effectively.
Additionally, these studies often highlight various strategies and technologies employed. This information can be critical when selecting the right components for one's system. Importantly, they can also showcase measurable outcomes, providing data that reinforces the value of implementing the right practices.
A key consideration when referencing case studies is to examine relevant metrics. Look not just at decisions made, but also at how they impacted the business in terms of cost savings, efficiency improvements, or sales growth. This thorough analysis ensures a comprehensive understanding that can guide future implementations.
"Real-world examples serve as a bridge between theory and practice, offering practical insights that improve decision-making in inventory management."
Successful Implementations
Successful implementations of inventory management systems can be found across various industries, illustrating the diverse approaches taken by organizations. For instance, Zara, a leading fashion retail chain, utilizes a unique just-in-time inventory system. This system allows them to minimize excess stock while quickly responding to fashion trends. By analyzing sales data and adjusting inventory accordingly, Zara has reduced lead times, enhancing customer satisfaction and profitability.
Another notable example is Amazon's use of advanced robotics in their warehouses. The company’s inventory management system integrates data analytics and machine learning to optimize stock levels. This ensures that products are available when needed, leading to faster delivery times. The combination of technology and efficient processes has set Amazon apart in the e-commerce landscape.
In the manufacturing sector, Toyota exemplifies successful inventory management through its well-known lean manufacturing system. By focusing on reducing waste and maintaining optimal inventory levels, Toyota has maintained high efficiency in production while minimizing costs. These implementations demonstrate the power of customized inventory solutions that have been derived from real-world experiences.
Lessons Learned from Failures
Studying failures in inventory management also provides valuable lessons. One significant case involves Target's attempt to enter the Canadian market. The company faced severe supply chain issues that led to empty shelves in stores, resulting in customer dissatisfaction. The failure highlighted the importance of proper supply chain management and thorough market research before launching new initiatives.
Similarly, McDonald's faced challenges with inventory management during a major menu change in 2015. The restaurant chain struggled to keep up with demand while managing new ingredients. This resulted in food shortages at locations, leading to negative customer experiences. The key takeaway here is the necessity for a well-planned transition process and ensuring adequate inventory levels during changes.
These examples serve as reminders that effective inventory management is not just about having a system in place. It is about understanding the unique challenges and developing strategies to mitigate potential risks. By learning from these failures, businesses can refine their approaches, helping to create robust systems that meet the needs of their operations.
Culmination
An effective inventory management system is crucial not only for optimizing stock levels but also for enhancing operational efficiency and reducing costs. Key considerations include ensuring accuracy in tracking, employing the correct methodologies, and leveraging technology for better data insights. By having a clear structure and processes in place, organizations are better positioned to respond to fluctuations in demand and shifts in market conditions.
Key Benefits of an Effective System:
- Improved decision-making through real-time data access.
- Enhanced customer satisfaction by maintaining product availability.
- Reduced carrying costs through better inventory turnover rates.
- Increased profitability as a result of optimized operations.
- Ability to scale operations seamlessly as the business grows.
"Inventory management is not just a backend function; it is central to achieving a competitive advantage in today’s business landscape."
Understanding these aspects not only aids in developing a capable inventory system but also aligns inventory operations with broader business goals. The future success of an organization hinges on its ability to manage inventory efficiently, reflecting the direct impact of this topic on business outcomes.
Recapping Key Takeaways
To summarize the discussions presented in this article:
- Inventory management is pivotal for operational success.
- Identifying specific business needs is a foundational step.
- Selecting the right methodologies, like Just-in-Time or FIFO, can significantly impact efficiency.
- Integration with existing systems should not be neglected as it enhances overall functionality.
- Continual evaluation and improvement of the inventory system is necessary for long-term sustainability.
Future Outlook for Inventory Management Systems
Looking ahead, inventory management systems will continue to evolve, influenced by advancing technologies and changing market dynamics.
Emerging trends like artificial intelligence (AI) and machine learning promise to enhance inventory accuracy and predictive capabilities. These technologies will help organizations anticipate demand and automate stock replenishment processes. Furthermore, the integration of IoT devices will allow for real-time tracking and reporting, providing deeper insights into inventory status.
Additionally, sustainability becomes more critical. Companies will increasingly focus on minimizing waste and optimizing supply chains to reduce their environmental impact. Embracing such innovations will not only improve efficiencies but can also enhance brand reputation and customer trust.